МЕТОДЫ УСТРАНЕНИЯ НЕИСПРАВНОСТЕЙ В КОНСТРУКЦИИ И ЭКСПЛУАТАЦИИ АВТОСЦЕПНЫХ УСТРОЙСТВ
Конференция: LXXXIII Международная научно-практическая конференция «Научный форум: технические и физико-математические науки»
Секция: Транспорт
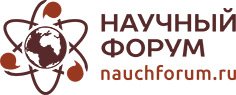
LXXXIII Международная научно-практическая конференция «Научный форум: технические и физико-математические науки»
МЕТОДЫ УСТРАНЕНИЯ НЕИСПРАВНОСТЕЙ В КОНСТРУКЦИИ И ЭКСПЛУАТАЦИИ АВТОСЦЕПНЫХ УСТРОЙСТВ
Несмотря на прочность и надежность конструкции, автосцепное устройство вагонов подвержено различным неисправностям, возникающим в процессе эксплуатации. Постоянные динамические нагрузки, механический износ, неблагоприятные погодные условия и ошибки при эксплуатации могут приводить к сбоям в работе сцепного механизма. Нарушение нормального функционирования автосцепки способно вызвать задержки в движении поездов, увеличение нагрузки на другие элементы подвижного состава и, в худших случаях, аварийные ситуации.
Неисправности автосцепного устройства можно разделить на несколько основных видов. Они включают механические повреждения корпуса и замковых механизмов, износ и поломку поглощающего аппарата, заедание сцепных узлов, а также нарушение фиксации сцепки в рабочем положении. Каждый из этих видов неисправностей требует своевременного выявления и устранения, поскольку даже незначительные отклонения в работе автосцепки могут привести к серьезным последствиям. Рассмотрим подробнее основные виды неисправностей, их причины и способы устранения.
Согласно данным, представленным на «Информационном сайте о железнодорожных вагонах: конструкция, устройство, расчет» [1], наиболее частыми причинами отказов автосцепок являются износ деталей, деформация и разрушение элементов, нарушение технологии изготовления и ремонта, а также воздействие климатических условий. Продолжительная эксплуатация приводит к истиранию ключевых элементов, таких как замкодержатель и тяговый хомут, что может ослабить сцепку и привести к саморасцепам. Высокие динамические нагрузки, возникающие при трогании поезда, торможении и маневрах, приводят к появлению трещин и разрушению отдельных частей автосцепки. Дефекты, возникшие в процессе производства или восстановления деталей, могут значительно сократить срок службы устройства. Резкие перепады температур, повышенная влажность и попадание абразивных частиц (песка, пыли) способствуют ускоренному износу механизмов.Исследования, проведенные на того же сайта[1], показали, что наиболее часто встречающимися причинами отказов автосцепных устройств являются износ и деформация ключевых компонентов, нарушения в процессе ремонта и монтажа, влияние внешних факторов и неправильная эксплуатация. Длительная эксплуатация приводит к значительному износу шипов, замкодержателей и других элементов, что ослабляет сцепление и может привести к саморасцепу. Внедрение современных материалов, улучшенных конструкций и регулярного контроля технического состояния автосцепного устройства способствует значительному снижению частоты отказов и повышению безопасности перевозок.
Отказы автосцепного устройства могут быть вызваны различными причинами, связанными как с эксплуатационными факторами, так и с конструктивными особенностями. Основные причины отказов включают естественный износ деталей, механические повреждения, нарушения в эксплуатации, а также заводские дефекты.
Одним из наиболее распространенных факторов, влияющих на частоту отказов, является износ элементов автосцепки, таких как замковый механизм, поглощающий аппарат и сцепные поверхности. Постоянные динамические нагрузки, удары при сцепке и торможении, а также воздействие климатических условий (перепады температур, влага, коррозия) ускоряют процесс износа.
Еще одним фактором является недостаточное техническое обслуживание. Несвоевременная диагностика и замена изношенных деталей могут привести к их внезапному выходу из строя в процессе движения. Влияние оказывают и производственные дефекты, такие как неточные размеры деталей или низкое качество материалов, что сокращает срок службы автосцепного устройства.
Таким образом, частота отказов автосцепки зависит от множества факторов, и для их снижения необходимо комплексное техническое обслуживание, контроль качества сборки и соблюдение правил эксплуатации. Регулярные проверки и применение современных материалов позволяют значительно повысить надежность автосцепного устройства и минимизировать риск аварийных ситуаций.
Методы обеспечения надежной и безопасной работы автосцепного устройства:
1. Визуальный осмотр-проводится для обнаружения внешних повреждений, трещин, деформаций и износа деталей. Особое внимание уделяется состоянию корпуса автосцепки, замкового механизма и поглощающего аппарата. Визуальный осмотр рекомендуется проводить регулярно, особенно перед началом рейса и после значительных механических воздействий.
2. Проверка с использованием шаблонов-для оценки износа и соответствия размеров деталей автосцепного устройства применяются специальные шаблоны, такие как комбинированный шаблон. С его помощью проверяют исправность действия предохранителя замка, ширину зева автосцепки, износ малого и большого зубьев, а также другие параметры. Правильное использование шаблонов позволяет выявить критические износы и деформации деталей [2].
3. Функциональные испытания-проверка работы механизмов автосцепки осуществляется путем имитации процессов сцепления и расцепления вагонов. Это позволяет выявить заедания, неправильную работу замкового механизма и другие функциональные отклонения. Такие испытания проводятся как в депо, так и непосредственно на линии при техническом обслуживании.
4. Неразрушающий контроль-для обнаружения скрытых дефектов, таких как внутренние трещины или дефекты материала, применяются методы неразрушающего контроля, включая ультразвуковую дефектоскопию, магнитопорошковый и капиллярный контроль. Эти методы особенно важны для проверки критически нагруженных элементов автосцепного устройства.
В зависимости от типа подвижного состава и условий эксплуатации устанавливаются различные виды осмотров автосцепного устройства:
- Наружный осмотр: проводится при текущем отцепочном ремонте вагонов и технической ревизии. Включает проверку состояния видимых частей автосцепки без ее разборки.
- Полный осмотр: выполняется при капитальном и деповском ремонтах. Предусматривает разборку автосцепного устройства, детальную проверку всех его компонентов и замену изношенных деталей [3].
Соблюдение регламентов технического обслуживания и применение указанных методов диагностики позволяют поддерживать автосцепное устройство в исправном состоянии, повышая безопасность и надежность железнодорожных перевозок.
Для обеспечения надежной работы автосцепного устройства и снижения частоты его отказов необходимо применять комплексный подход, включающий профилактические меры, регулярный контроль и повышение квалификации персонала.
Своевременное техническое обслуживание и регулярные осмотры позволяют выявлять и устранять потенциальные неисправности на ранних стадиях. Особое внимание следует уделять проверке состояния поглощающих аппаратов, замковых механизмов и других критически важных элементов автосцепки. Рекомендуется использовать специализированные стенды для испытаний и ремонта поглощающих аппаратов, что позволяет более точно оценить их техническое состояние и продлить срок службы [4].
Анализ отказов показывает, что значительная часть обрывов тяжеловесных поездов происходит из-за недостаточной прочности перемычки хвостовика автосцепки. Усиление этой детали и использование более прочных материалов могут существенно снизить риск подобных отказов [5].
Обучение и регулярная аттестация работников, ответственных за обслуживание и ремонт автосцепного оборудования, способствуют повышению качества проводимых работ и снижению вероятности ошибок, приводящих к отказам. Проведение сетевых школ и тренингов, направленных на изучение современных методов диагностики и ремонта автосцепок, является эффективной мерой в этом направлении [6].
Ведение подробной статистики отказов автосцепного устройства позволяет выявлять наиболее уязвимые элементы и разрабатывать меры по их укреплению. Организация качественного расследования и анализа причин отказов способствует разработке эффективных профилактических мероприятий и повышению общей надежности системы [7].
Комплексная реализация указанных мер позволит существенно снизить частоту отказов автосцепного устройства, повысить безопасность и эффективность железнодорожных перевозок.
Для снижения износа замкового механизма автосцепного устройства рекомендуется применять следующие меры:
- Регулярное техническое обслуживание и контроль состояния деталей: Периодические осмотры и проверки замкового механизма позволяют своевременно выявлять износ и повреждения. При обнаружении износа, превышающего допустимые нормы, необходимо проводить восстановительные работы, такие как наплавка и последующая обработка деталей до номинальных размеров. Например, выступы замка при износе на глубину более 5 мм допускается наплавлять с последующей обработкой до альбомных размеров [8].
- Использование качественных смазочных материалов: Применение соответствующих смазок на трущихся поверхностях замкового механизма снижает коэффициент трения, что уменьшает износ деталей и продлевает срок их службы. Регулярное обновление смазочного слоя и использование смазочных материалов, рекомендованных производителем, являются важными мерами профилактики износа [2].
Соблюдение этих рекомендаций способствует повышению надежности и долговечности замкового механизма автосцепного устройства, обеспечивая безопасность и эффективность железнодорожных перевозок.
В результате проведенного исследования можно сделать несколько важных выводов, которые касаются как технического состояния автосцепных устройств, так и практики их обслуживания. Анализ отказов автосцепных устройств на основе данных различных источников, таких как rollingstock.narod.ru, показывает, что частота неисправностей напрямую зависит от комплекса факторов, включая эксплуатационные условия, конструктивные особенности и уровень технического обслуживания.
Наиболее часто встречающимися причинами отказов являются механический износ ключевых компонентов, такие как замкодержатели и тяговые хомуты, а также деформация элементов из-за воздействия высоких динамических нагрузок, климатических условий и дефектов производства. Влияние этих факторов приводит к снижению эффективности сцепления и увеличению вероятности саморасцепов, что в свою очередь сказывается на безопасности движения и надежности подвижного состава.
Периодические осмотры, использование износостойких материалов, а также внедрение современных методов диагностики, таких как неразрушающий контроль и функциональные испытания, значительно повышают надежность автосцепок. Важно отметить, что внедрение систем мониторинга в реальном времени и улучшение технологий ремонта играют ключевую роль в снижении частоты отказов и повышении общей безопасности перевозок.
Также стоит выделить роль человеческого фактора в обслуживании автосцепных устройств. Повышение квалификации персонала, обучение современным методам диагностики и ремонту, а также соблюдение регламентов технического обслуживания способствуют снижению вероятности ошибок при эксплуатации и повышению качества работы обслуживающего персонала.
Таким образом, комплексный подход, включающий улучшение конструктивных элементов автосцепок, использование современных материалов, внедрение технологий мониторинга и регулярное техническое обслуживание, является основой для повышения надежности и безопасности железнодорожных перевозок. Важно также отметить, что ведение статистики отказов и анализ причин неисправностей позволяют своевременно выявлять уязвимые места в конструкции и эксплуатации автосцепных устройств, разрабатывать профилактические меры и укреплять элементы, подверженные износу. Все эти меры совместно помогут значительно снизить частоту отказов, предотвратить аварийные ситуации и повысить общую эффективность железнодорожного транспорта.
