ТЕКУЩЕЕ СОСТОЯНИЕ ИССЛЕДОВАНИЙ МОДЕЛИРОВАНИЯ РАСПРОСТРАНЕННЫХ ФОРМ КОРРОЗИИ САМОЛЕТОВ
Конференция: LXXXIII Международная научно-практическая конференция «Научный форум: технические и физико-математические науки»
Секция: Авиационная и ракетнокосмическая техника
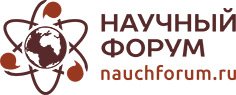
LXXXIII Международная научно-практическая конференция «Научный форум: технические и физико-математические науки»
ТЕКУЩЕЕ СОСТОЯНИЕ ИССЛЕДОВАНИЙ МОДЕЛИРОВАНИЯ РАСПРОСТРАНЕННЫХ ФОРМ КОРРОЗИИ САМОЛЕТОВ
CURRENT STATE OF RESEARCH INTO MODELLING COMMON FORMS OF AIRCRAFT CORROSION
Kuanysh Yerbolat
Master's student, Department of Aviation Engineering and Technology Academy of Civil Aviation, Kazakhstan, Almaty
Saliakyn Karipbayev
Supervisor, Ph.D. in Technical Sciences, Professor, Department of Aviation Engineering and Technology Academy of Civil Aviation, Kazakhstan, Almaty
Аннотация. В статье анализируются современные методы моделирования коррозии в авиаконструкциях. Рассмотрены ключевые подходы к компьютерному моделированию гальванической, щелевой и точечной коррозии с использованием современных вычислительных методов. Особое внимание уделено взаимосвязи между теоретическими моделями и их экспериментальной верификацией. Показаны перспективы развития данного научного направления для практического применения в авиационной промышленности. Результаты исследования могут быть использованы для повышения точности прогнозирования коррозионных повреждений и продления срока службы авиационных конструкций.
Abstract. The article analyzes modern methods for modeling corrosion in aircraft structures. It examines key approaches to computer simulation of galvanic, crevice, and pitting corrosion using advanced computational methods. Special attention is given to the relationship between theoretical models and their experimental verification. The prospects for developing this research field for practical applications in aviation industry are outlined. The study results can be used to improve corrosion damage prediction accuracy and extend service life of aircraft structures.
Ключевые слова: моделирование коррозии, конечный элемент, граничный элемент, динамический интерфейс
Keywords: corrosion modelling, finite element, boundary element, dynamic interface
Коррозионная стойкость самолета закладывается при проектировании, реализуется при производстве, поддерживается при техническом обслуживании и восстанавливается при капитальном ремонте.
Поэтому рассмотрение вопросов коррозии воздушных судов необходимо осуществлять системно на протяжении всего жизненного цикла самолета.
Проблемы в любом звене могут привести к «эффекту бочки» и напрямую повлиять на срок службы самолета.
В настоящее время проектирование защиты самолетов от коррозии в основном опирается на данные, накопленные существующими моделями, и опыт конструкторов, чтобы сначала спроектировать, а затем проверить его эффективность с помощью испытаний, что неэффективно и дорого для оценки. С непрерывным развитием компьютерных технологий и электрохимической теории коррозии непрерывное совершенствование привело к появлению технологии моделирования коррозии.
Эта технология основана на электрохимических принципах, путем тестирования поляризационных свойств материалов в различных условиях эксплуатации, использование конечных элементов или граничных элементов для прогнозирования коррозии структуры самолета коррозии место и степень коррозии в относительно короткий период времени, может значительно повысить самолет коррозии предотвращения проектных возможностей, обогатить методы оценки коррозии, в сочетании с соответствующей экспериментальной проверки модели, чтобы исправить, но также может быть непосредственно применен ко всему самолету прогнозирования коррозии, чтобы достичь всестороннего рассмотрения коррозии с системной точки зрения, а затем проверить свою эффективность путем тестирования, коррозии прогнозирования эффективности и высокой стоимости.
Он также может быть непосредственно применен к прогнозированию коррозии всего самолета, чтобы достичь цели всестороннего рассмотрения конструкции предотвращения коррозии самолета с системной точки зрения, тем самым устраняя ограничения оценки местных ключевых компонентов и достигая цели предсказуемой коррозии самолета.
Суть моделирования коррозии заключается в использовании математических методов для численного моделирования и расчета коррозионных повреждений.
По этой причине для моделирования коррозии были применены многие передовые математические методы, такие как нейронная сеть BP, машина опорных векторов [1] и т. д., и был достигнут определенный прогресс. Однако этот тип метода моделирования в основном использует состав металла, факторы окружающей среды, время и т. д. в качестве входных данных, а скорость коррозии, глубину коррозионных язв и т. д. в качестве выходных данных и подходит для одного металла. Более того, расчет модели часто требует большого количества инженерных данных в качестве поддержки, что требует чрезвычайно большого количества и качества данных. Обработка данных является объемной и трудоемкой задачей, поэтому имеет определенные ограничения при разработке.
С развитием электрохимической теории и компьютерных технологий методы моделирования методом конечных элементов или граничных элементов, основанные на электрохимических принципах, постоянно применяются для моделирования распространенных форм коррозии самолетов, таких как гальваническая коррозия, щелевая коррозия, точечная коррозия и т. д.
1 Гальваническая коррозия
Чтобы удовлетворить требования к легкости или прочности конструкции в процессе проектирования самолета, конструкторам часто приходится сочетать различные материалы, такие как муфты сталь-алюминий и алюминий-композит. Хотя такая форма соединения может позволить самолету удовлетворить требования к расчету прочности, поскольку разные материалы имеют разные электрохимические свойства, их соединение может легко вызвать гальваническую коррозию, что приведет к ускоренному ухудшению характеристик конструкции [2].
В этом случае более электрохимически активный материал (анод) будет корродировать с большей скоростью, поскольку материал с более высоким потенциалом (катод) подает катодный ток.
Такое ускоренное растворение металла, которое может быть локализованным или происходить в широких пределах, может существенно ухудшить механические свойства конструкции, что приведет к разрушению конструкции (разрушение, усталость и т. д.) или потере функции (протечки, перфорация).
Поэтому с точки зрения надежности проектирования и эксплуатации металлоконструкций крайне важно точно спрогнозировать зону возникновения гальванической коррозии и скорость коррозионной реакции.
1.1 Построение модели
С 1950-х годов Вабер и др. [3] начали проводить серию моделирования гальванической коррозии. Однако из-за незрелости компьютерных технологий в то время модели были относительно простыми. После вступления в XXI век, с быстрым развитием технологий обнаружения коррозии и постепенным усовершенствованием теории коррозии, моделирование коррозии стало постепенно признаваться учеными и стремительно развиваться. В частности, моделирование гальванической коррозии стало в той или иной степени применяться в сферах авиации, автомобилестроения, нефтехимии и т. д. В настоящее время исследования по моделированию гальванической коррозии можно условно разделить на два типа: моделирование атмосферной коррозии и моделирование иммерсионной коррозии, основанное на различных формах электролита на поверхности электродов:
- Построение модели атмосферной (тонкой пленки жидкости) гальванической коррозии.
Коррозия конструкций самолетов, обслуживающих прибрежные районы и острова, в основном вызвана атмосферной коррозией, которая по существу представляет собой электрохимическую коррозию под разной толщиной пленки жидкости [4]. Отличие от иммерсионной коррозии состоит в том, что различная форма пленки жидкости существенно повлияет на процесс массопереноса электродной реакции, что окажет большее влияние на коррозионное поведение металлов. По формам пленок жидкости при атмосферной коррозии в основном подразделяются на статически стабильные пленки жидкости, динамические пленки жидкости, пленки дисперсной жидкости и т. д. В настоящее время большинство исследований по имитационному моделированию атмосферной коррозии основано на статически стабильных пленках жидкости [5]. По сравнению с исследованиями в состоянии погружения, исследований по-прежнему недостаточно.
В основном это ограничивается тремя трудностями: во-первых, трудно проверить электрохимические свойства металлов под тонкими пленками жидкости, используя традиционные методы тестирования. Не только сложно настроить электрод сравнения и противоэлектрод в состоянии жидкой пленки, но и низкая надежность результатов измерений. Во-вторых, сложно построить геометрически сложные тонкие пленки жидкости. Принято считать, что толщина пленки жидкости менее 1 мм относится к категории атмосферной коррозии [6]. Во влажной атмосфере или влажной атмосфере толщина пленки жидкости обычно составляет менее 100 мкм.
Как добавить непрерывные и различной толщины исследовательские области электролита на поверхность сложных структур, является трудностью при моделировании методом конечных элементов или граничных элементов. В-третьих, трудно проверить или корректировать результаты моделирования. Чтобы проиллюстрировать точность результатов моделирования, часто необходимо разработать соответствующие эксперименты для проверки. Поскольку толщина тонких пленок жидкости обычно находится в микронном диапазоне, часто бывает трудно добиться стабильной пленки жидкости, соответствующей результатам моделирования в процессе испытаний.
На жидкую пленку в природной среде влияет изменчивая газовая фаза. Он будет испаряться и становиться тоньше в среде с низкой влажностью, а также загустеет из-за конденсации водяного пара в среде с высокой влажностью. Толщина жидкой пленки демонстрирует возвратно-поступательное динамическое изменение. Когда толщина пленки жидкости уменьшается, поверхностное натяжение увеличивается, в результате чего пленка жидкости отделяется и превращается в несколько небольших кусочков пленки жидкости, которые диспергируются. Утолщение пленки жидкости приведет к повторному агрегированию дисперсной пленки жидкости в целую пленку жидкости под действием силы тяжести, тем самым уменьшая дисперсию всей пленки жидкости. Изменение толщины и дисперсности динамических пленок жидкости приведет к изменению скорости коррозии металла под пленкой жидкости, причем изменения будут чрезвычайно большими, что также окажет существенное влияние на механизм коррозии пленки жидкости. Существует множество влияющих факторов, которые приводят к изменениям в поведении динамической коррозии пленки жидкости, и правила трудно измерить. Поэтому в настоящее время опубликовано очень мало результатов исследований по имитационному моделированию динамических пленок жидкости. Только Симиллион и др. [7] опубликовали соответствующие статьи в 2016 году, соответственно, в которых обсуждается влияние геометрии пленки жидкости и динамических изменений толщины пленки жидкости, вызванных испарением, на коррозию. Это также может дать новую исследовательскую идею для динамического моделирования атмосферной коррозии.
Чтобы проверить результаты прогнозирования модели атмосферной гальванической коррозии, многие исследователи провели лабораторные испытания на коррозию или полевые испытания на испытательных образцах и сравнили результаты коррозии с результатами прогнозирования модели.
- Построение модели гальванической коррозии в состоянии погружения.
Конструкция самолета сложна, и в некоторых местах из-за неправильной конструкции может быть плохой дренаж. Местное скопление воды из-за дождя, снегопада, чистки самолета и других факторов может легко вызвать коррозию при погружении в раствор.
По сравнению с атмосферной коррозией ранее было исследовано моделирование гальванической коррозии в состоянии погружения. Это связано с тем, что условия коррозионных испытаний в состоянии погружения легко контролировать, основные данные для моделирования легко получить, а результаты испытаний легко проверяемы. С 1950-х годов по настоящее время модель гальванической коррозии под погружением претерпела процесс постоянного совершенствования и обогащения от простоты к сложности и постепенно получила признание. Особенно за последнее десятилетие работа по моделированию гальванической коррозии достигла беспрецедентного развития. В настоящее время модели гальванической коррозии можно условно разделить на пять категорий.
Категория 1: Модель гальванической коррозии, которая определяет распределение потенциала и плотности тока на основе потенциального уравнения Лапласа и закона Ома, а затем рассчитывает глубину коррозии на основе закона Фарадея [8]. Этот тип модели предполагает, что концентрация частиц на поверхности электрода такая же, как концентрация тела раствора. Концентрация ионов в растворе не влияет на проводимость раствора электролита. То есть проводимость считается фиксированной величиной. Обычно он подходит для крупных деталей конструкции без длинных и узких зазоров.
Категория 2: Модель, которая определяет потенциал, плотность тока и распределение концентрации частиц на основе предположений о сохранении вещества и электронейтральности, а затем рассчитывает глубину коррозии на основе закона Фарадея [9]. Этот тип модели обычно делится на два типа: один предназначен для фиксации проводимости и расчета распределения концентрации, а другой — для расчета распределения концентрации на основе предположения об электронейтральности. Этот тип модели обычно подходит для ситуаций, когда в конструкции имеется длинный и узкий зазор, а внутри и снаружи зазора возникает разница концентраций, которая влияет на реакцию коррозии.
Категория 3: Модель гальванической коррозии с учетом эффекта стерических препятствий продуктов коррозии [10]. Этот тип модели является усовершенствованием модели второго типа с учетом тормозящего влияния осаждения продуктов на коррозию.
Категория 4: Модель гальванической коррозии, учитывающая влияние динамических изменений интерфейса на коррозию [11]. Этот тип модели учитывает влияние на коррозию, вызванное изменением соотношения площадей катода и анода, вызванным движением коррозионной границы раздела, и является детальным дополнением к первым трем типам моделей. В настоящее время в области моделирования коррозии отслеживание динамического интерфейса по-прежнему остается актуальной исследовательской проблемой.
Категория 5: Модель гальванической коррозии на основе случайно распределенных катодов и анодов. Этот тип модели появился относительно поздно. В настоящее время в основном вводятся случайные функции для случайного размещения катодов и анодов в разное время на одном и том же интерфейсе. Затем на основе модели первого типа рассчитывается изменение коррозионной границы раздела во времени.
1.2 Применение передовых методов обнаружения для определения
В настоящее время наиболее распространёнными устройствами для проверки точности моделей гальванической коррозии являются сканирующий Кельвин-зонд (Scanning Kelvin Probe, SKP), сканирующий вибрирующий электрод (Scanning Vibration Electrode Technology, SVET), массивы электродов [12], а также оборудование для анализа продуктов коррозии (рентгеновская дифракция (X-Ray Diffraction, XRD), энергодисперсионный спектрометр (Energy Dispersive Spectrometer, EDS)).
Сканирующий Кельвин-зонд — это бесконтактная, неразрушающая технология измерения потенциала поверхности металла в газовой среде, основанная на принципе колебательной ёмкости. Она в основном используется для сравнения распределения потенциалов, полученных в результате моделирования и экспериментальных измерений.
Сканирующий вибрирующий электрод использует вибрирующий электрод и фазовый детектор для линейного или поверхностного сканирования плотности тока на образце. Этот метод применяется для проверки соответствия между смоделированной и фактической плотностью тока. Например, Дешпанде использовал SVET для сканирования поверхности магний-сталь и магний-алюминий-сталь с шагом 0,5 мм × 0,5 мм и провёл сравнительный анализ с результатами моделирования, как показано на рисунке 1.
Рисунок 1. Сравнение гальванической коррозии магния и стали SVET и моделирования
1.3 Применение моделирования гальванической коррозии
С непрерывным прогрессом в материаловедении и улучшением характеристик новых материалов, высокопроизводительные материалы всё чаще используются в проектировании самолётов. Многокомпонентные металлические соединения стали обычным явлением, особенно для крепёжных элементов. При выборе материалов для удовлетворения требований прочности и лёгкости часто трудно учесть факторы коррозии, что создаёт значительные проблемы для технического обслуживания и ремонта самолётов во время эксплуатации. Коррозия конструкций самолётов в основном возникает в местах соединения металлов и вокруг крепёжных элементов, где из-за контакта разнородных металлов легко развивается гальваническая коррозия.
Моделирование гальванической коррозии, разрабатываемое и совершенствуемое более полувека, в настоящее время достигло относительно высокой зрелости в прогнозировании мест коррозии, её зон и даже глубины повреждений. Результаты исследований успешно применяются в авиационной отрасли многих развитых стран, включая США и Европу, и публикуются в виде монографий, научных статей и докладов на конференциях.
Одним из наиболее подробных описаний применения моделирования коррозии в авиации является монография Дерозе [13] из Швейцарского федерального института материаловедения и технологий (2013 г.) под названием «Коррозия алюминиевых сплавов в конструкциях самолётов: моделирование и симуляция». В ней систематически представлены макро-, микро- и мезоскопические методы моделирования коррозии в алюминиевых сплавах авиационных конструкций, что свидетельствует о начале активного использования этого подхода в Европе. В том же году доктор Палани [14] провёл серию исследований с использованием программного обеспечения Beasy для моделирования коррозии в соединениях углепластика и алюминиевого сплава 2024 в атмосферных условиях и при погружении в растворы.
Снихирова и соавт. расширили область применения моделей коррозии, использовав их для прогнозирования гальванической коррозии в соединениях Ti6Al4V-AA2024 в авиационных конструкциях. Их модель учитывает влияние продуктов коррозии на перенос частиц и изменение локального уровня pH, а также подчёркивает важность самопроизвольной коррозии сплава AA2024 в гальванических парах. Для проверки точности результатов Снихирова и коллеги применили передовые методы измерений, включая дифференциальную визуализацию и SVET, чтобы собрать данные и верифицировать разработанную модель.
2 Щелевая коррозия
В авиационных конструкциях присутствует множество металлических соединений, таких как стыки листовых материалов и области крепления элементов, где щелевая коррозия практически неизбежна. Моделирование щелевой коррозии существенно сложнее моделирования гальванической коррозии, поскольку геометрия зазора ограничивает транспорт частиц (например, кислорода), создавая разность концентраций между внутренней и внешней частью щели и тем самым ускоряя коррозионные процессы. Дополнительными критически важными факторами, влияющими на точность прогнозирования, являются геометрические деформации щели и накопление продуктов коррозии в её устьевой части.
Пионерские работы по математическому моделированию физики щелевой коррозии были выполнены Шарландом и Таскером [15], а также Уолтоном ещё в 1980-х годах. В 1990-х годах Шарланд значительно расширил эти исследования, разработав прогностическую модель эволюции ионной концентрации и электрического потенциала в металлических зазорах. Эта модель, основанная на физико-химических механизмах локальной активации при разрушении пассивной плёнки, учитывает процессы ионной миграции и химические реакции. Валидация модели на экспериментальных данных из различных источников показала её способность качественно воспроизводить коррозионные процессы, а в ряде случаев - и количественно их описывать. Однако предположение о разбавленности растворов привело к существенным погрешностям при моделировании коррозии в концентрированных электролитах.
До начала XXI века, в силу ограниченного понимания механизмов щелевой коррозии, исследования преимущественно фокусировались на процессах массопереноса в зазорах, рассматривая лишь действие концентрационных элементов, обусловленных градиентами ионов металлов и кислорода. В этот период отсутствовали модели, учитывающие совместное влияние эффекта автоокисления (окклюзионного автокатализа) и кислородных концентрационных элементов. Кроме того, ограниченные вычислительные возможности того времени не позволяли адекватно моделировать динамику изменения границ раздела фаз, вызванную процессами активного растворения и осаждения продуктов коррозии.
Начиная с 2010 года, исследования в области моделирования щелевой коррозии получили стремительное развитие как в отечественной, так и в зарубежной науке. В этот период в практику моделирования были внедрены современные математические подходы, в частности методы отслеживания подвижных границ раздела, такие как level-set и фазовое поле.
Значительный вклад в эту область внесли следующие работы:
- В исследовании была предложена произвольная лагранжево-эйлерова модель для имитации динамического процесса развития щелевой коррозии во временной области. Данная модель позволяет рассчитывать распределение потенциала и концентрации частиц в зазоре, а также отслеживать геометрические изменения границы раздела, вызванные активным растворением и осаждением продуктов коррозии.
- В работе разработан численный метод моделирования электрохимических условий в щелях и питтингах, вызванных гальванической коррозией в водной среде. Метод основан на расширенном методе конечных элементов (XFEM) для дискретизации безразмерных управляющих уравнений, с использованием функции level-set для описания морфологии границы раздела независимо от базовой конечно-элементной сетки.
- Исследование продемонстрировало применение фазового поля для моделирования щелевой коррозии железа в морской воде. Модель учитывает шесть типов ионов и соответствующие химические реакции, позволяя рассчитывать временные распределения ионных концентраций и потенциала в электролите, а также распределения таких параметров, как перенапряжение, pH и скорость коррозии при различных потенциалах металла.
3 Точечная коррозия
Точечную коррозию можно разделить на открытую питтинговую коррозию (рис. 2(а)) и закрытую питтинговую коррозию (рис. 2(б)) в зависимости от формы очага коррозии. Среди них раствор электролита в очаге открытой коррозии легко вытекает наружу, а внутренняя поверхность очага коррозии снова пассивируется, что останавливает расширение очага коррозии. Однако при коррозии с закрытыми очагами Cl- будет проникать извне в очаг коррозии, концентрироваться и гидролизоваться, вызывая постоянное снижение pH раствора электролита в очаге коррозии, тем самым ускоряя непрерывное расширение очага коррозии [2].
а) б)
Рисунок 2. Типы точечной коррозии
Алюминиевые сплавы, используемые в обшивке самолетов, и нержавеющие стали, применяемые для крепежных элементов, относятся к материалам, склонным к точечной коррозии. Точечная коррозия имеет много общего с щелевой коррозией - механизмы их развития на стадии распространения практически идентичны. Поэтому в некоторых публикациях точечную коррозию рассматривают как особый вид щелевой коррозии, отличающийся лишь более коротким каналом диффузии.
Процесс точечной коррозии обычно включает две стадии: зарождение (инициацию) и развитие. Некоторые исследования дополнительно подразделяют его на три этапа: образование зародышей, метастабильное состояние и стабильное развитие, однако принципиальных различий между этими классификациями нет.
Очаги точечной коррозии могут зарождаться как на гладкой пассивной поверхности металла, так и (что происходит чаще) в местах химической неоднородности или физических дефектов на поверхности металла или сплава. В настоящее время среди исследователей коррозии общепринятым является представление о механизме развития точечной коррозии, связанном с эффектом автокатализа внутри коррозионной полости или действием замкнутого коррозионного элемента, что принципиально совпадает с механизмом развития щелевой коррозии.
3.1 Моделирование зарождения точечной коррозии (образования зародышей)
Современные подходы к моделированию зарождения точечной коррозии в основном основаны на учете локальной электрохимической неоднородности. Рассмотрим в качестве примера алюминиевые сплавы. Их микроструктура чрезвычайно сложна и содержит множество интерметаллидных включений (Intermetallic Particles, IMPs), которые образуются в результате термической обработки специально добавленных легирующих элементов для улучшения механических свойств.
Многие IMPs являются "многофазными" и демонстрируют выраженную микроскопическую неоднородность. Включения с катодными свойствами (содержащие Fe, Cu) и анодные включения (содержащие Mg) по-разному ведут себя в электрохимическом отношении.
При контакте с матрицей Al они образуют микрогальванические пары, вызывая либо активное растворение матрицы, либо собственную коррозию.
Моделирование зарождения точечной коррозии на основе таких микрогальванических пар появилось сравнительно недавно.
Это связано главным образом с тем, что размеры большинства IMPs составляют микронный масштаб, что затрудняет измерение их электрохимических характеристик.
Только в начале XXI века появились соответствующие технологии микроэлектродных измерений [16] (рис. 3).
На их основе были проведены исследования электрохимических свойств интерметаллидных фаз в алюминиевых и магниевых сплавах, что заложило основу для моделирования зарождения точечной коррозии.
В 2011 году Дешпанде предложил метод level-set для различения микроанодных и микрокатодных зон на одной поверхности, проанализировав коррозионное поведение β-фазы вокруг α-фазы как в непрерывном, так и в дискретном вариантах. Это создало необходимые предпосылки для дальнейшего развития моделей зарождения точечной коррозии. Последующие исследования также внесли вклад в эту область.
Рисунок 3. Микроэлектродное электрохимическое измерительное устройство
3.2 Моделирование развития точечной коррозии (метастабильное и стабильное развитие)
В настоящее время моделирование развития точечной коррозии обычно предполагает, что пассивная пленка уже имеет дефекты, то есть не учитывает стадию зарождения, а сразу переходит к моделированию развития точечной коррозии.
Такие модели направлены на описание процесса развития отдельной коррозионной ямки и обычно основаны на законах переноса и электрохимической кинетики для расчета геометрической эволюции коррозионной ямки и распределения ионных концентраций во всей ямке, что имеет значительное сходство с моделированием щелевой коррозии.
Поскольку такое моделирование не требует измерений микроэлектрохимических характеристик, оно появилось относительно рано. Еще в 1980-х годах Шарланд и Таскер разработали его теоретическую модель.
В XXI веке различные передовые методы, такие как метод конечных объемов, клеточные автоматы, метод фазового поля, перидинамика и другие, были применены в имитационном моделировании, что значительно расширило методический арсенал.
Кроме того, различные формы повреждения пассивной пленки и различная ориентация зерен (рис. 4) также оказывают значительное влияние на развитие точечной коррозии.
Рисунок 4. Имитационное моделирование различных ориентаций зерен
Проведенный анализ современных подходов к моделированию коррозионных процессов в авиационных конструкциях позволяет сделать ряд важных выводов. Развитие вычислительных методов и экспериментальных технологий привело к значительному прогрессу в понимании механизмов гальванической, щелевой и точечной коррозии.
Современные модели коррозионных процессов достигли высокой степени детализации, позволяя учитывать как макроскопические электрохимические процессы, так и микроструктурные особенности материалов.
Особенно следует отметить успехи в моделировании точечной коррозии, где удалось раздельно описать процессы зарождения и развития повреждений, а также установить ключевую роль микронеоднородностей материала.
Применение передовых численных методов, таких как метод фазового поля, клеточные автоматы и перидинамика, открыло новые возможности для более точного прогнозирования коррозионных повреждений.
Эти методы позволяют учитывать сложные физико-химические взаимодействия и моделировать эволюцию повреждений в реальном масштабе времени.
Особую ценность представляют разработанные подходы к экспериментальной верификации моделей с использованием современных измерительных технологий.
Это обеспечивает необходимую достоверность прогностических расчетов и возможность их практического применения.
Дальнейшее развитие исследований в этом направлении должно быть сосредоточено на создании комплексных мультидисциплинарных моделей, объединяющих различные виды коррозии и учитывающих реальные условия эксплуатации авиационных конструкций. Решение этих задач будет способствовать повышению надежности и безопасности авиационной техники.
