Содержание азота в стали при выплавке в конвертерном и электросталеплавильных цехах
Конференция: I Студенческая международная научно-практическая конференция «Молодежный научный форум»
Секция: Технические науки
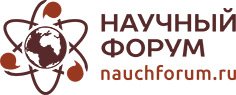
I Студенческая международная научно-практическая конференция «Молодежный научный форум»
Содержание азота в стали при выплавке в конвертерном и электросталеплавильных цехах
С развитием и совершенствованием технологий, к стали предъявляются все более жесткие требования, начиная от химического состава и заканчивая термической обработкой готового продукта. Сталеплавильный передел является одним из звеньев производственной цепи, обеспечивающим получение заданного химического состава.
Одним из важных аспектов в вопросе повышения качества стали является вопрос снижения газонасыщенности стали, в частности снижения содержания азота, особенно при выплавке особенно ответственного сортамента.
Негативное влияние азота проявляется в снижении пластических свойств стали, повышении хладноломкости и склонности стали к старению. Наиболее неблагоприятным считается выделение газов из раствора в газовую фазу. Выделение азота в отдельную фазу происходит в температурных областях существования феррита.
Оно сопровождается возникновением напряженности структуры металла и повышением его твердости и хрупкости[1]. Часто это приводит к разрушению металла. Выделение нитридной фазы при низких температурах происходит очень медленно, это явление и называют старением металла.
В металл азот вносится с шихтовыми материалами и поступает из атмосферы печи. Значительная часть азота в конвертерную ванну вносится с жидким чугуном[2]. Содержание азота в чугуне находится в пределах от 0,003 до 0,006 % (масс.).
Металлический лом представляет собой еще один источник азота, влияние которого необходимо учитывать при выплавке.
Увеличение его количества в металлошихте приводит к росту содержания азота в стали. Также азот вносится со шлакообразующими – известью, известняком и другими материалами. Большое влияние оказывает на содержание азота в стали частота дутья.
Было выявлено, что содержание азота в стали только увеличивается на каждом последующем переделе[3], поэтому необходимо достижение минимального содержания азота в шихтовых материалах. Изменение массовой доли азота на различных стадиях технологического процесса представлена на рисунке 1. Поэтому чистота шихтовых материалов является одним из важнейших факторов для получения требуемого содержания азота.
Рисунок 1. Динамика изменения массовой доли азота на различных стадиях технологического процесса
В зависимости от использования различного рода металлошихты в разных пропорциях, содержание азота может меняться. Поэтому путем варьирования количеством лома разной насыпной плотности, а также твердого чугуна можно добиться низких содержаний азота[4].
Изменения содержания азота в стали при увеличении доли различных видов металлошихты в завалке на 1 % представлены на рисунке 2.
Рисунок 2. Изменение содержания азота в стали при увеличении доли различных видов металлошихты(легковесного, среднего, тяжеловесного, твердого чугуна) в завалке на 1 %
Наиболее устойчивое и сильное влияние на содержание азота в полупродукте оказывает частота технического кислорода по азоту. На рисунке 3 показано влияние содержания азота в кислородном дутье на содержание его в металле перед выпуском из конвертера.
Рисунок 3 . Влияние содержание азота в кислородном дутье на содержание его в металле перед выпуском из конвертера
Удаление газа из металла происходит в процессе обезуглероживания за счет экстракции газов пузырьками СО. То есть, конечное содержание азота определяется соотношением двух процессов – поглощения и удаления газов.
Таким образом, во время продувки одновременно происходят два процесса – насыщение металла азотом в ограниченных объемах и удаление азота во всем объеме ванны пузырьками оксида углерода[5].
В начале продувки в конвертере содержание азота в чугуне близко в равновесной концентрации. Удаления азота идет слабо, так как расплав кипит слабо, не образуется пузырьков CO.
В середине продувки идет интенсивное окисление углерода, ванна кипит, коэффициент массопереноса увеличивается, поток из металла увеличивается. В конвертере содержание углерода выше, следовательно, образуется. большее количество пузырьков. Но в электропечи установлены горелки для вдувания кокса для науглероживания металла.
Концентрация азота снижается в течение всего времени продувки, достигает минимума при содержании углерода 0,08 – 0,12 % и снова возрастает к концу продувки. Осуществление продувки после снижения концентрации CO в отходящих газах ведет к насыщению металла азотом, что негативно сказывается на перспективах получения низкоазотистой стали. Содержание азота в конце продувки в значительной степени зависит от попадания атмосферного азота.
Влияние его сказывается лишь на величине прироста азота в металле в конце продувки. Также прирост в конце плавки зависит от чистоты дутья, от скорости обезуглероживания, а также от наличия промежуточных повалок при низком содержании азота.
На содержание азота определенное влияние оказывает дутьевой и шлаковый режимы плавки. В атмосфере рабочего пространства агрегатов всегда содержится азот, эжектируемый кислородной струей. Получение пенистых шлаков увеличивает степень экранирования электрических дуг и способствует снижению содержания азота в стали.
Также использование известняка в качестве шлакообразующего материала оказывает влияние на содержание азота перед выпуском. Реакция разложения приводит к интенсивному выделению диоксида углерода, что способствует выносу азота из металла пузырьками CO2.
В общем случае, содержание азота на выпуске из сталеплавильного агрегата больше, чем в электросталеплавильном процессе. Это связано с тем, что в электропечи в зоне электрических дуг идет интенсивное насыщение металла азотом. Это насыщение ускоряется в результате диссоциации молекул азота и водорода в зоне дуг. В связи с этим электросталь обычно содержит азота больше, чем конвертерная.
В таблице представлено содержание азота в полупродукте на выпуске из электропечи и конвертера ЧерМК ПАО «Северсталь».
Таблица
Содержание азота в полупродукте, выплавленном в электропечи и конвертере ЧерМК ПАО «Северсталь»
№ плавки |
Содержание азота в полупродукте, % |
|
Электропечь |
Конвертер |
|
1 |
0,0094 |
0,0051 |
2 |
0,0095 |
0,0058 |
3 |
0,0070 |
0,0054 |
4 |
0,0075 |
0,0063 |
5 |
0,0059 |
0,0049 |
6 |
0,0068 |
0,0055 |
7 |
0,0078 |
0,0058 |
Среднее |
0,0077±0,0011 |
0,0055±0,0004 |
Таким образом, для снижения концентрации азота в том и другом случае необходимо использование следующих методов:
-использование чистых по азоту шихтовых материалов;
-организация кипения ванны (удаление с пузырьками СО);
-предохранение металла от соприкосновения с азотосодержащей атмосферой в зоне очень высоких температур;
-использование для продувки кислорода, не содержащего примесей азота;
-связывание азота в прочные нитриды при введении в сталь нитридообразующих элементов
