Модернизация автоклава для вулканизации резиновых изделий
Конференция: I Международная заочная научно-практическая конференция «Научный форум: технические и физико-математические науки»
Секция: Машиностроение и машиноведение
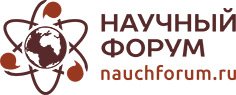
I Международная заочная научно-практическая конференция «Научный форум: технические и физико-математические науки»
Модернизация автоклава для вулканизации резиновых изделий
Modernization of rubber curing autoclave
Dmitri Kirgin
Сandidate of Technical Sciences, assistant professor in Irkutsk National Research Technical University, Russia, Irkutsk
AnastasiiaPogodaeva
Master’s degree student, Irkutsk National Research Technical University, Russia, Irkutsk
Аннотация. В статье рассматривается конструкция автоклава для вулканизации резиновых изделий АВТМ 2000-4000-12,5.Разобран принцип работы, выявлены недостатки. Предлагается конструкция альтернативного устройства, разработанная авторами статьи,позволяющая заменить источник тепла (паровой нагрев на электрический).
Abstract.The article deals with the design of rubber curing autoclave “АВТМ 2000-4000-12,5” (product of Kurgankhimmash LLC). The article gives a detailed description of principle of operation and analyzes imperfections. Authors of article developed an alternative device and offer it to use that allow to substitute the heat source (steam heating to electric).
Ключевые слова: автоклав; технологическое оборудование; автоматизация.
Keywords: autoclave; technological equipment; automation.
В резинотехнической отрасли промышленности процесс термообработки под давлением называется вулканизацией. Вулканизация –процесс, при котором пластичный («сырой») каучук превращается в резину. В результате вулканизации фиксируется форма изделия и оно приобретает необходимые свойства.Для реализации процесса вулканизации широко используются автоклавы [4]. Автоклав – это герметичный аппарат для ускоренного проведения физико-химических процессов при нагреве и повышенном давлении различных технологических изделий.
Конструкции и основные параметры промышленных автоклавов разнообразны, их ёмкость может составлять от нескольких десятков см³ до сотен м³, и предназначены они для работы под давлением до 150 МН/м² температуре до 500 °C.В автоклавах используются различные виды нагрева: паровой, с помощью горячей воды, индукционный, аэродинамический, электрический [1].
В данной работе предложен обзор автоклава АВТМ 2000-4000-12,5 (автоклав вулканизационный тупиковый без паровой рубашки механизированный горизонтальный с внутренним диаметром 2000 мм, длиной цилиндрической части 4000 мм, рабочим давлением 1,25 МПапредназначенного для вулканизации в паровой среде неформовых и других резинотехнических изделии с аналогичными режимами вулканизации. Данный автоклав послужил базой для научных исследований, проведенных в настоящей работе.
Эскизная схема автоклава представлена на рисунке 1. Автоклав состоит из следующих основных сборочных единиц: 1 - корпус; 2 - механизм поворота; 3 - байонетовый затвор; 4 - мостик подъемный; 5 - путь рельсовый; 6 - привод тележки; 7 - станция насосная; 8 - щит управления; 9 - пульт управления; 10 - тележка; 11 - цепь.
Рис. 1. Схема автоклава АВТМ 2000-4000-12,5
Процесс вулканизации (варки) подразумевает собой термообработку изделий паром при определенной температуре и давлении. Поэтому автоклав имеет сложную систему пневмовентилей предназначенных для поддержания постоянства этих двух величин. В эту систему входит шесть вентилей: вентиль подачи пара магистральный; вентиль подачи пара управления; вентиль сброса конденсата ДУ – 50 (диаметр трубы 50мм); вентиль сброса конденсата ДУ – 25; вентиль связи с атмосферой;вентиль подачи сжатого воздуха в автоклав.
Управление вентилями осуществляется сжатым воздухом из пневносистемы. Для того, что бы начать процесс вулканизации, оператору необходимо закрыть вентили связи с атмосферой и сброса конденсата, включить гидростанцию; установить тележку внутри автоклава; опустить мостик; закрыть крышку, кольцо; отключить гидростанцию. Затем закрыв вентили связи с атмосферой и сброса конденсата, включить подачу давления в уплотнение, убедится в наличии давления в уплотнительной прокладке, и только после этого приступить к первому этапу технологического процесса.
На этапе подготовки оператор должен периодически включать и выключать подачу пара в автоклав, следя затем, что бы температура и давление внутри сосуда вышли на заданные значения за промежуток времени. В обязанности оператора так же входит периодическое открытие и закрытие вентиля сброса конденсата, чтобы предотвратить накапливание конденсата на днище автоклава.
Охлаждение установки производится отключением вентиля подачи пара, открытием вентилей сброса конденсата и связи с атмосферой. В конце этого этапа оператор включает подачу воздуха внутрь автоклава.
После того как температура в автоклаве упадет до нужного уровня, выключается подача воздуха в автоклав. Как только давление внутри сосуда опустится до допустимой нормы, включается выдержка времени, по истечению которой, снимется блокировка на открытие кольца.
Вышеописанный способ регулирования параметров технологического процесса термообработки резиновых изделий морально устарел и требует модернизации управления с применением современных средств автоматизации. Паровой нагрев обеспечивает хорошую теплопередачу внутри автоклава, однако регулирование нагрева паром весьма энергозатратно, поскольку значительная часть тепла тратится на нагрев металлической части установки, а также уходит вместе с конденсатом при его сливе.
Авторами статьи предлагается альтернативный метод, позволяющий заменить источник тепла (паровой нагрев на электрический). В связи с этим, появляется возможность создать независимую систему регулирования температуры и давления.В качестве электрического источника тепла для нарастания температуры могут быть использованы теплоэлектронагреватели, а регулирование давления в емкости может осуществляться с помощью сжатого воздуха из пневмосистемы предприятия или от автономного компрессора[2].На данную разработку имеется патент РФ №122590.
Использование предлагаемого способа нагрева в камере для автоклавной тепловой обработки резиновых изделий под избыточным давлением позволит исключить ряд недостатков исследуемой установки и создать такую конструкцию емкости, которая обеспечит сокращение энергозатрат на термообработку деталей, при этом улучшит качество управления технологическим процессом производства резины вследствие независимого регулирования температуры и давления. Исключение парового нагрева, а соответственно и влажной среды внутри установки, позволит установить изоляцию с внутренней стороны автоклава. Такое расположение изоляции приведет к резкому сокращению расхода электроэнергии при разогреве рабочей камеры, а также исключит нагрев до рабочих температур стенок конструкции. Изоляционный материал (базальт) укладывается между стенками емкости и внутренней обшивкой, которая выполнена из листовой стали С20, толщиной 1-2 мм. Чтобы исключить воздействие нагрузок от избыточного давления на внутреннюю обшивку, в ней просверливаются сквозные отверстия диаметром 3 мм по всей поверхности в шахматном порядке с шагом 400мм.
Нагревательные элементы устанавливаются по внутренней стороне емкости. Места вывода ТЭНовгерметизируются.Для равномерного распределения тепла в камере устанавливается вентилятор, место ввода которого так же герметизируется сильфоновым уплотнением с двумя парами графитовых уплотнительных колец.
Регулирование нарастания давления осуществляется с помощью сжатого воздуха. Для возможности управления давлением в камере пневмоклапанзаменяется на задвижку с электроприводом, что, соответственно, способствует гибкости регулирования давления.
На рисунке 2 показана функциональная схема системы управления автоклавом при электрическом нагреве.
В данную схему автоклава входит: герметичный корпус 1; устройство подачи сжатого воздуха 2; система управления, состоящая из микроконтроллера 3, панели оператора 4, приборов ТЕРМОДАТ 5a и 5b, силовых твердотельных реле 6, датчика измерения температуры 7 и датчика измерения давления 8; теплоизолирующая оболочка 9, теплоэлектронагреватели 10, вентилятор 11, устройство сброса давления 12.
Теплоэлектронагревателиустанавливаются вдоль внутренней стороны герметичного корпуса между теплоизолирующей оболочкой и рабочим пространством автоклава. В торцевой части емкости устанавливается вентилятор, служащий для равномерного прогрева внутреннего объема сосуда.
Рис. 2 Функциональная схема системы управления автоклавом при электрическом нагреве
Теплоизолирующая оболочка устанавливается на внутренней стороне автоклава, что позволяет резко сократить расход электроэнергии при разогреве герметичного корпуса, так как ограничивает нагрев до рабочих температур его стенок [3].
Использование электронагревателей при осуществлении технологического процесса вулканизации обеспечит сокращение энергозатрат на термообработку деталей в 4,5 раза. При этом улучшит качество управления технологическим процессом производства резины вследствие возможности независимого регулирования температуры и давления.
Система автоматизированного управления автоклавом позволит осуществить:
- экономию энергоресурсов за счет точного соблюдения алгоритмов технологического режима;
- обеспечение качества технологического процесса за счет точного поддержания температуры и давления внутри автоклава;
- увеличение ресурса автоклава за счет соблюдения более точного технологического режима работы;
- реализацию автоматических защит и блокировок для обеспечения безопасности работы установки;
- снижение трудоёмкости обслуживания.
