ПРОБЛЕМА ЗАЛИПАНИЯ ПОКОВОК ПОСЛЕ ГОРЯЧЕЙ ОБЪЕМНОЙ ШТАМПОВКИ И ПУТИ ЕЕ РЕШЕНИЯ С ПОМОЩЬЮ CAD/CAE-СИСТЕМЫ
Конференция: LXVII Международная научно-практическая конференция «Научный форум: технические и физико-математические науки»
Секция: Машиностроение и машиноведение
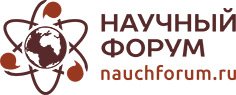
LXVII Международная научно-практическая конференция «Научный форум: технические и физико-математические науки»
ПРОБЛЕМА ЗАЛИПАНИЯ ПОКОВОК ПОСЛЕ ГОРЯЧЕЙ ОБЪЕМНОЙ ШТАМПОВКИ И ПУТИ ЕЕ РЕШЕНИЯ С ПОМОЩЬЮ CAD/CAE-СИСТЕМЫ
THE PROBLEM OF FORGINGS STICKING AFTER HOT VOLUMETRIC STAMPING AND WAYS TO SOLVE IT USING A CAD/CAE SYSTEM
Egor Markelov
Leading engineer-technologist, JSC NPO Lavochkina, Russia, Khimki
Vladimir Goncharov
Leading engineer-technologist, JSC NPO Lavochkina, Russia, Khimki
Аннотация. В работе показана проблема залипания поковок в штампе и предложены варианты ее решения с помощью моделирования в CAD/CAE-системе технологического процесса горячей объемной штамповки. Схватывание заготовок в штампе при повышенных температурах разупрочняет его, снижая ресурс работы оснастки.
Abstract. The paper shows the problem of sticking forgings in a die and offers solutions to it using modeling in a CAD/CAE system of the technological process of hot volumetric stamping. The setting of the blanks in the die at elevated temperatures softens it, reducing the service life of the tooling.
Ключевые слова: Обработка металлов давлением; ковка; штамповка; поковка; моделирование; CAD/CAE-система; QForm.
Keywords: Metal forming; forging; stamping; modeling; CAD/CAE-system; QForm.
В настоящее время моделирование технологических процессов горячей штамповки с помощью специализированных CAD/CAE-систем позволяет с достаточной точностью прогнозировать результаты деформирования, значительно снизить расходы и сократить сроки выпуска готовой продукции предприятия.
В машиностроительной отрасли детали должны обладать высокой стойкостью к динамическим, вибропрочностным, ударным, акустическим, циклическим нагрузкам при повышенных (пониженных) температурах. Поэтому метод анализа распределения механических характеристик поковок основных деталей узлов и отсеков конструкции, спрогнозированных в CAE-системе, позволяет повысить качество деталей машин.
Лидерами на рынке и зарекомендовавшими себя наилучшим образом среди CAE-систем, моделирующих процесс горячей штамповки, являются: импортные продукты Deform и Ansys/ls dyna, отечественный продукт QForm и др. Данные системы выполняют математическое моделирование процессов с использованием метода конечных элементов, который позволяет визуализировать результаты расчетов и произвести оценку основных параметров техпроцесса.
Цель работы:
- осуществить моделирование техпроцесса горячей объемной штамповки (ГОШ) на примере детали «Ресивер» из коррозионно-стойкой стали 12Х18Н10Т;
- спрогнозировать значения температурного поля поковки непосредственно в процессе ГОШ;
- оптимизировать технологический процесс ГОШ деталей.
Исследования проводили на заготовках, изготовленных из нержавеющей стали 12Х18Н10Т. Моделирование осуществлялось при помощи CAD/CAE-систем: NX, QForm. Обработка металла давлением полуфабрикатов осуществлялась паровоздушными молотами следующих моделей: МА2143, М134А. Испытания на растяжение образцов из заготовок проводили на разрывных машинах типа Р-5; неразрушающий контроль поковок производился промышленным компьютерным томографом V|tome|x m 300 General Electric [1, 2]. Термическая обработка образцов из заготовок проводилась в нагревательных печах ЭЦЭП.
Производственный брак в АО «НПО Лавочкина» стал причиной, подтолкнувшей к идее использования 3D-моделирования технологического процесса горячей объемной штамповки из стали 12Х18Н10Т для детали «Ресивер» (рисунок 1, а) в технологии предприятия [3,4], основными этапами которого являются:
- ковка при максимальной температуре нагрева 1170 °С (осадка в нижней части штампа);
- горячая объемная штамповка полуфабриката при максимальной температуре нагрева 1170 °С;
- смягчающая обработка (закалка) при температуре 1050 °С для улучшения обрабатываемости резанием и повышения коррозионной стойкости.
а) б)
а – деталь после механической обработки; б – поковка
Рисунок 1. Ресивер из коррозионно-стойкой стали 12Х18Н10Т
После двух переходов ГОШ на молоте 30 кН (3 тс) получается поковка детали «Ресивер» (рисунок 1, б).
В результате окончания ГОШ часто готовая поковка залипает в верхней части штампа. Это особенно опасно для работы штампа, так как количество теплоты, поступающее в штамп, возрастает с увеличением времени контакта заготовки со штампом. При кратковременном нагреве тонкого поверхностного слоя штампа (даже от 900 °С до 980 °С) не успевают произойти структурные изменения в штамповой стали и штамп сохраняет исходную твердость. При залипании поковки в ручье продолжительность теплового воздействия на штамп увеличивается в десятки раз [5], что приводит к постепенным структурным превращениям и уменьшению твердости металла штампа. Штамп в нашем случае изготовлен из стали 5ХНМ. Рекомендуемые условия работы данной стали от 400 °С до 450 °С. Распределение температур в процессе ГОШ показана на рисунке 2. Видно, что через 34 с рабочего процесса, когда штамп будет контактировать с деталью, она нагреется до 498 °С. Кратковременно такой режим работы допускается, но при залипании, которое длится несколько часов, происходит разупрочнение инструмента.
Рисунок 2. Температурная модель процесса ГОШ, созданная в QForm
Было выдвинуто два предположения залипания поковок при ГОШ:
- возможно в процессе ГОШ температурное поле штампуемой заготовки выходит за границы интервала ковки. Поэтому необходимо спрогнозировать значения температурного поля поковки;
- из-за неоднородности температурного поля заготовки и, следовательно, неравномерности деформации могут возникнуть участки сухого трения в результате чего произойдет схватывание металла поковки с материалом штампа. Это особенно характерно для таких технологических процессов, в которых наблюдается интенсивное скольжение деформируемого металла по инструменту. Увеличение деформации, повышающее усилие деформирования и гидростатическое давление, в значительной степени способствует схватыванию. Поэтому необходимо проанализировать усилие деформирования в технологическом процессе.
Этап освоения и внедрения технологии является самым затратным при традиционном подходе и включает в себя: выбор размеров и формы заготовки, анализ получаемых дефектов, корректировку оснастки и другие непредвиденные затраты. Использование CAE-системы приводит к увеличению продолжительности этапа проектирования, но убирает этап освоения и внедрения технологии, что позволяет достигнуть положительного экономического эффекта.
Для изучения причин залипания поковки была произведена имитация действующего технологического процесса горячей объемной штамповки за счет применения результатов 3D-моделирования в CAE-системе. Данный метод изучения технологического процесса хорошо зарекомендовал себя в работах [6–8]. Результат этого моделирования представлен на рисунке 3. Видно, что осаженный пруток подвергается ГОШ со следующими параметрами: время деформирования 5,7 мс; пластическая деформация от 0 до 4,6; усилие деформирования от 0 до 8,21 МН. Причем наиболее сильное увеличение деформации требуется после 3 мс.
а)
б)
в)
г)
а – моделирование ковки прутка (первый переход) в QForm; б – начало ГОШ в QForm; в – поковка после окончательного второго перехода в QForm; г – график зависимости усилия деформирования молотом от времени штамповки
Рисунок 3. Технология получения поковки на предприятии для детали «Ресивер» из стали 12Х18Н10Т
Для исключения схватывания поковки со штампом был предложен оптимизированный технологический процесс изготовления детали «Ресивер»:
- горячая объемная штамповка полуфабриката при максимальной температуре нагрева 960 °С (рисунок 4);
- смягчающая обработка (закалка) при температуре 1050 °С для улучшения обрабатываемости резанием и повышения коррозионной стойкости.
а)
б)
в)
а – начало ГОШ в QForm; б – поковка после ГОШ в QForm; в – график зависимости усилия деформирования молотом от времени штамповки
Рисунок 4. Оптимизированная технология получения поковки без залипания для детали «Ресивер» из стали 12Х18Н10Т
В отличии от действующей технологии при одинаковых исходных данных (конфигурация штампа и размеры прутка не меняются) в новом процессе была исключена осадка прутка в нижней части штампа и процесс ГОШ производится за одну операцию. Это исключило повторные нагревы полуфабриката и, следовательно, сократило время штамповки.
Из рисунка 4 видно, что время деформирования 11 мс; пластическая деформация от 0 до 5; усилие деформирования от 0 до 6,52 МН. Причем наиболее сильное увеличение деформации требуется после 8 мс. Снижение усилия деформирования, понижающее гидростатическое давление, в улучшенном технологическом процессе предотвратило залипание, что было подтверждено опытными работами. Уменьшение температуры нагрева ГОШ с 1170 °С до 960 °С было связано с анализом температурного поля поковки в QForm (рисунок 5), из которого видно, что в предыдущей технологии всего 3 °С не хватает для превышения температурного интервала ковки (температурные параметры ковки в [9] от 1200 °С до 850 °С). Достижение граничных значений температур из интервала ковки не желательно, так как при нижних значениях возрастает усилие деформирования, а при верхних, из-за повышенных температур, снижается ресурс инструмента и печей.
Рисунок 5. Модель температурного поля поковки в QForm
Механические свойства оптимизированных штамповок представлены в таблице 1. Исследование поковок методом компьютерной томографии не выявило появление неустранимых дефектов в виде несплошностей (рисунок 6).
Рисунок 6. Томографический снимок вида сбоку (right 1)
Таблица 1.
Механические свойства детали «Ресивер» из стали 12Х18Н10Т
Способ получения штамповки |
Механические свойства после смягчающей обработки |
||||
Направление вырезки образца |
Предел прочнос-ти σв, МПа |
Предел текучести σ02, МПа |
Относительное удлинение ε, % |
Относительное сужение ψ, % |
|
по технологии предприятия |
осевое |
548 |
273–292 |
50,8–51,6 |
76,7–78,6 |
радиальное |
554–556 |
278–298 |
53,2–54,4 |
74,9–78,8 |
|
по оптимизированной технологии |
осевое |
556 |
273-277 |
50,0-51,2 |
77,1-79,0 |
радиальное |
562 |
277-279 |
45,2-48,8 |
61,9-64,3 |
ЗАКЛЮЧЕНИЕ
1. В оптимизированной технологии ГОШ отсутствует залипание (схватывание) поковки с элементами штампа, так как металл течет более равномерно во всех направлениях благодаря правильно подобранной оптимальной силе удара (меньшей, чем в технологии предприятия) штамповочного молота, из-за чего снижается вероятность возникновения сухого трения и уменьшается гидростатическое давление на ручей штампа.
2. CAE-системы являются эффективным инструментом прогнозирования основных характеристик процесса горячей штамповки, что позволяет снизить расходы и сократить время на разработку техпроцесса штамповки за счет сокращения этапа освоения технологии.
