Формирование композиционного поверхностного слоя изделий из серого чугуна лазерным легированием силицидами
Конференция: XLII Международная научно-практическая конференция «Научный форум: технические и физико-математические науки»
Секция: Машиностроение и машиноведение
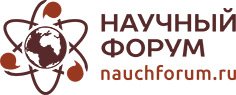
XLII Международная научно-практическая конференция «Научный форум: технические и физико-математические науки»
Формирование композиционного поверхностного слоя изделий из серого чугуна лазерным легированием силицидами
FORMATION OF A COMPOSITE SURFACE LAYER OF GRAY CAST IRON PRODUCTS BY LASER ALLOYING WITH SILICIDES
Oleg Devoino
Doctor of Technical Sciences, Professor, Head of the Industrial Research Laboratory "Plasma and Laser Technologies", Republic of Belarus, Minsk
Margarita Kargapolova
Candidate of Technical Sciences, Associate Professor leading researcher of scientific-research laboratory "Plasma and laser technologies", Republic of Belarus, Minsk
Irina Kosyakova
Junior Researcher of the branch research Laboratory "Plasma and Laser Technologies", Republic of Belarus, Minsk
Аннотация. В статье представлены результаты исследования микроструктуры серого чугуна СЧ20 после лазерного легирования силицидами. В результате корреляционного анализа установлена сильная связь между глубиной упрочненной зоны и скоростью обработки вида у=1-0,006Х. На ширину оплавленной зоны серого чугуна параметры лазерной обработки влияния не оказывают. Лазерная закалка позволяет уменьшить скорость изнашивания приблизительно в 2 раза, а лазерное легирование уменьшает скорость изнашивания приблизительно в 10-15 раз.
Abstract. The article presents the results of a study of the microstructure of gray cast iron SCH20 after laser alloying with silicides. As a result of the correlation analysis, a strong relationship was established between the depth of the hardened zone and the processing speed of the type y=1-0,006X. The width of the melted zone of gray cast iron is not affected by the laser processing parameters. Laser quenching reduces the wear rate by about 2 times, and laser alloying reduces the wear rate by about 10-15 times.
Ключевые слова: серый чугун; лазерное легирование; силициды; скорость изнашивания.
Keywords: grey cast iron; laser alloying; silicides; wear rate.
Важнейшим продуктом черной металлургии в мире наряду со сталью и железом остается чугун. Свое широкое применение в качестве конструкционного материала в машиностроении чугун получил благодаря своим свойствам и массовому применению при изготовлении деталей для машин, станков и оборудования.
Улучшить поверхностный слой чугунных изделий, повысить комплекс физико-механических и эксплуатационных характеристик возможно с использованием лазерного излучения. Преимущества лазерного излучения для обработки чугунных изделий: локальность обработки; небольшие остаточные напряжения, исключающие коробление деталей; возможность воздействия на труднодоступные места; отсутствие непосредственного механического контакта детали с элементами лазерной установки, что дает возможность управления всеми параметрами процесса с помощью компьютера; возможность упрочнения крупногабаритных и длинномерных деталей [1]. Т.к. обмазка для лазерного легирования составляет не более 0,15 мм, появляется возможность использовать дорогостоящие компоненты, которые не удорожают общую стоимость упрочнения.
В литературе известно повышение прочностных и эксплуатационных свойств чугунных изделий после легирования хромом, никелем, молибденом, кремнием, ванадием, титаном и медью.
Наиболее важным в практическом отношении легирующим элементом, по опубликованным данным [2], является кремний, который вместе с углеродом оказывает наибольшее влияние на структуру и свойства чугуна. [3]. Оценивая влияние легирующих элементов на чугун в процессе литья, в первую очередь, кремния, на кристаллизацию матрицы чугуна, следует учитывать не только среднее содержание его в металле, но также характер и степень микроликвации, образуемой в процессе кристаллизации. Вследствие неравномерного распределения элементов, в том числе кремния, процессы кристаллизации происходят неодновременно по всему объему и развиваются в разной степени, что приводит часто к образованию различных структур в соседних микрообъемах [4].
Кремний, как легирующий элемент обеспечивает образование на поверхности чугуна оксидов железа, а также собственных оксидов, защищая ее от коррозии. Чугуны, легированные кремнием, имеют повышенную жаростойкость [5].
Методика исследований. Для упрочняющей обработки использовалась установка лазерной закалки MLS-2-3DF. Данная установка позволяет производить обработку широкого спектра материалов, в том числе и посредством сканирования излучения по упрочняемой поверхности.
Исследование проводили на образцах 60х20х7 мм из чугуна СЧ20. После нанесения покрытий клеевым методом, наносили слой легирующих элементов и проводили лазерную обработку поверхности. Затем образцы разрезали поперек лазерных дорожек для исключения влияния нестабильности температурных условий нагрева и охлаждения на краях образца. Поперечные шлифы изготавливали по общепринятой методике (после заливки образцов в специальную пластмассу, предохраняющую края от заваливания). Поверхность покрытия и поперечные шлифы доводили механическим полированием в водном растворе окиси алюминия. Для выявления микроструктуры, образцы травили в 5-% растворе азотной кислоты в спирте.
Протравленные образцы были изучены на микроскопе «Micro-200» при увеличении от Х50 до Х1000.
Испытания на микротвердость приводили на приборе ПМТ-3 путем вдавливания в испытуемый образец четырехгранной алмазной пирамиды с углом при вершине 136° при нагрузке 100Г (0.98Н) (ГОСТ 9450-76).
Для оценки влияния лазерной обработки на изменения свойств поверхностного слоя рассматривалось совместное влияние диаметра лазерного пучка и скорости оплавления, причем использовался дробный факторный план типа 22. Матрица планирования приведена в табл. 1.
Таблица 1.
Кодовые значения и величины переменных, используемые в исследованиях
Номер эксперимента |
X1 |
X2 |
||
Код |
Значение, мм |
Код |
Значение, мм/мин |
|
1 |
-1 |
1 |
-1 |
100 |
2 |
+1 |
2 |
-1 |
100 |
3 |
- |
1 |
+1 |
600 |
4 |
+1 |
1 |
+1 |
600 |
Исходная структура необработанного образца из чугуна СЧ20 имеет феррито-перлитную структуру, форма графита – пластинчатая, расположение графита – розеточное (рис. 1).
Рисунок 1. Исходная структура серого чугуна СЧ20
Основным фактором, влияющим на формирование обработанного лазерным излучением слоя, являются высокая скорость нагрева поверхностного слоя (105–107 К/сек), обусловленная большой плотностью энергии и скоростью охлаждения, достигаемыми за счет теплоотвода в массу основы. Высокие скорости нагрева приводят к значительному сдвигу точек фазовых превращений, имеющих диффузионную природу. Большие скорости охлаждения расплавленной лазерным излучением зоны приводит к неполному протеканию диффузионных процессов, образованию большого числа зародышей различных фаз и формированию, поэтому мелкозернистой и неравновесной структуры [6,7].
Рисунок 2. Микроструктура чугуна СЧ20 после обработки оптоволоконным лазером Р=1 кВт, легирующий компонент SiС, скорости обработки 1000 мм/мин, x50
Сказанное выше относится и к формированию структуры оплавленных лазерным излучением покрытий на чугунных деталях. На рисунке 2 представлена зона оплавления чугуна, полученная в результате лазерной обработки образцов из чугуна СЧ-20.
При лазерном легировании зона лазерного воздействия состоит из зоны оплавления (закалки из жидкой фазы) и закалки из твердой фазы. Зона термического влияния состоит лишь из закалки из твердой фазы. В зоне оплавления при легировании SiС отсутствуют графитные включения, а структура представляет собой мелкодисперсные дендриты, состоящие из ветвей первого и второго порядка.
В таблице 2 представлены размерные параметры зон оплавления в зависимости от скорости обработки чугуна СЧ20, легированного SiC.
Таблица 2.
Размерные параметры зоны оплавления и зоны термического влияния в зависимости от скорости обработки чугуна СЧ-20 при N 1 кВт и d 4 мм, легирующий компонент SiC
Размерные параметры |
Скорость движения детали относительно луча лазера, мм/мин |
|||||||
400 |
500 |
600 |
700 |
800 |
900 |
1000 |
1100 |
|
L, мм |
4,1 |
4,3 |
4,1 |
4,2 |
4,2 |
4,1 |
4,1 |
4,2 |
H, мм |
0,8 |
0,73 |
0,64 |
0,54 |
0,53 |
0,50 |
0,41 |
0,4 |
На рисунке 3 показано влияние скорости обработки лазерного луча на глубину зоны проплава серого чугуна СЧ20 при N=1 кВт и d=4 мм, в качестве легирующих компонентов выступил SiC.
Рисунок 3. Влияние скорости обработки лазерного луча на глубину зоны проплава серого чугуна СЧ20 при N=1 кВт и d=4 мм, легирующий компонент SiC
При легировании SiC и при ширине луча лазера 4 мм и мощности 1 кВт L меняется от 0,8 до 0,4 мм и хорошо коррелирует со скоростью обработки (коэффициент корреляции 0,97).
На ширину оплавленной зоны L (рисунок 2) серого чугуна параметры лазерной обработки влияния не оказывают. Ширина лазерной дорожки варьируется от 4 до 4,7 мм.
На рисунке 4 представлена гистограмма скорости изнашивания серого чугуна СЧ20, серого чугуна после лазерной закалки ЛЗ и после лазерного легирования ЛЛ.
Рисунок 4. Гистограмма скорости изнашивания серого чугуна СЧ20 в состоянии поставки, серого чугуна после лазерной закалки ЛЗ и после лазерного легирования ЛЛ SiC
Как видно из рисунка 4, максимальная скорость изнашивания наблюдается у необработанного чугуна (0,3 мм3/км), лазерная закалка позволяет уменьшить скорость изнашивания приблизительно в 2 раза (до 0,15 мм3/км), а лазерное легирование уменьшает скорость изнашивания приблизительно в 10-15 раз (до 0,014-0,024 мм3/км).
Таким образом, для лазерного легирования деталей из серого чугуна выбраны легирующие компоненты, увеличивающие количество упрочняющей фазы и легирующие матрицу – SiC. В результате корреляционного анализа установлена сильная связь между глубиной упрочненной зоны и скоростью обработки вида у=1-0,006Х. На ширину оплавленной зоны серого чугуна параметры лазерной обработки влияния не оказывают. Ширина лазерной дорожки варьируется от 4 до 4,7 мм. Лазерная закалка позволяет уменьшить скорость изнашивания приблизительно в 2 раза (до 0,15 мм3/км), а лазерное легирование уменьшает скорость изнашивания приблизительно в 10-15 раз (до 0,014-0,024 мм3/км).
