РАЗРАБОТКА АЛГОРИТМА ДЛЯ АВТОМАТИЗАЦИИ ПРОЦЕССА ПУСКА ОБОРУДОВАНИЯ СЛОЖНЫХ ТЕХНОЛОГИЧЕСКИХ ПРОЦЕССОВ
Секция: 14. Ресурсосбережение
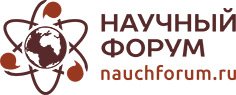
XXIII Студенческая международная заочная научно-практическая конференция «Молодежный научный форум: технические и математические науки»
РАЗРАБОТКА АЛГОРИТМА ДЛЯ АВТОМАТИЗАЦИИ ПРОЦЕССА ПУСКА ОБОРУДОВАНИЯ СЛОЖНЫХ ТЕХНОЛОГИЧЕСКИХ ПРОЦЕССОВ
Запуск высокотехнологичных агрегатов является сложной процедурой, состоящей из ряда операций, выполняемых последовательно или одновременно, конечным результатом которой является выход на рабочий режим оборудования либо технологических процессов, его использующих [4; 3].
При этом под рабочим режимом оборудования понимается такое состояние, при котором осуществляется получение продукта нужного качества в непрерывном режиме работы установки. Для процесса ректификации, например, под рабочим режимом понимается процесс получения дистиллята постоянного состава в непрерывном режиме.
Процесс вывода сложного технологического оборудования на рабочие режимы является строго формализованным и закреплен в соответствующих нормативных документах, чаще всего в технологических регламентах, которые в свою очередь содержат инструкцию с последовательностью операций, которые должен выполнить оператор. Однако, несмотря на строгую формализацию процесса пуска, эффективность его проведения во многом зависит от действий оператора, от уровня его квалификации опыта, опираясь на которые он самостоятельно определяет способ достижения требований, указанных в технологическом регламенте, например, определяет в какой момент времени и при каких внешних и внутренних условиях запускать каждую следующую операцию. При сложных взаимосвязях между операциями даже небольшие отклонения от технологического регламента, ошибка в определении условий окончания какой-либо операции или несвоевременного запуска следующей может усложнить процесс вывод агрегата/установки в рабочий режим, увеличить время запуска или создать условия, при которых установка вообще не сможет войти в рабочий режим. Таким образом ручной запуск высокотехнологичных агрегатов/установок является низкоэффективным и очень сильно зависит от человеческого фактора. В связи с чем разработка алгоритма для автоматизации пуска оборудования сложных технологических процессов является актуальной задачей для промышленных предприятий, позволяющей повысить безопасность и эффективность ведения сложных технологических процессов.
Для проведения работ по разработке алгоритма для автоматизации пуска оборудования сложных технологических процессов использована следующая методика:
1. Выбор объекта исследования;
2. Технологическое описание объекта исследования;
3. Описание основного оборудования, режимов работы установки и определение входных/выходных переменных процесса;
4. Определение последовательности технологических операций для запуска установки;
5. Описание процесса запуска оборудования по заданной последовательности операций;
6. Разработка алгоритма для автоматизации пуска оборудования установки.
Для проведения исследования необходимо осуществить выбор оптимального объекта. В качестве объекта для проведения данного исследования может быть выбран любой объект, обладающий следующими минимальными свойствами:
· быть наблюдаемым, то есть должна быть возможность в режиме реального времени получать информацию о значениях основных переменных, характеризующих состояние объекта управления;
· иметь структуру АСУТП, способную предоставить архивную информацию о ходе технологического процесса в стандартизированных форме и виде, понятных (подходящих) для проведения обработки данной информации;
· иметь возможность множественного проведения процедуры запуска для апробации предложенного алгоритма;
· обладать сложностью, иметь взаимосвязи между агрегатами и процессами, проходящими в них;
· иметь масштабируемую структуру АСУТП для возможности внедрения новых алгоритмов управления [2].
Для проведения исследования в данной работе в качестве объекта была выбрана экспериментальная лабораторная установка для разделения жидких смесей на тарельчатых ректификационных колоннах (рис. 1).
Рисунок 1. Внешний вид установки и главной мнемосхемы для осуществления управления
Технологическое описание установки для разделения жидких смесей на тарельчатых ректификационных колоннах [5].
Сырьевой продукт, в качестве которого используется водо-спиртовая смесь (с процентным содержанием спирта от 40 до 60 %) подается насосом в теплообменник, где подогревается до необходимой температуры. Подогретый продукт проходит через редуктор (для задания давления в трубопроводе) и направляется в сепаратор где разделяется на жидкую и паровую фазы. Паровая фаза отправляется в нижнюю (отгонную) часть колонны, а жидкая на верхнюю (выпарную) часть колонны. В колонне происходит процесс ректификации — массообменный процесс разделения многокомпонентных жидких смесей.
Обогрев нижней части колонны осуществляется рециркулирующим кубовым остатком, подогреваемым с помощью теплообменника. Таким образом, выходящий с нижней части кубовый остаток направляется в емкость сбора и частично уходит с установки, а частично насосом перекачивается обратно в колонну для поддержания протекания процесса ректификации. Важным показателем работы колонны является уровень в нижней ее части, поддержание которого на заданном уровне обеспечит защиту от так называемого «захлебывания» колонны и невозможности дальнейшего проведения процесса ректификации. Таким образом уровень в нижней части колонны К-101 поддерживается в заданном узком диапазоне. Пары из нижней части колонны поступают в низ ее верхней части, а жидкая фаза из верхней части переливается в верх ее нижней части. Пары из верхней части колонны поступают в дефлегматор, в котором они конденсируются. Сконденсировавшиеся в дефлегматоре пары стекают в виде флегмы через холодильник. Охлаждение необходимо для устойчивого длительного функционирования насоса подачи флегмы в верхнюю часть колонны. Далее охлажденная флегма поступает в сборник флегмы. Из нижнего слива, которого флегма поступает в насос и направляется потоком на верх верхней части колонны. Перед подачей в колонну флегма нагревается до требуемой температуры в теплообменнике. Другая часть флегмы отводится в виде дистиллята переливом через боковой штуцер данного сборника в вакуумируемый сборник дистиллята. Отбор дистиллята происходит самотеком, за счет разности высот между флегмовым и вакуумируемым сборником дистиллята.
Несконденсировавшиеся в дефлегматоре пары и газы поступают в ловушку, охлаждаемую льдом, которая нужна для снижения количества паров продукта, поступающих в вакуумный насос до минимально возможного. Особенно это важно при работе с натуральными нефтепродуктами. Слив сконденсировавшейся жидкости из ловушки осуществляется в линию флегмы. Из ловушки воздушная линия направляется в вакуумный коллектор. Туда же направлены воздушные линии из холодильника, из сборника флегмы и из сборника дистиллята.
В обе части колонны осуществляется непрерывный поддув азота из вакуум-коллектора в определенном количестве для обеспечения функционирования датчиков давления и уровня. Отдельно предусмотрена подача азота в нижнюю часть колонны, а также в сборники кубового продукта, флегмы и дистиллята для продувки.
На линии между вакуумным регулятором и вакуумным насосом установлена масляная ловушка, предназначенная для предотвращения попадания масла из насоса в вакуумируемую систему при внезапной остановке вакуумного насоса. К этой ловушке подсоединены вакуумные линии, ведущие к пробоотборникам, поскольку абсолютное давление в ловушке меньше, чем абсолютное давление в вакуумном коллекторе.
Вакуум в аппаратах установки создается масляным вакуумным насосом ВН, расположенном за пределами вытяжного шкафа. На линии сдувки выхлопа после вакуумного насоса расположен сепаратор выхлопа, предназначенный для предотвращения попадания масла из насоса в вытяжную вентиляцию по линии сдувки.
Установка функционирует в трех технологических режимах без учета аварийных режимов: режим пуска, режим останова и рабочий режим. Для поддержания технологических режимов лабораторная ректификационная установка обеспечена программно-техническими средствами АСУ ТП, имеющими трехуровневую иерархическую структуру. Верхний уровень представляет собой автоматизированное рабочее место оператора, реализованное на ПК с использованием SCADA “Genesis32”. Средний уровень реализован на основе ПЛК WAGO 750-841. Нижний уровень состоит из первичных преобразователей давления, температуры, расхода, отсечных клапанах, термостатах, перистальтических насосах. Выходом на рабочий режим в процессе эксплуатации лабораторной установки считается момент получения водо-спиртовой смеси, с содержанием спирта не менее 94 %.
Установка как объект автоматизации характеризуется 45 входными (контролируемыми) параметрами и 22 выходными (управляющими) переменными.
Экспериментальная установка для разделения жидких смесей перед пуском должна быть осмотрена, проверена ее исправность и готовность к работе всех аппаратов и трубопроводов, исправность контрольно-измерительных приборов, регуляторов температуры и давления в колонне, измерителей уровня жидкости в нижней части колонны приемниках ректификата, ректификационных емкостях и емкостях остатка.
Процесс «пуска-останова» ректификационной колонны должен проводиться в строго установленной последовательности.
Перед созданием системы автоматического пуска оборудования были проведены три запуска установки по заданной последовательности технологических операций и без применения специальных алгоритмов. В таблице 1 результаты данных запусков т. е. значения основных параметров, характеризующих процесс вывода на режим технологического оборудования.
Таблица 1.
Результаты запуска установки оператором-технологом без применения специальных алгоритмов
Расход исходного сырья, л/ч |
Температура низа |
Температура верха |
Расход флегмы в колонну л/ч |
Качество спирта % |
Время выхода на режим, мин |
0,09 |
90 |
84 |
2,43 |
81 |
123 |
0,09 |
90,5 |
79,5 |
0,9 |
88 |
91 |
0,09 |
100 |
75,2 |
1,147 |
94 |
54 |
Как видно из таблицы 1 время вывода оборудования на режим очень разнообразно изменяется от 123 минут до 54 минут и напрямую зависит от действий и опыта оператора, управляющего данной установкой.
Для реализации системы автоматизированного управления ректификационной установкой необходимо составить выполняющийся в строго установленной последовательности алгоритм, который должен быть формализован с помощью инженера-технолога. В ходе создания алгоритма, должны быть учтены все особенности процесса для оптимизации «пуска-останова».
Рисунок 2. Фрагмент алгоритма «пуска» установки
Разработанный алгоритм пуска был реализован в среде ProficyWorkflow [6] и интегрирован в виде подсистем в верхний уровень АСУТП, не изменяя ее структуры. Связь между существующей автоматизированной системой управления технологическим процессом и разрабатываемой системой поддержки оператора была установлена по средствам ОРС технологии. Структурная схема разработанной системы показана на рисунке 3. Для информирования оператора о ходе выполнения цикла технологического режима процесса «пуска-останова» экспериментальной установки в SCADA системе были созданы визуальные оповещения.
Рисунок 3. Структурная схема разрабатываемой системы
Для тестирования работоспособности алгоритма система была подключена к тренажеру, предназначенному для подготовки операторов к работе на действующей установке по разделению жидких смесей, и откорректирована для работы на модельной смеси «нонан-октан». В ходе экспериментов система показала наилучшие результаты по выходу на режим — 32 минуты. При проверке алгоритма на действующей установке получили время выхода на режим 50 минут с процентным содержанием спирта в дистилляте 95,6 %, что является лучшим результатом проведения всех экспериментов и напрямую доказывает эффективность разработанного алгоритма.
Система автоматизации на базе разработанного алгоритма позволила сократить время выхода на режим до 50 минут, что на 4 минуты и больше (в зависимости от опыта оператора) быстрее, чем запуск оборудования без специальных алгоритмов и повысить качество получаемого продукта на 1,6 %.
Таким образом система, основанная на разработанном в работе алгоритме, позволяет уменьшить вероятность ошибки оператора, которая может привести к уменьшению потерь сырья, энергоносителей, и непроизводительных потерь времени, а также позволяет снизить непродуктивную рабочую нагрузку на оператора и повысить безопасность ведения сложных технологических процессов.
Список литературы:
1. Дозорцев В.М. Компьютерные тренажеры для обучения операторов технологических процессов. — М.: СИНТЕГ, 2009. — 372 с.
2. Дитмар Шмид. Управляющие системы и автоматика: Техносфера, 2007, 584 с.
3. Лефлер Уильям. Переработка нефти, 2-е изд., пересмотренное / Пер с англ. — М.: ЗАО Олимп-Бизнес, 2004. — 224 с: ил.
4. Мановян А.К. Технология первичной переработки нефти и природного газа: Учебное пособие для вузов. 2-ое изд. — М.: Химия, 2001. — 568 с.
5. Технологический регламент по работе с лабораторной установкой «Тарельчатые ректификационные колонны».
6. Proficy* Workflow. Getting started/ Proficy SOA, V 2.00, 2012 — 130 p.
