Разработка узла ввода модельных загрязнений в технологический цикл экспериментального стенда по регенерации отработанных масел
Конференция: XII Международная научно-практическая конференция «Научный форум: инновационная наука»
Секция: Технические науки
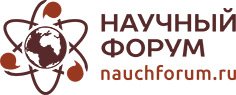
XII Международная научно-практическая конференция «Научный форум: инновационная наука»
Разработка узла ввода модельных загрязнений в технологический цикл экспериментального стенда по регенерации отработанных масел
Design of node for entering model impurities into the technological cycle of the experimental installation for the regeneration of used oils
Evgeniia Vylegzhanina
student, Bauman Moscow State Technical University - BMSTU, Russia, Moscow
Аннотация. В настоящее время активное внимание уделяется вопросам внедрения технологий по переработке отходов и их вторичному использованию. На базе лаборатории кафедры Э9 МГТУ им. Н.Э. Баумана разрабатывается стенд для исследования очистки от механических примесей вязких жидкостей, в частности отработанных моторных масел, способом гидродинамического фильтрования. Стенд спроектирован и установлен в лаборатории, однако осталось решить некоторые вопросы перед проведением экспериментов. В статье описывается предложенное решение одного из вопросов – способ ввода загрязнений в технологический цикл стенда.
Abstract. Currently, active attention is paid to the introduction of technologies for recycling. On the basis of the laboratory of the department of E9 BMSTU designs a installation for the study of cleaning of mechanical impurities of viscous liquids, in particular used motor oils, by the method of hydrodynamic filtering. The stand was designed and installed in the laboratory, but it remains to solve some issues before the experiments. The article describes the proposed solution of one of the questions - the way of introducing contaminants into the technological cycle of the stand.
Ключевые слова: регенерация; гидродинамическое фильтрование; струйный насос; ввод загрязнений; очистка масел; экспериментальный стенд.
Keywords: regeneration; hydrodynamic filtration; jet pump; input pollution; cleaning of oils; experimental stand.
Нефтяные масла находят широкое и разнообразное применение при эксплуатации современной техники. Каждый год увеличиваются объемы потребления смазочных материалов и, как следствие, объемы отработанных масел непрерывно растут. Масла и нефтепродукты в значительных концентрациях содержатся в ливневых, промышленно-ливневых и производственных сточных водах многих предприятий. Проблема очистки усугубляется наличием в этих водах дополнительных загрязнителей: значительных концентраций взвешенных веществ, нередко тяжелых металлов, фенолов и др. Высокая опасность этих загрязнителей для окружающей среды обусловливает очень жесткие требования к их содержанию в сточной воде, сбрасываемой в городские коллектора и напрямую в поверхностные водоемы.
Отработанные нефтепродукты токсичны, имеют невысокую степень биоразлагаемости (10-30%) и являются опасными отходами, которые подлежат обязательному сбору и утилизации. Однако, 26-77 % всех отработанных масел нелегально сбрасывается на почву и в водоемы; 40-48% – собирается, но из собранных отработанных масел только 14‑15% идет на очистку, а остальные 26-33% используются как топливо или сжигаются [2].
Актуальность и важность данной проблемы отражена в статье 22 Федерального закона от 30.03.1999 № 52-ФЗ «О санитарно-эпидемиологическом благополучии населения», отходы производства и потребления подлежат сбору, использованию, обезвреживанию, транспортировке, хранению и захоронению, условия и способы которых должны быть безопасными для здоровья населения и среды обитания. Основной документ, регулирующий передачу отработанного масла на переработку и утилизацию – это ГОСТ 21046-86 «Нефтепродукты отработанные. Общие технические условия». Также, согласно Федеральному закону от 29.12.2014 N 458-ФЗ (ред. от 29.12.2015) "О внесении изменений в Федеральный закон "Об отходах производства и потребления", все производители и импортеры минеральных и синтетических масел и смазочных материалов в России обязаны производить переработку отходов производства масел и смазочных материалов. Компании получили альтернативу выбора финансовой ответственности: самостоятельная утилизация отходов или уплата экологического сбора.
Создание и внедрение экологически безопасных технологий представляет одну из главных тенденций повышения эффективности мирового производства и формирование предпосылок перехода современной цивилизации к устойчивому развитию. Особое внимание уделяется разработке и внедрению ресурсосберегающих технологий, позволяющих безопасно для природы перерабатывать промышленные и бытовые отходы.
Безусловно данная актуальная проблема не могла быть не рассмотрена в научных и опытно-конструкторских работах кафедры Э9 «Экология и промышленная безопасность» МГТУ им. Баумана, одного из ведущих Российских и Международных институтов, рассматривающих техносферную безопасность в целом.
Как одно из направлений исследований была выбрана проблема очистки моторных масел от механических примесей и возвращение восстановленных масел в технологические процессы промышленности. В результате анализа и оценок существующих методов очистки нефтесодержащих вод, сотрудниками кафедры Э9 был отобран наиболее эффективный и наименее ресурсоемким метод - гидродинамическое фильтрование (далее ГДФ).
В основу очистки жидкостей ГДФ положена гидродинамическая теория З.Л. Финкельштейна о движении частиц примесей в потоке жидкости вблизи ФЭ [5]. При традиционной схеме очистки поток загрязненной жидкости направляется перпендикулярно плоскости ФЭ. Через него проходят те частицы, линейные размеры которых меньше размера фильтрующей ячейки. Частицы большего размера задерживаются и накапливаются со стороны падающего потока и постепенно «закупоривают» отверстия ФЭ. Поэтому при работе ФЭ в потоке загрязненной жидкости уменьшается его пропускная способность, повышается перепад давления на нем, а в конечном итоге он загрязняется и теряет работоспособность. После этого необходимо переводить забившийся ФЭ в исходное состояние путем замены либо эффективной промывки, которая определяется типом фильтра и характером задерживаемых им веществ. В схеме, предложенной З.Л. Филькенштейном, поток подается параллельно оси ФЭ, что предотвращает налипание загрязнений на ФЭ и увеличивает ресурс работы фильтра [6].
В настоящее время сотрудники кафедры Э9 с привлечением молодых бакалавров и магистров решают проблемы и вопросы, возникающие при моделировании метода ГДФ на экспериментальном стенде по регенерации отработанных масел [2]. Одной из таких проблем является создание модельной жидкости, имитирующей загрязнённые масла с механическими примесями и ввод этой жидкости в технологический цикл установки.
Для исследования процесса фильтрования в рабочую среду ГДФ необходимо вводить искусственные загрязнения. В качестве таких загрязнений были выбраны шлифовальные порошки искусственных и природных материалов, предназначенные для изготовления абразивных инструментов. Материалами шлифпорошков являются карбид бора; карбид кремния и электрокорунд. Фракционный состав материалов устанавливается ситовым, микроскопическим и комбинированными методами в зависимости от максимального размера крупной фракции.
При проведении первых испытаний модельный раствор загрязнённой среды смешивался в отдельной ёмкости и подавался к ГДФ обычным шестерёнчатым насосом. Однако для проведения широкомасштабного эксперимента такой метод не подходит, т. к. такой насос не предназначен для перекачивания загрязнённых жидкостей.
Было теоретически подтверждено, что ввод механических загрязнений с помощью струйного насоса имеет ряд преимуществ: отсутствие энергозатрат и механического износа механизмов, малые габариты вновь сконструированного блока для ввода примесей, высокую точность дозирования загрязнений.
Реализовать узел ввода модельных загрязнений предложено выполнить следующим образом: В отдельном баке имеется чистое моторное масло, которое подаётся в систему трубопроводов шестерёнчатым насосом. В другом баке готовится модельный концентрат, состоящий из воды и твёрдой фракции модельных загрязнений. При помощи проектируемого струйного насоса две жидкости смешиваются и подаются к ГДФ, где уже проводится эксперимент по очистке подготовленной жидкости от механических примесей.
Для проектирования струйного насоса был проведён расчёт основных параметров жидкостей, предлагаемых для применения в качестве модельной загрязнённой жидкости. Далее, по полученным исходным данным был выполнен расчёт гидравлических характеристик проектируемого насоса. По приведённой методике и рассчитанным величинам были получены все данные, необходимые для выполнения рабочих чертежей струйного насоса [1,4]. На рисунке представлен сборочный чертеж разработанного насоса.
Рисунок. Сборочный чертёж струйного насоса
1 – входной фланец с внутренней резьбой, 2 – фланец рабочего сопла, 3,4 – болт с контргайкой, 5 – набор уплотнительных прокладок,6 - фланец рабочей камеры со внутренней резьбой, 7 – рабочее сопло, 8 – рабочая камера, 9 – набор уплотнительных прокладок, 10 – трубопровод, 11 – камера смешения, 12 – фланец трубопровода, 13 – втулка коническая с внешней резьбой, 14 – гайка накидная системы трубопроводов установки
Работа узла построена следующим образом: насос крепится к имеющимся трубопроводам стенда фланцем входным 1 с внутренней резьбой и втулкой конической 13, имеющей внешнюю резьбу. По трубопроводу стенда рабочая жидкость, представляющая собой чистое моторное масло с плотностью ρ = 900 ( поступает через рабочее сопло 7 в рабочую камеру 8, где смешивается с жидкостью модельного загрязнения, инжектируемой через трубопровод 10 из бака для модельных загрязнений экспериментального стенда. Модельные загрязнения было принято готовить из смеси порошка карбида кремния с водой. Выбранная смесь будет иметь плотность ρ=1200 ( . Расходы жидкостей были подобраны таким образом, чтобы при смешении получалось масло, с массовой концентрацией механических примесей не более 1 %, так как большая концентрация недопустима по ГОСТу для отработанных масел [7]. После прохождения рабочей камеры, рабочий поток чистого масла и инжектируемый поток концентрата загрязнений попадают в камеру смешения 11 и через втулку коническую 13 попадают в систему трубопроводов стенда.
Конструкция спроектированного струйного насоса учитывает необходимость проведения экспериментов с изменением исследуемых параметров. Поэтому все основные части насоса являются разборными (с фланцевыми или резьбовыми соединениями), что позволит при необходимости заменить один из элементов насоса. Так же на входных и выходном участках предусмотрено резьбовое соединение, что позволяет быстро устанавливать насос в существующую систему трубопроводов, а также при необходимости заменить узел полностью.
Всестороннее исследование процесса фильтрования методом ГДФ возможно позволит усовершенствовать существующие фильтровальные установки, что в свою очередь позволит снизить себестоимость вторичного использования нефтепродуктов и тем самым снизить количество не возобновляемых отходов.
