СОВЕРШЕНСТВОВАНИЕ ТЕХНОЛОГИИ РЕМОНТА КОРПУСОВ ВКЛАДЫШЕЙ МОТОРНО-ОСЕВЫХ ПОДШИПНИКОВ ЛОКОМОТИВОВ
Секция: 8. Машиностроение
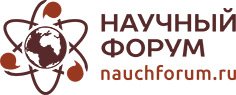
XX Студенческая международная заочная научно-практическая конференция «Молодежный научный форум: технические и математические науки»
СОВЕРШЕНСТВОВАНИЕ ТЕХНОЛОГИИ РЕМОНТА КОРПУСОВ ВКЛАДЫШЕЙ МОТОРНО-ОСЕВЫХ ПОДШИПНИКОВ ЛОКОМОТИВОВ
Важной частью многих видов железнодорожного транспорта считается моторно-осевой подшипник (МОП), являющейся одной из двух опор тягового двигателя. Он обеспечивает параллельность оси колесной пары и двигателя локомотива. МОП принимает на себя большие динамические нагрузки, а также нагрузки от трения. Безопасность эксплуатации электровозов и тепловозов во многом зависит от надежности колесно-моторного блока (КМБ), и в частности от моторно-осевого подшипника [2].
В процессе эксплуатации наблюдается износ моторно-осевых подшипников как по внутренней поверхности, залитой баббитом и контактирующей с осью колесной пары, так и по наружной поверхности, сопряженной с остовом тягового двигателя, а именно по бурту корпусов вкладышей.
Причинами отказов в работе МОП являются: неудовлетворительное техническое обслуживание и нарушение режимов эксплуатации со стороны локомотивных бригад, неудовлетворительное качество деповского ремонта, неудовлетворительное качество заводского ремонта и прочие причины.
Анализ статистических данных, приведенных на рисунке 1 показывает, что превалирующими неисправностями МОП являются: износ буртов корпусов вкладышей МОП (26 %), износ баббитового слоя (31 %) и усталостное выкрашивание баббитового слоя (17 %).
Для устранения выше перечисленных неисправностей МОП согласно существующей технологии ремонта необходимо выполнить следующие виды работ: выплавить старый баббитовой слой; восстановить геометрические размеры буртов корпусов; залить внутреннюю поверхность корпусов вкладышей новым баббитовым слоем; выполнить расточку вкладышей МОП по баббиту под ось колесной пары.
Рисунок 1. Распределение неисправностей моторно-осевых подшипников: 1 — износ буртов корпусов вкладышей МОП; 2 — износ баббитового слоя; 3 — усталостное выкрашивание баббитового слоя; 4 — трещины в корпусах вкладышей МОП; 5 — износ наружного диаметра корпусов вкладышей МОП; 6 — износ шпоночного паза корпуса вкладыша МОП
Существующая технология восстановления толщины бурта заключается в наплавке с внутренней стороны корпуса, так называемых сварных площадок и дальнейшей их механической обработки на токарном станке. Данные сварные площадки, как правило, три на каждом корпусе, наплавляют газовой сваркой с применение сварочных прутков. Фотографии новых корпусов и корпусов с восстановленным буртом по выше указанной технологии, приведены на рисунке 2.
Такой подход существенно снижает эксплуатационную надежность КМБ, так как при износах и срывах наплавленных площадок, возникают перекосы вкладышей в шапках МОП, а это приводит к уменьшению величины радиального зазора между вкладышем и осью колесной пары, увеличивая тем самым трение в узле и интенсивность изнашивания баббитового слоя. Наплавка всей поверхности бурта весьма длительный процесс, который существенно увеличивает производственного цикл ремонта и количество незавершенного производства.
а) б)
Рисунок 2. Корпуса и вкладыши моторно-осевых подшипников: а) новые корпуса вкладышей МОП; б) восстановленные вкладыши МОП
Для исключения выше указанных недостатков необходимо совершенствовать технологическую готовность производства при ремонте МОП посредством разработки и внедрения в локомотивных депо современных технологических процессов и специализированного технологического оборудования [1]. Для восстановления буртов корпусов вкладышей, предлагается применять холодную сварку, которая находит все большее применение в современном машиностроении особенно при сварке цветных металлов и сплавов.
Качество сварного соединения определяется исходным физико-химическим состоянием контактных поверхностей, давлением (усилием сжатия) и степенью деформации при сварке. Оно также зависит от схемы деформации и способа приложения давления. В зависимости от схемы пластической деформации заготовок сварка может быть точечной, шовной и стыковой.
Для данного вида деталей наиболее рациональным методом соединения является холодная шовная сварка, характеризующая непрерывностью монолитного соединения. Шовная сварка обеспечивает большую производительность, легко автоматизируется, не требует высокой квалификации рабочих, дает прочное соединение; она отличается малым расходом электроэнергии и материалов.
Пластическое деформирование холодным способом дает достаточный уровень долговечности и является достаточно экономичным, так как для изготовления дополнительной детали (накладки) можно использовать бракованные корпуса. Восстановление буртов корпусов вкладышей путем сварки давлением заключается в том, что на их внутренней поверхности располагаются накладки (рисунок 3), на которые прикладывается давления от инструмента гидравлического пресса, схема процесса приведена на рисунке 4.
Рисунок 3. Эскиз
Рисунок 4. Схема процесса сварки
Для образования плотного сварного соединения необходимо в первую очередь тщательно очистить поверхности бурта и накладки, после чего поверхности деталей сблизить между собой настолько, чтобы произошло взаимодействие атомов металла деталей. Кроме того, часть металла бурта корпуса вкладыша при пластическом деформировании заполняет паз накладки, обеспечивая тем самым плотное неразъемное соединение. Таким образом, прикладываемое усилие от инструмента, должно быть необходимым и достаточным для создания условия пластического течения металла в области контакта.
Расчет необходимого рабочего усилия выполняется по известным формулам:
(1)
где: — контактная площадь, мм2.
(2)
где: — предел текучести металла, МПа.
По расчетному рабочему усилию выбирается прессовое оборудование из условия . Технологический процесс восстановления буртов корпусов вкладышей с применением сварки давление, представлен в виде структурной схемы на рисунке 5.
Рисунок 5. Структурная схема технологического процесса
Внедрение данной технологии в ремонтных локомотивных депо позволить увеличить производительность и качество ремонта корпусов вкладышей МОП, что в сложившихся условиях роста локомотивного парка и ужесточению требований к их эксплуатационной надежности, будет экономически оправдано.
Список литературы:
1. Обрывалин А.В. Анализ технологической готовности производства при ремонте моторно-осевых подшипников тягового электродвигателя ТЛ-2К1 / А.В. Обрывалин, А.Е. Ольшанская // Материалы науч.-практ. конф. Инновационные проекты и новые технологии в образовании, промышленности и на транспорте: Омский гос. ун-т путей сообщения. Омск, 2012. С. 131—137.
2. Шантаренко С.Г. Технологическое оснащение предприятий для ремонта колесно-моторных блоков электровозов / С.Г. Шантаренко, А.А. Лаптев, Е.В. Пономарев // Материалы науч.-практ. конф. Инновационные проекты и новые технологии в образовании, промышленности и на транспорте: Омский гос. ун-т путей сообщения. Омск, 2010. С. 49—58.
