ИССЛЕДОВАНИЯ СВОЙСТВ СВАРНОГО СОЕДИНЕНИЯ ИЗ СТАЛИ 12Х18Н10Т
Секция: 7. Материаловедение
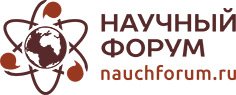
XXV Студенческая международная заочная научно-практическая конференция «Молодежный научный форум: технические и математические науки»
ИССЛЕДОВАНИЯ СВОЙСТВ СВАРНОГО СОЕДИНЕНИЯ ИЗ СТАЛИ 12Х18Н10Т
В процессе эксплуатации оборудования, машин и механизмов их детали часто работают в условиях контактирования с различными агрессивными средами и абразивными веществами, вызывающими не только износ [2]. В зависимости от условий взаимодействия металла со средой и их свойств, может протекать несколько видов коррозии: равномерная, питтинговая, межкристаллитная и растрескивание.
Известно, что структурно-фазовое состояние металла, формируещегося в процессе сварки и определеяющееся ее режими и способами, значительно влияет на физико-механические характеристики изделий. Изменение структуры и фазового состава конструкционных материалов при длительной эксплутации, зачастую, приводят к неблогоприятным последствиям.
В процессе сварки происходит диффузия элементов основного металла и сварочной проволки, приводящая к фазовым превращениям, изменению микроструктуры и свойств сварного соеденения в целом [3]. Сопротивляемость сварных соединений коррозионному разрушению, как правило, понижена вследствие теплофизического и химико-металлургического воздействия сварочного процесса, прежде всего на структуру металла в зоне формируемого неразъемного соединения, и связана с химическим составом металла шва и зоны термического влияния. В такой ситуации важной становиться проблема контроля качества сварных соединений.
Целью настоящей работы являеться исследование структуры, фазы, коррозионные свойства, а также на распределение механических свойств по зонам сварного соеденения из стали 12Х18Н10Т.
Материалы, оборудование и методики экспериментов.
В качестве материала исследования использавалась нержавеющая сталь аустенитного класса 12Х18Н10Т [1], сталь применяют в качестве коррозионностойкого и жаропрочного материала, хорошо сваривается всеми видами ручной и автоматической сварки. Для проведения исследований были сварены при помощи ручной дуговой сварки и изготовлены образцы. Регистрация наблюдаемых микроструктур поверхности сварных соединений осуществлялась на оптическом микроскопе Neophot-21, рентгеноструктурный анализ на дифроктометре ДРОН-3, а измерения микротвердости в зонах сварных соеденений проводилось на микротвердомере ПМТ-3 при нагрузке на индентор 0,98Н.
Коррозионные испытания образцов со сварными соединениями стали 12Х18Н10Т проводились методом (метод Хью), погружения в кипящий раствор, 65 % раствор концентрированной азотной кислоты Продолжительность испытаний составила 48 часов. После испытаний сварных соединений проводились исследования коррозионного разрушения сварных швов и ЗТВ.
Таблица 1.
Параметры образцов для испытания на коррозию
№ |
Образец |
S,см2 |
ρ,г/см3 |
1 |
12Х18Н10Т |
0,047 |
7,9 |
2 |
0,051 |
До погружения образцы были отшлифованы и обезжирены.
Схема аппаратуры для испытания на коррозию:
Колба Эрленмеера, закрываемая, либо четырехшариковым холодильником со шлифом (рисунок 1).
Рисунок 1. Схема установки для испытания на коррозию 1 — пробка-холодильник; 2 — задержки конденсата; 3 — колба Эрленмеера
Скорость коррозии K1 или K2 определяют по формулам:
, г/мм2 (1)
, мм/год (2)
Результаты экспериментов и их обсуждение.
Известно, что структура и свойства сварного соединения сильно зависят от энергетических параметров технологического процесса его получения [4].
Как показали результаты металлографических исследований сварной шов в стали характеризуется отчетливой границей раздела с основой и более мелкозернистой структурой (рисунок 2).
Рисунок 2. Микроструктура участка стали со сварным швом: а, б — граница сварного шва (левый участок) и основы (правый участок), в — микроструктура сварного шва
В структуре сварного соединения не обнаруживается неоднородная зона термического влияния (рисунок 2), как правило, различающаяся от основы существенно более высокой твердостью, что свидетельствует о высоком качестве сварки.
Ниже приведены результаты испытания образцов на микротвердость (рисунок 3). Как показали экспериментальные данные, сварной шов обладает низким значением микротвердости (на 22 % ниже) по сравнению с основой, а близлежащая к шву зона наоборот характеризуется несколько повышенной твердостью (на 6 % больше) (рисунок 3).
Таблица 2.
Результаты по потере массы сварного шва
№ |
Время испытания, ч |
Потеря массы, г |
Скорость коррозии,г/мм2 |
Скорость коррозии,мм/год |
1 |
48 |
0,01 |
0,013 |
0,15 |
2 |
48 |
0,02 |
0,025 |
0,14 |
Рисунок 3. Гистограмма микротвердости стали: 1, 5 — основа стали, 2 ЗТВ — зона термического влияния с левой стороны от шва; 3 — сварной шов; 4 ЗТВ — зона термического влияния с правой стороны от шва
Исходная аустенитная структура — гранецентрированная кубическая (ГЦК) преобразуется в мартенсит — объемноцентрированную тетрагональную (ОЦТ) при прокатке стали, а в случае сварки стали сохраняется в виде аустенита (рисунок 4). Как видно из рентгеновских дифрактограмм (рисунок 4), после сварки обнаруживаются те же рефлексы аустенита γ-Fe (рисунок 4, б), разница лишь в том, что интенсивности линий от участка со сварным соединением намного ниже, чем у основы.
Рисунок 4. Рентгеновские дифрактограммы стали: а — от основы, б — от участка со сварным швом
Заключение.
1. Установлено, что исходная аустенитная структура (ГЦК) преобразуется в мартенсит (ОЦТ) при прокатке стали, а в случае сварки стали сохраняется в виде аустенита.
2. Сварной шов в стали характеризуется отчетливой границей раздела с основой, пониженной микротвердостью и более мелкозернистой структурой.
3. В структуре сварного соединения нет неоднородной зоны термического влияния, как правило, различающаяся от основы существенно более высокой твердостью, что свидетельствует о высоком качестве сварки.
4. Установлена скорость коррозии сварного соеденения, как показывает результаты испытания шов стойки к коррозий, и оцениваеться в 4,5 балла по десятибальной шкале.
Список литературы:
1. Кайбышев О.А. Пластичность и сверхпластичность металлов / О.А. Кайбышев. — М.: Металлургия, 1975. — 280 с.
2. Куртепов М.М. О коррозии аппаратуры из нержавеющих сталей при концентрировании выпариванием ра¬диоактивных отходов // Атомная энергия, 1965. — Т. 19, № 2. — С. 153—157.
3. Рогачева Л.В. Исследование структуры и свойств сварного шва / Свердловск УПИ им. С.М. Кирова, 1981. — 14 с.
