РАЗРАБОТКА ЗАХВАТНОГО УСТРОЙСТВА ПРОМЫШЛЕННОГО РОБОТА ДЛЯ КУЗОВНОЙ СБОРКИ АВТОМОБИЛЕЙ
Журнал: Научный журнал «Студенческий форум» выпуск №5(184)
Рубрика: Технические науки
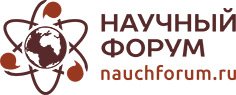
Научный журнал «Студенческий форум» выпуск №5(184)
РАЗРАБОТКА ЗАХВАТНОГО УСТРОЙСТВА ПРОМЫШЛЕННОГО РОБОТА ДЛЯ КУЗОВНОЙ СБОРКИ АВТОМОБИЛЕЙ
В данной статье рассмотрены этапы разработки и расчёта захватного устройства, устанавливаемого на торцевой части промышленного робота. Данное устройство служит для фиксации и транспортировки деталей кузовной части автомобиля.
Этап проектирования начинается с анализа исходных данных: геометрии автодетали; материала из которого автодеталь изготовлена; наличие не зафиксированных и подвижных деталей в сборке; последовательность обработки автодетали и особенности технологического процесса сборки.
Далее необходимо определится с типом прижимного механизма в зависимости от материала автодетали и необходимого усилия прижима. Для рассматриваемого проекта был выбран прижимной пневматический клапан фирмы “Tunkers”. Технологические особенности данного устройства позволяют настраивать угол открытия в пределах от 50 до 1350; также клапана обладают противоударным блоком контактов и имеют срок эксплуатации 3 миллиона циклов срабатывания.
Далее определим требуемое усилие зажима [1]. Для этого воспользуемся формулой 1, по которой усилие зажима можно определить по толщине листа в месте прижима:
(1)
где – толщина листа в месте прижима.
Все зажимы с поворотным расположением рычага обеспечивают определённый крутящий момент на приводной оси. Формула 2 показывает уменьшение действующей силы зажима в зависимости от длины рычага, рисунок 1:
(2)
После определения необходимой силы зажима в зависимости от положения изготовленной детали, необходимо определить момент зажима
(3)
Рисунок 1. Определение длины зажимного рычага
Для исходной автодетали места зажима имеют толщину 0,7мм. По формуле (1) рассчитаем требуемое усилие зажима:
По формуле (3) определим момента зажима:
Далее полученное значение позволяет нам определить тип применяемого зажима: V50.1 (рисунок 2).
Характеристики выбранного зажимного механизма: диаметр цилиндра 50мм; эффективный момент зажима 80Нм; вес 4,3 кг; расход воздуха 290 см3.
Количество прижимных механизмов рассчитывается по количеству точек прижима автодетали. Условия зажима автодетали во всех точках одинаковые по толщине в месте прижима и по свойствам материала, поэтому выбранный тип клампа V50.1 будет применяться для всем прижимов. Количество применяемых зажимных механизмов равно количеству точек прижима.
Рисунок 2. Зажим с рычажным механизмом V50.1
После определения типа прижимного механизма необходимо исключить поворота автодетали в плоскости прижима. Для этого необходимо установить дополнительные ограничители в виде позиционирующих цилиндров, работающих по отверстию без усилия. Роль подобного ограничителя сводится к тому, чтобы не допустить отклонения автодетали в процессе транспортировки, а также увеличивает точность позиционирования. Минимальное количество позиционирующих цилиндров необходимое для ограничения поворота детали по всем плоскостям – 2шт. Поскольку позиционирующий цилиндр работает не по усилию, а как ограничитель, то требования к его подбору минимальны. В нашем случае выбраны стандартные позиционирующие цилиндры SZK30, рисунок 3.
Помимо фиксирующих элементов захватное устройство необходимо оснастить датчиками присутствия. Для обеспечения надёжности используем два датчика один из которых будет дублирующий.
После того, как было определено количество прижимных механизмов и необходимого количества позиционирующих цилиндров можно приступать к этапу проектирования каркаса для захватного устройства.
Рисунок 3. Стандартный позиционирующий цилиндр SZK30
Проектирование захватного устройства базируется на Евро-грейферной технологии (EURO-Greifer-Tooling (EGT) [2]) и представляет собой сборку захвата из модулей стандартных компонентов. При проектировании было учтено, что грузоподъёмность промышленного робота составляет 210кг, диаметр фланца робота составляет 120мм.
В таблице представлена таблица стандартных EGT компонентов, использованных в процессе сборки захватного устройства:
Таблица 1.
Спецификация элементов сборки захватного устройства
Название компонента |
Внешний вид компонента |
Количество компонентов в сборке |
Восьмигранный профиль |
|
2,488м |
Базовая рама для выходного фланца робота |
|
1шт |
Переходники с восьмигранного профиля на 30мм круглый |
|
8шт |
Стальной круглый профиль 30мм |
|
2,955м |
Адаптеры для зажимов и соединительные элементы |
|
28шт |
Крепления для вакуумных эжекторов и датчиков |
|
2шт |
Переходники с 30мм на 30мм круглый профиль |
|
10шт |
Переходник на восьмигранный профиль |
|
12шт |
Плата крепления пневмоблока |
|
1шт |
Пневмоблок |
|
1шт |
После завершения всех подготовительных этапов и определения основных элементов каркаса захватного устройства можно приступать к этапу сборки. Сборка захватного устройства производится по геометрии автодетали с учётом расположения технологических отверстий. Внешний вид собранного захватного устройства представлен на рисунке 4.
Заключительный этап проектирования захватного устройства для промышленного робота заключается в расчёте нагрузки на оси робота. Для этого воспользуемся специализированным программным обеспечением KUKA Load [3], находящимся в свободном доступе на сайте разработчика.
Рисунок 4. Внешний вид захвата в сборе (вид спереди)
После завершения проектирования и указания материала всех элементов, входящих в состав захватного устройства, станет доступна расчётная информация по захватному устройству: центр масс; момент инерции и вес устройства, рисунок 5.
Рисунок 5. Расчётные данные модели захватного устройства
Используя полученные данные определим максимальную нагрузку на все оси робота в процессе транспортировки. На рисунке 6 представлены результаты статических (а) и динамических (б) нагрузок на оси промышленного робота:
Как видно из рисунка максимальная нагрузка приходится на 2-ю ось робота в статическом режиме, при этом нагрузка не превышает 70%. Полученный расчёт говорит о том, что собранное из представленных в спецификации (таблица 1) элементов, захватное устройство может использоваться промышленным роботом грузоподъёмностью до 210кг для транспортировки автодетали и выполнения некоторых технологических операций (например, стационарная точечная сварка).
|
|
а |
б |
Рисунок 6. Статические и динамические нагрузки на оси робота
В результате разработки и расчёта захватного устройства получена информация, позволяющая произвести сборку и установку захватного устройства на промышленный робот фирмы KUKA грузоподъёмностью не более 210кг с учётом веса автодетали.
