Имитационная модель логистической системы транспортировки жидкого чугуна металлургического предприятия
Конференция: XXXIII Международная научно-практическая конференция «Научный форум: технические и физико-математические науки»
Секция: Металлургия и материаловедение
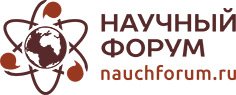
XXXIII Международная научно-практическая конференция «Научный форум: технические и физико-математические науки»
Имитационная модель логистической системы транспортировки жидкого чугуна металлургического предприятия
SIMULATION MODEL OF A LOGISTICS SYSTEM FOR TRANSPORTING LIQUID IRON OF A METALLURGICAL ENTERPRISE
Konstantin Vinogradov
Post-graduate student, Cherepovets State University, Russia, Cherepovets
Аннотация. Рассматривается задача создания имитационной модели логистической системы транспортировки жидкого чугуна на металлургическом предприятии. Исследование и построение модели выполнено с использованием инструментального средства AnyLogic. В качестве исходных данных были использованы реальные данные с производства. Эффективность работы имитационной модели достигается путём автоматического сбора в режиме реального времени всех статистических значений параметров объектов моделирования и принятия логистических решений на их основе.
Abstract. The article deals with creating a simulation model of a logistic system for transporting molten iron at a metallurgical enterprise is considered. Research and construction of the model was performed using the AnyLogic tool. As initial data, real data from production were used. The efficiency of the simulation model is achieved by automatically collecting in real time all the statistical values of the parameters of the objects of modeling and making logistics decisions based on them.
Ключевые слова: жидкий чугун; миксер; логистика; методы оптимизации.
Keywords: molten iron; mixer; logistics; optimization methods.
Обеспечение конвертерного цеха чугуном в достаточном количестве и требуемого качества является одним из наиболее ответственных процессов металлургического предприятия. Цикличность плавок конвертерного цеха и выпусков доменных печей не совпадают, это несовпадение сглаживается оперативным запасом чугуна в миксере, и чугуном который находится в процессе транспортирования. Характерной особенностью материального потока жидкого чугуна является отсутствие фазы промежуточного складирования на стадии его зарождения (непосредственный слив чугуна из доменной печи в транспортное средство) и весьма ограниченные возможности «складирования» на стадии его погашения (миксер конвертерного цеха)[2].
Количество локомотивов и миксеров зависящие от длительности операций и особенно межоперационных простоев технологического процесса транспортирования чугуна не всегда обеспечивают нормальный ритм основного производства. Это приводит к значительным производственным потерям и свидетельствует о необходимости повышения качества принимаемых управленческих решений и использования для этого имитационных моделей рассматриваемого процесса, более точно отражающих существующее положение с учетом интересов всех участников потокового процесса.
Решение данной задачи можно достичь разными методами, например, разработкой новых или усовершенствованных алгоритмов, основанных на нечёткой логике [5], математическим моделированием [1], имитационным моделированием [3-4]
Учитывая особенности технологических процессов доставки жидкого чугуна и поставленные задачи, определим в качестве объектов моделирования следующие агрегаты:
- доменные печи;
- подвижные миксеры для транспортировки чугуна до ворот конвертера;
- сталелитейные ковши для транспортировки чугуна от ворот конвертера до цеха.
В таблице 1 представлены технические характеристики объектов моделирования, представленных выше.
Таблица 1.
Технические характеристики объектов моделирования
Объект моделирования |
Технические характеристики |
|||
Расстояние до сталеплавильного цеха, м |
Расчётное время в пути, мин |
Производительность, т\сутки |
Грузоподъёмность, т |
|
1 |
2 |
3 |
4 |
5 |
ДП №1(л.1) |
1593 |
26 |
3300 |
– |
ДП №1(л.2) |
2103 |
34 |
||
ДП №2(л.1) |
1698 |
28 |
3200 |
|
ДП №2(л.2) |
2208 |
36 |
||
ДП №4(л.1) |
2040 |
32 |
7000 |
|
ДП №4(л.2) |
2040 |
32 |
||
ДП №4(л.3) |
2910 |
44 |
||
ДП №5(л.1) |
2400 |
36 |
13000 |
|
ДП №5(л.2) |
2400 |
36 |
||
ДП №5(л.3) |
3527 |
52 |
||
ДП №5(л.4) |
3527 |
52 |
|
|
Миксер №2 |
– |
– |
– |
568 |
Миксер №3 |
– |
– |
– |
602 |
Миксер №4 |
– |
– |
– |
568 |
Миксер №5 |
– |
– |
– |
587 |
Миксер №6 |
– |
– |
– |
550 |
Миксер №7 |
– |
– |
– |
517 |
Миксер №9 |
– |
– |
– |
445 |
Миксер №10 |
– |
– |
– |
474 |
Миксер №12 |
– |
– |
– |
489 |
Миксер №14 |
– |
– |
– |
545 |
Миксер №15 |
– |
– |
– |
513 |
Миксер №16 |
– |
– |
– |
513 |
Миксер №17 |
– |
– |
– |
518 |
Миксер №19 |
– |
– |
– |
459 |
Миксер №21 |
– |
– |
– |
564 |
Миксер №22 |
– |
– |
– |
448 |
Миксер №24 |
– |
– |
– |
488 |
Миксер №25 |
– |
– |
– |
517 |
Имитационная модель разработана со следующими допущениями:
- не учитывается изменение химического состава;
- в начальный момент времени все миксеры находятся под лётками доменных печей либо на запасных железнодорожных путях, доменные печи имеют нулевой объём жидкого чугуна;
С помощью встроенного инструментария AnyLogic построен имитационный план транспортной системы металлургического предприятия.
Реализована симуляция работы четырёх доменных печей. Схема расположения представлена на рисунке 1.
Рисунок 1. Схема расположения доменных печей в имитационной модели
Каждая доменная печь имеет определённое количество лёток в соответствии с реальным производственным процессом. Так же предусмотрены запасные пути, выполненные в виде синих пунктирных линий, на которые могут прибывать миксеры для ожидания свободного места под лёткой.
Каждая тонна чугуна создаётся согласно расписанию плавок в модели как отдельный агент. После создания чугуна в количестве равном вместимости миксера, поступает управляющее воздействие на слив чугуна. После наполнения миксер движется через участок взвешивания в сторону конвертерного цеха места слива чугуна в ковши. Если все железнодорожные пути заняты, то миксера останавливается и встаёт в очередь.
После слива чугуна в ковши, миксер разворачивается и движется в обратном направлении к доменным печам до развилки железнодорожных путей.
Сравнительная характеристика результата моделирования и фактического веса доставленного в конвертерный цех чугуна представлена на рисунке 2.
Рисунок 2. График зависимости количества чугуна от времени
График зависимости теоретической массы чугуна доставленной в конвертерный цех от времени (Мтеор) отражает реальную потребность конвертерного цеха в чугуне, т.е. то сколько должно быть доставлено, чтобы обеспечить отсутствие простоев производственного процесса в следствии недостатка или излишка доставленного чугуна.
График зависимости фактической массы чугуна доставленной в конвертерный цех от времени (Мфакт) получен на основе реальных данных и отражает результат приятия логистических решений человеком (диспетчером). На рисунке 4 видно, как график Мфакт отклонился от Мтеор, что свидетельствует о недостаточной массе жидкого чугуна, доставленной в конвертерный цех.
График зависимости теоретической массы чугуна доставленной в конвертерный цех от времени (Ммодел) получен на основе данных моделирования. Графики (Мтеор) практически совпадают (Ммодел), что свидетельствует о том, что решения принимаемые имитационной моделью эффективнее, чем решения, принятые диспетчером на указанном промежутке времени.
Проанализировав результаты моделирования, можно сделать вывод о том, что среднее значение относительной погрешности равно 3,43%.
Под относительной погрешностью, в данном случае, понимается отклонение данных, полученных в ходе моделирования, от теоретических (эталонных), то есть реальной потребности конвертерного цеха в жидком чугуне.
Причиной отклонения значений является различие начальных фактических и экспериментальных значений параметров технологического процесса, а именно:
- начальное расположение миксеров. В имитационной модели на старте миксеры находятся под лётками или на запасных путях.
- Текущий вес чугуна в доменных печах. В имитационной модели в начальный момент времени он равен нулю.
Выделим основные причины эффективности имитационной модели:
- Имитационная модель автоматически в режиме реального времени собирает все статистические значения параметров объектов моделирования
- Система за короткий промежуток времени (менее одной секунды) анализирует собранные данные и на их основе осуществляет принятие решений
- Управление движением миксеров осуществляется автоматически, без участия диспетчера
