Влияние внутренних напряжений на процесс коррозии образцов из стали 12Х1МФ
Секция: Технические науки
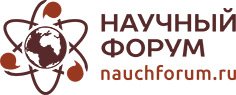
XXXVI Студенческая международная научно-практическая конференция «Технические и математические науки. Студенческий научный форум»
Влияние внутренних напряжений на процесс коррозии образцов из стали 12Х1МФ
Исследование выполнено при финансовой поддержке РФФИ в рамках научного проекта № 18-08-01265.
Сталь 12 Х1МФ широко применяется в энергетическом машиностроении в трубах пароперегревателей и трубопроводах высокого давления и имеет следующий химический состав: 0.08–0.15 C; 0.9–1.2 Cr; 0.25–0.35 Mo; 0.15–0.30 V; 0.4–0.7 Mn; 0.17–0.37 Si; ≤ 0.25 Ni; ≤ 0.2 Cu ;≤ 0.025 S; ≤ 0.030 P; остальное железо.
Проблема коррозионной стойкости металлов и сплавов актуальна не один десяток лет, а механизмы коррозии активно обсуждаются в печати [1 – 3].
Коррозия, как самопроизвольное окисление металлов, является вредным для промышленной практики процессом в связи с существенными необратимыми потерями металла. В качестве факторов, влияющих на коррозионные процессы, выделяют следующие [1 – 3]:
− природу металла, структуру и характер его поверхности, степень деформации и напряжённости (отклонением от равновесного состояния);
− наличие поверхностных плёнок окислов или иных соединений или адсорбированных веществ;
− химический состав, температуру и концентрацию электролита;
− давление, которое в свою очередь определяет растворимость водорода.
Факторы, влияющие на коррозионные процессы, разделяют на внешние, касающиеся влияния среды и условий эксплуатации, и внутренние, связанные с микроструктурой металла . Часто внутренние факторы недооценивают или ими вообще просто пренебрегают.
В этой связи цель настоящей работы заключается в установлении роли внутренних структурных напряжений на процесс разрушения металла от коррозии.
Методика определения параметра элементарной ячейки и внутренних напряжений
Параметр элементарной ячейки для кубических кристаллов рассчитывается по выражению:
,
где а – параметр элементарной ячейки, Å; (H K L) – индексы Миллера плоскости; d – межплоскостное расстояние, Å, которое устанавливается по формуле Вульфа-Брэгга: →
, где
λ – длина волны используемого излучения, Å.
Внутренние напряжения первого рода определяются по закону Гука:
где аi – текущий параметр элементарной ячейки, Å; а0 – параметр элементарной ячейки эталона, Å; Е – модуль нормальной упругости.
Рисунок 1. Схема вырезки образцов из стали 12Х1МФ
Установка для коррозионных испытаний имеет вид, изображенный на рис.2.
Рисунок 2. Принципиальная схема экспериментальной установки для проведения коррозионных испытаний :
1 – электропечь СУОЛ-0,4.4/12-М2; 2 – регулятор температуры; 3 – кварцевая трубка; 4 – экспериментальные образцы; 5 – подставка; 6 – переключатель регулятора температуры; 7 – нагреватель; 8 – термопара ПП; 9 – термопара ХА; 10 – пирометр; 11 – стальная труба; 12 – вытяжной шкаф; 13 – вентилятор; 14 – выхлопной патрубок; 15 – генератор пара; 16 – переходник; 17 – предохранительный клапан; 18, 19 – устройство поддержания температуры воды по методу Виккерса
Основной её элемент 1 – электропечь СУОЛ-0,4.4/12-М2, снабженная регулятором температуры 2 с переключателем 6. Температура в активной зоне печи контролировалась двумя термопарами: платинородий-платиновая 8 (ПП) и хромель-алюмелевой 9 (ХА). Термопара 8 работала совместно с регулятором 2, а датчик температуры 9 – с показывающим потенциометром 10. Нагреватель печи на рис. 2 обозначен позицией 7. Насыщенный пар образовывался из дистиллированной воды в парогенераторе 15, снабжённым устройством поддержания температуры воды 18 и предохранительным клапаном 17. Попадание пара из парогенератора 15 в кварцевую трубку 3 (рабочий участок установки), расположенную в активной зоне печи 1, осуществлялось через фланцевый переходник 16. В этой трубке 3 пар перегревался до необходимой температуры и омывал исследуемые образцы 4, располагающиеся на керамической подставке 5. Кварцевая трубка 3 соединена со стальной трубой – эжектором 11, которая способствовала организации требуемой среды вокруг образцов 4, так как пар двигался через рабочий участок установки благодаря работе, как парогенератора 15, так и вентилятора 13. Пройдя трубу 11, пар попадал в вытяжной шкаф 12, а затем через выхлопной патрубок 14 удалялся в атмосферу.
Методика коррозионных испытаний заключалась в выдержке исследуемых образцов в среде перегретого водяного пара (250 °C) на протяжении 500 часов.
Взвешивание образцов до и после коррозионных испытаний для определения прироста массы осуществлялось с помощью высокоточных аналитических весов Pioneer (точность измерения составляла 0,0001 г). Увеличение массы образцов подтверждало протекание процесса коррозии.
Рисунок 3. Удельный прирост массы образцов из стали марки 12Х1МФ
Из рис. 3 следует, что наибольший прирост массы отмечается у образцов №3, № 5, № 6, № 7 и № 8.
Особенность распределения внутренних напряжений для этих образцов заключается в том, что на одной из сторон они носят сжимающий характер, тогда как на другой стороне – растягивающий.
Рисунок 4. Распределение внутренних напряжений в образцах из стали марки 12Х1МФ
Из рис. 3, 4 следует, что коррозионным повреждениям в большей степени подвержены те образцы, у которых отмечается существенная неоднородность в распределении внутренних напряжений, и чем она значительнее, тем сильнее развивается процесс коррозии. Так, у образца №1 напряжения распределились следующим образом: на наружной поверхности 0 МПА, на внутренней поверхности + 96 МПа. Этот образец подвержен коррозии в меньшей степени, чем, для сравнения, образцы № 7 и № 8. У образца № 7 на тех же поверхностях напряжения составляют соответственно –96 МПа и +178 МПа, а у образца № 8 – это –274 МПа и + 81 МПа. Видно, что наиболее сильно корродируют именно эти образцы (рис. 3).
Таким образом, нельзя не учитывать роли внутренних напряжений в процессах разрушения, в том числе и от коррозии [4 – 8]. Возможно, в этих процессах внутренние напряжения, как структурный фактор, играют самостоятельное значение, а создание благоприятных распределений полей внутренних напряжений является ресурсом в повышении коррозионной стойкости стали.
