Оценка усталостной прочности конструкционных материалов и деталей машин
Конференция: XXI Международная научно-практическая конференция «Научный форум: инновационная наука»
Секция: Технические науки
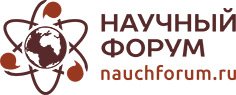
XXI Международная научно-практическая конференция «Научный форум: инновационная наука»
Оценка усталостной прочности конструкционных материалов и деталей машин
ESTIMATION OF FATIGUE STRENGTH OF CONSTRUCTION MATERIALS AND MACHINE DETAILS
Vladimir Kapralov
dr. tech. sciences, St. Petersburg Polytechnic University of Peter the Great, Russia, St. Petersburg
Nguyen Ngoc Thuan
graduate student, St. Petersburg Polytechnic University of Peter the Great, Russia, St. Petersburg
Аннотация. Усложнение эксплуатационных условий и реальной переменной нагруженности ответственных деталей энергетических машин требует расширения комплекса работ по уточнению оценок их усталостной прочности, долговечности и ресурса за счет совершенствования экспериментов.
Abstract. The increasing complexity of operating conditions and the actual variable loading of responsible parts of energy machines requires the expansion of the complex of works to refine the estimates of their fatigue strength, durability and resource by improving experiments.
Ключевые слова: усталость конструкционных материалов и деталей машин; накопление повреждений; случайные эксплуатационные нагрузки; прогнозирование долговечности.
Keywords: fatigue of structural materials and machine parts; damage accumulation; random operating loads; durability prediction.
Введение. В процессе эксплуатации энергетических машин напряжения, возникающие в деталях, в большинстве случаев переменны во времени и являются случайными функциями условий эксплуатации и времени. Они часто определяют их надежность и ресурс. При превышении уровня переменных напряжений определенного предела в материале детали происходит процесс накопления усталостных повреждений. Такой процесс называют усталостью металла, а соответствующее разрушение – усталостным. Проблема повышения надежности машин исключением разрушений вследствие усталости конструкционных материалов актуальна в большинстве отраслей машиностроения. Актуальность особенно велика в отраслях, где аварии вследствие разрушения ответственных деталей ведут к катастрофическим последствиям (энергетика, космонавтика, авиация, транспорт всех видов и т. д.). Для корректной оценки надежности и ресурса ответственных деталей, подверженных переменным нагрузкам, условия испытаний на усталость приближаются к эксплуатационным условиям. Целью данной работы является совершенствование расчетно – экспериментальных методов оценок надежности машин за счет приближения условия испытаний к эксплуатационным нагрузкам.
Методы проведения исследований. Деталь любой сложности можно представить как сочетание гладких элементов и элементов с конструктивными концентраторами механических напряжений. Вследствие этого, в первом приближении, можно исследовать гладкие образцы для оценки усталостных свойств материала. Экспериментов такого типа достаточно[2][3][4].
Оптимальная организация усталостных экспериментов представляет собой, иногда, сложную и важную задачу для оценок прочности, надежности и ресурса проектируемой машины. Для проведения экспериментов на усталость применяются испытательные машины различных типов. Тип испытательной машины определяется из целей работы и возможностей экспериментатора.
В зависимости от процесса изменения во времени напряжений в образце различают усталостные испытания при нагружении гармоническом (симметричный, асимметричный цикл), бигармоническом (наложение двух или более гармоник), программном (изменение амплитуды напряжений по этой некоторой программе) и случайном при различных типах случайных процессов. Габаритные размеры испытуемых образцов и развиваемые в установках усилия изменяются в широких пределах (например, диаметры образцов варьируются от 1 до 300 мм). Созданы установки для испытаний с имитацией эксплуатационных условий (пониженные и повышенные температуры, коррозионные среды, включая жидкие расплавленные металлы, вакуум и т.д.)
Частоты нагружения могут изменяться от нескольких циклов в минуту до 10-20000гц. и выше.
Усталостные испытания деталей машин.
Блок-схема установки для резонансных усталостных испытаний деталей такой сложной конструкции как консольные лопатки турбин или компрессоров, элементов трубопроводов и других деталей показана на рисунке 1. Установка предназначена для усталостных испытаний в резонансном режиме детали или образца на частоте одной из собственных форм колебаний. Для проведения таких испытаний небходимо знание спектра собственных частот и вида распределения переменных напряжений на частоте испытаний. Распределение переменных напряжений на поверхности деталей необходимо для установления мест наибольшей напряженности (мест вероятного усталостного разрушения).
Основа установки электродинамический вибростенд.
Рисунок.1. Блок-схема резонансных усталостных испытаний консольных лопаток турбин и компрессоров, элементов трубопроводов и других деталей на базе электродинамического вибростенда
Конструктивное исполнение электродинамических стендов различно.
Усилие, создаваемое силовой катушкой на платформе может быть различным (от долей килограммов до нескольких тонн).
Вибраторы электромагнитного типа конструктивно выполняются поразному.
Изменяя частоту магнитного поля можно получить резонансные колебания образца на одной из собственной частот. Испытания проводятся в резонансном режиме. В случае, если образец не располагает магнитными свойствами (помимо магнитной накладки) может использоваться развернутый камертон, часть которого выполняется из магнитного материала.
Пьезоэлектрические вибраторы
Пьезоэлектрические вибраторы представляют собой устройство которое работает по принципу противоположному принципу работы вибродачика. Они применяются для получения больших частот при малых весовых характеристиках установок.
Материалы пьезоэлементов те же, что и для вибродатчиков.
Пневматические или воздушные вибраторы (высокочастотные усталостные испытания)[19].
Возбуждение колебаний может осуществляться прерывающимся воздушным потоком. Воздушная струя создается истечением воздуха под давлением 5 – 7 кГ/мм2 из сопла. Сопла могут различных конструкций и диаметров. Прерывается поток диском с отверстиями или выступами. Требуемое число отверстий (или выступов) и частота вращения модулирующего диска определяются из требуемой частоты возбуждения испытываемой детали или узла. Связь этих величин понятна: f = nZ, здесь f – частота возбуждения, n – частота вращения модулирующего диска в герцах, Z – число отверстий (или выступов).
При проведении резонансных усталостных испытаний частота возбуждения, т.е. одна из собственных частот колебаний детали, как правило, определяется заранее.
Подобные испытания чаще всего проводятся с рабочими лопатками осевых компрессоров или турбин. Хотя бывают потребности исследования и других деталей и узлов. Возбуждение устойчивых резонансных колебаний в деталях требует стабилизации частоты вращения диска прерывающего струю. Это необходимо из-за сравнительно высокой добротности резонансных кривых деталей. Известно, что отклонение возбуждающей частоты от резонансной на 0,02% может привести к уменьшению амплитуды колебаний на 50%.
Стабилизация частоты вращения вала модулирующего диска осуществляется переменным током с согласованными частотой и напряжением. Источником питания стабилизирующего двигателя служит генератор звуковой частоты с усилителем. Выход на стабилизированный режим осуществляется специальным устройством для ввода системы в синхронизм.
В режиме синхронизации частота вращения вала модулирующего диска жестко связана с частотой, задаваемой генератором звуковой частоты. Регулировать частоту вращения в этом режиме можно при помощи генератора звуковой частоты.
Особенность подобных экспериментов в необходимости определять одну или несколько из спектра собственных частот детали и все испытания проводить по одной выбранной форме колебаний на незначительно отличающихся частотах.
Экспериментальное, расчетное и рачетно-экспериментальное определение собственных частот и форм колебаний детали или образца.
Каждой из собственных частот соответствует своя строго определенная форма колебаний, т.е. определенное распределение прогибов и переменных механических напряжений по профилированной части лопатки.
Применяются различные способы оценок собственных частот колебаний детали и исследования форм колебаний а также распределения напряжений при различных формах колебаний. Вот некоторые из них.
Формы колебаний методом песочных фигур (традиционный метод) получаются, если колебаниям на собственной частоте подвергнуть лопатку, установленную горизонтально, с насыпанными на нее тонким слоем сухого мелкого песка или талька. Метод этот применим только для сравнительно больших деталей (на мелких узловые линии, обозначенные песком, не видны) и обязательно с малой закруткой.
В процессе колебаний песок будет сброшен со всех мест поверхности лопатки, кроме узловых линий. Рис.2.[12]
Рисунок. 2. Затемненными местами показаны узловые линии на которых разместился песок. 1,2,3 – изгибные формы колебаний, 4 – крутильная форма, 5,6 – сложные изгибно-крутильные формы колебаний лопаток
Метод собственных колебаний предполагает возбуждение лопатки одиночным и весьма кратковременным импульсом. Спектр короткого импульса широк и непрерывен, следовательно энергия сигнала распределена по всему частотному диапазону, а не сосредоточена на нескольких отдельных частотах.
Вибрационный отклик конструкции на единичный импульс непрерывен в широком частотном диапазоне и будет иметь пики на собственных частотах конструкции. Схема ударного теста представлена на рис. 3а. Получающаяся в результате теста кривая в координатах амплитуда-частота располагает пиками, положение которых вдоль горизонтальной координаты (частоты) будет соответствовать значениям собственных частот конструкции (рис. 3б).
Методика ударного теста предполагает наличие специального анализатора сигнала с пъезодатчика - анализатора, выполняющего быстрое преобразование Фурье (БПФ). На рис. 6б приведена типичная кривая отклика конструкции на удар, полученная с помощью анализатора БПФ.
а) б)
Рисунок.3. Схема возбуждения колебаний и результат анализа собственных частот
Голографическая интерферометрия – это распространенное средство исследования колебаний деталей и узлов турбомашин. В основе таких установок источники когерентного света – оптические квантовые генераторы (ОКГ) или лазеры. Когерентный свет располагает постоянной длиной волны и почти постоянную начальную фазу. Принцип голографической интерферометрии был разработан в середине прошлого века и базируется на голографическом восстановлении волн.
Интерференционные полосы на восстановленном изображении представляют положение линий равных размахов колебаний точек поверхности лопаток (рис. 4).
Аналитические решения задачи оценки собственных частот и форм колебаний элементов конструкции турбин имеют достоинства и недостатки: к достоинствам следует отнести получение явных функциональных зависимостей собственных частот от основных геометрических параметров деталей, а также от свойств материалов; к недостаткам следует отнести существенные отличия в геометрии между упрощенной расчетной моделью и реальной деталью, а также упрощения в описании закрепления деталей; аналитические решения редко учитывают статическое напряженное состояние детали на собственные частоты[8][16].
Значительно больше возможностей по учету особенностей геометрии и условий закрепления лопаток и дисков предоставляют численные методы, среди которых доминирующее положение занимает метод МКЭ – метод конечных элементов.
В практике машиностроения используются такие опытные методы определения форм колебаний деталей турбомашин: метод использования песочных фигур (фигур Хладни); метод демпфирования; метод голографической интерферометрии; метод лазерно-компьютерной спекл-интерферометрии; лазерная виброметрия, основанная на эффекте Доплера.
Существуют несколько способов исследования распределения напряжений при колебаниях деталей на собственных частотах: препарирование тензорезисторами и регистрация их показаний в процессе колебаний на нужной форме; использование специальных лаковых покрытий (вид сетки растрескивания покрытий зависит от интенсивности переменных деформаций в различных местах поверхности детали); расшифровка восстановленных голографических интерферограмм; определение частот, деформаций и напряжений вибрирующей поверхности с помощью лазерного сканирующего доплеровского виброметра.
Измерение переменных деформаций и (или) напряжений на поверхностях при помощи лазерного измерителя вибраций базируется на применении метода видео-триангуляции.
Рисунок. 4. Интерферограмма и результаты ее обработки.
а) - интерферограма, б) - эпюры прогибов кромок, в) - распределение нормальных напряжений σ и максимальных касательных напряжений
Результаты исследования
При резонансных усталостных испытаниях испытуемый образец (лопатка) препарируется тензорезисторами для определения уровня задаваемых напряжений (деформаций). Испытуемый образец (лопатка) препарируется тензорезисторами, приклеивамыми в места наибольших напряжений при вобуждении колебаний на определенной собственной частоте.
Принимая во внимание весьма значительный разброс усталостной прочности даже стандартных образцов из материала одной плавки погрешность измерения механических напряжений (деформаций) играет при резонансных испытаниях существенную роль.
Суммарная дисперсия величин переменных механических напряжений (относительных деформаций), т.е. характеристика рассеивания замеренных величин в случайной выборке из партии лопаток, может быть представлена как сумма дисперсий отдельных составляющих погрешностей:
здесь: - дисперсия механических напряжений, вызванная i– той составляющей погрешностей.
Предполагается, что рассеивание механических напряжений вызывают следующие наиболее значимые независимые факторы, каждый из которых определяет собственное рассеивание, характеризуемое парциальной дисперсией: от нестабильности физических свойств материала лопаток (плотности, модуля Юнга, структурной неоднородности и т. д.) и изменчивости геометрических размеров в пределах чертежных допусков – ; от нестабильности свойств тензорезисторов, в том числе электрическое сопротивление, разброс коэффициента тензочувствительности, свойств клея т.д.
; вызванная различной жесткостью конкретного защемления лопаток в приспособлении на столе вибростенда, приводящей к изменению линии прогиба лопаток при колебаниях -
; за счет погрешностей тарирования -
; за счет нелинейности амплитудно-частотной характеристики тензометрического усилителя -
; за счет погрешности измерения стрелочным прибором -
; за счет погрешности измерения амплитуды колебаний при помощи оптического микроскопа -
.
Упомянутые факторы можно считать независимыми и поэтому:
=
+
+
+
+
+
+
+
;
- остаточная дисперсия, обусловленная суммарным влиянием факторов, не учтенных в эксперименте.
Последнее выражение можно представить так:
=
+
+
;
здесь - дисперсия, вызываемая средствами измерения. Она оценивается по многократным измерениям одной лопатки.
Анализ парциальных составляющих суммарной дисперсии осуществляется с учетом особенностей рассматриваемого фактора.
Дисперсия от нестабильности свойств тензорезисторов и дисперсия, вызванная различной жесткостью защемления оценивалась специальным исследованием экспериментально.
Дисперсия тарировки определяется таким образом:
где - оценка значения yi по уравнению регрессии, n - количество замеров при тарировке.
Величина дисперсии не зависит от xi=yi.
Составляющие суммарной дисперсии определяемые замерами по стрелочному прибору , погрешности измерения амплитуды при помощи оптического микроскопа
и несовершенством амплитудно–частотной характеристики тензометрического усилителя
определяется из того, что половина размаха погрешности соответствует трем величинам стандартного отклонения. Предполагая, что функция распределения замеров в пределах допустимой погрешности подчиняется нормальному закону распределения и
соответствует погрешности оценки, определяем
Материалы исследования показывают, что
40 – 45% суммарной дисперсии составляет рассеивание геометрических размеров лопаток
Дисперсия замеров механических напряжений (собственно погрешность измерений) составляет, примерно, 50% суммарной. Существенную часть дисперсии замеров занимает погрешность тарировки. Остаточная дисперсия
содержит не учтенные погрешности измерения и ошибки при учете учитываемых составляющих дисперсии.
Т.О. Коэффициенты вариации погрешностей замеров переменных механических напряжений тензорезисторами составляют, примерно, 11-13%. Повышение стабильности свойств тензорезисторов может снизить погрешность замеров переменных механических напряжений до минимальных пределов 7-10%.
Испытания на усталость при колебаниях близких к реальным, эксплуатационным.
Задача определения срока службы (долговечности) конструкции из-за разрушений вследствие усталости решается созданием в эксперименте на усталость случайного процесса переменного нагружения детали с максимальным приближением к эксплуатационному.
Создана и успешно использована блок – схема испытаний на усталость при случайных колебаниях представленная на рисунке 5. Блок – схема разработана и реализована применительно к рабочим лопаткам газовой турбины в условиях нормальной температуры.
Рисунок. 5. На рисунке цифрами обозначены: 1 – подвижный стол электродинамического вибростенда, 2 – электродинамический вибростенд, 3 – стойка белого шума (3a и 3b – дисплеи ), 4 – вибродатчик обратной связи (установлен на подвижном столе вибростенда ), 5- бесконтактный датчик колебаний лопатки, 6 – испытуемые лопатки, 7 – крепление лопаток на подвижном столе вибростенда, 8 – тензорезисторы, 9, 11, 14 – переключатели, усилитель тензометрический, 12 – электронный осциллограф, 13 – магнитный регистратор колебаний, 15 – стойка белого шума
В отличии от схемы испытаний, представленной на рис.1, на подвижном вибростоле устанавливаются несколько лопаток, препарированных тензорезисторами. Собственные частоты одной формы колебаний одновременно устанавливаемых лопаток должны быть в пределах =f2 – f1. В этом диапазоне частот при помощи стойки белого шума, управляющей вибростендом, создаются колебания с равной спектральной плотностью мощности и поддерживаются автоматически. Стабильность режима колебаний обеспечивается с помощью вибродатчика обратной связи 4. Вибродатчик 4 размещен на подвижном столе вибростенда.
Полоса частот возбуждения, формируемая посредством набора частотных фильтров пропускания стойки белого шума контролируется дисплеем 3b.
Реальный спектр колебаний подвижного стола вибростенда оценивается вибродатчиком 4 обратной связи и представляется на дисплее 3a.
Колебания каждой лопатки регистрируются тензорезисторами 8 и бесконтактными датчиками 5. Сигналы тензорезисторов (данные о вибронапряжениях) усиливаются тензометрическим усилителем 10, наблюдаются на экране электронного осциллографа 12 и регистрируются на магнитном регистраторе 13.
Спектральная плотность стационарного случайного процесса (СПМ) каждой лопатки представляется на дисплее анализатора дополнительной стойки белого шума 15.
При установившемся режиме колебаний подвижного стола вибростенда соотношение величин СПМ в соседних стробах анализатора стойки белого шума 15 неизменно до начала разрушения.
Признаком разрушения считалось уменьшение собственной частоты колебаний лопатки на 5–7 герц, что соответствовало появлению трещины размером 0,3–0,5мм. Изменение собственной частоты колебаний лопатки при разрушении можно определить по изменению соотношений СПМ в стробах спектра колебаний. С понижением собственной частоты колебаний лопатки СПМ увеличивается на меньших частотах и уменьшались на в стробах, соответствующих более высоким частотам.
Усталостные испытания высоконагруженных узлов машин.
Примером испытаний на усталость при сложном напряженном состоянии может служить испытания замковых соединений лопаток (замковая часть лопатки в соединении с натурным элементом диска) компрессоров и турбин. Они проводятся с приложением как переменных нагрузок, так и постоянного растягивающего усилия. Схема действующей установки для подобных испытаний показана на рисунке 6.
Растягивающее усилие прикладывается к исследуемому замковому соединению с помощью силового троса (1) через рессору (2) и образец (3). Усилие растяжения устанавливается и контролируется специальным тарированным динамометром (4). Для исключения возможных перекосов на шейке (5) захвата размещены восемь тензорезисторов, регистрирующих статические деформации.
Исследования осуществляются на специальных образцах замковых частей лопаток и дисков, полностью имитирующих конструкцию соединения замок – диск.
Рисунок. 6. Схема действующей установки для испытаний замковых соединений лопаток в условиях нормальных и рабочих температур
Регулирование и выбор частоты испытаний может осуществляться различными способами.
Система «образец – рессора» под действием статической нагрузки представляет собой балку переменного сечения с жестко защемленными концами. Характер изменения изгибающих моментов по длине системы при колебаниях по основному тону соответствует распределению моментов в балке, жестко защемленной с двух концов. Это легко подтверждается экспериментально.
Рисунок.7. Распределение изгибающих моментов в балке, изгибающейся по основному тону колебаний и защемленной с двух концов. Пунктирным кружочком обозначена зона образца в колеблющейся системе «Образец – рессора».
Для корректного экстраполирования в место разрушения важно знать распределение изгибающих моментов по длине образца. Измерение величин изгибающих моментов можно производить при помощи тензорезисторов, прикрепленных в нескольких сечениях образца.
Расчет разрушающего момента, действующего на замковое соединение, производится экстраполированием данных, полученных в сечениях образца на замковое соединение:
М = М2 + а2/а1 (М2 + М1),
М2, М1 – изгибающие моменты в сечениях образца, причем сечение 2 ближе к исследуемому замковому соединению, а2,а1 – параметры, определяемые геометрическими размерами системы « образец–рессора».
В области обведенной пунктирным кружком на рисунке 7 распределение изгибающих моментов можно считать линейным.
Этот эксперимент может проводиться как при нормальной температуре, так и при рабочей температуре замковых соединений лопаток турбины. Для этого на исследуемое соединение размещается электрическая печь, отлаживается нужное температурное поле.
Выводы Для решения проблем повышения надежности, увеличения безопасности эксплуатации, повышения усталостной прочности, эксплуатационной долговечности, ресурса машин привлекаются различные способы возбуждения колебаний ответственных узлов или деталей с целью приближения условий эксперимента к реальной их переменной нагруженности. Повышение надежности машин осуществляется совершенствованием расчетно–экспериментальных методов оценок указанных характеристик.
Развитие приемов оценок сопротивляемости деталей переменным напряжениям (нагрузкам) уменьшением погрешности измерений при нагружении при испытаниях позволяет существенно снизить погрешность расчетов надежности машин.
