ЛАЗЕРНАЯ РЕЗКА ТВЕРДЫХ ПОВЕРХНОСТЕЙ
Секция: 5. Лазерные технологии
лауреатов
участников
лауреатов


участников


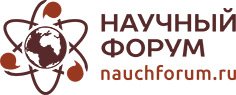
XXXIII Студенческая международная заочная научно-практическая конференция «Молодежный научный форум: технические и математические науки»
ЛАЗЕРНАЯ РЕЗКА ТВЕРДЫХ ПОВЕРХНОСТЕЙ
Лазерной резкой или разделением называется процесс достаточно быстрого локального нагрева, плавления и испарения материалов остросфокусированным лазерным излучением[1]. По виду воздействия на материал лазерный луч аналогичен газовому пламени и плазменной дуге (тепловой источник), однако концентрация его мощности на несколько порядков выше и составляет 106 –107Вт/см2.
Существуют несколько основных видов лазерной резки: резка в режиме испарения и резка в режиме плавления.
При резке в режиме испарения температура материала разогревается до температуры кипения и вещество из канала реза удаляется в парообразном состоянии. Механизм испарения характерен для материалов, в которых энергия удельного испарения мало отличается от удельной энергии плавления, например, для ситала. Резка в режиме плавления характерна для металлов при действии на них непрерывного изучения для удаления расплава в зону обработки подается струя газа – это режим при низких скоростях резки характеризуется образованием и удалением расплава. Качества реза при этом не высокое, увеличение же скорости резки переводит процесс в стационарный режим и качества реза увеличивается.
Основными недостатками механических методов резки являются потери в материалах, низкая производительность процесса, износ и поломка инструмента, все это результат контакта инструмента с материалом.
Основные недостатки термических методов низкое качество реза и невозможность обработать неметаллических материалов. Здесь бессильна и газопламенная и плазменная технология.
Лазерной резке поддаются практический все материалы не зависимо от твердости. Благодаря отсутствие механических усилий могут разрезаться не жесткие материалы, а жесткие лишь фиксироваться без специального закрепления[2,3]. При этом обеспечиваются высокая точность и качество реза (малая ширина и параллельные кромки), малая зона нагрева, большая производительность процесса и возможности точного, автоматизированного управления.
Лазерной резке одинаково легко поддаются такие высокотвердые материалы, как металлокерамика, стеклоуглерод, композиционные материалы на основе нитей бора и углерода и тугоплавкие материалы (вольфрам, рений, тантал, молибден и др.) [4].
Высокое качество реза достигается при лазерной резке стеклоткани, наряду с этим улучшаются условия труда за счет уменьшения количества стеклопыли по сравнению с механической резкой[4].
Таким образом преимущества лазерных методов резки материалов заключается в следующем:
1) Возможность разделения лазером обширного класса материалов независимо от их твердости;
2) Возможность получения узких разрезов с минимальной зоной термического влияния в результате острой фокусировки обеспечивающей локальность нагрева;
3) Практический полное отсутствие механического воздействия на обрабатываемый материал (возможна обработка легкодеформируемых и нежестких материалов), в связи с чем отпадает необходимость в закреплении образца можно ограничиться лишь фиксацией;
4) Высокая производительность процесса;
5) Возможность контроля и строгой регламентации пребывания материала при высоких температурах в случае применения лазеров импульсного периодического действия;
6) Возможность полной автоматизации процессана высоком уровне. В состав автоматизированного лазерного комплекса обычно входят лазер с источником питания, система управления;
7) Осуществление многопозиционной обработки.
В то же время применение лазерного излучения для резки материалов нельзя считать универсальным средством. Из недостатков стоит отметить глубина проникновения излучения в вещество, имеет ограничение. связанное как с естественной расфокусировкой пучка так и с погашением части излучения на стенках канала. К основным недостаткам лазерной резки относят низкий КПД установки и высокую стоимость оборудования[1].
Целью данной работы является подбор оптимальных режимов лазерной резки на различных твердых поверхностях с помощью импульсного инфракрасного Nd:YAG лазера с длиной волны 1064 нм. Максимальная мощность лазерного излучения составляет 110 Вт, частота следования импульсов 10 кГц и длительность импульса 84 нс.
В процессе лазерной резки средняя мощность лазерного излучения изменялась в диапазоне от 5.4 Вт до 88.9 Вт, скорость перемещения лазерного луча по поверхности для всех образцов составила 1 мм/сек., диаметр лазерного пятна на поверхности образца изменялся в пределах от 300 до 560 мкм. Лазерную резку проводили на поверхностях пластмасс различного цвета и жести. В таблице 1 отображены режимы лазерной резки для каждой из твердой поверхностей. На рисунке 1 наглядно отображены режимы лазерной резки различных поверхностей.
Таблица 1.
Режимы лазерной резки твердых материалов
Материал |
Средняя мощность лазерного излучения, Вт |
Скорость перемещения, мм/сек. |
Диаметр лазерного пятна на поверхности образца,мкм |
Пластмасса (черная) |
5,4 |
1 |
300 |
Жесть |
88,9 |
1 |
320 |
Пластмасса(оранжевая) |
7,8 |
1 |
360 |
Пластмасса (желтая) |
9.7 |
1 |
960 |
Рисунок 1. Результаты лазерной резки Nd:YAG лазером с длиной волны 1064 нм а)пластмасса(черная); б) пластмасса(оранжевая);в)жесть; г)пластмасса (желтая)
На качеств лазерной резки существенно влияют такие параметры как: средняя мощность лазерного излучения, скорость перемещения лазерного пятна по поверхности, диаметр лазерного пятна на поверхности материала, физические свойства материала, вид лазерной резки, длина волны, и длительность импульса, а также вид лазерной резки. Лазерная резка металлов требует гораздо большей плотности мощности лазерного излучения, и максимальное качество лазерного излучения, т.е. фокусировки лазерного луча в минимальное возможное пятно.
Список литературы:
1. Григорьянц А.Г., Шиганов И.Н., Мисюров А.И. Технологические процессы лазерной обработки: Учеб. пособие для вузов / Под ред. А.Г. Григорьянца. - М.: Изд-во МГТУ им. Н.Э. Баумана, 2006. – 664 c.
2. Лазерные технологии обработки материалов: современные проблемы фундаментальных исследований и прикладных разработок. Под ред. В.Я. Панченко. – М.: Физматлит, 2009, 664 с.
3. Ковалев О. Б. Фомин В. М. Физические основы лазерной речки толстых листовых материалов. — М ФИ.'Ш ЛТ.Л ИТ. 2013 — 256 с.
4. Григорьянц А.Г. Основы лазерной обработки материалов. – М.: Машиностроение, 1989. – 304 c.
