ИННОВАЦИОННЫЕ ТЕХНОЛОГИИ ДЛЯ УТИЛИЗАЦИИ SO2 ИЗ ОТХОДЯЩИХ ГАЗОВ МЕТАЛЛУРГИЧЕСКИХ ПРЕДПРИЯТИЙ
Конференция: CCIII Студенческая международная научно-практическая конференция «Молодежный научный форум»
Секция: Технические науки
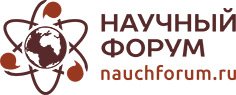
CCIII Студенческая международная научно-практическая конференция «Молодежный научный форум»
ИННОВАЦИОННЫЕ ТЕХНОЛОГИИ ДЛЯ УТИЛИЗАЦИИ SO2 ИЗ ОТХОДЯЩИХ ГАЗОВ МЕТАЛЛУРГИЧЕСКИХ ПРЕДПРИЯТИЙ
Аннотация. Утилизация отходящих газов на предприятиях цветной металлургии проводится с использованием старых технологий, направленных на получение серной кислоты. Такие технологии оправдывают себя при дальнейшем использовании "крепких" газов, с высоким содержанием SO2, таких как газы автогенных процессов и конвертирования. Переработка бедных газов восстановительных процессов требует значительных материальных затрат и усложняет технологию производства серной кислоты. Для таких газов в настоящей работе рассмотрена возможность использования раздельной их утилизации с использованием новых способов химической абсорбции карбонатным расплавом, с дальнейшей регенерацией карбонатно-сульфатного расплава с получением богатых по SO2 газов, пригодных для производства серной кислоты.
На основании металлургических расчетов материального баланса электроплавки сульфидных медных концентратов, применительно к условиям ЖМЗ, показана возможность глубокой очистки бедных по SO2 газов путем химической их абсорбции карбонатным расплавом щелочных металлов. Установлено, что при использовании данной технологии содержание SO2 в газах снижается с усредненных 2% до 0,02%. Извлечение серы в карбонатный расплав составляет ~97%.
Ключевые слова: электроплавка, материальный баланс, отходящие газы, очистка от SO2, химическая абсорбция, регенерация, серная кислота.
Введение
Загрязнение воздуха диоксидами серы является одной из наиболее серьезных проблем. Очистку отходящих газов от SO2 на многих металлургических заводах проводят пропусканием потока отходящего газа через известняк (CaCO3) или гашеную известь (Са(ОН)2). Эти методы не достаточно эффективны и обладают рядом недостатков [1, 2, 3]: высокое остаточное содержание серы в газах; процессы довольно дорогие; большой выход неиспользуемых твердых отходов (в основном, загрязненного примесями от сгорания угля, гипса - CaSO4), количество которых составляет несколько процентов от общей массы газов.
С учетом новых задач, поставленных перед промышленными предприятиями страны в «Стратегии «Казахстан-2050»: новый политический курс состоявшегося государства» [4], «Концепции по переходу страны к «зеленой» экономике» [5], очевидно практическое отставание в разработке мероприятий по защите окружающей среды и обеспечении экологической безопасности страны.
Разработка технологии по утилизации SO2 из отходящих газов полностью отвечает приоритетным направлениям научного, научно-технического и социально-экономического развития Республики Казахстан.
В работах [6, 7, 8] предложено высокоэффективное решение глубокой очистки отходящих газов ТЭЦ от SO2 (SO2 <0,003%) путем абсорбции SO2 расплавом карбонатов щелочных металлов. В работах [9, 10, 11] показано эффективное решение дальнейшей регенерации карбонатно-сульфатных расплавов путем его восстановления монооксидом углерода. Недостатком способа является дополнительное сжигание угля для получения СО. Применительно к очистке отходящих газов металлургических предприятий технология требует совершенствования.
На Жезказганском медеплавильном заводе (ЖМЗ) отходящие газы после электропечи содержат низкое содержание SO2 (1,5-3%) и после разбавления их с крепкими газами конвертирования, направляются на производство серной кислоты. Такая схема производства кислоты сопровождается большими затратами и усложняет общую технологическую схему производства серной кислоты. Температура отходящих газов из электропечи достаточно высока и составляет до 450 ºС. Отходящие газы, выбрасываемые в атмосферу, содержат от 1,5 до 3% SO2. Представляет интерес возможность глубокой очистки газов, получаемых после электропечи, способом химической абсорбции SO2 эвтектическим расплавом щелочных металлов.
Цель настоящей работы проведение оценки использования способа химической абсорбции газов эвтектическим расплавом щелочных металлов для очистки отходящих газов SO2, получаемых при электроплавке сульфидных медных концентратов.
Методы исследования
При выборе исходных данных для проведения материального баланса способа очистки отходящих газов от SO2 были учтены основные параметры, необходимые для проведения технологических расчетов.
Технологические расчеты сводились к составлению материального баланса электроплавки сульфидных медных концентратов в электропечи с определением распределения металлов и объема отходящих газов и содержания в них SO2, в условиях стабильной работы печи – плавка оптимального состава шихты.
При проведении расчетов использованы данные заводской практики ЖМЗ по составам исходных и получаемых продуктов электроплавки.
Металлургические расчеты проводились с использованием специальной программы, разработанной авторами настоящей работы.
Результаты и их обсуждение
Работа электропечи на ЖМЗ осуществляется от трех трансформаторов, мощностью ~ 17000 кВА каждый. Рабочая мощность печи – до 35 мВт. Производительность печи по твердой шихте – 50 т/ч. При электроплавке используются самообжигающиеся электроды диаметром 1200-1400 мм.
Сырьем для руднотермической плавки служит гранулированная медьсодержащая шихта, которая состоит из медного концентрата и известняка. В виде оборотного материала в шихту добавляют жидкий конвертерный шлак. Усредненные химические составы исходных продуктов плавки приведены в табл.1.
Таблица 1.
Химические составы исходных продуктов плавки
Наименование продуктов |
Содержание, % масс. |
|||||||
Cu |
Pb |
Zn |
Fe |
S |
SiO2 |
CaO |
Al2O3 |
|
Концентрат |
26-33 |
до 3 |
0,5-20 |
8-12 |
15-20 |
15-25 |
3-8 |
3-4 |
Известняк |
- |
- |
- |
0,4-1,2 |
- |
1,5-5,0 |
51-55 |
0,3-1,0 |
Конв. шлак |
3-10 |
2-7 |
2-5 |
27-32 |
- |
22-29 |
1,5-4,0 |
3-4 |
Первичный анализ результатов промышленных плавок – составов штейна и шлака показал, что получаемые продукты по составу варьируют незначительно и сохраняют тенденцию постоянства состава. Это свидетельствует о том, что процесс руднотермической плавки высоко оптимизирован за счет поддерживания постоянного состава исходной шихты; выбора оптимальных технологических параметров и режимов процесса, высокой организации труда и т.д.
Содержание серы в получаемых штейнах варьирует в пределах от 22 до 25%. Штейны электроплавки характеризуются высоким содержанием свинца, цинка и мышьяка и содержат, % (масс.): 40-50 Cu, 10-20 Fe, до 10 Pb, 4,0 Zn и 0,03-0,084 As.
Шлаки содержат повышенное содержание кремнезема, которое меняется в пределах от 40 до 55%. Содержание оксидов кальция и алюминия находится на уровне 18 и 7%, соответственно. Аналогично штейнам, шлаки содержат повышенные содержания свинца, мышьяка и цинка, %: до 0,5 Cu, 0,3-1,0 Pb и 0,1-0,12 As. Содержание цинка в шлаках находится на уровне 10%.
На основании математической обработки ежесуточных и средних ежемесячных данных химических составов реальных штейнов и шлаков рассчитан материальный баланс потоков и распределение металлов между исходными продуктами электроплавки. Общее количество массива, подвергнутого обработке, составило 208 точек (парные анализы составов штейнов и шлаков). Расчеты проведены на ЭВМ по специально разработанным программам. Полученные результаты приведены на рис.1 и 2.
Рисунок 1. Материальный баланс потоков электроплавки
Рисунок 2. Распределение металлов между исходными продуктами электроплавки
Нетрудно видеть, что исходная шихта электроплавки в основном представлена медным концентратом (68%) и конвертерным шлаком (30%).
Выход пылегазовой смеси незначителен и составляет 7%. Процесс электроплавки характеризуется значительным выходом шлаков 43%. Выход штейна – на уровне 50%.
Установлено, что доля меди, поступающего с конвертерным шлаком для доизвлечения, составляет ~10% от общего содержания меди в шихте. При этом с конверторным шлаком в исходную шихту поступает около 2 т свинца, что составляет порядка 70% от его общего содержания в исходной шихте. Из 100% мышьяка, поступающего с концентратом, 23% возвращается в шихту электроплавки.
Полученные результаты показывают, что значительное количество примесей - свинца и мышьяка, в исходную шихту вносятся с конвертерным шлаком. Циркуляция свинца и мышьяка в цепи «плавка – конвертирование» ведет к их накапливанию, что в конечном итоге значительно снижает качество продуктов, получаемых при электроплавке и конвертировании. Это подтверждается результатами по распределению меди, свинца и мышьяка между продуктами плавки, которые приведены на рис. 3.
Рисунок 3. Распределение металлов между полученными продуктами электроплавки
Небольшой выход пылегазовой смеси и установленное распределение меди, свинца и мышьяка между продуктами плавки указывают на то, что поведение свинца и мышьяка в процессе электроплавки, в основном, определяется их распределением между шлаком и штейном. Так, в результате расчетов установлено, что свинец при электроплавке концентрируется в штейне. До 30% свинца переходит в шлак, что формирует безвозвратные его потери.
Газоходный тракт электропечи состоит из вертикального газохода округлого сечения, установленного на своде со стороны шлакового торца, пылевой камеры, двух циклонов марки СИОТ-13, горизонтального и скоростного газоходов, двух дымососов (один рабочий, другой резервный) и колокольных затворов для перевода газа в электрофильтр. После электрофильтров газы поступают в сборный газоход.
В сборном газоходе газы электропечей смешиваются с газами конвертеров и по соединительному коллектору поступают на тонкую очистку в сухие электрофильтры, после чего, направляются на производство серной кислоты. Перевод электропечных газов в трубу осуществляется при достижении температуры газа 180°С и ниже.
При работе электропечи на мощности 20-26 МВт, объем газа, выходящего из печи колеблется в пределах 18-25 тыс. нм3/час. Газ на выходе из печи содержит 25-30 г/м3 пыли и частично обеспыливается в вертикальном газоходе. Последующая очистка газов от пыли до уровня пыли в них 5-6 г/м3 происходит в пылевой камере и циклонах.
Ниже на основании технологических расчетов показана возможность очистки отходящих газов электропечи от SO2 путем химической абсорбции эвтектическим расплавом щелочных металлов.
При расчетах использованы теоретические основы химической абсорбции SO2 из отходящих газов, подробно изложенные в работе [6, 7].
Данные принятые для расчетов приведены в табл.2.
Таблица 2.
Исходные данные, принятые для расчета химической абсорбции SO2 из отходящих газов электропечи карбонатным расплавом щелочных металлов
Наименование |
Показатели |
Температура отходящих газов, °С |
400 |
Состав отходящих газов, %: SO2 CO2 H2O O2 N2 |
2,18 4,59 1,74 20,33 71,16 |
Состав расплава щелочных металлов, %: Li2CO3 Na2CO3 K2CO3 |
43,5 31,5 25 |
α |
1 |
Результаты материального баланса химической абсорбции отходящих газов карбонатным расплавом приведены в табл.3.
Установлено, что для полной утилизации SO2 из отходящих газов потребуется 37,95 т карбонатного расплава. Содержание SO2 в отходящих газах, после химической абсорбции газов снижается с 2,18% до 0,02%. При этом обеспечивается высокое до 97% извлечение серы в карбонатный расплав. Очищенные газы после химической абсорбции выбрасываются в атмосферу.
Таблица 3.
Материальный баланс процесса химической абсорбции газов электропечи карбонатным расплавом щелочных металлов
Загружено |
т |
% |
Получено |
т |
% |
Отходящие газы |
100 |
72,49 |
Газы после процесса абсорбции |
98,83 |
71,64 |
в том числе: |
|
в том числе: |
|
|
|
SO2 |
2,18 |
|
SO2 |
0,02 |
|
CO2 |
4,59 |
|
CO2 |
4,59 |
|
H2O |
1,74 |
|
H2O |
1,74 |
|
О2 |
20,33 |
|
О2 |
21,32 |
|
N2 |
71,16 |
|
N2 |
71,16 |
|
Карбонатный расплав |
37,95 |
27,51 |
Карбонатно-сульфатный расплав |
39,12 |
28,36 |
в том числе: |
|
|
в том числе: |
|
|
Li2CO3 |
16,51 |
|
K2SO4 |
5,87 |
|
Na2CO3 |
11,95 |
|
Li2CO3 |
17,21 |
|
K2CO3 |
9,49 |
|
Na2CO3 |
16,04 |
|
Всего |
137,95 |
100 |
Всего |
137,95 |
100 |
Высокие температуры отходящих газов из электропечи (700 ºС) можно использовать для поддержания температуры карбонатного расплава щелочных металлов, что значительно снизит материальные затраты на осуществление процесса.
Полученный в результате химической абсорбции карбонатно-сульфатный расплав подвергается дальнейшей регенерации монооксидом углерода и/или природным газом с получением карбонатного расплава и крепких по содержанию SO2 газов [7, 8], которые можно использовать для производства серной кислоты.
Таким образом, предложенное в настоящей работе решение по очистке отходящих газов электропечи от SO2, при имеющемся на ЖМЗ специальном оборудовании для производства серной кислоты, легко может быть интегрирована в действующую технологическую схему, что значительно снизит затраты на производство серной кислоты.
Выводы:
- На основании расчета материального баланса электроплавки сульфидных медных концентратов применительно к условиям Жезказганского медеплавильного завода показана возможность использования технологии очистки отходящих газов электропечи от SO2 с использованием способа химической абсорбции газов эвтектическим расплавом карбонатов щелочных металлов.
- Показано, что в зависимости от характера и условий производственной деятельности электроплавки для решения задачи глубокой очистки отходящих газов электропечи от SO2 можно использовать способ химической абсорбции газов, который не потребует больших материальных затрат и может быть легко интегрирован в действующую технологическую схему завода для производства серной кислоты.
- Применение способа глубокой очистки отходящих газов от SO2 на ЖМЗ откроет широкие возможности для повышения экологической безопасности и технолого-экономической эффективности предприятия в целом.
Исследования проводились в рамках грантового финансирования Комитета науки Министерства науки и высшего образования Республики Казахстан на 2021-2023 годы по приоритетному направлению «Геология, добыча и переработка минерального и углеводородного сырья, новые материалы, технологии, безопасные изделия и конструкции» проекта № АР09259637 «Разработка высокоэффективной безотходной технологии для утилизации золы от сжигания угля с получением товарных продуктов».
