ОСОБЕННОСТИ ПОСТРОЕНИЯ ТРЕХМЕРНЫХ МОДЕЛЕЙ ДЛЯ ИССЛЕДОВАНИЯ ЖЕСТКОСТИ ТЕХНОЛОГИЧЕСКОГО ОБОРУДОВАНИЯ И ОСНАСТКИ
Секция: 8. Машиностроение
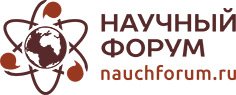
VII Студенческая международная заочная научно-практическая конференция «Молодежный научный форум: технические и математические науки»
ОСОБЕННОСТИ ПОСТРОЕНИЯ ТРЕХМЕРНЫХ МОДЕЛЕЙ ДЛЯ ИССЛЕДОВАНИЯ ЖЕСТКОСТИ ТЕХНОЛОГИЧЕСКОГО ОБОРУДОВАНИЯ И ОСНАСТКИ
Одной из основных задач технологической подготовки современного производства является интеграция в решении конструкторских, технологических и производственных задач. Важное значение имеет предварительная оценка возможностей технологической системы по обеспечению производительности и качества обработки. Одним из методов решения этой задачи является симуляция обработки с применением трехмерных моделей. Этот способ применяется пока для проверки правильности отработки управляющих программ, однако, может иметь перспективное применение для оценки упругих деформаций при обработке. В данной статье рассматриваются основные вопросы расчета упругих деформаций технологической системы в среде NX. Процесс решения этой задачи состоит из следующих этапов:
1. Формирование трехмерных моделей заготовки, приспособления, инструмента, станка. Поскольку проектирование этих элементов технологической системы производится разными службами предприятия, их формирование производится параллельно. Пакет программ NX предоставляет богатый функционал операций при разработке моделей. Проектирование можно вести с применением различным методик. В данном случае выполнялась модернизация приспособления, аналог которого был спроектирован и изготовлен ранее. Поэтому разработка приспособления велась подетально и сводилась, по сути, к оцифровке бумажной конструкторской документации. Создание трехмерных моделей составляющих приспособления производилось традиционным методом — на новом эскизе формировался контур (рис. 1а), создавалась операция вытягивания для определения основного массива материала (рис. 1б) и формировались конструктивные подробности: фаска, поднутрение и паз. Для облегчения построения строили сперва половину детали, затем применяли функцию «Зеркальное тело» (рис. 1в). Полученные два тела объединяли в одно, используя булеву операцию объединения (рис. 1г), и назначали материал на деталь.
Рисунок 1. Создание трехмерной модели детали
Аналогично создавали модели других деталей и из них сформировали сборку. Удобной возможностью в NX является возможность добавлять в сборку сразу несколько компонентов (рис. 2а).
а) б)
Рисунок 2. Создание сборной модели
Выбирая различные виды сопряжений, в том числе касание или выравнивание по расстоянию (рис. 2б) можно получить сборку требуемой конфигурации. Также удобным является то, что детали можно изменять непосредственно в контексте сборки. Тем самым можно корректировать размеры и форму деталей, а также добавлять мелкие конструктивные элементы, например, крепежные отверстия (рис. 3).
Рисунок 3. Изменение деталей в контексте сборки
Таким образом, полностью формируется сборка приспособления вместе с заготовкой (рис. 4).
Рисунок 4. Сборная модель приспособления с заготовкой
Аналогично выполняется сборка инструментального комплекта — режущего инструмента в сборе со вспомогательным инструментом. Трехмерная модель станка может быть подготовлена заранее, поскольку она может использоваться при решении других задач производства.
2. Формирование конечно-элементной модели. Целью данного этапа является формирование конечно-элементной сетки, то есть разбиение твердотельных моделей на связанные трехмерные элементы.
Необходимо иметь в виду, что чрезмерная подробность самой трехмерной модели и чрезмерная ее дискретизация приводит к повышенному потреблению системных ресурсов и времени расчета, что не всегда оправдано. Поэтому при подготовке к формированию конечно-элементной сетки необходимо выполнить упрощение трехмерной модели — подавить несущественные для расчета конструктивные элементы — мелкие геометрические элементы, отверстия, скругления и т. п. Степень этого упрощения зависит от поставленных целей исследования, допустимой точности результата, вычислительных ресурсов.
Рисунок 5. Сборная конечно-элементная модель станка, приспособления, инструмента, заготовки
3. Подготовка к расчету. На данном этапе указывается тип выполняемого расчета. Для решения поставленных задач исследования достаточно наиболее простого варианта — линейного статического анализа.
В рамках данного расчета необходимо подготовить следующие данные:
3.1. Задать нагрузки. Было использовано допущение, что на результаты решения задачи оказывают влияние только силы, возникающие при резании. Силы резания определялись по эмпирическим закономерностям для составляющих Pх, Py, Pz, далее путем квадратичного суммирования была определена их равнодействующая. Согласно третьему закону Ньютона, равнодействующие были приложены к заготовке и к инструменту в точке их контакта при резании.
3.2. Задать граничные условия (ограничения). В качестве граничного условия, ограничивающего смещение сборной модели как твердого тела, моделировалось крепление станины к фундаменту.
3.3. Задать условия контакта моделей в сборке. Моделированию связей между элементами в сборной модели необходимо придавать большое значение, поскольку на долю смещений в контактах приходится до 80—90 % всех деформаций станка, и неправильное моделирование контактов может привести к неадекватным результатам. В рамках данной работы моделирование линейного контактного взаимодействия между поверхностями производилось упрощенным методом с помощью функции NX «Соединение поверхность—поверхность», причем значения контактных жесткостей моделировались с помощью коэффициента штрафа [1, с. 282].
Рисунок 6. Конечно-элементная модель с учетом нагрузок, ограничений и контактов между поверхностями
4. Проведение расчета. Согласно заданным условиям, решатель NX Nastran производит расчет напряженно-деформированного состояния технологической системы.
5. Визуализация полученных результатов и их анализ.NX выводит результаты графически, показывая деформированное под заданной нагрузкой состояние системы (рис. 7).
Рисунок 7. Карта результатов линейного статического расчета
Видно, что наибольшие деформации имеет ветвь инструмента — силы резания приводят к повороту инструмента. Кроме того, значительным деформациям подвергается шпиндельная бабка станка (рис. 8). При обработке точных изделий это существенно повлияло бы на погрешность обработанной поверхности. Кроме того, можно определить численные значения деформаций в заданных точках (рис. 8).
Рисунок 8. Деформации шпиндельной бабки станка
По результатам расчета видно, что спроектированное приспособление обладает высокой жесткостью и в изменении не нуждается. Напротив, инструментальная система нуждается в повышении жесткости, что можно сделать, изменяя конструкцию инструмента или схему резания.
Список литературы:
- Гончаров П.С. NX Advanced Simulation. Инженерный анализ / Гончаров П.С., Артамонов И.А., Халитов Т.Ф., Денисихин С.В., Сотник Д.Е. — М.: ДМК Пресс, 2012. — 504 с.
- Решетов Д.Н., Портман В.Т. Точность металлорежущих станков. — М.: Машиностроение, 1986. — 336 с.
