ТИПЫ ПОТЕРЬ НА ПРЕДПРИЯТИИ, АНАЛИЗ ИСТОЧНИКОВ, ПОСЛЕДСТВИЙ, ПУТЕЙ ВЫХОДА
Секция: 8. Менеджмент
лауреатов
участников
лауреатов


участников


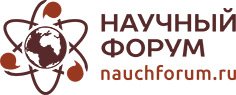
XXIV Студенческая международная заочная научно-практическая конференция «Молодежный научный форум: общественные и экономические науки»
ТИПЫ ПОТЕРЬ НА ПРЕДПРИЯТИИ, АНАЛИЗ ИСТОЧНИКОВ, ПОСЛЕДСТВИЙ, ПУТЕЙ ВЫХОДА
В данной статье будут рассмотрены причины потерь на производственном предприятии, а также их источники и анализ последствий. В дельнейшем при помощи этой статьи можно будет избежать потерь или минимизировать их, если избавиться от них нельзя.
Уменьшения издержек на производстве всегда было актуально для производителей, но вот пути уменьшения не всегда были очевидны.
И в этом случае менеджерам снова приходится возвращаться к анализу производственных расходов. Для начала стоит структурировать расходы, разделить на те, от которых избавится, не получится, т. е. те, которые необходимы, и на те, которые можно убрать. Иными словами, нам нужно избавится от тех процессов, за которые потребитель не будет нам платить, т. е. устранить тот вид деятельности, который не будет добавлять ценности нашему продукту. Если в процессе изготовления существуют такие операции то, именно они и будут, называется потерей.
В современных предприятиях, выявление и снижение потерь становится наиболее приоритетной целью, т. к. от этого зависит эффективность фирмы.
Понятие потерь впервые было услышано от Тайити Оно, выдающийся японский бизнесмен, с 1978 года — председатель совета директоров компании Toyota Spinning and Weaving. Считается отцом производственной системы Тойоты. Он описал семь видов потерь, которые чаще всего встречаются на предприятиях. На японском языке пери называют «мудами». Муда — это означает, отходы, потери, ошибки, убыточная деятельность.
Тайити Оно в своей системе выделил 7 основных видов потерь:
- Потери, связанные с перепроизводством;
- Потери связанные с ожиданием производства;
- Потери из-за лишней транспортировки;
- Потери из-за лишней обработки;
- Потери из-за лишних запасов;
- Потери из-за лишних движений;
- Потери, связанные с дефектной продукцией.
Ожидание, этот вид потерь наименее опасен, поскольку несет за собой минимальный урон предприятию. Потери ожидания, в первую очередь связаны с тем, что процесс планирования и процесс производства не совсем точно связаны между собой, в связи с чем возникает увеличение времени на производства единицы продукции. Особенно, это проблема актуальна для отечественных фирм. В основном, проблема не состыковки плана и процесса связана со сложностью их анализа, ввиду того что приходится учесть множество факторов (количество смен, производительность оборудование, количество заказа, состояние рынка и т. д.). Для этого от предприятия требуется чтобы, ответственные за закупки, производство и сбыт, четко взаимодействовали между собой. Чтобы определить время ожидания нужно провести хронометраж работы персонала и оборудования. Количество простоя за определенный период и будет временем ожидания. Чтобы уменьшить время ожидания работника, во время простоев можно поручить ему не сложную работу, например, уборку. Как правило, возможность улучшения процесса планирование присутствует всегда. И основным путем устранения этой потери будет, выравнивание производственных процессов.
Дефектная продукция. Выпуск продукций, которая не будет отвечать требования потребителя, является очень затратной потерей. Чтобы узнать на сколько выпуск бракованной продукции повлиял на эффективность производства нужно подсчитать затраты на сырье, время работы, утилизация или переработка брака. Источником такой потери выступает: неправильная технология производства, низкое качество сырья, низкоквалифицированный работник, оборудование. Как правило, на производственном предприятии должны существовать службы по контролю за выпуском дефектной продукции. И устранение потерь, связанных с дефектом, в первую очередь начинается с анализа функционирования контролирующих служб. Решением здесь может быть это внедрение контролирующих подразделений на каждый этап перехода продукции от одного процесса к другому. Например, установить датчик, через который будет проходить полуфабрикат, который будет сверять изделие с нормативом.
Лишняя обработка. Потребитель заплатит лишь в том случае, если продукт будет соответствовать всем его требованиям, которые у него в приоритете. Например, человек хочет приобрести мобильный телефон, у него есть ряд требований, которыми он должен обладать. Одно из этих требований, белый корпус у телефона, но вы можете производить только черные, поэтому после того как вы произвели телефон вам придется его перекрашивать в белый цвет чтобы он нашел своего потребителя, потому что телефон уже изготовлен и всем остальным требованиям он соответствует. Перекраска в данном случае будет лишней обработкой, а это увеличение времени изготовления, лишние затраты сырья и труда. Источник такой потери будет: не понимания того чего хочет потребитель, несовершенство технологии и отсутствие стандарта. Прежде чем выполнить заказ, производитель должен четко понимать какими свойствами должен обладать продукт чтобы в итоге он нашел своего потребителя. Это понимание должно быть прописано в стандарте для работника. В свою очередь стандарт должен быть отражен в технологической карте, по которой рабочий будет выполнять свою работу шаг за шагом. Чтобы определить существует ли такая проблема как лишняя обработка, нужно выяснить какие свойства продукта у потребителя в приоритете, а какие он ставит на второй план или вовсе не использует. Что бы избавится от такой потери нужно разработать стандарт продукта, в котором не будет лишних операции, которые бы добавляли не нужную ценность продукту, а для этого необходимо тщательно изучить желание потребителя.
Лишние запасы. На первый взгляд покажется, что запасы несут за собой наименьшие потери, а в некоторых случаях и вообще не несут вреда. Но если разобраться, то, можно найти много минусов, один из них, это то, что, со временем все теряет свою стоимость, и запасы не являются исключением. Для хранения запасов также нужно какое-то помещение, которое молотого что его нужно найти, его нужно обслуживать. А если у вас большое количество запасов и много помещений где они хранятся, то отсюда снова вытекает еще одна проблема, связанная с поиском на складах нужного материала. С другой стороны, запасами можно компенсировать нестабильность спроса на продукцию. Источником избыточных запасов может быть: выпуск больших партий продукции и, несогласованность системы планирования производства и системы ответственной за количество поставок материалов. Вследствие, чего происходит увеличение затрат на содержание, затраты на увеличение площади, затраты на поиск продукции, а если еще и товар будет поврежден при транспортировке, тоже лишние затраты. Что бы вычислить потери от запасов, нужно определить сколько на складе материалов, которые не будут востребованы до ближайшей поставки, нужно посчитать затраты на содержание и обслуживание помещения где хранятся запасы. Путем решения выхода из этой проблемы будет, сокращение партии производства, наладка системы планирования производства и поставок.
Перепроизводство. Сперва может показаться что перепроизводство не может являться потерей, а даже наоборот плюсом. Потому что многие предприятия пытаются наращивать производство, с целью увеличения прибыли. И в погоне за большим выпуском продукции не учитывают, что количество продукции, которую готовы купить потребители определяется спросом на рынке. В итого большое количество произведенного товара залеживается на складах. В следствии чего фирма вынуждена быстро реализовать залежавшийся, а иногда и испорченный товар. Иногда фирма пытается не то что выйти в ноль, а хотя бы минимизировать убытки. Перепроизводство считается самой опасной потерей, так как, из нее вытекают все остальные, но ее и проще всех остальных выявить и исключить, нужно просто не производить лишнего, а производить только под заказ. Источник в данном случае будет: производство большими партиями, опережающее производство, не стабильное качество выпускаемой продукции, избыток оборудования. В последствии, и происходит избыток готовой продукции, плохое качество, излишние расходы на сырье и материалы. Определить потери от перепроизводства можно просто посчитав количество не востребованной продукции, которая будет залеживаться на складах. Путем решения будет только равномерная нагрузка на производственную линию.
Транспортировка. Полностью от перемещения избавиться невозможно, так как, между операциями материалы или полуфабрикаты необходимо перемещать от одного пункта к другому или увезти уже готовую продукция в специальное помещение, чтобы она на складировалась возле рабочего места. В это случае, можно лишь максимально сократить затраты на транспортировку. Отсюда можно сделать вывод что без потерь на транспортировку нельзя обойтись. Источником лишней транспортировки будет выступать: большое расстояние между пунктами передачи, нерациональное размещение производственных станков, отдаленность складов. В последствии это может вызвать: затраты на транспортировку, на поиск материалов на складах, повреждение продукции. Что бы выявить потери от лишней транспортировки нужно посчитать стоимость перемещений т. е. затраты на горючее, электроэнергию, и т. д. Сюда еще можно включить стоимость продукции, которая было испорчена из-за транспортировки. Чтобы минимизировать затраты на транспортировку нужно: оптимально расставить производственные участки чтобы, путь транспортировки был максимально коротким и безопасным. Также желательно избавиться от удаленных запасов, но, если они присутствуют, пускай будут под рукой.
Лишние движения. Иными словами — это суета. Если не приглядываться, то покажется что, у работника кипит работа. Но если присмотреться, то сразу понятно, что эта хаотичность действии не добавляет ценности продукту. Такую потерю легко заметить и не менее, сложнее устранить. Источник: неправильно организованное рабочее место, несогласованность действий и отсутствие четкой инструкции. Вследствие чего происходит снижение производительности, быстрая утомляемость, травматизм. Выявить проблему такого типа поможет хронометраж работы рабочего. Что бы выйти из этой ситуации нужно: повысить квалификацию рабочих, оптимизировать рабочий процесс, рациональная расстановка рабочего места.
Если проанализировать российские предприятия, то наиболее эффективно систему бережливого производства применило производственное предприятие ОАО «Камаз». После внедрения бережливого производства, предприятия значительно сократила свои потери, тем самым увеличила получаемую прибыль. В последствии применения систем, у предприятия, на 1 рубль затрат приходилось более ста рублей прибыли. Чтобы достигнуть такого успеха, руководству компании нужно было обучить весь персонал, потому что без массового вовлечения эффекта от внедрения бережливого производства будет мало. Но тут встает вопрос, как обучить весь персонал без отрыва от производства? Предприятие идет на хитрость и берется обучать персонал в период кризиса, тем самым ликвидируя возможность срыва производства. За период с 2006 года по 2011 год, предприятием было обучено принципам бережливого производства почти 90 тысяч человек, стандартизировано порядка 2500 операции, освобождено около 364 тысяч кв. м площади, высвобождено 4500 ед. оборудования, внедрено 7 тысяч проектов. Учитывая все это предприятия получило экономический эффект в размере почти 15 миллиардов рублей.
Список литературы:
- Тайти Оно — [Электронный ресурс] — Режим доступа. — URL: https://ru.wikipedia.org/wiki/Оно,_Тайити (Дата обращения 24.04.2015).
- Бережливое производство — [Электронный ресурс] — Режим доступа. — URL: https://ru.wikipedia.org/wiki/Бережливое_производство (Дата обращения 24.04.2015).
- Принципы организации бережливого производства промышленного предприятия — [Электронный ресурс] — Режим доступа. — URL: http://www.rae.ru/monographs/188-5932 (дата обращения 24.04.2015).
- Бережливое производство на КАМАЗе — [Электронный ресурс] — Режим доступа. — URL: www.youtube.com/watch?v=ubcfLp8Zj2g (дата обращения 24.04.2015).
