Проведение экспериментов по выявлению проблем обработки резанием композиционных материалов
Журнал: Научный журнал «Студенческий форум» выпуск №12(33)
Рубрика: Технические науки
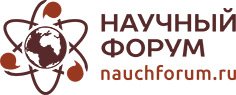
Научный журнал «Студенческий форум» выпуск №12(33)
Проведение экспериментов по выявлению проблем обработки резанием композиционных материалов
CARRYING OUT EXPERIMENTS TO IDENTIFY THE PROBLEMS OF CUTTING PROCESSING OF COMPOSITE MATERIALS
Egor Krivogin
Undergraduate, Department of Machine Building Technology Far Eastern national university, Russia, Vladivostok
Аннотация. В статье рассматривается прямое получение качественных оценок и численных данных для сравнения достижимых показателей качества резания композиционных материалов. Установлена принципиальная возможность безаварийного резания данного типа образцов на данной установке с любыми доступными параметрами. Собрана и обработана информация для дальнейшего анализа – об устранимых и неустранимых дефектах, влиянии внешних факторов, возможностях оптимизации процесса.
Сделана попытка просто и доступно изложить наиболее важные сведения об обрабатываемости композитов.
Abstract. The article deals with the direct obtaining of qualitative estimates and numerical data for comparison of achievable quality parameters of cutting of composite materials. Сollected and processed information for further analysis - on removable and unrecoverable defects, the influence of external factors, the possibilities of optimizing the process. The possibility of accident-free cutting of this type of specimen at a given plant with any available parameters is established in principle. An attempt is made simply and easily to present the most important information about the workability of composites.
Ключевые слова: композит, композиционные материалы, ширина реза, расслоение, вытягивание нитей, износ нитей, образец.
Keywords: composite, composite materials, width of cut, stratification, stretching of threads, thread wear, sample.
Целью эксперимента является прямое получение качественных оценок и численных данных для сравнения достижимых показателей качества резания композиционных материалов.
Показатели качества реза можно разделить на три группы.
Первая, это геометрический параметр:
· ширина реза;
Вторая, наличие недопустимых (неустранимых) дефектов материала реза и прилегающих областей:
· оплавление;
· выгорание отдельных слоев;
· расслоение;
· вытягивание нитей;
· износ нитей;
Третья, наличие допустимых (устранимых) дефектов материала реза и прилегающих областей:
· недорез волокон;
· иное повреждение прилегающей поверхности.
Любой из физических способов резки композиционных материалов на практике представляет собой результат многопараметрической оптимизации, примененной к часто плохо определенному и не всегда устойчивому набору технологических условий, поэтому даже теоретически нельзя рассчитывать на получение рекомендаций в виде оптимальных режимов резания. Однако ограниченный по ресурсам эксперимент может указать диапазоны параметров, в которых можно получить приемлемое качество реза по тому или иному сочетанию параметров. Дальнейшее совершенствование режима резания может являться только результатом опытной эксплуатации конкретной технологической установки в совокупности с набором технологических задач.
Поскольку количество образцов и доступных экспериментальных установок ограничено, то эксперименты предусматривают последовательное получение лишь необходимых показателей качества, начиная с констатации факта возможности резания. Будучи приложено к ограниченной материальной базе эксперимента (в случае исчерпания доступных мест реза), правило означает исполнение экспериментов в порядке уменьшения приоритета:
1) установление принципиальной возможности безаварийного резания данного типа образцов на данной установке с любыми доступными параметрами на усмотрение экспериментатора; в зависимости от возможности выполнения этого пункта экспериментатор может принять решение о прекращении эксперимента – с указанием причин;
2) установление принципиальной возможности резания на минимально устойчивых значениях технологических параметров для данного вида оборудования (этот пункт зачастую может быть объединен с предыдущим);
3) установление диапазона или нескольких диапазонов параметров процесса, при которых достигается удовлетворительные показатели геометрической группы качества реза;
4) установление диапазонов параметров процесса, при которых достигается удовлетворительное качество по группе неустранимых дефектов;
5) установление диапазона параметров процесса, при которых достигается удовлетворительное качество по группе допустимых (устранимых) дефектов;
Принцип последовательного независимого исследования (достижения) отдельных показателей качества позволяет сократить количество необходимых экспериментов, не жертвуя достоверностью.
Таким образом, при выполнении задач эксперимента первоочередное внимание обращается на первые три задачи (поскольку они могут помочь изъять тот или иной метод резки из дальнейшего рассмотрения), собирается и обрабатывается информация для дальнейшего анализа – об устранимых и неустранимых дефектах, влиянии внешних факторов, возможностях оптимизации процесса.
Образы для экспериментальной резки представляют собой прямоугольные слоеные панели 150х180мм определенной толщины, выполненные сплошными слоями материалов.[1] Состав и размеры образцов представлены в таблице 1.
Таблица 1.
Состав и размеры образцов
№ Образца |
№Слоя |
Состав слоя |
Количество слоев |
Толщина образца мм |
1 |
1 |
Стеклоткань Т-10-80 |
1 |
1,4 |
2 |
Углеткань УТ-900-2,5 |
2 |
||
3 |
Стеклоткань Т-10-80 |
1 |
||
2 |
1 |
Стеклоткань Т-10-80 |
1 |
5,75 |
2 |
Углеткань УТ-900-2,5 |
18 |
||
3 |
Стеклоткань Т-10-80 |
1 |
||
3 |
1 |
Органит 12Т |
1 |
2,1 |
2 |
Углепластик КМУ-11ТР |
4 |
||
3 |
Органит 12Т |
2 |
||
4 |
Углепластик КМУ-11ТР |
1 |
||
5 |
Органит 12Т |
2 |
Образцы изготовлены с применением метода термоотверждения или клеевых материалов. Черновое разрезание на отдельные панели произведено алмазным абразивным инструментом.
Для эксперимента приведено описание материала (таблица 2), в которое входит информация о количестве, толщине и глубине залегания слоев, приведена общая толщина, справочные свойства всех материалов, примененных для изготовления панели.
Таблица 2.
Спецификация структуры панелей(заготовок) с учетом толщины слоев
Образец 1 |
||||
№ листа |
Материал |
Кол-во слоев |
Ориент. нитей |
Толщина |
1 |
Стеклоткань Т-10-80 |
1 |
0° |
0,4 |
2 |
Углеткань УТ-900-2,5 |
2 |
0° |
0,6 |
3 |
Стеклоткань Т-10-80 |
1 |
0° |
0,4 |
Образец 2 |
||||
№ листа |
Материал |
Кол-во слоев |
Ориент. нитей |
Толщина |
1 |
Стеклоткань Т-10-80 |
1 |
0° |
0,4 |
2 |
Углеткань УТ-900-2,5 |
2 |
0° |
0,6 |
3 |
Углеткань УТ-900-2,5 |
4 |
0° |
0,96 |
4 |
Углеткань УТ-900-2,5 |
12 |
0° |
2,88 |
5 |
Стеклоткань Т-10-80 |
1 |
0° |
0,4 |
Образец 3 |
||||
№ листа |
Материал |
Кол-во слоев |
Ориент. нитей |
Толщина |
1 |
Органит 12Т |
1 |
0° |
0,08 |
2 |
Углепластик КМУ-11ТР |
4 |
0° |
1,2 |
3 |
Органит 12Т |
1 |
90° |
0,08 |
4 |
Органит 12Т |
1 |
0° |
0,08 |
5 |
Углепластик КМУ-11ТР |
1 |
0° |
0,3 |
6 |
Органит 12Т |
2 |
90° |
0,08 |
Стеклоткань Т-10-80 - Ткань стеклянная Т-10-80 ГОСТ 19170-73.
Стеклоткани Т-10-80. Представляют собой стеклянные волокна и тканые материалы, используемые для изготовления стеклопластиков. Характеризуются высокой прочностью на разрыв, низким удельным весом, низкой теплопроводностью, высокой теплостойкостью, стойкостью к химическому и биологическому воздействию. Классифицируются по типам волокон и переплетения, которые влияют на анизотропию свойств. Для целей механообработки важной их особенностью является высокая твердость и абразивные свойства. В виде тканей или препрегов кроятся механическими ножницами и ультразвуковыми устройствами резки.[2]
Органит 12Т - Препрег органопластик Органит 12Т, ТУ 1-595-11-632-2001.
Органиты (органотекстолиты). По причине близости химического происхождения связующего и наполнителя, часть свойств материала более равномерна по всему объёму: химическая активность, плотность, теплопроводность, термостойкость и горючесть примерно одинаковые, что способствует принципиально большей применимости термических методов резки. Сходство материалов матрицы и наполнителя способствует наибольшей адгезии волокон и связующего среди всех ПКМ. Существует анизотропия механических свойств, что делает механообработку зависимой от направления волокон. Особенность органитов – большая по сравнению с углеволокном и стекловолокном степень растяжения волокон, что приводит к эффекту смятия и недорезания волокон. Рекомендуется обработка алмазным абразивом. Возможные методы обработки – плазменный, лазерный, фрезерный, ультразвуковой, гидроабразивный. Тонкие листовые детали хорошо режутся механическими ножницами с твердосплавными рабочими кромками.[3]
Углеткань УТ-900-2,5 - Углеткань УТ-900-2,5 ТУ6-06-16-105-88.
Углеродные волокна и тканые материалы: лента типа ЛУ, жгут типа ВМН, углеткани. Углеволокно, из которого создаются углеткани, состоит из волокон 5-10 мкм в диаметре, образованных из атомов углерода. Материал обладает низким удельным весом и высокими прочностными характеристиками, низкой плотностью, низким температурным коэффициентом линейного расширения, высокой устойчивостью к ионизирующему излучению и воздействию большинства химически агрессивных реагентов, низким коэффициентом трения. Электропроводны, обладают большой удельной поверхностью. С точки зрения механической обработки важно расположение волокон относительно направления механического воздействия. Поперечный сдвиг и излом облегчены, и, напротив, прочность на разрыв максимальна среди всех применяемых в ПКМ наполнителей. В виде тканей или препрегов кроятся механическими ножницами и ультразвуковыми устройствами резки.[4]
Углепластик КМУ-11ТР - КМУ-11ТР ТУ1-595-11-573-99.
По удельным характеристикам (отношению прочности и жесткости к плотности) углепластики превосходят все известные металлические аналоги, такие как сталь, титан, алюминий в 5-8 раз. Однако низкая прочность на излом приводит к относительно легкому поперечному разрушению слоёв. Типовой рекомендуемый способ обработки – абразивный с помощью инструмента с алмазным напылением. Высокая теплопроводность и тугоплавкость волокон затрудняют термическое разрушение наполнителя и приводят к разрушению смежного объёма связующего, причем в значительной по величине области. Электропроводность делает возможной обработку электрофизическими методами. Также возможна: плазменная, лазерная, ультразвуковая, гидроабразивная, фрезерная резка.[5]
Эксперимент проводился на универсально-фрезерном станке JMD-26X2 XY. Максимальная частота вращения горизонтального шпинделя-1300 об/мин, размер стола-1120х260мм, мощность двигателя-2.2 кВТ (таблица 3).
Таблица 3.
Основные характеристики универсально-фрезерного станка JMD-26X2 XY
№ п/п |
Описание модели |
JMD-26X2 XY |
1 |
Максимальный диаметр сверления, мм |
40(Чугун) 16(Автоподача, Чугун) |
2 |
Максимальный диаметр концевого фрезерования, мм |
25 |
3 |
Конус шпинделя |
ISO 40(вертикальный) |
ISO 40(горизонтальный) |
||
4 |
Частота вращения вертикального шпинделя, об/мин |
67,103,171,210,263,322,420,645,1070,1315,1640,2010 |
5 |
Частота вращения горизонтального шпинделя, об/мин |
40,60,80,110,150,200,270,380,510,680,950,1300 |
6 |
Расстояние между вертикальным шпинделем и стойкой, мм |
200-550 |
7 |
Расстояние между вертикальным шпинделем и столом, мм |
80-420 |
8 |
Расстояние между горизонтальным шпинделем и столом, мм |
0-340 |
9 |
Ход пиноли вертикального шпинделя |
120 |
10 |
Размер стола, мм |
1120х260 |
11 |
Ход стола, мм |
600х300 |
12 |
Двигатель, модель/мощность, кВт |
YD100L-6/4 1,5/2,2 кВт(вертикальный) |
Y100L1-4 2,2 кВт(горизонтальный) |
||
13 |
Габаритные размеры (ДхШхВ), мм |
1580х1450х2150 |
Масса, кг |
1300 |
В качестве инструмента использовалась фреза дисковая отрезная P6AM5 125х3.5мм ГОСТ 2679-93.[6]
В течение и после проведения экспериментов по резанию необходимо провести измерения образцов. Для этого использовался штангенциркуль 0.05мм.
В ходе эксперимента было использовано следующие закрепление: на стол универсально-фрезерного станка устанавливалась металлическая пластина 180х180 мм и шириной 5мм. Сверху устанавливалась экспериментальная пластина с вылетом под обработку в 30мм. Для дополнительной фиксации поверх экспериментальной пластины была установлена еще одна металлическая пластина 180х180 и шириной 5мм, и вся эта конструкция закреплялась двумя прижимами с противоположных сторон.
Эксперимент проводился при следующих условиях: было выбрано три частоты вращения шпинделя (200, 510 и 1300 об/мин) и две скорости подачи (74 и 170 мм/мин), фрезерование пазов выбрано попутное. На протяжении всего эксперимента использовался один и тот же инструмент - фреза дисковая отрезная P6AM5 125х3.5мм ГОСТ 2679-93.
Эксперимент по резанию состоял в получении пазов в панелях, обработке полученных данных, фотографировании образцов структур реза, занесении результатов в таблицы и анализе результатов экспериментов.
Основной упор в эксперименте сделан на исследовании показателей качества обработки при использовании режущего инструмента при разных режимах резания.
Для качественной оценки или измерения показателей качества реза использовались следующие инструменты и методики.
Ширина реза (геометрический параметр). Измеряется штангенциркулем, 0,05мм, среднее трех замеров.
Оплавление (неустранимый дефект), определяется визуально по изменению цвета, по отражению света на срезе.
Выгорание отдельных слоев (неустранимый дефект), определяется визуально.
Расслоение (неустранимый дефект), определяется визуально.
Износ нитей, махрение, измочаливание (неустранимый дефект), определяется визуально.
Недорез волокон (устранимый дефект), определяется визуально.
Иное повреждение прилегающей поверхности (устранимый дефект), определяется визуально.
В ходе эксперимента, при использовании различного материала и разных режимов обработки, были получены следующие данные для определения ширины реза (таблица 4 и таблица 5).
Таблица 4.
Определение ширины реза при разных режимах обработки
Образец 1 |
|||
Подача мм/мин |
Скорость вращения шпинделя об/мин |
||
200 |
510 |
1300 |
|
74 |
3,8 |
3,6 |
3,5 |
170 |
3,65 |
3,6 |
3,6 |
Образец 2 |
|||
Подача мм/мин |
Скорость вращения шпинделя об/мин |
||
200 |
510 |
1300 |
|
74 |
3,6 |
3,5 |
3,5 |
170 |
3,5 |
3,6 |
3,6 |
Образец 3 |
|||
Подача мм/мин |
Скорость вращения шпинделя об/мин |
||
200 |
510 |
1300 |
|
74 |
3,7 |
3,7 |
3,5 |
170 |
3,6 |
3,8 |
3,8 |
Таблица 5.
Визуальная оценка качества реза
Образец 1 |
||
Подача 74 мм/мин |
||
Скорость вращения шпинделя об/мин |
||
200 |
510 |
1300 |
Фото №1 |
Фото №2 |
Фото №3 |
|
|
|
Качественная оценка реза |
||
Недорез волокон нижних слоев, вытягивание нитей |
Износ нитей |
Износ нитей, Недорез волокон |
Подача 170 мм/мин |
||
Скорость вращения шпинделя об/мин |
||
200 |
510 |
1300 |
Фото №4 |
Фото №5 |
Фото №6 |
|
|
|
Качественная оценка реза |
||
Недорез волокон нижних слоев |
Износ нитей |
Износ нитей |
Образец 2 |
||
Подача 74 мм/мин |
||
Скорость вращения шпинделя об/мин |
||
200 |
510 |
1300 |
Фото №7 |
Фото №8 |
Фото №9 |
|
|
|
Качественная оценка реза |
||
Износ нитей |
При осмотре поверхностных дефектов обнаружено не было |
Износ нитей |
Подача 170 мм/мин |
||
Скорость вращения шпинделя об/мин |
||
200 |
510 |
1300 |
Фото №10 |
Фото №11 |
Фото №12 |
|
|
|
Качественная оценка реза |
||
Износ нитей |
Износ нитей и небольшой недорез волокон |
При осмотре поверхностных дефектов обнаружено не было |
Образец 3 |
||
Подача 74 мм/мин |
||
Скорость вращения шпинделя об/мин |
||
200 |
510 |
1300 |
Фото №13 |
Фото №14 |
Фото №15 |
|
|
|
Качественная оценка реза |
||
Износ нитей, недорез волокон |
Недорез волокон |
Недорез волокон |
Подача 170 мм/мин |
||
Скорость вращения шпинделя об/мин |
||
200 |
510 |
1300 |
Фото №16 |
Фото №17 |
Фото №18 |
|
|
|
Качественная оценка реза |
||
Износ нитей, недорез волокон |
Износ нитей |
Износ нитей, недорез волокон |
По результатам экспериментов видно, что при одинаковых режимах ширина реза у пластин различная. Это говорит о том, что состав пластин влияет на качество обработки, и для достижения наилучшего результата, для каждой пластины необходимо подбирать режимы индивидуально, в зависимости от состава пластины.
Для анализа полученных данных было использовано приложение MS Excel и инструмент анализа данных Регрессия.
Принятые обозначения для расчетов:
Для образца 1.
Y – ширина реза, мм |
X1 – скорость вращения шпинделя, об/мин |
X2 – подача, мм/мин |
Рисунок. 1. Данные ширины реза, скорости вращения шпинделя и подачи для образца 1
Для образца 2.
Y – ширина реза, мм |
X1 – скорость вращения шпинделя, об/мин |
X2 – подача, мм/мин |
Рисунок. 2. Данные ширины реза, скорости вращения шпинделя и подачи для образца 2
Для образца 3.
Y – ширина реза, мм |
X1 – скорость вращения шпинделя, об/мин |
X2 – подача, мм/мин |
Рисунок. 3. Данные ширины реза, скорости вращения шпинделя и подачи для образца 3
Для построения уравнения множественной регрессии сначала необходимо рассчитать параметры линейного уравнения множественной регрессии. Данная операция проводится с помощью инструмента анализа данных Регрессия. Для этого выбираем меню СервисàАнализ данныхàРегрессия. Далее заполняем появившееся диалоговое окно следующим образом:
После нажатия кнопки ОК получим следующий результат:
Таблица 6.
Регрессионная статистика для образца 1
Регрессионная статистика |
|
Множественный R |
0,889166129191044 |
R-квадрат |
0,790616405300585 |
Нормированный R-квадрат |
0,58123281060117 |
Стандартная ошибка |
0,0354443446574554 |
Наблюдения |
5 |
Таблица 7.
Дисперсионный анализ для образца 1
Дисперсионный анализ |
|||||
|
df |
SS |
MS |
F |
Значимость F |
Регрессия |
2 |
0,00949 |
0,00474 |
3,7759 |
0,2094 |
Остаток |
2 |
0,00251 |
0,00126 |
|
|
Итого |
4 |
0,012 |
|
|
|
Коэффициенты |
Стандартная ошибка |
t-статистика |
P-Значение |
||
Y-пересечение |
3,570 |
0,06139 |
58,1483 |
0,0002964 |
|
200 |
-0,000066 |
0,0000363 |
-1,8184 |
0,2106271 |
|
74 |
0,00053 |
0,00035 |
1,52936 |
0,2657951 |
Таблица 8.
Регрессионная статистика для образца 2
Регрессионная статистика |
|
Множественный R |
0,761002641010043 |
R-квадрат |
0,579125019624261 |
Нормированный R-квадрат |
0,158250039248522 |
Стандартная ошибка |
0,0410304755212873 |
Наблюдения |
5 |
Таблица 9.
Дисперсионный анализ для образца 2
Дисперсионный анализ |
|||||
|
df |
SS |
MS |
F |
Значимость F |
Регрессия |
2 |
0,00463 |
0,00231 |
1,3760 |
0,4208 |
Остаток |
2 |
0,00336 |
0,00168 |
|
|
Итого |
4 |
0,008 |
|
|
|
Коэффициенты |
Стандартная ошибка |
t-статистика |
P-Значение |
||
Y-пересечение |
3,556 |
0,07107 |
50,0365 |
0,0003991 |
|
200 |
-0,000041 |
0,0000419 |
-0,9848 |
0,4285106 |
|
74 |
0,00041 |
0,00040 |
1,0400 |
0,4075334 |
Таблица 10.
Регрессионная статистика для образца 3
Регрессионная статистика |
|
Множественный R |
0,563194988477863 |
R-квадрат |
0,31718859504658 |
Нормированный R-квадрат |
-0,36562280990684 |
Стандартная ошибка |
0,152366622881838 |
Наблюдения |
5 |
Таблица 11.
Дисперсионный анализ для образца 3
Дисперсионный анализ |
|||||
|
df |
SS |
MS |
F |
Значимость F |
Регрессия |
2 |
0,02156 |
0,01078 |
0,4645 |
0,6828 |
Остаток |
2 |
0,04643 |
0,02321 |
|
|
Итого |
4 |
0,0679 |
|
|
|
Коэффициенты |
Стандартная ошибка |
t-статистика |
P-Значение |
||
Y-пересечение |
3,480 |
0,26393 |
13,1855 |
0,0057026 |
|
200 |
0,000015 |
0,00015 |
0,1007 |
0,9289631 |
|
74 |
0,00142 |
0,0014 |
0,9526 |
0,4413124 |
По результатам вычислений составим уравнение множественной регрессии для каждого образца:
Образец 1: y=a+b1x1+b2x2
Y=3,58-22,92x1+0,00053x2
Образец 2: y=a+b1x1+b2x2
Y=3,53+15,34x1+0,0002x2
Образец 3: y=a+b1x1+b2x2
Y=3,48-0,73x1+0,0001x2
Оценку надежности уравнения регрессии дает F-критерий Фишера. По данным регрессионного анализа, Fфак. =3,77(образец 1), Fфак. =0,03(образец 2), Fфак. =0,46(образец 3). Табличное значение F-критерия при числе степеней свободы 1 и 24 при уровне значимости 0,05 составит: F=9,55, т.е. фактическое значение F не превышает табличное (для всех образцов) и можно сделать вывод, что данное уравнение невозможно использовать для описания эксперимента.
Также по данным регрессионного анализа видно, что коэффициент детерминации R^2=0.79(образец 1), R^2=0,03(образец 2), R^2=0,32(образец 3). Он оценивает долю вариации результата за счет представленных в уравнении факторов в общей вариации результата. В нашем случае эта доля составляет 79%, 3% и 32% и указывает на весьма тесную связь факторов, только для первого образца, с результатом. Для образца 2 и 3 не достаточно данных чтобы использовать уравнение для описания эксперимента.
В результате серии экспериментов по резке композиционных материалов, методом лезвийная фрезерная обработка, на трех разных образцах, получены данные о практической возможности резания таких материалов указанным методом. Экспериментально получены данные о различных режимах резания, проанализированы параметры качества реза при каждом режиме резания.
Так как это был первый эксперимент, и он был направлен на установлении принципиальной возможности безаварийного резания данного типа образцов на данной установке с любыми доступными параметрами, то в процессе были выявлены следующие проблемы:
- при обработке некоторых пластин возникал неприятный запах, который мешал оператору находиться рядом с оборудованием.
- пластины из углеткани очень сильно крошились и так же источали неприятный запах.
- при обработке некоторых пластин возникал очень сильный шум(«писк»), который так же затруднял нахождение оператора рядом с оборудованием.
В последующих экспериментах предлагаются следующие решения ранее возникших проблем:
- установление дополнительной вытяжной системы рядом с обрабатываемой деталью.
- ограждение участка, во избежание разлета крошек материала.
- использовать другие режимы резания, большую скорость вращения шпинделя( от 2000 об/мин) и малую подачу.
