Обеспечение безопасности процесса переработки газового конденсата
Журнал: Научный журнал «Студенческий форум» выпуск №21(42)
Рубрика: Технические науки
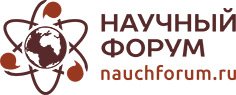
Научный журнал «Студенческий форум» выпуск №21(42)
Обеспечение безопасности процесса переработки газового конденсата
Аннотация. В статье рассмотрены возможные аварийные ситуации, которые могут возникнуть при переработке газового конденсата, их опознавательные признаки и оптимальные способы противоаварийной защиты. Для предотвращения данных аварийных ситуаций предложено использовать систему прогнозирования и оценки безопасности ОПО с использованием комплексной модели обеспечения безопасности.
Ключевые слова: газовый конденсат, стабилизация, аварийные ситуации, безопасность, опасный производственный объект, прогнозирование.
Keywords: gas condensate, stabilization, emergencies, safety, hazardous production facilities prediction, forecasting.
Газоперерабатывающие предприятия относятся к промышленным объектам повышенной опасности и отличаются высокой аварийностью эксплуатируемых объектов, несовершенством систем управления технологическими процессами и противоаварийной защиты, износа оборудования.
Анализ характера и причин аварий в данной отрасли [1] показывает, что в последнее десятилетие большинство из них (около 95 %) связано со взрывами: 54% в аппаратуре, 46% в производственных зданиях и на открытых технологических площадках. Статистика показывает, что из общего количества взрывов в 42,5% случаев происходят взрывы сжиженных углеводородных газов. При залповых выбросах горючих 7 % не сопровождаются воспламенением, 35% завершаются взрывами, в 23% случаев взрывы сочетаются с пожарами, 34% сопровождаются только пожарами.
На основании анализа результатов технического расследования аварий на предприятиях отрасли [2] выявлены следующие основные причины и условия возникновения и развития аварий:
· пожаровзрывоопасные свойства применяемого сырья, конечных и побочных продуктов;
· аппаратное оформление – наличие на установке аппаратов, находящихся под давлением, высокая плотность расположения оборудования, значительные объёмы взрывоопасных материалов, находящихся в аппаратах;
· ведение процесса при сравнительно высоких давлениях (до 1,6 МПа) и высоких температурах (до 250 ºС);
· выход параметров технологического процесса за критические значения изменения давления, температуры, уровня жидкости, состава сырья, дозы и скорости подачи сырья;
· нарушение герметичности оборудования;
· неисправность средств регулирования и противоаварийной защиты процессов;
· непрофессиональные и ошибочные действия обслуживающего персонала, в том числе при проведении сварочных и ремонтных работ, неудовлетворительная ревизия состояния оборудования и трубопроводов;
· нарушение правил технической эксплуатации, а также некомпетентность при принятии решений в экстремальных ситуациях;
· невыполнение на предприятиях графиков планово-предупредительного ремонта оборудования, некачественный монтаж или ремонт оборудования;
· вероятность появления источника воспламенения.
Процесс переработки газового конденсата является пожаро- и взрывоопасным в связи с тем, что он связан с проведением процесса ректификации при повышенных температурах и давлении, а его продуктами являются пары углеводородов, большинство из которых имеют низкую температуру вспышки и в результате взаимодействия с кислородом воздуха образуют смеси, взрывающуюся при наличии огня или искры.
Сущность процесса заключается в стабилизации конденсата с получением углеводородных газов, сжиженной пропан-бутановой фракции (ПБФ) и стабильного конденсата - газового конденсата, получаемого путем очистки нестабильного газового конденсата от примесей и выделения из него углеводородов С-С [3]. На рисунке 1 представлена схема одного из технологических блоков установки стабилизации конденсата.
Рисунок 1. Схема технологического блока установки стабилизации конденсата
Т–101/1 – теплообменник, К–101/1 - ректификационная колонна, ВХ–101/1-3, ВХ–102/4– холодильники, Е-101/1 - емкость орошения, Н-101/1,2, H-102/1,2 - насосы
В ходе изучения эксплуатационной документации подобных объектов были выявлены возможные аварийные ситуации, которые могут возникнуть при осуществлении данного процесса:
· выход параметров процесса за предельно допустимые значения.
· разгерметизация оборудования через торцовые и сальниковые уплотнения, фланцевые соединения, разгерметизация колонной и емкостной аппаратуры, змеевиков печей.
· выброс продукта из разрушенных аппаратов, трубопроводов с образованием взрывоопасного облака
· пожар
· взрыв парогазовоздушной смеси
Ключевая роль в обеспечении безопасности от возможных аварий отводится системам противоаварийной защиты, позволяющим проводить постоянный мониторинг наиболее важных зон объекта, а в критических ситуациях выполнять необходимые действия для предотвращения серьезных последствий.
Система противоаварийной защиты является компонентом распределенной системы управления (РСУ), которая в свою очередь является компонентом автоматизированной системы управления технологическим процессом (АСУ ТП) опасного производственного объекта (ОПО).
Система противоаварийной защиты предназначена для предупреждения и предотвращения аварийных ситуаций, которые могут возникнуть во время технологических процессов как в результате влияния человеческого фактора, так и из-за сбоев в работе оборудования.
Она строится на специально сертифицированных для таких целей моделях программируемых контроллеров. Контроллеры имеют дублированную архитектуру, что в несколько раз повышает отказоустойчивость оборудования отвечающее за предотвращение аварийных ситуаций.
В случае возникновения опасности развития аварийной ситуации контроллеры противоаварийной защиты реализуют алгоритмы по предотвращению аварийных ситуаций в соответствии с правилами локализации аварийных, принятыми на предприятии.
Система противоаварийной защиты параллельно с основной системой автоматизированного управления следит за состояниями аварийных сигнальных датчиков. В случае срабатывания которых система ПАЗ разрывает управление задвижками и двигателями от основной автоматизированной системы управления, в результате чего они останавливаются или закрываются.
Не меньшую роль в обеспечении промышленной безопасности в нефтегазоперерабатывающей отрасли имеет прогнозирование возможных аварийных ситуаций с дальнейшим их предупреждением.
Современным способом решения данной задачи является внедрение системы прогнозирования и оценки безопасности опасного производственного объекта (ОПО) с использованием комплексной модели обеспечения безопасности [4]. На рисунке 2 представлена схема осуществления системы прогнозирования и оценки безопасности ОПО.
Данная система включает рабочую станцию оператора с программным обеспечением, позволяющим строить комплексную модель обеспечения безопасности, производить расчеты показателей безопасности, риска и эффективности, сервер, сеть передачи и сбора информации, контроллеры ввода-вывода информации, коммутатор, сервер АСУ ТП, подключенный к системе через локальную вычислительную сеть объединенной расчетной системы; инженерно-технические системы обеспечения безопасного функционирования объекта, подключенные через модули ввода-вывода, блок сбора и обработки информации по режимам функционирования и параметрам технологического процесса, блок сбора и обработки информации по показателям надежности функционирования элементов РСУ, АСУ ТП, ПАЗ, технологического оборудования, блок сбора и обработки информации по опасным составляющим объекта, авариям и аварийным инцидентам, база данных по проектным решениям, база данных по комплексной модели обеспечения безопасности; база данных по показателям надежности, база данных по опасным составляющим объекта, блок моделирования, расчетный блок, блок анализа и оценки результатов моделирования и расчета показателей; блок выработки альтернативных технических решений и блок принятия решений.
Рисунок 2. Схема осуществления системы прогнозирования и оценки безопасности ОПО с использованием комплексной модели обеспечения безопасности
Данный способ относится к автоматизированным системам управления безопасностью опасного производственного объекта и может быть использован на всех этапах жизненного цикла объекта, а именно при проектировании, строительстве, эксплуатации и ликвидации опасного производственного объекта.
Система отличается тем, что анализ надежности, безопасности и эффективности функционирования опасного производственного объекта осуществляется с помощью общего логико-вероятностного метода (ОЛВМ). В блоках сбора и обработки информации обработка данных осуществляется с помощью единых алгоритмов, адаптированных к специфике конкретного опасного производственного объекта и с учетом имеющейся у проектировщика дополнительной информации о свойствах проектируемой системы опасного производственного объекта.
Техническим результатом изобретения является оценка состояния безопасности объекта на основе анализа расчетов показателей безопасности и риска и выработка рекомендаций по проведению мероприятий, направленных на снижение вероятности возникновения аварий и масштабов их последствий.
В результате прогнозирования и оценки показателей безопасности выбирается наиболее безопасный вариант проектных решений и утверждается комплексная модель обеспечения безопасности, которая будет сопровождать объект на последующих этапах жизненного цикла [4].
Таким образом, внедрение данной системы позволит минимизировать риск возникновения аварий на опасном производственном объекте, даст возможность своевременно выявить «слабые места» в обеспечении промышленной безопасности, а также провести необходимые мероприятия, направленные на предупреждение аварий и несчастных случаев.
