Организация подготовки производства на «КАЗ им. С.П. Горбунова» с применением PLM – системы
Конференция: XXI Международная научно-практическая конференция «Научный форум: технические и физико-математические науки»
Секция: Информатика, вычислительная техника и управление
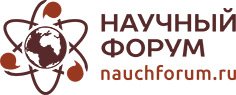
XXI Международная научно-практическая конференция «Научный форум: технические и физико-математические науки»
Организация подготовки производства на «КАЗ им. С.П. Горбунова» с применением PLM – системы
В статье рассматривается проблема обеспечения интеграции и совместного использования информации, выпускаемой на всех этапах жизненного цикла изделия (ЖЦИ), в рамках внедрения PLM-системы на «КАЗ им. С.П. Горбунова». Применение PLM-системы позволяет обеспечить рост конкурентоспособности выпускаемой продукции и эффективности производства: повысить качество выпускаемой продукции, сократить сроки подготовки производства.
Для предприятий, имеющих наукоемкое серийное производство и длительный цикл разработки изделий, производства и эксплуатации наиболее актуальна проблема обеспечения интеграции и совместного использования информации, выпускаемой на всех этапах ЖЦИ.
«Казанский авиационный завод имени С.П. Горбунова» филиал ПАО «Туполев» («КАЗ им. С.П. Горбунова») было основан в 1932 году в городе Казань и является одним из крупнейших предприятий авиационной промышленности России. Основное направление деятельности «КАЗ им. С.П. Горбунова» - серийное производство военных и гражданских самолетов, а также товаров народного потребления. Выпуск такой продукции в современных условиях немыслим без широкого использования информационных технологий на всех этапах ЖЦИ. Обеспечение конкурентоспособности «КАЗ им. С.П. Горбунова» связано с быстрым освоением и выпуском новых изделий, удовлетворяющих требованиям заказчиков. Сократить время вывода на рынок нового изделия и, тем самым, повышение эффективности своей деятельности, производственным предприятиям позволяет применение технологии управления жизненным циклом продукции (изделия) и информационной системы в качестве инструмента реализации технологии. Для управления жизненным циклом продукта используются PLM-системы (англ. product lifecycle management). «КАЗ им. С.П. Горбунова» для управления жизненным циклом продукции использует – пакет масштабируемых программных решений для поддержки жизненного цикла изделий, созданный на основе открытой платформы PLM Teamcenter [1, 2]. Применение PLM-системы является стратегическим направлением «КАЗ им. С.П. Горбунова», следуя которым обеспечивается рост конкурентоспособности выпускаемой продукции и эффективности производства.
«КАЗ им. С.П. Горбунова» осуществляет разработку и сопровождение конструкторских составов изделия на базе PLM-системы Teamcenter. Для проектирования электронной модели изделия (ЭМИ) используется интегрированная с Teamcenter система автоматизированного проектирования NX. На рис. 1 приведен пример организации хранения данных о детали в Teamcenter.
Рисунок 1. Архитектура хранения данных о детали в Teamcenter
ЭМИ разрабатываются с применением концепции «мастер-модель» (рис. 2), суть которой состоит в том, что любая ЭМИ созданная однажды используется в качестве исходных данных, исходная ЭМИ при этом не меняется, а используется ее ассоциативная копия. Применение концепции «мастер-модель» позволяет распараллелить работу конструкторов основного производства, конструкторов газодинамических расчетов, конструкторов оснастки, конструкторов-металлургов, программистов ЧПУ.
Рисунок 2. Концепция «мастер-модель»
Проектирование систем обвязки ГТД происходит в системе NX без выпуска бумажных чертежей, при этом сборка ГТД осуществляется с применением электронного макета на базе технологии интерактивных сборочных инструкций, что в свою очередь позволяет:
- Выявить ошибки на этапе проектирования;
- Отработать систему обвязки до изготовления и сборки;
- Повысить качество сборочной операции;
- Сократить затраты на изготовление и содержание макета изделия;
- Сократить использование человеческого труда.
«КАЗ им. С.П. Горбунова» разработан на базе Teamcenter единый классификатор, содержащий актуальную нормативно-справочную информацию, что позволяет сократить сроки проектирования и ошибки за счет использования неактуальной информации.
Разработка управляющих программ измерения и обработки производится с применением симуляции. «КАЗ им. С.П. Горбунова» выделяет следующие положительные эффекты от симуляции измерения и обработки:
- Визуализация движений станка и процесса измерения;
- Отладка и оптимизация программы измерения;
- Снижение времени контроля детали;
- Проверка траектории измерения на столкновение с деталью и оснасткой;
- Сохранение дорогостоящего оборудования (измерительной головки);
- Сокращение времени простоя оборудования;
- Сокращение времени на отладку управляющих программ на оборудовании (т. к. большую часть этого вспомогательного времени программист тратит на отладку управляющих программ на симуляторе CSE в программном обеспечении NX CAM вместо станка);
- Снижение вероятности аварийных ситуаций на оборудовании (т. к. управляющая программа поступает на станок уже в протестированном на симуляторе CSE виде);
- Возможность тестирования сторонних управляющих программ (например, написанных вручную) на симуляторе CSE.
При симуляции обработки в NX CAM удалось сократить общее время получения первой годной детали за счет исключения затрат времени на исправление недочетов в управляющей программе и во время проведения наладки станка с ЧПУ.
Для проектирования оснастки применяется технология «бесчертежного проектирования». Пример применения технологии представлен на рис. 3. Вся информация необходимая, для изготовления ДСЕ хранится в ЭМИ, при этом весь процесс инжиниринга выполняется без использования чертежей. В процессах изготовления используются данные из 3D-модели. Для этого, рабочие места оборудуются компьютерной техникой (планшетные компьютеры, ноутбуки, рабочие станции). Чертежи, при необходимости формируются на последнем этапе разработки, когда конструкция изделия полностью утверждена или даже прошла необходимые испытания.
Рисунок 3. «Бесчертежная технология» проектирования
Преимущества «Бесчертежной технологии»:
- Сокращение времени на проверку документации;
- Сокращение времени на разработку УП для ЧПУ и КИМ;
- Сокращение времени за счет отсутствия необходимости оформления чертежа (по сравнению с оформлением и чертежа и модели);
- Исключение вероятности проведения изменений только в чертеже (без изменения модели);
- В модели меньше вероятности сделать ошибку и легче ее отследить и исправить, в итоге ошибок производства будет меньше, а ошибки на этапе производства самые дорогие.
Технологическая подготовка производства «КАЗ им. С.П. Горбунова» осуществляется на базе Teamcenter Manufacturing – набор компонентов, являющийся неотъемлемой частью PLM-системы Teamcenter, обеспечивающий поддержку инженерных процессов, связанных с технологической подготовкой производства [3]. Разработка межцеховых маршрутов, операционных технологических процессов (ТП), операционных маршрутов, переходов, назначение оборудования и средств технологического оснащения, расчет режимов обработки, разработка операционных эскизов, расчет трудовых норм, управление данными числового программного управления (ЧПУ) и координатно-измерительных машин (КИМ), построение циклорам обработки. Работа в единой информационной среде обеспечивает сквозной процесс управления составом от конструкторского к технологическому, с последующим формированием эксплуатационного состава. На рис. 4 представлена общая архитектура хранения данных конструкторского, технологического и эксплуатационного состава.
Рисунок 4. Архитектура хранения данных конструкторского, технологического и эксплуатационного состава
Разработка, согласование, утверждение, учет и изменение всех инженерных документов, а всех этапах проектирования осуществляется в электронном виде на основе бизнес-процессов, создаваемых в системе управления workflow, которая является частью PLM-системы Teamcenter. По результатам согласования (утверждение или изменение) версия объекта получает соответствующий статус. Согласование в электронном виде жестко привязано к схеме согласования, любой участник процесса может видеть на какой стадии находится объект, отправленный по процессу. В случае отклонения задачи специалист обязан оставить замечания или комментарий иначе отклонить задачу участнику согласования не удастся. Любой участник процесса согласования видит все замечания оставленные другими участниками. Все участники согласования получают сообщение по электронной почте о том, что к нему пришла задача, которую необходимо выполнить. Для оптимизации процесса используется подход запараллеливания задач согласования и обработки данных, что позволяет сократить сроки утверждения документов. Единая информационная среда источников и потребителей информации прежде всего позволяет кардинально изменить назначение бумажного документа и рассматривать его не как носитель информации, а как отчет, сформированный на основе соответствующего информационного объекта базы данных. Бумажный документ становится носителем юридического статуса и представляет собой набор данных из базы, распечатанный на бланке. При этом электронный документ сохраняется в централизованном электронном архиве, являющимся неотъемлемой частью системы, и связывается с объектом базы данных, на основании которого он был получен. Создатели информации (конструкторы, технологи) и ее потребители работают с соответствующим информационным объектом напрямую, имея при этом доступ к электронным документам в рамках прав, предоставленных им системой.
Применение на «КАЗ им. С.П. Горбунова» PLM-системы для управления полным жизненным циклом изделия позволило получить следующие эффекты, представленные в таблице 1.
Таблица 1.
Эффекты от применения PLM-системы на «КАЗ им. С.П. Горбунова»
Эффект |
Задача |
Описание преимущества |
Сокращение сроков, Повышение качества |
Конструкторская подготовка производства |
|
Сокращение сроков, Повышение качества |
Технологическая подготовка производства |
|
Сокращение сроков, Повышение качества, Снижение цены
|
Производство изделия
|
|
