Метод нанесения функциональных покрытий на рабочие поверхности деталей подшипников
Секция: Технические науки
лауреатов
участников
лауреатов


участников


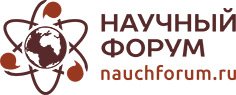
XL Студенческая международная научно-практическая конференция «Технические и математические науки. Студенческий научный форум»
Метод нанесения функциональных покрытий на рабочие поверхности деталей подшипников
Аннотация. В работе приведены методы нанесения функциональных покрытий на рабочие поверхности деталей подшипников качения.
Нередко условия работы подшипников превышают пределы их возможностей, из – за чего могут возникать различные проблемы в работе подшипников и, соответственно, целых устройств. С учетом все возрастающих требований к различным промышленным компонентам, производители стремятся разработать оптимальные сочетания материалов и технологий подшипниковых покрытий. Так возникает необходимость нанесения покрытий на рабочие поверхности деталей подшипников, позволяющих увеличить качество их работы и эксплуатационный срок службы.
Для промышленных подшипников качения и скольжения доступно довольно много методов нанесения покрытий, которые выполняют ту или иную функцию. При этом каждое сочетание покрытий дает свои преимущества.
Цель работы: провести сравнение методов нанесения функциональных покрытий на рабочие поверхности деталей роликоподшипника 42305 и выявление их недостатков. Также на основании данного анализа выделить оптимальный метод нанесения функциональных покрытий.
Среди методов нанесения защитных покрытий, основанных на воздействии на поверхность детали потоков частиц и квантов с высокой энергией, большое внимание привлекают вакуумные ионно-плазменные методы. Характерной их чертой является прямое преобразование эклектической энергии в энергию технологического воздействия, основанной на структурно-фазовых превращениях в осажденном на поверхности конденсате или в самом поверхностном слое детали, помещенной в вакуумную камеру.
Основным достоинством данных методов является возможность создания весьма высокого уровня физико-механических свойств материалов в тонких поверхностных слоях, нанесение плотных покрытий из тугоплавких химических соединений, а также алмазоподобных, которые невозможно получить традиционными методами.
Кроме того, эти методы позволяют:
• обеспечивать высокую адгезию покрытия к подложке;
• равномерность покрытия по толщине на большой площади;
• варьировать состав покрытия в широком диапазоне, в пределах
одного технологического цикла;
• получить высокую чистоту поверхности покрытия;
• экологическую чистоту производственного цикла.
Широко известен такой метод нанесения покрытия, как ионное распыление.
Ионные распылители разделяют на две группы:
• плазмоионные, в которых мишень находится в газоразрядной плазме, создаваемой с помощью тлеющего, дугового и высокочастотного разряда - 23 МГц. Распыление происходит в результате бомбардировки мишени ионами, извлекаемыми из плазмы;
• автономные источники без фокусировки и с фокусировкой ионных пучков, бомбардирующих мишень. В наиболее простом случае система распыления состоит из двух электродов, помещенных в вакуумную камеру. Достоинство данного метода заключается в возможности получения покрытий из тугоплавких металлов, сплавов и химических соединений.
Одной из наиболее перспективных обработок является плазменная технология, интенсивно разрабатываемая как в нашей стране, так и за рубежом. Использование низкотемпературной плазмы эффективно не только для переплава металлов и сплавов, напыления износостойких, жаропрочных и коррозионностойких покрытий, резки и сварки различных материалов, но и для поверхностного упрочнения различных изделий.
Плазменное поверхностное упрочнение находит широкое применение как в условиях мелкосерийного и единичного (в том числе ремонтного), так и крупносерийного и массового производства. Сущность его заключается в термических фазовых и структурных превращениях, происходящих при быстром концентрированном нагреве рабочей поверхности детали плазменной струей (дугой) и теплоотводе в материал детали.
Более перспективный метод повышения эксплуатационных характеристик и трибологических свойств рабочих поверхностей подшипников качения представлен методом нанесения покрытия на рабочие поверхности в процессе совместной доработки подшипников в собранном виде. Он является наиболее оптимальным и перспективным для работы методом.
Сущность данного метода заключается в одновременном нанесении покрытия на все рабочие поверхности деталей подшипника в процессе имитационной обработки в собранном виде. В результате кинематики перемещения наружных и внутренних колец обрабатываемого подшипника в условиях их перекоса, на рабочих поверхностях его деталей обеспечивается проскальзывание, позволяющее наносить функциональное покрытие, находящееся в зоне контакта с валом установки для нанесения функционального покрытия. Методика нанесения включает в себя то, что в процессе приработки подшипника создаётся перекос наружного кольца относительно внутреннего на 20 градусов ±10 минут, за счет пересечения поперечных плоскостей их симметрии. В центре симметрии подшипника при принудительном вращении со скоростью 50 об/мин в течение 40…50 с, наружного и внутреннего колец вокруг их осей, в процессе одной операции выполняется сообкатывание рабочих поверхностей подшипника качения собственным комплектом тел качения. Далее на поверхность дорожки качения подшипника размещают упрочняющие или защитные покрытия при помощи устройства, имитирующее медицинскую капельницу
На рис. 1 отображены рабочие поверхности подшипников - дорожки качения внутренних колец, на которые будет нанесено функциональное покрытие, а именно: состав, содержащий примерно около 20% высокодисперсного медного порошка с размером частиц 2×10-6м - ПМВД-0 (ТУ 1790-040-12288779-2005), 15% дисульфид молибдена с размером частиц 7×10-6м - ДМИ-7 (ТУ 48-19-133-90), остальное глицерин.
Рисунок 1. Роликоподшипник 42305, где 1 - наружное кольцо подшипника, 2 - внутреннее кольцо подшипника, 3 - ролик (шарик) подшипника, А – покрытие, О - центр подшипника, О1- центр ролика
Материалом наружного и внутреннего кольца подшипника является сталь 8Х4В9Ф2-Ш, роликов – сталь 15Г1.
В ходе исследований получено выражение, отражающее влияние на толщину покрытия рабочей поверхности внутреннего кольца роликоподшипника технологических факторов имитационной обработки в собранном виде:
мкм, (2)
м/мин
мм
где t – толщина покрытия рабочей поверхности внутреннего кольца роликоподшипника, мкм;
Vo– линейная скорость вращения центра О1 ролика, вокруг центра О подшипника, м/мин;
Vо1– линейная скорость вращения ролика вокруг собственной оси О1, м/мин;
αм– угол контакта рабочей поверхности ролика и обрабатываемой поверхности, º;
Vд – линейная скорость перемещения точек обрабатываемой поверхности, м/мин;
– радиусы кривизны, соответственно, обрабатываемой поверхности и рабочей поверхности ролика, мм;
Ни, Нд – твердость по Бринеллю, соответственно, рабочей поверхности ролика и обрабатываемой поверхности, кгс/мм2;
– максимальная высота микронеровностей обрабатываемой поверхности, мм;
– общее число микровыступов на единице рабочей поверхности ролика,шт./мм2;
к–показатель степени расположения микровыступов;
Ho – расстояние вершин наиболее выступающих микровыступов до центра их группирования в направлении нормали к рабочей поверхности ролика, мм;
rи – радиус рабочей поверхности ролика, мм;
zи – количество роликов в обрабатываемом подшипнике;
n0 – частота вращения комплекта роликов вокруг обрабатываемой поверхности внутреннего кольца, об/мин;
– время обработки, мин.
nд– частота вращения обрабатываемой поверхности, об/мин;
rд– радиус обрабатываемой поверхности, мм.
Выражение (2) позволяет определить толщину покрытия, наносимого на рабочую поверхность внутреннего кольца роликоподшипника в процессе его имитационной доработки в собранном виде в течение времени .
Используя полученное выражение, можно проанализировать влияние геометрических и кинематических характеристик имитационной доводки деталей роликоподшипников на толщину покрытия дорожки качения внутреннего кольца (рис.2).
Рисунок 2. Зависимость толщины покрытия t от твердости обрабатываемой поверхности Нд, где t – толщина покрытия рабочей поверхности, мкм
Количество роликов в подшипнике также оказывает влияние на производительность нанесения покрытия.
Как видно из рис.3, с увеличением количества роликов в подшипнике эффективность обработки возрастает.
Рисунок 3. Зависимость толщины покрытия t нанесения покрытия на роликовую дорожку от количества роликов Zр в подшипнике, где t – толщина покрытия рабочей поверхности, мкм
На рис.4 представлены теоретическая и экспериментальная зависимости, отражающие влияние частоты вращения комплекта роликов на производительность нанесения покрытия. Как видно из данного рисунка, погрешность расчета не превышает 20%, что вполне приемлемо для инженерных расчетов.
Рисунок 4. Зависимость толщины покрытия t нанесения покрытия на роликовую дорожку от частоты nоб вращения комплекта роликов:
1 – теоретическая кривая; 2 – экспериментальная кривая, где t – толщина покрытия рабочей поверхности, мкм
Выводы: проведен сравнительный анализ методов нанесения функциональных покрытий на рабочие поверхности деталей подшипников качения, в ходе которого было выявлено, какой из методов является более эффективным в своём использовании.
Показано, что полученная математическая модель нанесения покрытия на рабочую поверхность внутреннего кольца роликоподшипника в процессе имитационной обработки учитывает значительное количество факторов, позволяет исследовать их влияние на эффективность процесса, обладает достаточной точностью и чувствительностью и может быть использована для исследования закономерностей предложенного метода нанесения покрытия, а именно: состав, содержащий примерно около 20% высокодисперсного медного порошка, 15% дисульфид молибдена, 65% глицерина, на рабочие поверхности деталей роликоподшипника.
На основании анализа выделен оптимальный метод нанесения функционального покрытия, а именно: состав, содержащий примерно около 20% высокодисперсного медного порошка, 15% дисульфид молибдена, 65% глицерина.
