Анализ методов построения размерных структур технологических процессов механической обработки
Конференция: IX Студенческая международная научно-практическая конференция «Молодежный научный форум»
Секция: Технические науки
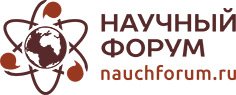
IX Студенческая международная научно-практическая конференция «Молодежный научный форум»
Анализ методов построения размерных структур технологических процессов механической обработки
Основными источниками для анализа методики построения оптимальной структуры технологических размерных цепей являются работы авторов: Мордвинова Б.С., Перминова А.В., Косоротовой Ю.Н.
Мордвинов Б.С.
Применение графов при проектировании геометрической структуры технологического процесса.
Графы служат не только для размерных расчётов, но могут быть использованы непосредственно для проектирования технологических процессов. Основное достоинство этого метода – возможность выявить допустимые варианты технологического процесса и выбрать наиболее рациональные. Здесь не ставится задача дать исчерпывающую методику проектирования, а только ознакомить с её основными принципами с тем, чтобы можно было их творчески применить к конкретным задачам проектирования и на этой основе построить геометрическую структуру технологического процесса.
Граф геометрической структуры представляет собой дерево. Это дерево соответствует составляющим звеньям размерных цепей. Замыкающие звенья (размеры чертежа, припуски) также описываются деревом. При совмещении этих двух деревьев возникает граф взаимосвязанных размерных цепей. Если в технологическом процессе изменит базы или последовательность обработки, то образуется новая геометрическая структура технологического процесса и иные по составу размерные цепи, следовательно, при проектировании технологического процесса нужно выбрать такие базы и такую последовательность обработки, чтобы на графе получить наиболее короткие размерные цепи. Но при уменьшении количества звеньев в одной цепи может возрасти их количество в других цепях, связанных с ней. Поэтому при проектировании технологического процесса возникает задача построить некоторую оптимальную геометрическую структуру. Оптимальной будем считать ту структуру, у которой по сравнению с другими возможными вариантами структур сумма ожидаемых погрешностей всех замыкающих звеньев – наименьшая. Если задачу упростить, приняв допуск всех составляющих звеньев равным единице, то минимальным должно быть общее количество составляющих звеньев во всех размерных цепях, возникающих при осуществлении технологического процесса.
Задача построения оптимальной геометрической структуры решается в несколько этапов.
1. Разработка плана операций и выделение в нём групп и рядов операции:
Рисунок 1. Группы операций
2. Выбор вариантов «чёрных» и «чистовых» баз:
Рисунок 2. Матрица баз
3. Минимизация (сужение) количества баз:
Рисунок 3. Суженная матрица
4. Поиск кратчайших путей, связывающих базы:
Рисунок 4. Геометрическая структура технологического процесса
5. Построение оптимальной геометрической структуры с учётом технологических и конструкторских ограничений:
Рисунок 5. Размеры чертежа и припуски
Перминов А.В.
Моделирование оптимальной размерной структуры технологических процессов механической обработки.
Рыночная экономика ставит перед предприятиями машиностроения две основные задачи: обеспечение качества изделия и конкурентоспособности производства. Это ведет к постоянному увеличению объемов и росту сложности проектных и конструкторских работ, связанных как с созданием самого изделия, так и с технической подготовкой его производства, которая и является в настоящее время наиболее трудоемкой частью проектирования. Таким образом, важнейшим средством интенсификации производства в машиностроении является автоматизация проектирования технологии, которая должна обеспечить автоматизацию инженерного труда как в рутинных, так и в творческих областях и значительно уменьшить время на подготовку производства. Автоматизация проектирования является инструментом решения задач на более высоком качественном уровне.
Были выведены критерии оптимальности размерных структур. Этими критериями являются структурный – минимальная сумма всех составляющих звеньев во всех размерных цепях размерной структуры (∑N) и экономический – минимальный объем снимаемого припуска (∑Q).
Так же была создана и описана математическая модель размерной структуры технологического процесса.
MRS={S(Ттрс),S(Тсп)}, (1)
Используя модель размерной структуры вновь создаваемого технологического процесса можно построить множество размерных структур. Если не учесть взаимодействия размеров, то большинство из них не сможет обеспечить необходимых свойств технологического процесса, они не будут адекватными.
Адекватной называется такая размерная структура, которая позволяет рассчитать все операционные технологические размеры и размеры исходной заготовки.
Ограничить количество вариантов размерных структур, исключив из рассмотрения неадекватные, позволяет матрица размерных цепей.
Рисунок 6. Матрица размерных цепей
Матрица размерных цепей разработана с учетом представления математической модели размерной структуры технологического процесса и позволяет наилучшим образом представить варианты размерной структуры. Она представляет собой запись в виде матрицы системы уравнений размерных цепей технологического процесса. Для решения матрицы размерных цепей введем понятие идеальной размерной структуры.
Любая размерная структура технологического процесса для деталей типа тел вращения может быть представлена в виде квадратной матрицы размерных цепей. Окончательно, если определитель матрицы размерных цепей не равен 0 (теорема Крамера), то размерная структура технологического процесса является адекватной.
При использовании матрицы размерных цепей также упрощается расчет сложных размерных цепей, поскольку можно использовать формулы Крамера для неизвестных звеньев.
На рисунке 7 представлен алгоритм оптимизации размерной структуры технологического процесса с помощью матрицы размерных цепей.
Рисунок 7. Блок-схема алгоритма
Косоротова Ю.Н.
Автоматизация выбора вариантов размерной структуры технологического процесса механической обработки при проектировании автоматической линии на стадии технического предложения.
При разработке технологического процесса механической обработки, реализуемого на автоматических линиях, на стадии технического предложения отсутствует необходимая информация о составе используемого оборудования, оснастки, транспортных средств и т. п. Избранные схемы базирования детали определяют ее положение в пространстве в разные моменты времени, стороны доступности обработке и в конечном счете конструкцию агрегатных станков.
Используемые комплекты технологических баз должны обеспечить оптимальную концентрацию переходов в каждой операции, следовательно, размерная структура технологического процесса должна очертить границы этой концентрации.
Избираемый вариант базирования должен обеспечивать: точность изготовляемой детали, возможность применения простых и удобных приспособлений, рациональное распределение припусков под обработку. Обеспечение требуемой чертежом точности готовой детали является главной целью технологического проектирования.
Она должна выступать в качестве основного ограничения выбора размерной структуры, отсеивающего недопустимые варианты.
Целесообразность использования тех или иных приспособлений ограничивает возможное разнообразие схем базирования, сужает область поиска приемлемого варианта и, следовательно, также выступает в роли ограничения.
В качестве критерия выбора варианта базирования в работе использована суммарная величина ожидаемых колебаний всех припусков под обработку, характеризующая их распределение. Рациональное распределение припусков обеспечивает:
· плотный однородный слой материала на поверхностях;
· равномерное распределение припуска на обработку на каждой отдельной поверхности;
· сокращение объема металла удаляемого при обработке.
Качество поверхностного слоя определяется величиной и равномерностью снимаемого с поверхности припуска, равной сумме погрешностей технологических размеров, входящих в размерную цепь данного припуска.
Сокращение величин колебаний припусков в партии деталей стабилизирует межпереходные размеры, что способствует повышению надежности работы автоматических обрабатывающих систем, позволяет вести обработку на режимах, близких к оптимальным (и, следовательно, увеличивать производительность оборудования), способствует уменьшению упругих и тепловых деформаций, что особенно важно при чистовой обработке.
В некоторых случаях (при обработке отверстий, пазов и т. п.) равномерность распределения припуска на поверхности является необходимым условием возможности проведения обработки.
Ограничение колебания припуска на обработку каждой такой поверхности становится равнозначным ограничениям на величины колебания конечных размеров детали, т. е. конструкторским допускам.
Объём удаляемого с обрабатываемой поверхности металла Qi (мм куб) определяется её площадью Si (мм кв) и величиной снимаемого припуска Zi(мкм). Величина припуска может варьироваться в пределах, определяемых ожидаемой величиной колебания припуска в партии деталей Pi.
При сравнимых величинах площадей обрабатываемых поверхностей можно считать:
∑SiPi→∑Pi=P→min (2)
Минимизация суммарной величины колебания припусков не даст достижимого минимума массы заготовки из-за разницы в площадях обрабатываемых поверхностей.
Полученные зависимости, принятые ограничения и сделанные в результате анализа размерной структуры выводы позволили определить последовательность необходимых действий при проектировании, представленную на рисунке 8.
Рисунок 8. Блок-схема алгоритма выбора вариантов структуры тех. процесса
Проведя анализ представленных источников делаем выводы:
1. Мордвинов Б.С. в своей методике используя теорию графов и матрицы баз формирует оптимальную геометрическую структуру технологического процесса. Основным критерием, по которому автор формирует оптимальную структуру, является оптимизация количества технологических баз. Недостаток методики состоит в том, что построение структуры осуществляется «ручным» способом, т. е. без применения ЭВМ Использование этого метода приводит к перебору большого количества вариантов структур, что занимает много времени.
2. Перминов А.В. использует наиболее современную методику проектирования размерных структур технологического процесса деталей типа тел вращения, которая полностью автоматизирована. Методика основывается на создании размерной структуры с минимально возможным количеством составляющих звеньев размерных цепей и минимальным объемом припуска. Недостаток заключается в том, что данная методика применима для типовых деталей. Для оригинальных необходима дополнительная разработка размерных структур.
3. Косоротова Ю.Н. в своей методике обеспечивает построение оптимальной размерной структуры технологического процесса минимальной суммой ожидаемых величин колебаний припусков и применением в расчетах Э.В.М.
4. Особенность методики состоит в том, что минимальная сумма ожидаемых величин колебаний припусков достигается наибольшим количеством составляющих звеньев в технологической цепи размера, заданного чертежом между технологическими базами.
5. Методика возможна к применению при обработке деталей с низкой точностью размеров и из дорогих материалов, где снятие припуска больше минимального нецелесообразно.
6. Недостаток методики – не учитывается ограничение «удобство измерения технологического размера». В расчетах используется Э.В.М., но исходные данные (методы обработки поверхности, технологический процесс, базирование) подготавливаются в «ручную».
