БЕРЕЖЛИВОЕ ПРОИЗВОДСТВО, СИСТЕМА 5С
Секция: 8. Менеджмент
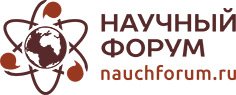
XXI Студенческая международная заочная научно-практическая конференция «Молодежный научный форум: общественные и экономические науки»
БЕРЕЖЛИВОЕ ПРОИЗВОДСТВО, СИСТЕМА 5С
Бережливое производство (lean production) — это одна из концепций управления предприятием, направленная на минимизацию всех возможных издержек. Эта концепция предусматривает участие не только руководства, но и всех остальных сотрудников. Организация должна ставить перед собой задачу — совершенствоваться день ото дня. Именно в этом и заключается основная идея бережливого производства, которая была впервые придумана и применена в конце 20-го века основателем производственной системы автомобильного гиганта Тойота Таиши Оно. Именно он собрал воедино все передовые методы увеличения эффективности производства в стенах завода Тойота.
В бережливое производство входит множество инструментов управления, которые сами по себе просты, но применение их требует некоторых усилий. Одним из самых важных и эффективных является система 5С. Именно она определяет стабильность производимых операций, необходимую для создания и поддержки непрерывных усовершенствований. Главной ее целью является создание ясной, идеально организованной рабочей среды, в которой каждый сотрудник не должен даже задумываться о том, где лежит нужная для работы вещь — всё всегда должно находиться на своем месте.
Если попробовать дать четкое определение данному инструменту, то 5С — это система наведения порядка, чистоты, укрепления дисциплины, повышения производительности и создания безопасных условий труда с участием всего персонала. Данная система позволяет практически без затрат не только наводить порядок на предприятии (повышать производительность, сокращать потери, снижать уровень брака и травматизма), но и создавать необходимые условия для реализации сложных и дорогостоящих инноваций, а также обеспечивать их высокую эффективность за счет радикального изменения сознания работников, их отношения к своему делу.
Данная система называется «5С», так как она включает в себя пять принципов организации рабочего места, которые обеспечивают хороший визуальный контроль над рабочим процессом. Каждое из названий данных принципов в японском языке начинается с буквы «С»:
· Сейри (сортировка): отделить необходимые предметы — инструменты, запчасти, материалы, документы — от ненужных, чтобы в последствии избавиться от последних.
· Сейтон (рациональное расположение): упорядочение оставшихся предметов, то есть необходимо поместить каждую вещь на свое место.
· Сейсо (уборка): сохранять рабочее место в чистоте.
· Сейкецу (стандартизация): быть предельно аккуратным за счет выполнения первых трёх «С».
· Сицуке (совершенствование): соблюдать дисциплину, обеспечивающую выполнение первых четырех «С», чтобы в результате все данные пункты вошли в привычку.
Рисунок 1. Принцип системы 5С
Далее я опишу поподробнее, как на практике выполняются вышесказанные принципы.
Сортировка. Все предметы на производстве сортируют на несколько частей:
· необходимые всегда — предметы, используемые в работе в данный момент;
· необходимые иногда — предметы, используемые в работе, но в данный момент не востребованы;
· ненужные — брак, неиспользуемые инструменты, тара, посторонние предметы.
В процессе сортировки ненужные предметы помечают «красной меткой» и затем удаляют из рабочей зоны.
Рациональное расположение. Расположение предметов всегда должно отвечать требованиям безопасности, качества и эффективности работы. Помимо этого, существует ряд правил расположения вещей:
· легко найти;
· легко взять;
· легко использовать;
· легко вернуть на место.
Уборка. Рабочее место необходимо постоянно держать в полной чистоте. Для этого существует некоторый распорядок действий:
· создание карты или схемы, которая разобьёт все рабочие места на условные зоны;
· определение группы сотрудников, за которыми закрепляется конкретная зона для уборки;
· определение времени уборки — утреннее (5—10 минут до рабочего дня), обеденное (5—10 минут после обеда) или после окончания рабочей смены (по завершению работы, а также во время простоев).
Стандартизация. Данный шаг предусматривает письменное закрепление правил по уходу за рабочим местом, по ходу выполнения работы и других процессов. Необходимо создать рабочие инструкции, которые включат в себя описание пошаговых действий по поддержанию порядка. А также вести разработки новых методов контроля и вознаграждения отличившихся сотрудников.
Совершенствование. Создание привычки бережного ухода за рабочим местом в результате многократного применения всех предыдущих правил. Помимо этого, необходимо непрерывно совершенствовать эту систему ухода.
Основные преимущества данной системы заключаются в следующем:
· снижение невынужденных ошибок в документах;
· создание благоприятной рабочей атмосферы;
· повышение производительности труда;
· увеличение прибыли фирмы, вследствие чего, увеличение заработной платы самих рабочих;
· легкость применения инструмента — нет необходимости в применении никаких новых управленческих концепций и технологий.
Можно увидеть, каких результатов позволяет достичь система 5С на примере научно-производственного объединения «МИР». Данное предприятие создает системы автоматизированного учета энергоресурсов, системы управления энергообъектами, а также производит измерительные приборы.
В 2004 году данная организация начала внедрять систему 5С. Но еще до этого был проведен обучающий семинар с начальниками подразделений, которые в свою очередь ознакомили своих подчиненных. Помимо этого, была создана специальная комиссия, в обязанности членов которой входил контроль над выполнением требований системы. Проверки проводились 2 раза в месяц.
Следует отметить тот факт, что работникам разрешалось не предъявлять для проверки места для личного пользования. Это было сделано для того, чтобы поддерживать доброжелательные отношения между сотрудниками и администрацией. Внедрение проходило в соответствии со всеми ранее сказанными правилами — в 5 этапов.
Было введено «Золотое правило», которое закрепляло ответственность каждого сотрудника за результат своей работы и за результат работы коллектива. Помимо того, была организована единая структура файлов в ПК сотрудников (так называемое «дерево папок»). В результате, в 2006 году была получена работающая система, вносящая, по оценкам специалистов, 16-процентный вклад в улучшение качества продукции.
Более того, на предприятии проводится сбор, так называемых, «новинок»: эффективных решений, которые предлагают сами сотрудники, по поводу устранения различных проблем системы.
Но, как обычно бывает, при внедрении системы существует ряд довольно типичных проблем. Главная проблема — мотивация сотрудников для использования системы 5С. Именно из-за нежелания некоторой части персонала придерживаться данной технологии система была полностью введена на полгода позже, чем планировалось.
Некоторые сотрудники могут считать, что их рабочее место не надо оптимизировать, так как оно и так находится в идеальном состоянии. Задача руководителя заключается в том, чтобы объяснить, почему это не так, и что рабочее место можно улучшить.
Так, для устранения нежелания выполнять требования с сотрудниками был проведен большой объем работ по разъяснению и консультированию, что принесло положительный эффект. Теперь, когда система уже внедрена, позиция у работников изменилась: они недоумевают, как можно было раньше обходиться без соблюдения предложенных требований, ведь они так естественны и удобны.
Кроме того, каждый квартал проводится подведение итогов и награждение лучших подразделений и сотрудников за лучшие рабочие места.
Итоги введения системы получились весьма положительными:
· Любой документ может быть найден за 30 секунд;
· Исключение потерь документов благодаря наличию ответственных за порядок в шкафах с документацией общего пользования;
· Сохранность электронной информации и повышение скорости поиска электронных документов благодаря организации единой структуры хранения информации в ПК каждого подразделения с учетом специфики работы;
· Поддержание высокого уровня дисциплины;
· Улучшение косметического вида офисов и производства;
· Сокращение аварийных простоев благодаря обслуживанию сотрудниками своих рабочих мест;
· Сокращение брака;
· Снижение себестоимости продукции.
Таким образом, можно с уверенностью сказать, что система 5С является весьма эффективной. Несмотря на то, что внедрение занимает немало времени, данный инструмент всегда помогает достичь успеха. Главное, о чем никогда нельзя забывать — это психология персонала. Он должен понимать, что выполняет одну задачу для достижения общей цели, все должны быть настроены на положительный результат.
В заключении хочется сказать, что без внедрения системы 5С другие системы качества будут приносить существенно меньший результат, поэтому рассмотренный инструмент является очень хорошим и эффективным средством для роста качества продукции и услуг предприятия.
Список литературы:
1. http://www.mir-omsk.ru.
2. http://cfin.ru.
3. http://elibrary.udsu.ru.
4. http://ru.wikipedia.org.
