ОПТИМИЗАЦИЯ РАСЧЁТА РАБОЧЕГО КОЛЕСА ЦЕНТРОБЕЖНОГО НАСОСА
Секция: 8. Машиностроение
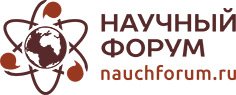
XXXV Студенческая международная заочная научно-практическая конференция «Молодежный научный форум: технические и математические науки»
ОПТИМИЗАЦИЯ РАСЧЁТА РАБОЧЕГО КОЛЕСА ЦЕНТРОБЕЖНОГО НАСОСА
Центробежный насос относится к классу динамических машин, в которых перемещение жидкости и требуемый напор создаются за счёт центробежной силы, возникающей при воздействии лопастей рабочего колеса на жидкость. Общий принцип действия основан на использовании сил инерции и вязкости.
Центробежный насос получили широкое применения во многих сферах человеческой деятельности:
· для перекачивания чистой (холодной/горячей) воды в системах водоснабжения структур ЖКХ, муниципальных водоканалов;
· в системах подачи технической воды обеспечивая технологические процессы промышленных предприятий нефтеперерабатывающей и металлургической отрасли;
· для обеспечения водой садоводческих и дачных посёлков;
· в системах пожаротушения жилых и гражданских объектов;
· для подъёма жидкостей на артезианских колодцах и буровых скважинах;
· на объектах ТЭЦ, АЭС, для обеспечения работы основных и вспомогательных систем станций, связанных с использованием чистой и технической воды [1,2].
Широкая область применения центробежного насоса во всех отраслях промышленности и народного хозяйства, является доказательством весьма обширной распространённости данного агрегата. Изучение устройства и принципа действия насоса, с целью совершенствования конструкции и повешения эффективности работы, является весьма актуальной задачей.
На начальной стадии проектирования любого агрегата проводится предварительный расчёт. Для центробежного насоса, весьма подробно описана методика расчёта в работе А.А. Ломакина [3]. Это издание является достаточно устаревшим для технической литературы, однако, этот источник и его второе издание и в настоящее время продолжают оставаться одной из лучших работ по лопастным насосам, как в отечественной, так и в зарубежной литературе.
В данной методике расчёта велика вероятность ошибки, вызванная человеческим фактором. В расчётных формулах имеется 13 констант, которые выбираются из заданного диапазона. Каждая константа имеет описание и рекомендации по её выбору. Не смотря на это, зачастую достаточно сложно подобрать единственное верное значение. Например, выходной угол лопасти выбирают из диапазона , где большие значения угла соответствуют тихоходным колёсам, средние - средним колёсам, меньшие - быстроходным колёсам. Коэффициент быстроходности колеса центробежного насоса лежит в пределах
. Из этого следует: что если
, то возникает сложность и неточность в определении класса быстроходности колеса и как итог, неточность выбора выходного угла лопасти. Так же имеется недостаток, связанный с округлением промежуточных величин при расчёте параметров насоса.
Ошибка или неточность в расчётах приводят к неверным геометрическим и параметрическим значениям насоса, которые на конкретном изделии приведут к появлению кавитационный явлений, к возникновению вихревых ударных и диффузорных потерь, к увеличению объёмных потерь, возникновению дополнительной закрутки потока и появлению обратных токов. Важно особо точно определить геометрию входа в колесо т.к. именно эта часть насоса определяет картину течения жидкости во всём агрегате [4,5].
Вследствие выше указанных факторов, снизится полный КПД насоса, повысится энергопотребление. В конечном счете, эти явления спровоцируют быстрый износ или выход из стоя агрегата.
В настоящее время стратегией развития многих государств является энергосбережение. Наша страна, не исключение, так в статье 24 Федерального Закона № 261-ФЗ [6] предъявляются требования по сокращению энергетических ресурсов, в размере трёх процентов ежегодно на предприятиях муниципальной и бюджетной сферы. Программа Правительства РФ «Энергоэффективность и развитие энергетики», подпрограмма «Энергосбережение и повышение энергоэффективности» [7] предполагает сокращение издержек на все виды энергоресурсов.
Любое предприятие озадачено вопросами энергосбережения и повышения ресурса работы агрегата. Например, при выплавки стали в доменной печи, круглосуточную работу по перекачке охлаждающей воды выполняют центробежные насосы. Неэффективная работа или выход из строя насоса, может привести к серьёзному ущербу для предприятия.
Авторами данной статьи многократно проводился расчёт рабочего колеса центробежного насоса по методике «ручного» расчёта по [3]. В связи с часто встречаемой большой погрешностью между величинами, определяемыми в конце расчёта, нами предлагается программа по оптимизации расчёта канала колеса центробежного насоса. Программа основана на поиске оптимального значения коэффициентов, используемых в расчётных формулах. Программа сохранена в формате .exe и может свободно использоваться в независимости от пакета, в котором она написана. Программа написана на языке Pascal.
Анализ формул, входящих в расчет, показал, что часть коэффициентов влияет на погрешность коэффициента стеснения dk1, а другая часть на коэффициент стеснения dk2. На рис. 1 представлена обобщенная блок схема, которая показывает наличие в программе два вида циклов, в зависимости от влияния коэффициента. В начале программы мы вводим исходные данные: расход, напор, давление, число оборотов и необходимое число лопастей. Далее, математический пакет производит расчет в автоматическом режиме. При этом операторы, показанные в циклах, это все формулы, кроме той, которая включает в себя эмпирический коэффициент, рассматриваемый в данный момент.
Рисунок 1. Обобщённая блок схема
Программа включает в себя 13 циклов. Расчет происходит по принципу последовательного приближения. Для каждого коэффициента может выбраться определенный шаг, на который он будет изменяться при последующем повторении. На каждый шаг происходит сравнение погрешностей с предыдущим шагом, в том случае, если погрешность уменьшается, коэффициент становится эталонным и сохраняется в памяти программы. Если же происходит увеличение погрешности, то шаг просто пропускается, а коэффициент, находящийся в памяти остается без изменений. За начальный эталонный коэффициент берется минимально возможный, затем при каждом шаге происходит его увеличение в зависимости от выбранных параметров деления.
Данная структура помогает уменьшить используемую программой память, кластер содержит информацию только о двух значениях, вместо множества, если бы использовались матрицы и массивы. Таким образом, мы получаем постепенное уменьшение погрешности, шаг за шагом. Цикл перебирает ровно столько значений, сколько шагов было выбрано. По истечении счетчика в памяти сохраняется минимальное значение погрешности и коэффициент, при котором эта погрешность была достигнута. Далее происходит переход на новый цикл, где происходит аналогичное действие, только со следующим значением.
Важно отметить, что массив имеет место в расчете. Он содержит в себе значения диаметра вала, которые принимаются исходя из ГОСТа. Блок схема выбора диаметра вала представлена на рис. 2.
Рисунок 2. Блок схема для определения диаметра
После того, как произошел расчет диаметра, это число округляется и сравнивается со значениями, находящимися в массиве ГОСТ. Если оно после округления равняется одному из значений находящихся в массиве, то величина остается неизменной и сохраняется для последующего использования в других формулах. Если же подходящего значения нет, то округленная величина увеличится на единицу, далее опять сравнивается. Так происходит до тех пор, пока не найдется нужное значение по ГОСТу.
На рис. 3 представлено рабочее окно программы, в котором проектировщиком вводятся исходные данные.
Рисунок 3. Рабочее окно программы
Важно отметить, что в список ввода исходных данных входит число лопастей, в дальнейшем этот параметр планируется внедрить в программный цикл, для автоматического выбора количества лопаток. Как только пользователь ввел все исходные значения, рабочая область дополняется строчками расчета, представленными на рис. 4.
Рисунок 4. Вывод результатов расчёта
Программа отображает все необходимые значения коэффициентов, в дальнейшем, для удобства использования они будут выводиться с пояснениями. Для точности полученных данных, все расчеты производятся без ручного округления. На двух последних строчках представлены самые важные показатели, погрешности в долях. В случае если значение хотя бы одного из них составляет более 0,02 данные введенные предварительно пользователем некорректны, опираясь на условие метода расчета А.А. Ломакина[3], допустимая погрешность менее 2%.
В результате программа выдаёт итоговую погрешность менее 1%, что говорит о высокой точности расчёта геометрических и параметрических значений рабочего колеса центробежного насоса.
Благодаря использованию данной программы сокращается время расчёта, одновременно увеличивается точность и достоверность полученных данных.
