Особенности формирования вибрационного химико-механического оксидного покрытия.
Конференция: VIII Международная научно-практическая конференция "Научный форум: технические и физико-математические науки"
Секция: Машиностроение и машиноведение
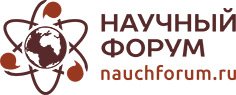
VIII Международная научно-практическая конференция "Научный форум: технические и физико-математические науки"
Особенности формирования вибрационного химико-механического оксидного покрытия.
Аннотация. Сделана попытка выяснить механизм образования оксидной пленки при комбинировании метода вибрационной обработки и оксидирования.
Ключевые слова: оксидная плёнка; механизм формирования; оксидное покрытие.
В основу изучения механизма формирования оксидной пленки положена методика определения характера расположения, размеров, глубины и форы следов обработки при работе в среде полиэтиленовых шаров в процессе оксидирования и без оксидирующего раствора и установления качества пленки, общего вида поверхности с помощью оптических и электронно-микроскопических методов исследований.
В работах авторов Бабичева А.П. Устинова В.П. (1) имеются сведения о формировании поверхностного слоя в процессе вибрационной обработки в среде металлических тел. Эти процессы сопровождаются пластическим деформированием поверхностных слоев металла в условиях многократного динамического контакта частиц рабочей среды с деталью.
При комбинировании метода вибрационной обработки и оксидирования взаимодействие рабочей среды (полиэтиленовых шаров) и поверхностного слоя обрабатываемого материала осуществляется через прослойку образующейся оксидной пленки и раствора, находящихся в зоне контакта. Согласно теории химического оксидирования образование оксидной пленки, рост ее является результатом взаимодействия металла с рабочим раствором, которое осуществляется через поры пленки, образующейся в процессе оксидирования.
В процессе вибрационной обработки частицы рабочей среды наносят удары по обрабатываемой поверхности. В зоне контакта возникают напряжения, обеспечивающие пластическую деформацию, что приводит к увеличению дислокаций и образованию активных дислокационно-вакансионных центров. Под воздействием циркулирующей рабочей среды и деталей образуется сравнительно равномерный слой пластически-деформированного активного металла.
Увеличение внутренней энергии поверхностных слоев металла в результате пластической деформации приводит к повышению адсорбционной активности металлической поверхности.
Скорость химических реакций зависит от числа активных молекул. В результате скольжения шаров относительно поверхности деталей, взаимного колебания атомных групп составляющих молекулы, повышенной энергии движения рабочей среды происходит активация молекул оксидирующего раствора, за счет получения ими дополнительной энергии. Об активации молекул свидетельствует увеличение толщины оксидной пленки, полученной при ВиО 4,5-5 мкм, (без ВиО 3-3,5 мкм). ВиО сообщает ионам дополнительную энергию, необходимую для преодоления увеличивающегося расстояния между металлом и растущей оксидной пленкой.
Таким образом, последовательное нанесение большого числа микроударов частиц рабочей среды при их взаимном соударении и скольжении приводит к повышению химической активности не только металлической поверхности, но и молекул оксидирующего раствора.
Характерный след от удара шара о поверхность оксидированной детали показан на рис. 1. Визуальный анализ фотоснимка дает основание считать, что при ударе шара деформация направлена в глубь образца. Это же подтверждается и профилограммой отпечатка, где видны незначительные навалы по краям лунки (рис.2) в сторону проекции вектора скорости шара (рис. 3).
Рисунок 1. Характерные следы прямого и косого удара шара, по поверхности металла с оксидной пленкой, толщиной 1 мкм
ВУ 2000 ГУ 80
Рисунок 2. Профилограмма отпечатка прямого удара шара
ВУ 2000 ГУ 80
Рисунок. 3 Профилограмма отпечатка косого удара шара
Вибрирующая среда, контактируя с поверхностью растущей оксидной пленки, разрыхляет ее, чем облегчает доступ оксидирующего раствора к поверхности металла. Реакционная способность раствора усиливается за счет активации составляющих его компонентов.
Интенсивность протекающих процессов отмечается не только в реакционной зоне, но и в зоне непосредственного контакта. Под воздействием нормальных и тангенциальных сил поверхностный слой оксидной пленки деформируется, как за счет воздействия шаров, так и за счет вибрирующего раствора.
И.А. Одинг к сдвиговым процессам пластической деформации относит механизм скольжения, проявляющийся в перемещении одной части зерна по отношению к другой. Внешне проявление этого перемещения выражается образованием на поверхности металла полос скольжения.
Полученная структура алюминия АДI до и после обработки. Показывает изменение зерен, уменьшение размера и вытягивание их параллельно плоскости обработки зерен алюминия.
Визуальный анализ фотоснимков показывает, что на исследуемой поверхности имеется большое число беспорядочно расположенных следов обработки - выступов и впадин. Они имеют разнообразную форму, глубину и размеры. Видны мелкие углубления и продольные разнонаправленные риски разнообразной формы и размеров, что является следствием прямых и косых ударов. Контуры следов неровны, что свидетельствует о переменном характере движения шара относительно обрабатываемой поверхности.
На различных участках рельефа поверхности видны кратерообразные следы прямого воздействия шара о поверхность, деформация направлена вглубь образца. Видны множество следов, полученных от ударов шаров, направленных под углом к поверхности, что свидетельствует о скользящем ударе, вызывающем сдвиг и хрупкое разрушение материала.
При рассмотрении фотоснимков поверхности образцов, обработанных в течение 5 минут отмечается неоднородность обработанной поверхности. Она представляет собой пересечение исходных шероховатостей со следами обработки. Различаются полированные участки поверхности и участки со следами разрушения. Поверхность покрыта кратерами - впадинами различного типа.
Съем металла во времени протекает нелинейно.В начале обработки протекает инкубационный период, в течение которого заметной потери массы не наблюдается. Как показали исследования, в этот период образуются вмятины - отпечатки, происходит накопление скрытой энергии разрушения, охрупчивание поверхностных слоев обрабатываемого материала.
При более длительной обработке наблюдается соприкосновение и наложение множества единичных следов и поверхность в местах скопления большого числа следов обработки представляет многократно передеформированный слой.
При рассмотрении следов видно, что отдельные шары при столкновении с обрабатываемой поверхностью оставляют на ней прерывистый след, состоящий из более мелких следов, обусловленных характером движения шаров.
При таком перекрестном характере расположения рассмотренных следов обработки образуется своеобразный микрорельеф.
Анализируя полученные результаты можно отметить, что при ВиО в среде полиэтиленовых шаров на поверхности образуются следы кратерообразного типа, являющиеся следствием прямого удара; следы удлиненной формы, образующиеся в результате скольжения шара относительно обработанной поверхности и следы смешанного типа, являющиеся следствием как скольжения, так и прямого соударения. Большая часть следов обработки носит смешанный характер.
Большое число обработочных следов, покрывающих почти всю поверхность образца, указывает на протекание процессов пластического деформирования на микроуровне и разрыхления поверхностного слоя.
Эти явления имеют большое значение при формировании оксидной пленки и микрорельефа поверхности, так как непосредственный контакт шара происходит по оксидной пленке.
Многочисленными исследованиями установлено наличие пластического течения материала в тонком поверхностном слое образца по ходу движения отдельной гранулы. При прямом ударе шара деформация направлена вглубь образца. Большинство следов свойственны ударам шаров, направленным под углом к поверхности, которые вызывают хрупкое разрушение оксида и сдвиг отдельных частиц. Такое разрушение поверхности позволяет взрыхлять слой оксида с образованием мелкодисперсных частиц, часть из которых схватывается своими ювенильными поверхностями с оксидом, иногда попадая в поры и уменьшая их объем, частично уносится оксидирующим раствором, частично уплотняется последующими ударами шаров и приобретает полированный вид.
Первоначальный контакт шара происходит по вершинам микронеровностей. В процессе обработки увеличивается площадь контакта покрытия с поверхностью в результате закругления радиуса выступов. На профилограмме шлифованной поверхности, записанной после обработки в полиэтиленовых шарах и после совмещения с оксидированием видно, что в результате деформирования гребешков микронеровностей под воздействием ударов шаров происходит уменьшение шероховатости, увеличение радиуса закругления вершин выступов.
Следовательно, в результате вибрационной обработки оксидная пленка разрыхляется и сглаживается в процессе ее роста.
В зоне контакта, благодаря скользящим ударам шаров, частицы оксидной пленки ориентируются параллельно обрабатываемой поверхности, о чем свидетельствуют блестящие участки на поверхности покрытия, хорошо видимые на микрофотографии, (рис.4).
На ней изображен вид поверхности оксидного покрытия, полученного при вибрационной обработке. Следует отметить, что более 50% поверхности покрытия, полученного в результате виброобработки, имеет ориентацию частиц параллельно плоскости скольжения.
Рисунок 4. Вид оксидного покрытия, полученного в процессе вибрационной обработки
Для сравнения на рис. 5 представлена микрофотография оксидной пленки, полученной стандартным способом.
Рисунок 5. Вид оксидного покрытия, полученного традиционным способом
Анализируя снимки можно сделать вывод, что при нанесении покрытия в стационарных ваннах, то есть без приложения нагрузки, зерна гидроксида имеют беспорядочную ориентацию, а полученные в процессе вибрационной обработки ориентированы параллельно плоскости скольжения.
Подводя итог проведенных исследований, можно заключить, что вибрационная обработка в среде полиэтиленовых шаров позволяет совместить три технологических этапа:
- подготовку поверхности под покрытие - очистку от загрязнений и окислов, активацию поверхностного слоя в результате пластического деформирования и увеличения плотности дислокаций поверхностных слоев, образование ювенильных поверхностей; увеличение площади контакта;
- получение оксидной пленки;
- отделку поверхности
- создание определенного микрорельефа, повышение отражательной способности и качества поверхностного слоя.
