Повышение эффективности обработки отверстий в деталях оснастки
Секция: Технические науки
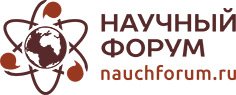
XXXIII Студенческая международная научно-практическая конференция «Технические и математические науки. Студенческий научный форум»
Повышение эффективности обработки отверстий в деталях оснастки
В настоящее время в цехе инструментальной оснастки изготавливается широкая номенклатура корпусных и крепежных деталей, деталей несущих конструкций, а также деталей оснастки для подготовки производства.
На участке цеха, более 85% процентов деталей оснастки переведены на высокопроизводительные многоцелевые станки с ЧПУ. Предприятие закупает новое оборудование и внедряет новые технологии, что расширяет номенклатуру применяемой оснастки.
Детали оснастки имеют множество отверстий, разных по типу конструкции и размеров, а также требованиями к точности и качеству поверхностей. В зависимости от назначения, отверстия служат под крепежные изделия (болтовое и винтовое соединение), под технологические колонки для фиксации и взаимного ориентирования деталей оснастки относительно друг друга, под штифтовое соединение, осей, штырей и так далее.
На рисунке 1 приведен пример детали оснастки «Основание», которая изготавливается в цехе на высокопроизводительных станках с ЧПУ.
Рисунок 1. Основание в приспособлении для выкладки кожуха
В процессе разработки технологического процесса (ТП) и управляющей программы (УП), систематически встречаются определенные типы отверстий, для окончательной обработки которых применяются разные методы (фрезерование, развертывание, растачивание). И как показывает практика, методы окончательной обработки назначаются по-разному, исходя из личного опыта каждого технолога.
Например, на высокопроизводительном многоцелевом станке с ЧПУ, окончательная обработка отверстия диаметром 18 мм, глубиной 40 мм с точностью H по 7 квалитету может производиться следующими методами: фрезерование по круговой интерполяции, развертывание и чистовое растачивание. Заданные требования по качеству выполнены, но отверстие было изготовлено тремя разными методами.
Для назначения эффективного метода обработки отверстия, позволяющего добиться требуемых параметров, необходимо знать назначение отверстия, а также возможности режущего инструмента и оборудования.
На сегодняшний день, отсутствует классификация изготавливаемых отверстий в цехе. Также нет четких рекомендаций по изготовлению систематически встречаемого типа отверстия с вариативностью методов окончательной обработки.
В совокупности, данная проблема приводит к отсутствию единообразия процесса изготовления на типовые отверстия в деталях, производимых в цехе.
Описанные в источниках [1, 2] типы и классификации отверстий содержат сокращенную информацию для общего машиностроения. Для определения возможных методов обработки, необходимо разработать классификацию отверстий в цехе по параметрам обрабатываемого диаметра, глубины, точности и шероховатости.
«Традиционные» методы обработки, описанные в литературе [1, 2] рассмотрены для универсального оборудования с применением стандартного инструмента. В нынешних реалиях, с использованием современного оборудования и инструмента, информация, касаемая точностных и качественных характеристик режущего инструмента и производительности оборудования является неактуальной.
Цель работы в повышении эффективности обработки отверстий в деталях, изготавливаемых в цехе с применением многоцелевых станков с ЧПУ.
Для достижения поставленной цели, необходимо решить следующие задачи:
1. Провести анализ и разработать классификацию изготавливаемых отверстий.
2. На основании анализа возможных и применяемых методов, составить эффективные технологии изготовления типовых отверстий и определить тип отверстий с вариативностью методов окончательной обработки, в условиях цеха.
3. Определить эффективность методов (фрезерование, развертывание, растачивание) при изготовлении отверстий с вариативностью окончательной обработки в условиях цеха.
В процессе рабочей деятельности, был проведен анализ более 50 сборочных единиц приспособлений (штампы, пресс-формы, форм-блоки, приспособления для остекления и т.д.) и более 150 наименования деталей, изготовленных в цехе.
Была рассмотрена конструкция отверстий в приспособлениях и прилегающие спецификации к чертежам.
На основании описанных в литературе [1-3] типов и классификаций отверстий, а также проведенного анализа сборочных единиц изготавливаемой оснастки, была разработана классификация отверстий, изготавливаемых в цехе, см. рисунок 2.
Рисунок 2. Классификация изготавливаемых отверстий в цехе
Отверстия, определенные в классификации, подразделяются на 4 типа:
- Крепежно – резьбовые отверстия (обозначение А и B) - данный тип отверстий предназначен для болтового и винтового сопряжения деталей;
- Установочные отверстия (обозначение С) - данный тип отверстий предназначен для фиксации соединения и взаимного ориентирования деталей с помощью технологических пальцев, штифтового соединения, штырей и осей;
- Направляющие отверстия (обозначение D) - данные отверстия обеспечивают точное направление и взаимное ориентирование деталей с помощью технологических колонок;
- Направляющие отверстия (обозначение E) - данные отверстия изготавливаются для запрессовывания втулок под пальцы и технологические колонки под направляющие.
На основании проведенного анализа возможных технологий изготовления отверстий, а также разработанной классификации (см. рисунок 2) и имеющегося инструментального оснащения в цехе инструментальной оснастки АО «У-УАЗ», были составлены технологии изготовления типовых отверстий, с целью определения типа отверстия с вариативностью методов окончательной обработки.
- Крепежно – резьбовые отверстия: изготовление данной группы отверстий не требует высоких точностных характеристик и качества поверхности, что позволяет производить обработку типовыми операциями.
- Установочные отверстия: изготовление установочных отверстий требует высоких точностных характеристик и качества поверхности, так как имеют глубину L/D>3, где D – диаметр фрезы (наибольший диаметр 16 мм.) и шероховатость Ra 0.4 мкм. Данные отверстия рекомендуется обрабатывать предварительными получистовыми проходами методом фрезерования, чтобы снизить увод оси отверстия. Добиться высоких требований к шероховатости (Ra 0.4 мкм) возможно только методом развертывания.
- Направляющие отверстия: требования, предъявляемые к точности и качеству поверхностей для направляющих отверстий высокие, точность 7 квалитет (редко 9) с шероховатостью Ra 0.8-1.6 мкм. К данным отверстиям, нередко предъявляются требования к перпендикулярности и соосности оси. Диапазон диаметров направляющих отверстий 5-50 мм, и глубины 8-74 мм. Что увеличивает варианты окончательной обработки (фрезерование, развертывание, растачивание).
Проведенный анализ позволил сделать следующее заключение, что отверстия диаметром 18-20 мм, глубиной 38-48 мм, точностью Н7 и шероховатостью Ra 0.8 мкм являются типом отверстия с вариативностью методов окончательной обработки, так как все три метода способны обеспечить точностные и качественные характеристики на заданные параметры глубины и диаметра.
Данные отверстия систематически встречаются в деталях оснастки, изготовляемых в цехе. При разработке ТП и УП появляются спорные моменты, касаемо назначения наиболее эффективного метода окончательной обработки. Исходя из этого, необходимо определить эффективность трех методов обработки для данной группы отверстий.
От назначенного метода обработки отверстия в детали зависит эффективность использования технических возможностей производства, применяемого оборудования и инструмента. Производственный процесс можно рассматривать как затраты времени на изготовляемую продукцию. Эффективность изготовления детали имеет прямую зависимость от применяемых методов обработки на станке, и в соответствии с ГОСТ3.1109, состоит из следующих критериев:
1. Нормы штучного времени (Тшт.).
2. Нормы подготовительно заключительного времени (Тп.з).
3. Затраты на инструмент.
В ходе проведения эксперимента, была рассмотрена деталь «Плита нижняя» из материала Ст3 (см. рисунок 3). Выполняемая операция: обработка двух отверстий Ø20 (Н7), длиной l=45 c шероховатостью поверхности Ra 0.8 мкм. Заготовка – поковка, масса 37.3 кг. Станок – высокоскоростной многоцелевой станок с ЧПУ СИГАС ВС-168.
Рисунок 3. Нижняя плита гибочного штампа (красным выделены два отверстия под технологические колонки)
Инструментальное оснащение.
Сверление: Гидравлический патрон с хвостовиком DIN69871, 50ER40 SHORT»; цанга ER40 SEAL 15-16 JET2; твердосплавное сверло Corodrill 460.1-1600-120A1-XM GC34.
Фрезерование: Термопатрон DIN69871-SRKIN; фреза корпусная Widia M270TD016A16L160; пластина M270HF16; цельная твердосплавная фреза Widia, серия 571816006MT.
Развертывание: Патрон TM-HA04-93020-630547; развертка серии Cororeamer 435.B-2000-A1-XF H10F.
Растачивание: Патрон для соединения MB с коническим хвостовиком DIN69871; головки для чистового растачивания BHF MB16-MB50; державка IHRF; пластина CCMT 060204-14.
На основании проведенного хронометража операций и произведенных расчетов нормы штучного и подготовительно – заключительного времени, затрат на инструмент, можно сделать заключение, что при окончательной обработке отверстий с вариативностью методов (Ø18-20; точность Н7; длиной 38-48 мм; шероховатостью Ra 0.8 мкм), эффективность применения метода фрезерования выше, на основании следующих критериев:
1. Норма штучного времени.
Норма штучного времени при методе фрезерования – 24 мин. ниже, чем при развертывании – 26,8 мин. и растачивании - 24.7 мин, см. рисунок 4. Небольшая разница заключается в том, что меняется только окончательная операция основного времени.
Рисунок 4. Зависимость нормы штучного времени (Тшт.) от метода окончательной обработки отверстий
2. Подготовительно – заключительное время.
Затрачиваемое подготовительно – заключительное время при методе фрезеровании – 27.8 мин. ниже, чем при растачивании - 54.2 мин. и развёртывании - 29.7 мин, см. рисунок 5.
Рисунок 5. Зависимость подготовительно - заключительного времени (Тп.з) от метода окончательной обработки отверстий
Это обусловлено трудоёмкостью настройки расточной системы на заданный размер – 24.2 мин. с необходимостью установки пробной заготовки. В то время, при методе фрезерования процесс настройки на заданный размер занимает 0.9 минуты при обработке первого отверстии в детали (партии).
- Затраты на инструмент.
На основании произведенных расчетов затрат на режущий инструмент и приведенных графиков зависимости (см. рисунок 6), при обработке данных отверстий, экономически целесообразнее применять метод фрезерования – 235,5 руб., в отличии от развертывания – 435,6 руб. и растачивания – 537 руб.
Рисунок 6. Зависимость затрат на инструмент от метода окончательной обработки отверстий
Разница показателей, это следствие основного времени окончательной обработки отверстия, дороговизны расточных державок и пластин, разверток и их меньшей стойкости, чем у фрезы.
На основании проведенного хронометража, расчетов нормы штучного и подготовительно – заключительного времени, расчет затрат на инструмент и приведенных графиков зависимости, можно сделать вывод, что при окончательной обработке отверстий с вариативностью методов (Ø18-20, длиной 38-48 мм, с точностью H по 7 квалитету и шероховатостью поверхности Ra 0.8 мкм) в условиях цеха, применение метода фрезерования является наиболее эффективным.
