Управление технологическими объектами в реальном времени в системе литейного производства
Журнал: Научный журнал «Студенческий форум» выпуск №7(58)
Рубрика: Технические науки
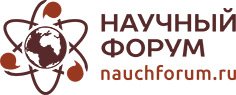
Научный журнал «Студенческий форум» выпуск №7(58)
Управление технологическими объектами в реальном времени в системе литейного производства
Система реального времени – автоматические системы, управляющее воздействие которых вырабатывается в промежутке времени между двумя соседними потоками информации с объекта управления.
Функцией АСУ ТП называют совокупность действий, направленных на достижение частной цели управления. Отличительной особенностью функцией является их законченность с технологической точки зрения, т.е. функция включает: получение информации из вне, ее обработку и выдачу результатов так же во внешнюю среду.
Для каждой функции реализуется полный набор определенных функций.
Технологический процесс – это совокупность трех действий: накопление, переработка и транспортировка.
Объекты реального времени делятся на 2 класса: дискретные и непрерывные процессы (рассматриваются за определенный промежуток времени).
Дискретные процессы – такие процессы, для которых можно определить точный момент с начала и окончания производственного цикла.
Непрерывные процессы – такие процессы характеристики, состояния которых изменяются непрерывно во времени и по множеству значений этих параметров в некоторых пределах.
Условием начала выполнения данного бизнес-процесса является поступление чертежа детали в литейный цех, вместе с ним задается план выпуска литых заготовок, в котором указываются сроки сдачи отливок в механический цех и количество отливок. По распоряжению начальника цеха начальник отдела назначает технолога для разработки технологического процесса. Технолог, руководствуясь стандартами предприятия, разрабатывает ТП в специальной программе Intermech на ПК. ТП включает в себя множество различных операций, которые выполняют квалифицированные рабочие на специальном оборудовании.
Рисунок 1. Главная функция
Перед разработкой ТП технолог, проанализировав чертеж детали, назначает припуски, формируя будущую заготовку, и отправляет заявку на создание 3D-модели заготовки конструктору.
Имея готовую 3D-модель заготовку в программе NX, можно приступать к разработке литейной оснастки, проектированием которой занимается конструктор, руководствуясь чертежом детали и картой заготовки.
Получив 3D-модель оснастки, необходимо разработать чертежи, по которым рабочие будут создавать готовую оснастку на станках с ЧПУ. Производство одной пресс-формы занимает несколько месяцев, после чего готовую оснастку необходимо проверить.
Пресс-форма служит для получения выплавляемой модели, которая полностью повторяет конфигурацию заготовки, поэтому важно соблюдать все геометрические размеры при разработке оснастки. В ее полость запрессовывают модельную массу, после небольшой выдержки вынимают готовую модель и собирают в блок с литниково-питающей системой. Все операции рабочие выполняют по инструкциям предприятия и операционным картам, которые разрабатывает технолог.
Рисунок 2 . Декомпозиция главной функции
Модельный блок после сборки поступает на операцию нанесения керамического покрытия и вытопки модельной массы, тем самым, получая готовую оболочку для заливки блока металлом. Прежде чем провести операцию «плавка-заливка» блок прокалывают в прокалочный печи при определенной температуре, заданной технологом, и заливают металлом. После затвердевания блок проходит операцию обрубки литниково-питающей системы на станках и зачистки и доводки геометрии самой заготовки. После проверки на годность отливку сдают в механический цех.
Рисунок 3. Декомпозиция функции получения литейной оснастки
На рисунке 3 показана декомпозиция функции получения литейной оснастки.
Пресс-форма состоит из большого числа элементов, туда входят: матрицы, разрядки, вставки, планки, винты, болты и т.д. [1]. Конструктор разрабатывает 3D-модель оснастки в программе NX на своем ПК, учитывая 3D-модель заготовки, разъем и количество моделей в пресс-форме.
После утверждения технологом 3D-модель оснастки, конструктор разрабатывает чертежи каждой части пресс-формы для наиболее точного изготовления.
Готовые чертежи поступают в механический цех, где изготавливают пресс-форму на станках с ЧПУ. Время изготовления одной пресс-формы занимает от двух месяцев до полугода.
Готовые пресс-формы проходят проверку в системе ATOS [2] и запускаются в производство.
Применение пресс-формы необходимо для особо ответственных деталей (лопатки ГТД, проставки и т.д.) серийного производства, где важным фактором производства является качество и конфигурация модели [1]. Для единичного или мелкосерийного производства применение пресс-формы невыгодно для предприятия.
