Сравнительный анализ электроимпульсной и электроискровой обработки металла
Журнал: Научный журнал «Студенческий форум» выпуск №17(68)
Рубрика: Технические науки
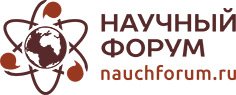
Научный журнал «Студенческий форум» выпуск №17(68)
Сравнительный анализ электроимпульсной и электроискровой обработки металла
Аннотация. В данной статье рассмотрены электроимпульсная и электроискровая обработки металлов, относящейся к нетрадиционным видам металлообработки.
Ключевые слова: электроэрозионная обработка (электроискровая, электроимпульсная, электроконтактная обработки).
Введение
Быстрое развитие авиационной, космической и роботизированной техники в современном мире нуждается в разработке и последующем их применение новых жаропрочных, тугоплавких и в то же время легких материалах, таких как никель- и хромсодержащих, а так же титановых сплавов. Решение множественных технологических и конструкторских задач, должны решить подобные типы материалов. Но такие материалы возможно обработать только с применением электрического тока, так как не смотря на сложность технологического процесса их обработки, использование электрического тока позволяет обработать подобные виды материалов без изменения их физико-механических свойств из-за которых они и применяются в космонавтике и авиации.[1] Ниже представлены основные электрические способы обработки заготовок, которые осуществляют удаление слоя металла под воздействием термического, химического или комбинированного действия электрического тока, подводимого непосредственно к детали и инструменту. При этом преобразование электрической энергии в другие виды энергии происходит в зоне обработки, образованной взаимодействующими поверхностями инструмента и обрабатываемой заготовки. Основными способами обработки материала с помощью электрического тока являются:
электроэрозионный, электрохимический, электроэрозионно-химический и электромеханический методы. При электроэрозионном методе удаление слоя материала с поверхности заготовки и изменение свойств поверхностного слоя детали происходит благодаря термическому воздействию электрического тока.
На сегодняшний день широкое распространение в промышлености получили такие способы электроэрозионной обработки как: электроискровой, электроимпульсный, анодно-механический, электроконтактный.
Все эти способы направлены на решение узких задач таких как:
- Удаление слоя материала с заготовки и получение заданной формы и размеров;
- Повышение износостойкости поверхностного слоя готовой детали.
Рисунок 1. Общая классификация электроэрозионных способов обработки металлов
На основе схемы 1 можно определить, что используя электроискровой и электроимпульсный способы можно произвести как удаление металла, так и упрочнение поверхностного слоя, а электро-контактный и анодно-механический позволяют только производить удаление металла с заготовки.[2]
Наиболее перспективными являются методы с использованием электрического тока для обработки деталей из твердых сплавов, жаропрочных сталей и специальных трудно обрабатываемых сплавов, получающих все большее применение в связи с повышением давлений, температур и скоростей в машинах и аппаратах, что в свою очередь указывает на то, что потребность промышлености в использовании электроэрозионных способов обработки будет только расти. Подтверждением данного факта является то, что данный вид обработки всё время развивается. За небольшой промежуток времени произошло значительное улучшение технико-экономических показателей электроэрозионных способов обработки - произошло повышение производительности, улучшения качества поверхности, возросла точность. Стойкость инструмента при этом значительно возросла, а энергоемкость процесса снизилась. Интенсивное развитие методов металлообработки с использованием электрического тока и ассимиляция их в самостоятельную отрасль электротехнологии началось после изобретения в 1943 г. Б. Р. и Н. И. Лазаренко электроискрового способа и В. Н. Гусевым - анодно-механического способа.
Эти способы были дополнены в 1948 г. новым применением электроконтактной обработки (заточка по методу инж. М. Е. Перлина),
Развитие электроискрового и анодно-механического методов проходило по вектору создания множественных, опытных конструкций приспособленных и специальных электроэрозионных станков, автоматических регуляторов и освоения новых технологических операций. Но производительность таких способов была слишком мала в результате чего было решено разработать новые аналоги данных видов обработки. Результатом разработок в данной отрасли стал электроимпульсный метод. Активное развитие электроимпульсный метод получил в 1951 г. Этот способ обработки при осуществлении прошивочно-копировальных работ позволил по сравнению с электроискровым способом повысить скорость удалена металла на максимальных режимах в 5-10 раз при наличии возможности ее дальнейшего увеличения, снизить износ инструмента в 5-20 раз и энергоемкость в 2-3 раза. Он обладает лучшими технико-экономическими показателями и более широкой областью применения, чем электроискровой. Основное применение данный способ получил в прошивочно-копировальных работах, представляющих наибольшую трудность для осуществления, но при этом более универсальные по технологическим возможностям.
Физические условия осуществления размерной электроэрозионной обработки
Для обеспечения высококачественной размерной обработки заготовок за счет использования энергии электрического тока нужно обеспечить соблюдение трёх важнейших условий.
- Энергия электрического тока должна поводиться в область обработки в виде импульса очень короткой продолжительности.
При непрерывающейся подаче импульсов снижается точность обработки, появляется дефектный слой, ухудшается качество поверхности и исчезает одно из важнейших технологических качеств электрической обработки.
- Зона обработки, к которой подводится импульс, должен быть очень мал.
Для быстрого снятия слоя металла с большого участка на обрабатываемой заготовке, нужно значительно повысить силу импульса, а это вызовет увеличение элементарного съема. При увеличении элементарного съема металла, ухудшается шероховатость и падает точность обработки.
- Импульсы должны подаваться к простым участкам металла, которые следует удалять, непрерывно и с высокой частотой. Что сделает процесс непрерывным и обеспечит стабильную обработку заготовки.
Разновидности электроэрозионной обработки металлов
Обработку металлов электричеством можно разделить на три группы:
Первая группа - основана на контактном подводе тока, её относят к электромеханической обработке.
Вследствие того, что контактный подвод тока не обеспечивает заданные размеры при обработке, а так же не достигается необходимый слой снимаемого металла. При электромеханическом способе удаление металла осуществляется резцом, режущая кромка которого является в то же время контактной поверхностью.
К обрабатываемой детали и резцу, которые являются электродами, подводят переменный ток, в месте контакта происходит нагрев заготовки. Такой нагрев необходим только для снижения усилий резания и таким образом его можно заменить на любой другой тепловой источник.
Как показывает практика, затрачивание энергии для нагрева поверхности заготовки при таком способе является нецелесообразным и не приводит к росту производительности и увеличения стойкости инструмента. Это объясняется тем, что для достижения хоть какого-либо значительного нагрева необходимо вводить сильные токи, а так же это приводит к тому, что режущая кромка резца нагревается более сильно, что приводит к значительному снижению стойкости инструмента.
При малых токах нагревание поверхности детали настолько незначительно, что практически не оказывает ни какого влияния на величину усилия резания.
Вторая группа - к ней можно отнести электроискровой и электроимпульсный методы и их промежуточные разновидности, примером таких способов могу быть, обработка апериодическими импульсами на релаксационном генераторе, такая обработка включает в себя элементы обоих способов.
Третья группа - объединяет диодно-механический и электроконтактный способы, они основаны на использовании комбинированного контактно-дугового подвода тока.
Классификация электроэрозионных методов обработки, по способам подвода энергии представлена в схеме 2.
Рисунок 2. Распределение методов обработки металлов по способам подвода энергии
В зависимости от того, какой из способов преобладает в какой-либо комбинации, можно сказать что это электроконтактная обработка с импульсным питанием или электроимпульсная обработка с вращающимся электродом. Это относится ко всем четырем комбинациям основных способов электроэрозионной обработки.
Разберем принципиальные отличия разновидностей размерной электроэрозионной обработки внутри второй и третьей групп.
Электроимпульсный и электроискровой способы отличаются конструкцией генераторов рабочих импульсов, основными параметрами импульсов и полярностью электродов.
Электроконтактный и диодно-механический в основном отличаются по виду применяемого тока и рабочей среды, в которой проходит процесс обработки.
В результате сравнения основных параметров этих способов, можно сделать вывод о том, что анодно-механический метод является более предпочтительным по сравнению с электроконтактным способом. При более простых условиях эксплуатации и простоте конструкции самой установки. Эти различия определяют и области их применения.
Вследствие вышеперечисленного эти электроэрозионные способы размерной обработки металлов имеют в основе единую физическую природу – слой металла удаляется путем термического действия электрического тока.
Основные отличия состоят в механизме удаления металла и в средствах технического обеспечения выполнения условий размерной электрообработки.
Сравнивая удельный расход энергии на снятие металла разными способами показывает, что наиболее энергозатратным способом является метод электрохимического растворения (3,85 квт-ч/кг), затем метод плавления (0,35 квт-ч/кг).
При механической обработке удельный расход энергии в значительной степени зависит от вида обработки.
Сопоставляя эти данные следует иметь в виду, что расход энергии для методов электрохимического растворения и плавления, мало зависит от механических свойств материалов из которых выполнены заготовки, хотя при механической обработке увеличение твердости обрабатываемого материала значительно повышает затраты энергии для протекания процесса резания. Однако необходимо отметить, что удельные фактические расходы в электрохимических и электроэрозионных установках значительно выше представленных данных вследствие потерь энергии, которые неизбежны при ее преобразовании в процессе обработки.
С энергетической точки зрения эти данные определяют целесообразность применения электроэрозионных методов для обработки токопроводящих материалов с высокой твердостью.
Учитывая свойства отображения (копирования), выполняемого на электроэрозионных станках по очень простой кинематической схеме, без силового привода, и возможности проведения ряда спецопераций, недостижимых при мехобработке, позволяет расширить область применения электроэрозионных методов на детали из легкообрабатываемых материалов, но обладающих сложной конфигурацией, делающую невозможной их механическую обработку.
Анализ способов подведения энергии электрического тока к инструменту и детали показывает, что для осуществления физического процесса удаления слоя металла необходимо специализированное оборудование – установка или станок, включающий в свою конструкцию такие элементы как: автоматический регулятор, генератор импульсов, систему снабжения рабочей среды.
Электротехнологические характеристики
Электоротехнологические характеристики электроэрозионных способов обработки позволяют определить по заданным размерам, конфигурации и материалу заготовки, какие режимы механической обработки и в какой последовательности необходимо применять для того, чтобы получить деталь с необходимыми размерами и чистотой обработанной поверхности, при этом машинное время будет минимально.[3] Электротехнологические характеристики при электрической обработке аналогичны режимам резания при механической обработке металлов.
Характеристики и области применения размерной электроэрозионной обработки
Рассмотрим основные характеристики и области технологического применения разновидностей электроэрозионной обработки металлов.
Приведённые данные по производительности, чистоте обработанной поверхности и энергоемкости процесса относятся к обработке различных по площади, на различных режимах обработки, определяющих отсутствие участков оплавления и покрытия, т. е. при оптимальных плотностях токов.
Электроискровой способ - скорость удаления слоя металла на высоких режимах обработки при работе со сталью составляет в среднем 600 мм3 /мин и близка к максимально возможной для данного способа обработки металлов. Удельный расход электрического тока на повышенных режимах составляет 20-50 квт-ч/кг диспергированного металла. Износ инструмента по отношению к объему снятого металла достигает 25-120 и более процентов. Чистота обработанной поверхности на минимальных режимах достигает 4-го класса (Нср= 25-30 мк) при скорости удаления 10-15 мм3 /мин. Последующее улучшение чистоты обработанной поверхности сопровождается значительным уменьшением скорости срезания слоя металла. Так, для получения поверхности 5-го класса чистоты (Нср = 16-19 мк), при электроискровом способе производительность обработки меньше 5 мм /мин. Удельное затрачивание энергии на минимальные режимы в десятки и даже сотни раз выше, чем на жесткие. При обработке твердых сплавов производительность процесса на минимальных режимах, приблизительно, в два с половиной раза ниже, чем при обработке сталей. Однако при этом достигается лучшая чистота обработанной поверхности. Применение более жестких режимов резания при обработке твердых сплавов ограничивается образованием на поверхности обрабатываемой заготовке трещин. Электроискровой способ - преимущественно применяется в настоящее время для прошивочных работ, изготовления полостей сложной конфигурации, а также для шлифования. Электроимпульсный метод имеет преимущества по сравнению с электроискровой. Улучшение различных характеристик этого способа обработки определено применением специальных независимых генераторов энергии.
Производительность на максимальных режимах электроимпульсного прошивочно-копировального станка КБ МСиИП с ламповым генератором превышает 5000 мм3 / мин, при этом чистота поверхности получается не достаточного класса. Указанная производительность может быть повышена на соответствующей площади до нескольких десятков сантиметров квадратных в минуту, при повышении мощности импульсов. Энергоемкость на максимальных режимах составляет 8-12 квт-ч/кг дисперги-ого металла, износ инструмента достигает 0,2 – 20 %. Чистота полученной поверхности, на данном станке на минимальных режимах, соответствует 4-му классу (Нср=25-30 мк). Последующее уменьшение режима обработки для улучшения качества поверхности приводит к увеличению энергоёмкости и уменьшению производительности. Рассмотренные технологические характеристики минимальных режимов возможно улучшить при применении современных генераторов, но вопрос о резком повышении производительности обработки на минимальных режимах нельзя считать решенной, но направления для решения этих проблем определены. Область преимущественного применения электроимпульсного способа та же, что и электроискрового, но, учитывая более высокие технико-экономические показатели, возможно более широкое его применение.
Примеры операций
Технологические операции, производство которых целесообразно на электроэрозионных станках. К таким операциям относят:
- изготовление отверстий малых диаметров – до 0,1мм;
- обработка твердосплавных пластин и заточка фасонных резцов;
- обработка стружколомающих канавок на пластинах резцов;
- удаление сломанного инструмента и крепежных деталей в корпусах и массивных деталях;
- производство сеток и щелей разной формы;
- обработка шаров для шарикоподшипников, притирка валиков, обработка сложных поверхностей, в том числе гребных винтов, обдирка чугунного литья.
Рассмотрим некоторые модели современных электроэрозионных станков и примеры отдельных технологических операций, которые могут быть на них осуществлены
Электроискровые станки
Универсальный прошивочно-копировальный электроискровой станок предназначен для изготовления электроискровым способом сквозных и глухих отверстий произвольной формы в любых токопроводящих материалах, преимущественно трудно обрабатываемых. На электроискровых станках можно прошивать отверстия, начиная с диаметра 0,1 мм, а в некоторых случаях и ниже, что механическим сверлением осуществить трудно. Полуавтомат для шлифования рабочего конуса распылителя. Станок предназначен для электроискрового шлифования и вывода эксцентричности рабочего конуса распылителя по отношению к посадочному цилиндрическому отверстию.
Электроимпульсные станки
Универсальный прошивочно-копировальный станок предназначен для получения и восстановления электроимпульсным методом ручьев штампов, прошивания отверстий любой формы, прессформ, обработки заготовок из трудно обрабатываемых токопроводящих материалов. Электроимпульсный мобильный станок предназначен для удаления сломанного инструмента и крепежа из массивных корпусных деталей, таких как станины станков, блоки двигателей, рамы металлоконструкций.
Специальный прошивочно-копировальный станок предназначен для изготовления большого количества ступенчатых щелей в ситах угольных центрифуг.
Заключение
В приведённой выше статье рассмотрено, чем электроимпульсный и электроискровой методы обработки твердых и легированных металлов преимущественно отличаются от других способов обработки аналогичных видов материалов. Анализируя современные потребности быстроразвивающихся отраслей современной экономики и жизнедеятельности человека, а также его интересы в познании суровых районов земного шара освоении ближнего и дальнего космоса позволило сделать вывод о том, что данные виды изменения и получения форм и размеров заготовок при изготовлении деталей для изделий в различных областях практически незаменимы.
