РАЗМЕРНЫЙ АНАЛИЗ КОНСТРУКЦИИ УЗЛА С ПРИМЕНЕНИЕМ КОМПЬЮТЕРНОГО МОДЕЛИРОВАНИЯ
Секция: 8. Машиностроение
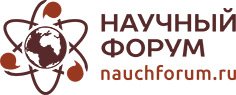
XII Студенческая международная заочная научно-практическая конференция «Молодежный научный форум: технические и математические науки»
РАЗМЕРНЫЙ АНАЛИЗ КОНСТРУКЦИИ УЗЛА С ПРИМЕНЕНИЕМ КОМПЬЮТЕРНОГО МОДЕЛИРОВАНИЯ
Проблема качества сборки как заключительного этапа процесса создания машин и механизмов и основного способа обеспечения заявленных эксплуатационных характеристик является особенно актуальной при производстве высокотехнологических изделий машиностроения, к которым относятся изделия с повышенными требованиями к точности эксплуатационных параметров, надежности и долговечности.
Усложнение изделий за счет использования составных конструкций обусловлено множеством объективных причин, таких как обеспечение простоты технологии изготовления, повышение технологичности, экономия материалов, обеспечение ремонтопригодности. Увеличение элементарного состава машин в то же время приводит к повышению неопределенности системы, значительному колебанию функциональных параметров, уменьшению устойчивости к воздействию внешних параметров.
Размерный анализ конструкций является важным этапом размерной отработки конструкций, так как позволяет установить взаимосвязи деталей и сборочных единиц, определить методы достижения требуемой точности, проанализировать правильность простановки размеров и допусков на чертежах, повысить технологичность конструкции, установить последовательность сборки машины и ее сборочных единиц .
Размерный анализ конструкций и технологических процессов — это совокупность расчетно-аналитических процедур, осуществляемых при разработке и анализе конструкций и технологических процессов механической обработки, включая:
- построение специальных размерных схем технологических процессов;
- выявление и фиксацию взаимосвязей всех размерных параметров, в том числе с применением теории графов;
· выявление размерных цепей конструкций и технологических процессов;
· проверку и установление рациональных способов простановки размеров в чертежах;
· назначение достаточного и необходимого числа технических требований;
· назначение обоснованных допусков, минимально необходимых припусков;
· проверочный расчет возможности обеспечения чертежных размеров и технических требований;
· расчет средних и минимальных припусков;
· определение номинальных значений операционных размеров;
· определение толщины покрытий, глубины азотирования и других характеристик.
Размерный анализ предусматривает выполнение большого числа действий. Трудоемкость размерного анализа весьма значительна — размерный анализ одной конструкции или одного технологического процесса может занимать от 20 до 60 часов. Решение проблемы снижения трудоемкости размерного анализа конструкций и технологических процессов возможно на основе его автоматизации [1; 2; 3; 4; 8; 10; 11; 12].
При математическом моделировании размерных цепей конструкций и технологических процессов применяется теория графов, которая позволяет связать теоретические положения с вычислительными алгоритмами, реализуемыми на ЭВМ.
Размерные цепи классифицируются по ряду признаков:
· по области применения (конструкторские, технологические, измерительные);
· по месту в изделии (подетальные, сборочные);
· по расположению звеньев (линейные, угловые, плоские, пространственные);
· по виду звеньев (скалярные или векторные);
· по характеру взаимных связей (независимые, параллельно связанные, последовательно связанные, комбинированно связанные).
При составлении схемы размерной цепи на сборочный чертеж или на конструктивную схему механизма наносят изображение замыкающего звена, затем, начиная от одной из поверхностей (осей), ограничивающих замыкающее звено, последовательно выявляют составляющие звенья, непосредственно используемые при решении поставленной задачи, и доходят до второй поверхности (оси), ограничивающей замыкающее звено с другой стороны.
Размерная цепь представляет собой множество объектов (поверхностей или осей) и множество связей между ними (размеров). Такие структуры являются графом и их можно изучать с помощью теории графов, при этом процесс выявления размерных цепей упрощается и легко формализуется.
Для проведения размерного анализа кроме размерной схемы составляется уравнение размерной цепи, вытекающее из условия замкнутости:
с1А1 + с2А2 +...+ сm+nАm+n = 0,
где: А1, А2, ..., Аm+n – номинальные значения всех звеньев размерной цепи; с1, с2, ..., сm+n — коэффициенты, характеризующие степень влияния изменения звена на изменение замыкающего звена, или передаточные отношения.
В размерных цепях с параллельными звеньями (линейные цепи)
|с1| = |с2| = ... = |сm+n| = 1.
В плоских и пространственных размерных цепях (общий случай)
.( i = 1, 2, ..., m+n).
Если увеличение составляющего звена приводит к увеличению замыкающего звена, то передаточное отношение положительно; если — к уменьшению, то передаточное отношение отрицательно.
В зависимости от вида размерной цепи и ее сложности передаточное отношение можно определять различными методами:
1. Метод изменения. Метод заключается в последовательном изменении каждого из составляющих звеньев при неизменных значениях остальных звеньев и анализе влияния этого изменения на значение замыкающего звена. Применяется при наличии сложной зависимости между звеньями, а также в тех случаях, когда определяются только отклонения замыкающего звена и не находятся его номинальные значения.
2. Метод проецирования. Все составляющие звенья проецируются на направление замыкающего звена, а их передаточные отношения определяются как косинусы углов, образуемых составляющими звеньями с направлением замыкающего звена. Применяется при расчете плоских размерных цепей.
3. Метод дифференцирования. Передаточное отношение каждого составляющего звена определяется как частная производная от замыкающего звена, т.е. путем дифференцирования уравнения размерной цепи. Применяется при расчете размерных цепей, для которых легко составляется и дифференцируется аналитическое выражение с замыкающим и составляющим звеньями.
Для линейных размерных цепей номинальное значение замыкающего звена представляет собой разность между суммами номинальных значений увеличивающих и уменьшающих звеньев:
,
где: m — число увеличивающих звеньев; n — число уменьшающих звеньев.
В общем случае номинальное значение замыкающего звена
Два последних уравнения являются основными уравнениями линейных и плоских размерных цепей.
Целью размерного анализа конструкций является обеспечение, в конечном счете, качества изделий и их экономичной сборки на основе определения, во-первых, всех размеров и допусков узла — замыкающих звеньев размерных цепей и, во-вторых, всех размеров и допусков деталей узла и, в первую очередь, составляющих звеньев, согласованных по точности с точностью замыкающих звеньев.
Методика автоматизированного размерного анализа конструкций должна предусматривать широкое использование возможностей ЭВМ как для исключения рутинных расчетных операций, так и при обеспечении информацией для принятия творческих решений.
Общая методика автоматизированного размерного анализа конструкций включает следующие этапы.
1. Представление информации о сборочной единице в виде, пригодном для ввода в ЭВМ, для чего осуществляется переход от описания конструкции узла в виде сборочного чертежа к описанию конструкции в виде геометрической модели узла и геометрических моделей деталей с фиксацией всех размеров и допусков (отклонений), выявлением взаимосвязей между деталями и назначением замыкающих звеньев и требований к ним.
2. Подготовка исходных данных для ввода в ЭВМ в виде текстового файла, проверка правильности файла исходных данных с помощью программы для ЭВМ и уточнение геометрических моделей деталей и узла по результатам проверки.
3. Выявление с помощью программы для ЭВМ структуры размерных цепей и ее анализ с уточнением простановки размеров деталей.
4. Назначение допусков (отклонений) на замыкающие и составляющие звенья размерных цепей и фиксация их в файле исходных данных.
5. Проверка и обеспечение допусков на замыкающие звенья размерных цепей с помощью программы для ЭВМ.
6. Проверка и обеспечение значений отклонений замыкающих звеньев размерных цепей с помощью программы для ЭВМ.
7. Анализ результатов размерного анализа.
С целью более полной автоматизации размерного анализа технологических процессов разработана программа для ЭВМ «Размерный анализ технологических процессов осесимметричных деталей «NORMAL» [9]. При расчете линейных и диаметральных технологических размеров с помощью данной программы также применяется метод на основе использования матрицы смежности графа [6].
Решение вариантов одной задачи предусматривает возможность использования первоначально введенной информации для многократного повторения решения при изменении условий расчета, значений размерных параметров или частичного изменения состава операций в списке исходных данных.
Для обеспечения простоты кодирования информация о сборочной единице, детали, заготовке и технологическом процессе механической обработки представляется в виде геометрических моделей, имеющих только плоские и цилиндрические поверхности, с табличным описанием [5].
Для визуализации конструкции сборочной единицы и схемы припусков в программах применяется метод построения изображений [7] на основе данных, содержащихся в геометрических моделях сборочной единицы, детали, заготовки и технологического процесса механической обработки.
В современных условиях усложнения конструкций и повышения требований к технологическим процессам невозможно повысить качество и сократить сроки выполнения размерного анализа баз применения средств автоматизации проектирования и инженерного анализа.
Список литературы:
1. Аввакумов В.Д. Расчет сборочных размерных цепей на ЭВМ // Сборка в машиностроении, приборостроении. — 2006. — № 10. — С. 9—13.
2. Взаимозаменяемость, стандартизация и технические измерения: Учеб. для вузов / А.И. Якушев, Л.Н. Воронцов, Н.М. Федотов. — 6-е изд., перераб. и доп. — М.: Машиностроение, 1986. — 352 с.
3. Иващенко И.А. Технологические размерные расчеты и способы их автоматизации. — М.: Машиностроение, 1975. — 222 с.
4. Калачев О.Н. Интерактивное моделирование размерных изменений заготовки при проектировании технологического процесса механической обработки // Информационные технологии. — 2001. — № 2. — С. 10—14.
5. Масягин В.Б. Автоматизация размерного анализа осесимметричных конструкций // Проблемы разработки, изготовления и эксплуатации ракетно-космической и авиационной техники: Матер. III регион. науч. конф., посвящ. памяти главного конструктора ПО «Полет» А.С. Клинышкова. — Омск: Изд-во ОмГТУ, 2008. — С. 227—231.
6. Масягин В.Б. Метод расчета линейных технологических размеров на основе матричного представления графа // Технология машиностроения. — 2004. — № 2. — С. 35—40.
7. Масягин В.Б. Формирование изображений геометрических моделей деталей, заготовок, операционных эскизов и сборочных единиц с помощью ЭВМ // Механика процессов и машин. — Омск: Изд-во ОмГТУ, 2000. — С. 192—196.
8. Мордвинов Б.С., Яценко Л.Е., Васильев В.Е. Расчет линейных технологических размеров и допусков при проектировании технологических процессов механической обработки. — Иркутск, Иркутский госуниверситет, 1980. — 104 с.
9. Свидетельство о государственной регистрации программы для ЭВМ № 2008614062. Размерный анализ технологических процессов осесимметричных деталей «NORMAL» / В.Б. Масягин // Роспатент, — М., 2008.
10. Скворцов А.В. Автоматизированная система комплексного размерного анализа в среде CALS/ИПИ-технологий // Вестник машиностроения. — 2007. — № 5. — С. 36—42.
11. Сметанин Ю.М., Трухачев А.В. Методические указания для проведения размерного анализа техпроцессов с использованием графов. — Устинов: Устиновский механический институт, 1987. — 43 с.
12. Хармац И. КОМПАС-АВТОПРОЕКТ: точный контроль над технологической информацией. Новые модули и новые возможности системы // САПР и графика. — 2004. — Июнь. — С. 17—19.
