APPLICATION OF HYDROGENIZATION PROCESSES IN THE PETROCHEMICAL INDUSTRY
Журнал: Научный журнал «Студенческий форум» выпуск №40(176)
Рубрика: Химия
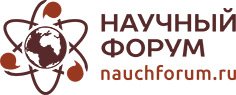
Научный журнал «Студенческий форум» выпуск №40(176)
APPLICATION OF HYDROGENIZATION PROCESSES IN THE PETROCHEMICAL INDUSTRY
ПРИМЕНЕНИЕ ГИДРОГЕНИЗАЦИОННЫХ ПРОЦЕССОВ В НЕФТЕХИМИЧЕСКОЙ ПРОМЫШЛЕННОСТИ
Иванова Анна Дмитриевна
студент, Астраханский государственный технический университет, РФ, г. Астрахань
Abstract. The article deals with issues related to the development of the main technologies of hydrogenization processes in the petrochemical industry. The effect of catalysts that accelerate the rate of reactions and metal promoters deposited on the catalyst carrier on the activity of the main hydrogenization processes.
Аннотация. В статье рассматриваются вопросы, связанные с развитием основных технологий гидрогенизационных процессов в нефтехимической промышленности. Влияние катализаторов, которые ускоряют скорость протекания реакций, и металлических промоторов, нанесенных на носитель катализатора, на активность основных гидрогенизационных процессов.
Keywords: hydrogenization processes, hydrocracking, hydrotreating, catalyst, petroleum products.
Ключевые слова: гидрогенизационные процессы, гидрокрекинг, гидроочистка, катализатор, нефтепродукты.
Today, the processes associated with high-temperature processing of crude oil at high pressure or in the presence of a catalyst are important and relevant. The development of hydrogenization processes is associated with the need to increase the quality requirements of commercial petroleum products, reduce the cost of hydrogen production and create highly efficient catalysts. The issues of the development of hydrogenation processes are widely used in modern processes of oil refining and petrochemistry[1].
These processes are used to produce high-quality gasoline with high octane numbers, to improve the quality of diesel, boiler fuels and lubricating oils.
There are many technologies for hydrogenization processes: hydrotreatment, hydrodeparaffinization, hydroisomerization, hydrogenation of alkenes and arenes in oil fractions, hydrocracking of oil fractions, hydroconversion and others. Hydrotreating and hydrocracking processes occupy a leading place among these processes [2]. Therefore, the purpose of the work is to consider the main hydrogenization processes.
Hydrotreating is a hydrogenization process that favors the purification of oil fractions and residues from harmful impurities, due to the breaking of the C-S, C-N and C-O bonds and the subsequent hydrogen saturation of the formed hydrocarbon radicals. As a result, sulfur, oxygen and hydrogen are released in the form of H2S, NH3 and H2O and naphthenic hydrocarbons [3]. The hydrotreating process is greatly influenced by catalysts that accelerate the reaction. For greater efficiency of the process, hydrotreating catalysts should have a high hydrogenation ability and a low cleavage ability. Generally, hydrotreating catalysts consist of:
1) Active components (18-25% by weight) that perform hydrogenating functions: sulfides and oxides of Mo, Ni, Co and partially Cr, W, Fe;
2) Oxides of aluminium, zeolites, alumoselicates performing acidic functions such as cracking and isomerization;
3) Oxides of silicon, titanium, zirconium, aluminum that perform a binding function and have a developed surface and high mechanical strength [1].
In addition to the action of catalysts, the hydrotreating process is influenced by temperature, pressure, the multiplicity of circulation of hydrogen-containing gas, the volumetric feed rate of raw materials and the thermal effect. Hydrotreating should be carried out in the temperature range 260 - 420 oC, so that there is no slowing down of desulfurization reactions and acceleration of cracking and coking. The total pressure in the system should be 2.5-6.0 MPa, while the partial pressure of hydrogen should be 1.5-3.7 MPa [3]. The volume feed rate of raw materials is the ratio of the volume of raw materials supplied to the reactor within one hour to the volume of the catalyst in the reactor. It directly affects hydrotreatment, because with a decrease in the volumetric feed rate of raw materials, the degree of its purification increases.
Hydrotreating of gasoline fractions is carried out to prepare the feedstock for the reforming process. There is a process of hydrotreating gasoline of straight-run gasoline fractions (naphtha) and gasoline fractions of catalytic cracking. The first one is based on the reactions of hydrogenolysis and incomplete destruction of molecules in a hydrogen-containing gas medium. The second process is aimed at reducing sulfur and diene hydrocarbons in commercial gasoline [3].
Hydrotreating of kerosene fractions is based on increasing thermal stability and is designed to reduce the content of sulfur, olefins and resins in jet fuel.
Hydrotreating of diesel fractions is carried out to reduce the content of sulfur and polyaromatic carbohydrates, because polyaromatic hydrocarbons reduce the cetane number of fuel.
Hydrotreating of petroleum residues (fuel oil and tar) in various ways is aimed at clarifying oils and giving them chemical resistance, corrosion resistance, environmental friendliness.
Hydrocracking is an oil refining process designed to produce low-sulfur fuel distillates, liquefied gases from various raw materials. The hydrocracking process helps to increase the yield of light distillates by converting raw materials such as gas oil. The yield of light distillates largely depends on the presence of catalysts and their properties [5].
The activity of the hydrocracking process can be achieved by using the acidic component of the catalyst carrier: halogenated oxide of aluminum, amphoteric aluminoselicates, oxide of silicon and zeolites.
The most effective are zeolite-based catalysts, which are characterized by high hydrocracking activity and selectivity.
Catalysts with high acidic and optimal hydrogenating activities affect the yield of fractions, reducing the yield of paraffins, improving the anti-knock characteristics of gasoline fractions [4].
Hydrocracking improves the quality of gasoline and distillate.
The hydrocracking process makes it possible to process almost all petroleum distillates. The raw materials supplied to hydrocracking should not contain asphaltenes and high molecular weight condensed compounds, because these compounds as a result of the hydrocracking process lead to the formation of coke settling on the surface of the catalyst, which leads to rapid disactivation of the catalyst [1].
Analyzing the data obtained, it can be concluded that the leading role of hydrogenization processes lies in the hydrotreating and hydrocracking of petroleum products. The activity of hydrogenation processes can be achieved through the use of various catalysts and metal promoters deposited on the catalyst carrier.
As promoters, metals of VI groups, such as Mo or W and VIII groups can be used: Ni, Co, sometimes Pt or Pd. Also, hydrogenization processes depend on temperature, pressure and volumetric feed rate of raw materials.
