УПРАВЛЕНИЕ НЕСООТВЕТСТВИЯМИ В МАШИНОСТРОИТЕЛЬНОМ ПРОИЗВОДСТВЕ НА ПРИМЕРЕ «ПАРОПЕРЕГРЕВАТЕЛЯ 1 СТУПЕНИ» ДЛЯ СЕПАРАТОРА ПАРОПЕРЕГРЕВАТЕЛЯ
Журнал: Научный журнал «Студенческий форум» выпуск №10(233)
Рубрика: Технические науки
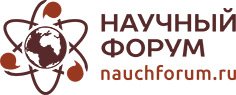
Научный журнал «Студенческий форум» выпуск №10(233)
УПРАВЛЕНИЕ НЕСООТВЕТСТВИЯМИ В МАШИНОСТРОИТЕЛЬНОМ ПРОИЗВОДСТВЕ НА ПРИМЕРЕ «ПАРОПЕРЕГРЕВАТЕЛЯ 1 СТУПЕНИ» ДЛЯ СЕПАРАТОРА ПАРОПЕРЕГРЕВАТЕЛЯ
Аннотация. В статье представлен пример отчёта о несоответствии продукции машиностроительного производства. В процессе изготовления обнаружено несоответствие конструкторский и производственно- техничкой документациям, в связи с чем выписан отчёт о несоответствии. Также в данной статье представлены временные сдерживающие действия, направленные на устранение выявленного несоответствия в производстве. Данная процедура осуществляется на основе методологии 8D, благодаря которой формируются корректирующие и предупреждающие действия для устранения возможности повторного появление подобных несоответствий.
Ключевые слова: рабочая конструкторская и производственно-техническая документации, управление несоответствиями, управление качеством, методология 8D, временные сдерживающие действия, корректирующие действия, предупреждающие действия.
Вступление (Introduction):
При производстве изделий и оборудований в любой организации возникают трудности в сфере качественного изготовления: обнаружение дефектов, отклонение от требований рабочей конструкторский и/или производственно-технологической документаций. Несоответствие может появиться на любом этапе жизненного цикла продукции: при проектировании, конструировании, изготовлении, монтаже или эксплуатации изделия. В машиностроительном производстве на этапе изготовления оборудования возникают следующие виды несоответствия продукций, например, геометрические и габаритные размеры не соответствуют требованиям чертежа, перпендикулярность деталей после сварки нарушена, толщина лакокрасочного покрытия меньше требуемой в инструкции по консервации, механическая обработка детали не соответствует требованиям чертеж и т.д. При несоответствии продукции требуемым конструкторской и производственно-технической документациям осуществляются действия, направленные на их устранение, в связи с чем возникают потери времени производства. Для устранения потерь и повышения качества изготавливаемых изделий необходимо внедрить в производство контроль несоответствиями продукций.
Целью управления несоответствиями является предотвращение их повторного появления, исключение вероятности неумышленного (непреднамеренного) использования или поставки несоответствующей продукции потребителю (заказчику), а также принятие решения по несоответствию. Данная деятельность относится как к выпущенной продукции, так и полученной от сторонних организаций. [1]
Целью данной статьи является: продемонстрировать, как управление несоответствиями на основе методологии 8D при внедрении в производственный процесс способствует координации деятельности предприятия, устранению бракованных изделий, улучшению качества изготавливаемой продукции, усовершенствованию конструкторской и производственно-технической документаций.
При осуществлении производственной деятельности в силу различных факторов могут возникать несоответствия, связанные с невыполнением требований, как внутренних, установленных на предприятии, так и внешних требований, определенных соответствующими нормами и правилами, регулирующими деятельность.
Для обнаружения всех дефектов изготавливаемого оборудования контроль осуществляется в несколько этапов. Первый этап – это визуально измерительный контроль сварного соединения инспектором отдела технического контроля, далее в зависимости от рабочей конструкторской и производственно-технической документаций осуществляются следующие виды контроля: капиллярный контроль, радиографический, ультразвуковой контроли и т.д. После их завершения производится контроль качества готового изделия уполномоченной организацией и/или заказчиками.
Вид контроля уполномоченной организации определяется в плане качества изделия. В данном документе прописаны контрольные точки, которым присваиваются статусы: WP, HP, WP(R). Для контрольных точек плана качества работникам уполномоченной организации, выполняющим работы по оценке соответствия в форме приемки, устанавливается статус участия «НР», «WP» или «WP (R)». Статус участия «Hold Point» — «точка задержки, HP»: контроль осуществляется путем непосредственного участия в контрольных операциях (испытаниях) с условием, что на время проведения данных операций производственный процесс должен быть остановлен и его продолжение возможно только после получения удовлетворительного результата их выполнения. Статус участия «Witness Point» — «точка освидетельствования, WP», в данной точке контроль осуществляется путем наблюдения за ходом технологических и/или контрольных операций (испытаний) без останова производственного процесса. Статус участия «Witness Point (Report)» — «точка освидетельствования по документам, WP (R)»: контроль осуществляется по документам путем проверки отчетной документации по результатам проведения соответствующих операций. [2]
До начала проведения приёмки оборудования представитель заказчика и уполномоченная организация осуществляют контроль в соответствии с планом качества, контроль соответствующих изделий и производственного процесса их изготовления. При статусе точки плана качества «WP» уполномоченная организация осуществляет контроль путём наблюдения за ходом операции. В случае обнаружения несоответствия во время наблюдения за ходом производственного процесса выписывается отчет о несоответствии, который способствует предприятию – изготовителю устранить брак.
Управление несоответствиями на машиностроительных предприятиях чаще всего осуществляется на основе методологии 8Д. Решение проблем качества с помощью данной методики базируется на методологическом или аналитическом методе. Система 8D предназначена для определения именно коренных причин несоответствий. Она также включает в себя разработку корректирующих и предупреждающих действий, то есть разработку краткосрочного решения проблемы и реализацию долгосрочных планов для предотвращения повторения этих проблем в будущем. [3]
Управление несоответствиями осуществляется с учетом методологии 8D путем выполнения следующих задач и процедур:
− оповещение о несоответствии;
− формирование Команды;
− уточнение и/или дополнение описания несоответствия (при необходимости);
− планирование и реализация коррекции и ВСД;
− определение коренных причин несоответствия;
− разработка и реализация корректирующих действий;
− разработка и реализация предупреждающих действий;
− формализация выводов. [1]
Благодаря временным сдерживающим действиям (ВСД) устраняется несоответствие, а благодаря корректирующим и предупреждающим действиям, определяются коренные причины возникновения несоответствия и в производство внедряются новшества, которые помогают улучшить качество изготавливаемой продукции (способствуют устранению возможности появления повторных несоответствий в будущем).
Так, в рамках проведения оценки соответствия в контрольной точке 9.6 WP Плана качества АЭС АККУЮ «Пароперегреватель 1 ступени», в процессе наблюдения за ходом технологических и контрольных операций по выполнению сварных швов С03, С04, С05, С06, при проверке документации по ремонту, а также при осмотре изготавливаемого оборудования выявлены следующие несоответствия:
1. В отчёте по радиографическому контролю сварных соединений и наплавок указанные мастером производственного подразделения отметки о проведении и исправлении дефектных мест не координируются с видами операций, указанными инженером лаборатории.
2. В отчёте по радиографическому контролю сварных соединений и наплавок проконтролированы выборки сварного шва С06 работником службы качества, мастером отражены добранные выборки для сварного шва С06, без предъявления работнику службы качества. При проверке журнала пооперационного контроля производственного подразделения, в форме ИК1/3 выявлена отметка мастера о проведении сварочных (ремонтных) работ на сварном шве С06 (место 22) без заключения результата контроля ОТК, что также подтверждается отметкой в карте выдачи сварочных материалов из кладовой на рабочее место и требованием на выдачу сварочных материалов в количестве 1,7 кг. 3. При осмотре оборудования, а именно выборок сварного шва С05 установлено, что в районе дефектных участков 12, 1, 2, 3, указанных в Приложении А, производились сварочные работы без предъявления работнику службы качества, а также без отметки в журнале пооперационного контроля.
После опубликования, присвоения номера, и формировании уведомлении осуществляется анализ значимости, данное несоответствие было принято «незначительным», объём работ назначен D3. Сформированная команда с лидером приняла решение осуществить следующие виды коррекций и ВСД:
По пункту 1 - Ремонтное место 10 (сварного шва С05) после отметки инженера центральной лаборатории методов неразрушающего контроля «10-годен, варить» было добрано для обеспечения возможности выполнения сварки, и данное действие не является несоответствием на основании п. 6.5 (второй абзац и последний абзац) инструкции 66.04.1341.
Заключение по результатам радиографического контроля "варить" свидетельствует об отсутствии дефектов в выборке; при указании размеров выборки (ремонтное место № 10) мастером допущена опечатка в значении глубины выборки при заполнении отчета по РГК. При предъявлении размеров выборок работникам БТК мастером производственного подразделения и инспектором технического контроля зафиксированы фактические размеры выборок. Сварочные работы данного ремонтного места не проводились. Объяснительные прилагаются;
По пункту 2- Внести в отчет по радиографическому контролю сведения по заварке дефектного места №22. (Мастером производственного подразделения в отчете по радиографическому контролю не был отражен факт заварки ремонтного места № 22 сварного шва С06, по которому была команда "варить" 06.10.2022, факт проведения сварочных работ места № 22 был отражен только в карте операционного контроля ИК-1/3.
Учитывая то, что работником отдела технического контроля не был подписан факт заварки дефектного места 22 (по причине отсутствия указания конструктора и сварщика) в операционном журнале, было принято решение о выборке заваренного места. Выборки сварного шва, проконтролированные мастером и занесенные в отчет № 779/715 были повторно проконтролированы мастером и предъявлены на контроль работникам отдела технического контроля. До проставления электронной подписи инспектором ТК в схеме радиографического контроля у мастеров производственного продразделения есть возможность проведения корректировки своих записей, поэтому мастер производственного подразделения исправил размеры выборок по факту проведенного контроля.
По п. 3- Сварочные работы на сварных швах С03-С06, кроме заварки дефектного места № 22 11.10.2022 не производились.
В настоящее время проводится контроль полноты удаления дефектов в сварных швах, выписан отчет о несоответствии, провести дополнительное ознакомление мастеров производственного подразделения с инструкцией ИК-1.
При любых несоответствиях, обнаруженных на различных стадиях жизненного цикла продукции, при неудовлетворительном состоянии оборудования или оснастки необходимо провести:
– анализ технологического процесса изготовления продукции с целью выявления причин появления несоответствий и их устранения;
– анализ технической документации на изготовление продукции. В случае обнаружения каких-либо ошибок в технической документации необходимо внести соответствующие изменения;
– контроль выполнения ранее принятых мероприятий и оценка их эффективности;
– контроль внесения изменений, являющихся результатом корректирующих действий, в соответствующую документацию.
После реализации всех мероприятий в отношении несоответствия проводится оценка их результативности. Оценивается период, позволяющий определить наличие/отсутствие повторного несоответствия.
В случае если в указанный период несоответствие повторно не выявлено, то выполненные действия исключили из системы менеджмента причину несоответствия и могут считаться результативными. В противном случае регистрируется повторное несоответствие, и процедура повторяется. [4]
На основании статистических данных (база несоответствий), сформированных посредством контура, структурными подразделениями проводится анализ областей зарегистрированных несоответствий, состава запланированных мероприятий в разрезе отчетного периода. По результатам такого анализа формируются мероприятия, направленные на совершенствование как отдельных процессов, так и системы менеджмента в целом. [4]
Выводы (Conclusions)
В данном примере после обнаружения несоответствия производился ряд действий, направленных на его устранение: внесение в отчет по радиографическому контролю сведения по заварке дефектного места, ознакомление мастеров производственного подразделения с инструкцией ИК-1, контроль полноты удаления дефектов в сварных швах.
Однако только осуществления временных сдерживающих действий недостаточно. Нужно вносить в производство корректирующие и предупреждающие действия, в целях устранения возможности появления повторных подобных несоответствий. В данном случае в производственно – техническую документацию, а точнее в спецификацию процесса сварки и в инструкцию по устранению дефектных мест, внесены изменения, а также усилен контроль радиографического контроля.
В машиностроительном производстве сформирована высокая культура работы с несоответствиями, процедура управления которыми внедрена во все процессы и виды деятельности предприятия. Все это является мощным инструментом для обеспечения стабильного выполнения производственных планов компании по строительству атомных электростанций, поддержания высокого уровня надежности и безопасности производственной инфраструктуры, как для работников, так и для окружающей среды.
Приложение А
Эскиз сварного шва C03, C05.
