Разработка плана обслуживания: техническая деятельность на уровне эксплуатации
Конференция: LI Студенческая международная научно-практическая конференция «Молодежный научный форум»
Секция: Технические науки
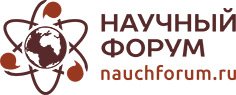
LI Студенческая международная научно-практическая конференция «Молодежный научный форум»
Разработка плана обслуживания: техническая деятельность на уровне эксплуатации
Аннотация. В данной статье основное внимание уделяется операционному уровню деятельности производственного предприятия и рассматривается возможность анализа режима сбоев и последствий (failure mode and effects analysis) [FMEA], который является центральным элементом решения, ориентированного на надежность (Reliability Centred Maintenance) [RCM], и решения проблемы периодического обслуживания (periodic maintenance problem) [PMP] для конкретного случая. FMEA предоставляет данные для PMP в контексте сбоев и узких мест в машинах и оборудовании. PMP использует методы оперативных исследований, чтобы найти оптимальный план обслуживания. Эта комбинация двух методов (RCM / FMEA и PMP) становится мощным инструментом для снижения общей стоимости обслуживания и уменьшения частоты отказов производственной линии. Линия по производству корпусов проверяется с использованием комбинации FMEA и PMP. Ключевые слова: стратегия обслуживания, FMEA, RCM, оптимизация обслуживания, математическое моделирование PMP.
1. ВВЕДЕНИЕ
В настоящее время производственные предприятия одной отрасли конкурируют, делая акцент на каждом аспекте предпринимательской деятельности. Высокий уровень автоматизации поддерживает усилия компании, чтобы быть на более высокой позиции по сравнению с другими. Эта так называемая современная автоматизация требует профессионального подхода к вопросам технического обслуживания машин. Деятельность, связанная с обслуживанием оборудования, становится все более очевидной и важной с точки зрения качества и производственных затрат. Это означает, что компании указывают на увеличение расходов на техническое обслуживание и обслуживающего персонала. В некоторых отраслях нередки случаи, когда отделы технического обслуживания и эксплуатации являются самыми крупными, и каждый из них составляет 30 процентов от общей рабочей силы. К сожалению, хотя методологии, разработанные для создания систем управления техобслуживанием, в основном являются ключевыми для оптимизации стратегии техобслуживания, они обычно не предлагают план действий для операционного уровня, и это часто является проблемой для инженеров. То есть многие методы учитывают планирование мероприятий по обслуживанию на производственном предприятии, просто слишком подчеркивая стратегию, которая обычно связана с управленческими обязанностями высшего и среднего звена. Это означает, что персонал на эксплуатационном уровне часто выполняет задачи по обслуживанию, которые являются слишком общими и вряд ли могут быть перенесены в план обслуживания. Недостаточно сформулировать стратегии, потому что для обеспечения работы интегрированной системы должна присутствовать приверженность руководства целям обслуживания. Однако главный недостаток методов технического обслуживания на оперативном уровне заключается в том, что они требуют вводной информации, которую трудно получить. Многие из этих (входных) факторов нелегко оценить из-за неопределенности, связанной с оценкой характеристик отказа/ремонта компонентов/узлов производственной системы. Взятые вместе эти соображения показывают, что:
• Большинство методов обслуживания предназначены для высшего руководства и поэтому имеют трудности с внедрением в производственную систему.
• Эти методы обслуживания для операционного уровня требуют ввода информации для составления плана обслуживания. Эта статья решает эти две проблемы и рассматривает возможность реализации комбинации двух методов на производственной линии кейса. В FMEA в качестве первого шага используется для выявления пробелов посредством анализа эффекта отказов в производственной линии корпуса и после оценки эти результаты переносятся в PMP. На втором этапе PMP, полностью основанный на математическом моделировании, решает задачи планирования с помощью исследования операций - результаты PMP представляют собой план технического обслуживания, которому необходимо следовать. Анализируется план технического обслуживания производственной линии для случая, как основного результата практической реализации двухэтапной комбинации методов, и проводится оценка возможных преимуществ плана технического обслуживания. Рассматривается целесообразность сочетания двух методов - RCM / FMEA и PMP для других или аналогичных производственных систем.
2. ТЕХНИЧЕСКОЕ ОБСЛУЖИВАНИЕ
Техническое обслуживание требуется для всех типов техники. Тип выполняемого обслуживания можно определить как профилактическое или корректирующее обслуживание. Профилактическое обслуживание проводится с заранее установленными интервалами или в соответствии с установленными критериями и предназначено для уменьшения вероятности отказа. Корректирующее обслуживание выполняется после сбоя и предназначено для ремонта системы. Другими словами, профилактическое обслуживание выполняется до сбоя, а корректирующее обслуживание - после сбоя. Все работы по техническому обслуживанию на производственных предприятиях можно разделить на шесть основных групп:
• модели оптимизации обслуживания
• методы обслуживания
• график технического обслуживания
• измерение эффективности обслуживания
• обслуживание информационных систем
• политика обслуживания
Первые три вида деятельности могут быть связаны с операционным уровнем производственного предприятия.
3. RCM / FMEA
Подход, основанный на надежном техническом обслуживании (RCM), может предоставить данные, необходимые в качестве входных данных для модели PMP. RCM - это метод создания эффективных стратегий обслуживания. Термин «техническое обслуживание, ориентированное на надежность» относится к программе планового технического обслуживания, предназначенной для реализации возможностей, присущих надежности оборудования. Одним из основополагающих предположений теории обслуживания всегда было наличие фундаментальной причинно-следственной связи между плановым обслуживанием и эксплуатационной надежностью. Методология анализа сбоев и эффектов (FMEA) использовалась в течение многих лет во многих различных отраслях промышленности, чтобы помочь аналитикам понять возможные варианты сбоев в проекте, а затем оценить риск, связанный с этими сбоями, и определить наиболее подходящие корректирующие действия. Тот же метод анализа является центральным компонентом методологии RCM, которая также доказала свою эффективность для разработки безопасных, надежных и экономически эффективных политик обслуживания оборудования. Процесс анализа RCM включает в себя выполнение режима отказа, эффектов и анализа (FMEA), выбор важных функций, а также оценку задач и выбор задач.
Результатом анализа FMEA является оборудование в производственной линии, наиболее типичные отказы отдельных машин и возможный эффект. Эти данные могут быть перенесены в PMP для планирования работ по обслуживанию.
4. ОБСУЖДЕНИЕ
Решение, найденное с помощью Excel Solver, можно считать оптимальным. Однако следует отметить, что такой подход, объединяющий два метода - FMEA и PMP, выявил несколько ограничений. Во-первых, реализация математического аппарата Excel Solver. Максимум переменных принятия решения равен 200, и это означает, что самая большая модель имеет 10 машин и 20 периодов планирования технического обслуживания. Однако есть более жесткое ограничение - Excel Solver пробует приблизительно 20000 комбинаций переменных решения за 1,6 часа для модели 6x8. По истечении этого времени моделирование останавливается и, следовательно, не достигает заданного времени поиска решения. Причина в том, что Солверу нужно гораздо больше ресурсов для целочисленных и двоичных задач. Эту точку зрения поддерживают разработчики Solver. Целочисленные переменные делают задачу оптимизации невыпуклой, и, следовательно, ее гораздо сложнее решить. Память и время решения могут увеличиваться экспоненциально по мере добавления большего числа целочисленных или двоичных переменных. Возможное решение в этом случае - перенести модель в Matlab или разработать собственное программное приложение.
5. ЗАКЛЮЧЕНИЕ
Комбинация двух методов подходит для производственной линии корпуса. Комбинация FMEA и PMP может быть легко интегрирована в производственную систему. FMEA может применяться к производственным системам любой сложности от одного компонента оборудования до отдельной машины и производственной линии. PMP может использоваться для планирования работ по техническому обслуживанию для различного числа машин и различных горизонтов планирования. Это означает, что комбинация FMEA и PMP может изменить свой масштаб. С другой стороны, практическая реализация PMP должна быть рассмотрена в будущих исследованиях и экспериментах. Разработка программного приложения может стать необходимым для дальнейших исследований. Процедуры испытаний на предприятии показывают, что комбинация методов подходит именно для операционного уровня производственной компании.
