Влияние различных факторов на прочностные свойства неофлюсованных окатышей
Секция: Технические науки
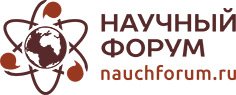
XL Студенческая международная заочная научно-практическая конференция «Молодежный научный форум: технические и математические науки»
Влияние различных факторов на прочностные свойства неофлюсованных окатышей
В настоящее время большое значение придается прочностным свойствам окатышей, так как окатыши после обжига претерпевают большое количество перегрузок до следующего металлургического передела. При транспортировке окатышей, а это происходит в большинстве случаев в металлургическом производстве, так как производство окатышей и производство черных металлов находятся на достаточно больших расстояниях, они разупрочняются [6,с.43].
Одним из факторов. Влияющим на прочностные свойства окатышей является фракционный состав шихты. Фракционный состав шихты немаловажный показатель, влияющий на прочность окатышей. Основным компонентом шихты железорудной части является концентрат, значительная часть которых являются сравнительно бедными. Так, содержание железа содержится в пределах 61,8–65,8%, а оксида кремния от 12,1 до 7,5% соответственно. На Лебединском горно-обогатительном комбинате для производства окатышей используется концентрат, содержащий 68,16% Feобщ и 4,73% SiO2. Представим массовую долю частиц в зависимости от изменения фракционного состава в таблице 1 [3, с. 351].
Таблица 1.
Физические характеристики шихтовых материалов для производства окатышей на Лебединском горно-обогатительном комбинате
Размер фракции |
Массовая доля частиц, %. фракцией (мм) |
||||
концентрат |
известняк |
доломитовый известняк |
доломит |
бентонит |
|
>0,315 |
- |
- |
- |
- |
- |
0,25-0,315 |
- |
- |
- |
- |
- |
0,15-0,25 |
0,5 |
- |
- |
- |
- |
0,10-0,15 |
0,7 |
0,1 |
- |
0,2 |
- |
0,074-0,10 |
2,0 |
1,1 |
0,1 |
0,8 |
- |
0,05-0,074 |
5,5 |
5,1 |
2,8 |
3,3 |
6,6 |
0,04-0,05 |
20,2 |
6,7 |
7,4 |
7,2 |
10,8 |
<0,04 |
71,1 |
87,0 |
89,7 |
88,5 |
82,6 |
В таблице 1 была представлена массовая доля частиц шихтовых материалов. Вариационный ряд размера фракций концентрата был представлен в восьми позициях, из которых: фракции размером <0,04 занимают в общем объеме 71,1%, 20,2% приходится на фракцию 0,04–0,05 и остальные 8,7% на фракции от 0,074 до 0,15 мм.
Следует заменить, что фракционный состав шихты во всем своем объеме имеет большую часть фракции <0,04 мм. Так процентный состав этой фракции известняка составляет 87%, доломитового известняка 89,7, доломита и бентонита 88,5 и 82,6 соответственно.
Содержание частиц железорудного концентрата фракции <0,05мм в железорудном концентрате ЦГОКа, СевГОК-3, ЛебГОКа не превышает 68,6–75,6%, а их удельная поверхность находится на уровне 150–155м2/кг [3, с.351].
Для сравнения представим данные (СевГОК-1,2; МихГОК, ОЭМК, КостГОК) концентраты на этих комбинатах содержат >85% частиц фракцией <0,04 мм при удельной поверхности 185–220 м2/кг. Важно акцентировать, что при одинаковом количестве фракции <0,05мм (91–94%) в концентратах на разных горно-обогатительных комбинатах удельная поверхность их существенно различается (от 153 до 202 м2/кг). При этом концентраты с низкой удельной поверхностью получают с использованием бесшаровой схемы измельчения [3, с. 349]. Следовательно, удельная поверхность концентрата, так же как и фракционный размер существенно влияет на качество сырых и обожженных окатышей.
Добавки в шихту могут тоже внести свой вклад в изменение прочностных свойств окатышей. В качестве добавок, улучшающих прочностные свойства окатышей, можно использовать обожженный возврат или твердое топливо. Установлено, что при вводе в шихту обожженного возврата снижается температура обжига и повышаются прочностные свойства обожженных окатышей в процессе их восстановления. При вводе в шихту для получения окатышей (~10 кг/т) твердого топлива температура обжига снижается на 40–80°С, уменьшается удельный расход природного газа и содержание мелочи в готовой продукции, температура начала плавления повышается на 105–125°С и на 100–110 °С сокращается температурный интервал плавления [3, с. 354].
Использование легкоплавких добавок предполагает упрочнение окатышей, а именно увеличение холодной прочности [9, с.10]. Установили, что как офлюсованные, так и неофлюсованные окатыши с добавкой легкоплавких силикатов (родусит, эгирин, зеленая слюда) уплотняются при обжиге в большей степени, чем с тугоплавкими силикатами (кварц, куммингтонит, хлорит) [1, с.127].
Таблица 2.
Химический состав силикатной связки неофлюсованных окатышей с разными минералами нерудной части концентрата
Силикаты нерудной части |
Массовая доля компонентов, % |
||||
Feобщ |
SiO2 |
MgO |
Na2O |
K2O |
|
Эгирин |
23±1,5 |
56±3,0 |
- |
10±4,0 |
- |
Родусит |
16±1,0 |
58±2,0 |
4,0±1,0 |
5±2,0 |
- |
Зеленая слюда |
18±1,0 |
63±3,0 |
4,7±1,0 |
0,2±0,1 |
9±1,5 |
Особенности поведения каждого из силикатов в процессе обжига влияют на металлургические свойства окатышей, что особенно четко выражено у неофлюсованных окатышей. Лучшие физико-механические свойства и прочность при восстановительно-тепловой обработке имеют неофлюсованные окатыши, в состав шихты которых введен эгирин, родусит, зеленая слюда. Значительно ниже проявляются эти свойства у окатышей из концентрата с силикатами в виде кварца, хлорита, куммингтонита и биотита (табл. 2), однако степень восстановления у окатышей с тугоплавкими силикатами выше. Это объясняется различиями в характере развития упрочняющей связки окатышей[1].
Для усиления прочностных свойств в шихту окатышей вводят связующие добавки. В качестве наиболее распространенных связующих используют бентонит, известняк, известь, доломит, Ca(OH)2, CaCl, MgCl2, Na2CO3, различные каучуки, резину гуар и т.д. [4, c.160].
Добавка бентонита увеличивает прочность окатышей в зонах сушки и обжига. Основными преимуществами применения бентонита являются: улучшает комкуемость, повышает прочность сырых окатышей, улучшает газопроницаемость при обжиге на колосниковой решетке, способствует уменьшению образования мелочи, уменьшает истирание [4; 5; 7; 8].
В последнее время пытаются найти замену бентонитовой глине, это связанно с отдаленностью мест зарождения бентонита, от мест расположения обогатительных фабрик, так же с относительно высокой стоимостью бентонитовых добавок [7, с.39].
В качестве заменителя бентонита исследовался леонардит. Леонардит – это субстанция, которая содержит большое количество гуминовых кислот, в которых под действием щелочей образуют гель. Этот гель выполняет роль связующего. В табл. 3 приведено влияние связующих на прочность окатышей.
Таблица 3.
Влияние связующих на прочность
Связующее |
Количество связующего, кг/т концентрата |
Конечная влажность, % |
Прочность при раздавливании Н/окатыш |
Бентонит |
0 |
8,5 |
9,22/8,43 |
3 |
8,24 |
11,57/36,48 |
|
5 |
9,39 |
9,22/55,21 |
|
8 |
10,08 |
11,96/68,35 |
|
Гуматы |
1,5 |
7,83 |
11,77/41,29 |
3 |
8,23 |
10,49/55,50 |
|
6 |
7,81 |
10,20/89,73 |
(Примечание: Во всех случаях определяли прочность окатышей по результатам трех сбрасываний с высоты 457мм. В числителе – прочность влажных, а в знаменателе – прочность сухих окатышей) [4, c164].
Связующие добавки должны обеспечивать не только прочность окатышей, но и достаточно высокую скорость их роста. Бентонит замедляет скорость роста комков шихты. Использованием гуматов напротив, можно увеличить вдвое скорость роста комков.
Следующим фактором, влияющим на прочностные характеристики окатышей является интенсификация работы оборудования. Достигается двумя путями: 1) улучшением конструкций машин или аппаратов; 2) совершенствованием технологических процессов в аппаратах данного вида.
Главными техническими путями интенсификации работы оборудования данного подвида будут: увеличение температуры, давления и концентраций реагирующих веществ в сочетании с применением катализаторов и перемешиванием реагирующих масс.
Хотя для увеличения скорости процессов важно, наоборот, уменьшение температуры, применение вакуума и уменьшение концентраций веществ. Далее следует, что в хим. технике пользуются спросом самые разные варианты тех. режима: температуры от абсолютного нуля до нескольких тысяч градусов; давления в производственных аппаратах бывают от абсолютного вакуума до нескольких тысяч атмосфер.
Зачастую возможность применить высокие температуры и давление ограничено стойкостью конструкционных материалов, из которых сделано оборудование, или разложением реагентов и, наконец, экономической эффективностью интенсифицирующих факторов. Следствием механизации, автоматизации и перехода процесса с периодического на непрерывный режим.
Рассмотрев основные факторы, влияющие на прочностные свойства окатышей, можно сказать, что нет единого ответа на вопрос какой из способов является самым действенным. Можно только сделать вывод, что все зависит от вида руды, предприятия, местонахождения завода, а также его финансовых возможностей.
