ВНЕДРЕНИЕ БЕРЕЖЛИВОГО ПРОИЗВОДСТВА С ИСПОЛЬЗОВАНИЕМ ТЕХНИКИ VSM И ИМИТАЦИОННОГО МОДЕЛИРОВАНИЯ НА ПРИМЕРЕ ОРГАНИЗАЦИИ ПО ПРОИЗВОДСТВУ ДВЕРЕЙ И ОКОН
Секция: 8. Менеджмент
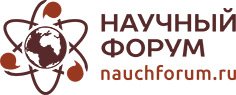
I Студенческая международная заочная научно-практическая конференция «Молодежный научный форум: общественные и экономические науки»
ВНЕДРЕНИЕ БЕРЕЖЛИВОГО ПРОИЗВОДСТВА С ИСПОЛЬЗОВАНИЕМ ТЕХНИКИ VSM И ИМИТАЦИОННОГО МОДЕЛИРОВАНИЯ НА ПРИМЕРЕ ОРГАНИЗАЦИИ ПО ПРОИЗВОДСТВУ ДВЕРЕЙ И ОКОН
В последние годы многие организации внедряют принципы бережливого производства (lean production) с целью достижения недосягаемого конкурентного преимущества. Однако не все смогли достичь своих целей. Многие компании, которые сначала заявляют о том, что выигрывают от бережливого производства, часто выясняют потом, что улучшения остаются локальными. Одна из причин заключается в том, что менеджмент имеет неполное понимание принципов бережливого производства и, как результат, не может извлечь все выгоды, которые смогла получить Тойота.
Другие причины неудач включают в себя недостаток (или отсутствие) понимания менеджерами того, как осуществлять бережливое производство, какие изменения произойдут в организации с внедрением бережливого производства, как бережливое производство повлияет на показатели деятельности организации и т. д.
Ответить на эти вопросы может техника бережливого производства под названием Value Stream Mapping (VSM) — Карта Потока Ценности — совместно с имитационным моделированием на специальных компьютерных программах. VSM представляет собой технику, которая используется для построения и анализа материального и информационного потоков, которые присутствуют при удовлетворении требований клиента. Рассмотрим данную технику на примере условной компании ABC, которая производит окна и двери. Суммарная производственная мощность — около 100.000 окон в год. С учетом того, что компания производит окна по индивидуальным заказам, данное производство попадает под категорию единичного или мелкосерийного производства.
В последнее время строительный сектор в России находится на подъеме. Естественно, спрос на окна и двери также растет. Например, спрос на одном из заводов компании ABC по прогнозам увеличится с 40 окон до 60 окон в день. Проанализировав производственную систему, менеджеры компании обнаружили несколько областей, где возможны значительные улучшения. Например, уровень производства, который измеряется в площади изделий за смену, составляет 160 квадратов за 8-часовую смену. Этот показатель является достаточным только для удовлетворения существующего спроса в 40 окон в день; при этом завод страдает от недостатка мощностей для удовлетворения спроса в будущем. Другой аспект рассматриваемой организации заключается в том, что уровень запасов внутри предприятия находится на относительно высоком уровне. В настоящее время незавершенное производство (НЗП) на всем заводе занимает 1000 квадратов в день, т. е. в среднем 125 квадратов перед каждой рабочей станцией (всего их 8). Из-за низкого уровня производства, низкой мощности и высокого уровня запасов топ-менеджмент ABC планирует внедрить принципы бережливого производства с целью остаться конкурентоспособными и удовлетворять постоянно растущий спрос без особого увеличения ресурсов за счет устранения излишних трат, мешающих нормальному функционированию.
Менеджмент ABC начинает реализацию бережливого производства. В качестве отправной точки, для обеспечения понимания новых принципов и процедур бережливого сотрудниками ABC, были организованы необходимые тренинги по таким инструментам и техникам бережливого производства, как 5S (система организации и рационализации рабочего места — сортировка, соблюдение порядка, содержание в чистоте, стандартизация, совершенствование), Кайзен (непрерывное улучшение), VSM, Muda (излишние траты) и др.
Следующий этап — изображение VSM, которое включает два шага: на первом отображается карта текущего состояния, а на втором — карта будущего состояния. В случае рассматриваемой организации текущее состояние VSM отображено на Рисунке 1.
Рисунок 1. Карта потока ценностей (текущее состояние)
На Рисунке 1 можно увидеть, что время, добавляющее ценность, равно только 1476 секундам, в то время как время на производство составляет около 12,53 дней или 360864 секунд. Соотношение равно 0,0041, что ясно говорит нам о том, что производственный процесс включает в себя деятельность, не добавляющую ценности. Следующий шаг состоит в вычислении такта (допустимого времени изготовления одного продукта). В настоящее время спрос равен 40 окнам или 160 квадратам. Завод работает в одну смену по 8 часов (это время не включает в себя перерывы на обед — 30 минут — и перерывы на чай — 15 минут). Таким образом, доступное время находится так: 8 х 60 х 60 = 28800 секунд. Таким образом, такт для текущего состояния равен 8 х 60 х 60/160= 180 секунд/кв.м. Из Рисунка 1 также можно увидеть, что такие этапы, как резка профиля, обработка, сборка и сварка имеют меньший цикл по сравнению с тактом, а время, необходимое для остальных стадий, больше такта. Из-за этого происходит хранение избыточного количества запасов в цехах.
Однако если будущий спрос составит 60 окон в день, или 240 квадратов, несоответствие между циклами различных стадий переработки и тактом будет очень большим. Такт в соответствии с будущим ожидаемым спросом будет равен 8 х 60 х60/240 = 120 секундам, и в этом случае только первый этап сможет удовлетворить потребительский спрос, поскольку он имеет самое низкое время цикла — 85 секунд.
Поэтому для устранения проблем, вызванных текущим состоянием VSM, менеджеры организации выбрали следующие элементы бережливого производства для реализации: 5S для организации рабочего места; Кайзен для упрощения процесса комбинированием/устранением/упрощением операций; обеспечение ритмичности производственного процесса для достижения непрерывного производственного процесса; изменение планировки для уменьшения числа действий рабочих и ненужных транспортных операций.
Они также разработали будущее состояние VSM для визуализации их видения организации после устранения всех ненужных трат с помощью перечисленных элементов бережливого производства. Рисунок 2 иллюстрирует будущее состояние VSM. Из данной карты видно, что после применения упомянутых техник бережливого производства НЗП сокращается до среднего уровня в 20 квадратов, время на производство сокращается до 1,4 дня, общее время цикла становится равным 740 секундам, время такта — 120 секундам и норма обработки вырастает до 1,8 %. Однако несоответствие между циклами различных стадий переработки и тактом все еще сохраняется, но данное различие уже не столь велико, как до внедрения бережливого производства.
Рисунок 2. Карта потока ценностей (будущее состояние)
Итак, изобразив карты текущего и будущего состояний, можно сделать вывод о преимуществах и недостатках техники. VSM позволяет:
· визуализировать и ясно видеть весь поток;
· обнаружить излишние траты в потоке ценности;
· установить связь между информационными и материальными потоками;
· понять, какой будет организация в будущем; все ли мероприятия, направленные на повышение эффективности, осуществлены правильно.
У VSM также есть ряд недостатков:
· VSM — это статичный инструмент по своей природе, и он может отразить состояние цеха только в какой-то определенный день.
· Карта будущего состояния изображается с предположением, что все проблематичные зоны будут полностью разрешены. Однако на практике вся проблема целиком может оказаться неразрешенной.
· Создание карты потока создания ценности вручную, отображение и внесение в неё каких-то изменений — трудоемкий процесс, требующий много времени.
Данные, которые были собраны в ходе развития текущего состояния VSM, используются для разработки имитационной модели с помощью специальных компьютерных программ. На Рисунке 3 изображен снимок имитационной модели текущего состояния VSM. На Рисунке 4 изображен снимок имитационной модели будущего состояния VSM.
Благодаря использованию имитационной модели мы можем видеть, как изменилась планировка производственного цеха в соответствии с выбранными техниками бережливого производства (VSM, процесс упрощения, обеспечение ритмичности производственного процесса, изменение планировки, укрупнение технологических операций, сокращение площадей цеха). В соответствии с имитационной моделью, расстояние между пунктом хранения материалов и пунктом отправки готовой продукции сократилось. Перепланировка позволяет сократить транспортные операции, количество и расстояние передвижений рабочих, высвобождает значительную площадь и в целом сокращает время прохождения изделий через цикл операций. Спланированный таким образом цех легче контролировать и в случае возникновения сбоя можно быстрее выявить его источник и незамедлительно исправить ситуацию.
Рисунок 3. Снимок имитационной модели текущего состояния VSM
Рисунок 4. Снимок имитационной модели будущего состояния VSM
В Таблице 1 приведено сравнение выполненных мер для текущего и будущего состояния VSM после проведения имитационного моделирования.
Таблица 1.
Сравнение выполненных мер для текущего и будущего состояния VMS
Показатель работы |
Текущее положение |
Будущее положение |
Спрос за день 1. В окнах 2. В квадратных метрах |
40 160 |
60 240 |
Первоначальный запас на начало моделирования (в днях) 1. Резка профилей 2. Дренажная трассировка 3. Укрепление 4. Сварка 5. Сборка 6. Шлифование 7. Стеклование 8. Упаковка и отправка |
1120(7) 150(0.94) 85(0.53) 120(0.75) 250(1.56) 125(0.78) 100(0.63) 55(0.34) |
240(1)
30(0.125)
20(0.083) 20(0.083) 20(0.083) 20(0.083) |
Общее время цикла (в мин.) |
63.36 |
42.72 |
Длительность цикла изготовления изделия, дн. |
37.78 |
12.68 |
Норма обработки |
0.17 |
0.39 |
Время такта (в секундах) |
180 |
120 |
Продолжительность цикла (в секундах) 1. Резка профилей 2. Дренажная трассировка 3. Укрепление 4. Сварка 5. Сборка 6. Шлифование 7. Стеклование 8. Упаковка и отправка |
85 152 58 150 320 296 205 210 |
147
120
146 132 110 115 |
Общие запасы незавершенного производства после 30 дней использования модели 1. В окнах 2. В квадратных метрах |
4992 1248 |
1196 299 |
Произведено частей после 30 дней использования модели 1. В квадратных метрах 2. В окнах |
7956 1989 |
10535 2561 |
Расстояние, пройденное окном (в метрах) |
62.5 |
54 |
Численность рабочей силы |
24 |
17 |
Используемая площадь цеха (в квадратных метрах) |
1587 |
720 |
Помимо тех результатов, которые получены с помощью имитационной модели, организация сможет достичь, ряд других преимуществ:
· Расстояние между пунктом хранения материалов и пунктом отправки готовой продукции сократилось. При старой планировке это расстояние было равно 62 метрам. После изменения планировки расстояние сократилось на 9 метров и составило 53 метра.
· Уровень незавершенного производства также в среднем удалось сократить на 76 %. Например, количество незавершенного производства после 30 дней моделирования было равно 1248, в то время как в будущей модели данное количество составило 299.
· Внедрение Кайзен и обеспечение ритмичности производственного процесса привело к сокращению продолжительности цикла на различных этапах производственной линии. Таким образом, общее число изделий, которые могут быть произведены, может увеличиться на 28,5 %. Если дальнейшие процессы для улучшения будут предприняты, то вся организация может стать более продуктивной, и тогда это сможет удовлетворить будущий спрос в 85 окон в день с существующими мощностями.
Таким образом, использование имитационных моделей, внедрение некоторых инструментов и техник бережливого производства, таких, как обеспечение ритмичности производственного процесса, 5S и т. д., влияют на показатели производительности предприятия. Это было доказано путем сравнения показателей текущего и будущего состояния VSM. Оказалось, что произошли существенные улучшения в производительности, а также сокращение запасов, времени цикла и т. д., при сохранении существующих мощностей. Таким образом, эти модели являются эффективным инструментом для менеджеров и инженеров для демонстрации того, как их производство, предприятие будет выглядеть в будущем после внедрения техник и принципов бережливого производства. Можно сделать вывод о том, что рассмотренная организация находится на правильном пути в реализации бережливого производства, и если менеджеры и инженеры организации будут внедрять его элементы правильно, то компания повысит свою конкурентоспособность.
Список литературы:
1. Стерлигова А.Н., Фель А.В. Операционный (производственный) менеджмент. Учеб. пособие для вузов — М.: Инфра-М, 2009. — 187 с.
2. John Shook, Mike Rother. Misunderstandings about value-stream mapping, flow analysis, and takt time // Lean Enterprise Institute, One Cambridge Center — 2009. Vol. 2. № 3. P. 13—19
3. Peter Hines, Nick Rich. The seven value stream mapping tools / / International Journal of Operations & Production Management — 1997. Vol. 17. № 1. P. 46—64
