ADAPTIVE HYDRAULIC AND PNEUMATIC ACTUATORS
Журнал: Научный журнал «Студенческий форум» выпуск №21(200)
Рубрика: Технические науки
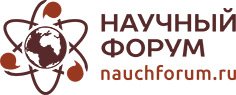
Научный журнал «Студенческий форум» выпуск №21(200)
ADAPTIVE HYDRAULIC AND PNEUMATIC ACTUATORS
One of the promising directions in the development of hydraulic and pneumatic drives is associated with the development of adaptive drives capable of controlling objects in conditions of changing parameters of technological processes. The task of adapting the drive to changing loads includes stabilizing the speed of movement of the output link of the drive associated with the control object, as well as automatic correction of its positioning coordinates. There are three main ways to control the speed - throttle, volumetric and frequency.[1]
Throttle control of the hydraulic drive has the following advantages: ease of implementation, low cost, the possibility of smooth regulation in a wide range. However, it has significant disadvantages: low efficiency, caused by large energy losses, as well as an increase in the temperature of the working fluid, which leads to the need to use heat exchangers.
Compared to throttle, when using volume control, there is no heating of the working fluid, and it also has a high efficiency. The main disadvantage of volumetric regulation is the high cost associated with the complexity of the design of variable pumps.
In turn, frequency regulation is characterized by high efficiency and ease of implementation of control automation, as well as the absence of heating. However the range of regulation is limited by the capabilities of the frequency controller, and the value of the operating range of the pump speed. In terms of cost, it is inferior to throttle control.
One of the examples of an adaptive pneumatic drive is given in our article [2], where a method for controlling the movement of the output links of the servo system of pneumatic drives and the actuator associated with it is considered. Improving the dynamic and quality characteristics is achieved through a proportional-integral-derivative (PID) controller. A mathematical model created in the Simulink graphical simulation environment based on the Matlab program showed that as a result, the positioning process time is reduced, which leads to a decrease in the cycle time, and as a result, an increase in productivity. Also, by reducing the pressure in the piston cavity, energy costs are also reduced.
Also, to improve accuracy and efficiency, an adaptive PID controller is used, which adjusts its parameters in real time in accordance with the adopted model and control goal.
Carriage point moderators can be attributed to adaptive hydraulic and pneumatic drives. Point moderators are superior to older type moderators. The operational and design disadvantages of older types of retarders include: complexity, bulkiness, excessive specific material consumption, large inertia and instability of braking characteristics. In turn, point-type wagon retarders do not consume external energy, they do not require a traditional automated control system, since they operate in the "self-tuning" mode. Such moderators include TDJT-101, which was investigated in our work. Modeling and research was performed in the Simulink environment. The obtained dynamic characteristics are consistent with those presented in the operating instructions for the TDJT-101 jack-type retarder. At different speeds and masses of the car, the simulation results showed that the time of transients varies greatly. This negatively affects the speed of such deceleration systems for wagons and the marshalling fleet as a whole, which requires the development of an adaptive retarder control system.
The development and implementation of adaptive hydraulic drives in mobile machines for harsh operating conditions is becoming an urgent task. The key element of these machines is the proportional valve, which is used in gearboxes and attachments. Proportional valves on the market are designed for flow rates from 40 l/min, which do not meet the criteria for energy efficiency and control accuracy. In this regard, the team of authors is faced with the task of designing a proportional valve for low costs, manufacturing a prototype, and studying its characteristics as part of an adaptive gearbox drive system.
