Экспериментальное определение уравнения для расчета оптимальных скоростей обработки точением тонкостенных алюминиевых деталей
Секция: Технические науки
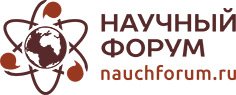
XXIX Студенческая международная научно-практическая конференция «Технические и математические науки. Студенческий научный форум»
Экспериментальное определение уравнения для расчета оптимальных скоростей обработки точением тонкостенных алюминиевых деталей
В статье [1] рассмотрена проблема подбора технологических условий для обработки тонкостенных деталей из алюминиевых сплавов. Показано, что возникающие остаточные напряжения при получении заготовок и их дальнейшей механической обработке приводят к нежелательным и недопустимым изменениям размеров и формы деталей. Поэтому целесообразно использовать оптимальные режимы резания, на которых значение сил резания минимально, а значит и минимальны остаточные напряжения и деформации деталей.
Для изготовления деталей, подвергающихся короблению, часто используется дюралюминиевый сплав Д16Т. С использованием графоаналитического метода профессора Силина С. С. [2], можно получить уравнение обрабатываемости для расчета оптимальной скорости резания при точении для сочетания материалов инструмента и заготовки ВК8-Д16Т следующего вида:
, (1)
где а1– толщина среза, м; t, S – соответственно глубина резания и подача, м; а – температуропроводность обрабатываемого материала, м2/с; сρ – удельная объемная теплоемкость обрабатываемого материала, Дж/(м3 · с · град.).
Использование зависимости (1) для расчета оптимальных режимов обработки не совсем корректно, т. к. на практике обработка детали выполняется инструментами зарубежных фирм Iscar, Sandvik Coromant и др., поэтому данную зависимость необходимо преобразовать с учетом особенностей современных режущих инструментов. Современные режущие инструменты отличаются от использованных ранее в 70-х, 80-х годах прошлого века наличием стружколомающих поверхностей, износостойких покрытий с низкими коэффициентами трения, новой геометрией режущего клина, маркой твердого сплава и др. Для учета особенностей современной твердосплавной пластины, например IC907 SNMG120408-TF, необходимо получить уточненное уравнение для расчета минимальной стабилизированной силы резания при оптимальной температуре в зоне резания в следующем виде:
Pzmin = kп ·682·S0,71 ·t0,94 (2)
Для определения коэффициента kп в уравнении (2) необходимо выполнить ряд экспериментальных работ. Произведена токарная обработка тонкостенной алюминиевой заготовки, показанной на рисунке 1.
Рисунок 1. Обрабатываемая кольцевая заготовка
Обработка заготовки производилась на универсальном токарно-винторезном станке NH 22. Составляющие силы резания Pz, Ру и Рх регистрировались универсальным динамометром УДМ–600, подключенным посредством 10-разрядного аналого-цифрового преобразователя к ПЭВМ. Это позволило существенно снизить погрешности измерения и упростить дальнейшую статистическую обработку результатов. Для определения температуры резания измерялась термо-ЭДС естественной термопары заготовка-резец, образующейся в процессе резания. На рисунке 2 представлена установка для проведения экспериментов с приспособлением для закрепления кольцевых заготовок.
Экспериментальные исследования проводились в два этапа. На первом этапе выполнялась токарная обработка кольцевых заготовок на заводских режимах резания инструментами из твердого сплава ВК8, IC907 и IC20 (без покрытия). Цель эксперимента – получить значение поправочного коэффициента kп для уравнения (2). Режимные параметры обработки и результаты экспериментов приведены в таблице 1.
Рисунок 2. Экспериментальная установка на базе токарного станка NH 22
На втором этапе исследования по уравнению (1), в котором учтено влияние твердосплавного инструмента из сплава IC907 по сравнению с инструментом из сплава ВК8 была определена оптимальная скорость для инструмента из сплава IC907.
Таблица 1.
Результаты экспериментов
№ |
Инструментальный материал |
IC20 SNMG120408-GN |
IC907 SNMG120408-TF |
IC907 SNMG120408-TF |
ВК8 |
ВК8 |
1
|
Геометрия инструмента |
α = 5° γ=10° φ= φ1=45° r=0,8 мм |
α = 10° γ=10° φ=45°; φ1=20° r=0,8 мм |
|||
2 |
Скорость резания v, м/с |
4,4 |
4,4 |
5,6 |
5,6 |
4,4 |
3 |
Глубина резания t, мм |
0,5 |
||||
4 |
Подача инструмента S, мм/об |
0,1 |
||||
5 |
Сила резания Pz, Н |
55 |
29 |
48 |
65 |
71 |
6 |
Сила резания Pу, Н |
16 |
11 |
14 |
– |
– |
7 |
Сила резания Pх, Н |
6 |
2,8 |
5 |
– |
– |
Затем одна заготовка из алюминиевого сплава была обработана инструментом из твердого сплава IC907 на скорости v = 4,4 м/с, применяемой в заводском технологическом процессе, а другая заготовка из алюминиевого сплава была обработана на оптимальной скорости vО = 5,6 м/с, рассчитанной по уравнению обрабатываемости (1).
Результаты экспериментов по обработке заготовок резанием показали следующее:
1) Тангенциальная составляющая силы резания Pz при обработке материала инструментом из сплава IC907 снижается на 26% по сравнению с инструментальным сплавом ВК8 при прочих равных условиях, что дает возможность использовать поправочный коэффициент kп = 0,74 в полученном уравнении обрабатываемости. Уравнение обрабатываемости для сочетания Д16Т– IC907 имеет следующий вид:
(3)
2) составляющие силы резания при обработке материала инструментом из сплава IC907 ниже сил резания на 30-50% по сравнению с обработкой сплавом IC20 (без покрытия) при прочих равных условиях.
Выводы
1. Тангенциальная составляющая силы резания Pz при обработке заготовки инструментом из сплава IC907 снижается на 26% по сравнению с инструментальным сплавом ВК8 при прочих равных условиях, составляющие силы резания при обработке заготовки инструментом из сплава IC907 ниже сил резания на 30-50% по сравнению с обработкой сплавом IC20 (без покрытия) при прочих равных условиях.
2. Оптимальная скорость резания, определенная расчетным путем по полученному уравнению обрабатываемости выше скорости резания, назначенной в заводском технологическом процессе, что обеспечивает повышение производительности обработки при одновременном повышении стойкости режущего инструмента.
