СПОСОБЫ ОБЕСПЕЧЕНИЯ НАДЕЖНОСТИ ГАЗОРАСПРЕДЕЛИТЕЛЬНЫХ СЕТЕЙ
Журнал: Научный журнал «Студенческий форум» выпуск №15(194)
Рубрика: Технические науки
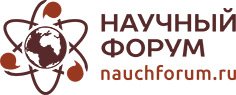
Научный журнал «Студенческий форум» выпуск №15(194)
СПОСОБЫ ОБЕСПЕЧЕНИЯ НАДЕЖНОСТИ ГАЗОРАСПРЕДЕЛИТЕЛЬНЫХ СЕТЕЙ
Аннотация. Одной из основных задач эксплуатации систем газораспределения и газопотребления является безопасная и бесперебойная подача газа потребителям, снижение эксплуатационных расходов, затрат на рабочую силу и повышение экономической эффективности. В статье описан опыт технической диагностики газораспределительных сетей. Обозначена проблема опасных дефектов.
Была проведена работа по выбору режимов рентгеновского контроля на наиболее распространенных диаметрах труб для газовых сетей, подбору материалов и оборудования, необходимых для рентгеновского контроля.
Ключевые слова: газораспределительные сети, аварии, надежность, безопасность, газовые сети, диагностика, дефекты, фокусное расстояние, рентгенографический метод.
Основным требованием к газораспределительной системе является обеспечение надежности, безопасности и эффективности в экономическом и экологическом планах [5].
Надежность - это способность технической системы функционировать без сбоев в течение длительного периода времени. Для системы газораспределения надежность может быть представлена как обеспечение безопасной работы системы газоснабжения. Задача обеспечения надежной работы газораспределительной системы заключается в решении двух основных задач: своевременном обнаружении дефектов и прогнозировании условий их развития вплоть до момента разрушения.
В дополнение к оценке аварийного риска повреждения газопровода на основе характера соединения, типа повреждения, давления перекачиваемого газа, диаметров газопроводов, также важно оценить воздействие утечки газа из поврежденных газопроводов на окружающую среду.
Чтобы выбрать эффективные меры по предотвращению пожароопасных ситуаций в случае аварийных выбросов и неконтролируемых утечек газа, необходимо сначала изучить процессы этих ситуаций, чтобы получить необходимые данные для их практического применения.
Опыт диагностики газовых сетей показывает, что среди всех выявленных дефектов значительную часть составляют дефекты монтажа, вызванные нарушением технологии прокладки газопроводов и установки газовой арматуры, а также разрушительными коррозионными процессами.
Согласно статистике, в последние десятилетие на газораспределительных сетях было зарегистрировано более 1700 аварий с общим ущербом в 7 миллионов рублей в год. Анализ имеющейся статистики показал, что в общем количестве аварий при распределении и использовании природного газа, аварии на газопроводах составляют до 50%. Несчастные случаи, связанные с распределением и использованием газа, составляют около 30%, и последствия этой категории аварий более серьезны и имеют значительные материальные затраты [3].
Основная часть методических принципов и общих требований к расчету вероятности аварий и инцидентов на газовых сетях и анализу рисков представлена в Приказе Ростехнадзора от 04.04.2016 № 144 "Об утверждении Руководства по технике безопасности "Методические основы анализа опасностей и оценки рисков риск аварий на опасных производственных объектах" и включают в себя: анализ и организацию работы; выявление опасностей; оценку рисков, уточнение объектов, включенных в систему газораспределения (насколько опасны определенные линейные объекты и их участки), разработку различных рекомендаций по снижению рисков на основе этой информации.
Таким образом, накопление и систематизация данных о характере чрезвычайных ситуаций и степени ущерба позволяет выявить наиболее уязвимые области и разработать институциональные меры по их предотвращению и устранению, в том числе посредством различных исследований и проектов, направленных на повышение безопасности систем газораспределения, минимизацию материального ущерба и гибель людей.
В то же время расчет оптимального уровня надежности, как одной из категорий осуществимости, включающий в себя анализ и оценку рисков, должен быть одним из необходимых этапов для разработки проектов газораспределительных систем и их последующей эксплуатации. На сегодняшний день большинство сетей газораспределения и газопотребления выполнили нормативный срок службы и их дальнейшая эксплуатация целесообразна на основе оценки технического состояния, определения работоспособности и остаточного ресурса, анализа экономической эффективности эксплуатации с дальнейшей модернизацией и реконструкцией. Качество оценки технического состояния газопроводов зависит от уровня оснащенности лаборатории неразрушающего контроля и квалификации специалистов [4].
Выполнение работ по комплексной диагностике газораспределительных сетей и экспертизе промышленной безопасности строго регламентировано документацией действующих нормативных актов Ростехнадзора и внутренними правилами ОАО "Газпром", выполнение которых направлено на выявление большинства основных видов дефектов, снижающих надежность.
Как показывает опыт диагностики газовых сетей, больше всего выявленных дефектов - это дефекты монтажа, которые вызваны нарушением технологии прокладки газопроводов и монтажа газового оборудования. Они включают в себя порезы и свищи на сварных швах, нарушения геометрии сварного шва, переломы ствола трубы, неполное заполнение подготовки кромок.
В то же время большинство дефектов сварных соединений представляют собой внутренние трещины, которые не являются трещинами (так называемые подповерхностные дефекты).
Их обнаружение возможно только с использованием различных специализированных методов неразрушающего контроля (ультразвукового, магнитного и рентгенографического).
Значительная часть повреждений вызвана эксплуатационными дефектами (истончение стенки трубопровода из-за эрозии и механических воздействий, вмятины, потеря герметичности резьбовых соединений и фланцев, усталостные трещины и т.д.). Основными механизмами повреждения подземных газопроводов являются различные виды коррозии. Проблема опасных дефектов заключается в том, что коррозионные процессы чаще всего носят локальный, неоднородный характер, и без специальных диагностических мероприятий такие дефекты визуально не обнаруживаются [6].
Рисунок 1. Сварочная трещина в газопроводе высокого давления
Рисунок 2. Газопровод поврежден коррозией
Рентгенографический метод является одним из методов контроля для обнаружения внутренних и поверхностных дефектов сварки (поры, цепочки пор, корень, трещины, раковины, шлаковые включения и т.д.). Импульсные рентгеновские аппараты с низким током и нерегулируемой энергией рентгеновского излучения используются в качестве источника излучения в различных условиях. Для записи изображений используются наиболее чувствительные к излучению толстые рентгеновские пленки. Их недостатком является низкая контрастность и детальная рентгенографическая чувствительность. Кроме того, используются усиливающие флуоресцентные экраны, которые еще больше увеличивают геометрическую размытость [1].
В процессе осмотра создается рентгеновская пленка, показывающая сварной шов и область, прилегающую к кости, для оценки его качества. Основными критериями обнаружения дефектов в сварных швах являются [5]:
1.достигнутая рентгенографическая чувствительность рентгенографического изображения (определяется по эталону);
2. значение оптической плотности;
3. время экспозиции;
4. фокусное расстояние от источника излучения до поверхности сварки;
5. тип и марка рентгеновской пленки;
6. оптимизация режимов рентгеновского контроля.
В целях снижения эксплуатационных расходов, затрат на рабочую силу и повышения экономической эффективности была проведена работа по выбору режимов рентгеновского контроля в диаметрах труб, более распространенных для газовых сетей, а также по выбору материалов и оборудования, необходимых для контроля рентгеновских режимов, оптимальный контроль рентгеновских лучей (с использованием рентгеновских аппаратов down ARINA-5.7) был определен на примере контроля рентгеновских лучей от сварочного аппарата 1717 по ГОСТ 16037-80 из стальной трубы диаметром 108 мм и толщиной стенки 3,5 мм (рис. 3).
Рисунок 3. Внешний вид круглого сварного шва С17 по ГОСТ 16037-80 стальная труба 108х3,5 мм
Для определения оптимальных режимов рентгеновского контроля были выбраны два типа рентгеновских пленок AGFA F8 (толстые) и AGFA D7 (тонкие) с двумя флуоресцентными экранами.
Было произведено практическое сравнение полученных расчетных значений с экспериментальными значениями фокусного расстояния, производительность и качество полученных рентгеновских изображений были связаны с соответствием их критериям обнаружения дефектов. Чтобы сравнить расчетные и экспериментальные значения фокусного расстояния со временем экспозиции, были получены изображения сварки круглой трубы диаметром 108 мм с использованием различных типов рентгеновских пленок (AGFA D7 и AGFA F8) и с разными фокусными расстояниями.
Анализ полученных рентгеновских изображений показал, что использование выбранной схемы контроля и примененного типа пленки F8 обеспечивает полное соответствие критериям для локализации и визуализации наличия или отсутствия дефектов в сварном соединении. В то же время сравнение расчетного значения с экспериментальным значением фокусного расстояния позволяет сделать вывод, что его изменение в сторону уменьшения расчетного значения не влияет на качество изображения и на критерии обнаружения дефектов в кольцевом сварном соединении.
Также было экспериментально доказано, что сокращение времени экспозиции соответствует критериям обнаружения дефектов и повышает эффективность рентгеновского контроля. При выполнении проверки с пленкой типа D7 рассчитанное значение фокусного расстояния не обеспечивает качество изображения, соответствующее критериям обнаружения дефектов, поскольку имеется несоответствие в параметре оптической плотности. Возможны отклонения в уменьшении фокусного расстояния от расчетного значения, что сокращает время экспозиции и повышает вероятность того, что критерии обнаружения дефектов при сварке будут соблюдены [2].
Таким образом с помощью рентгенографического метода были определены основные критерии обнаружения дефектов в сварных соединениях, определены оптимальные режимы рентгеновского контроля с использованием импульсных рентгеновских аппаратов на стальных трубах большого и малого диаметров, рассчитано фокусное расстояние для газовых труб разного диаметра, а также было определено разрешенное время экспозиции.
Установлено, что бесперебойное газоснабжение может быть обеспечено качественным выполнением плановых и профилактических работ, соблюдением нормативных требований, непрерывным мониторингом и прогнозированием значений параметров системы, быстрым реагированием и взаимодействием служб газораспределительной организации.
