УЛЬТРАЗВУКОВОЙ И МАГНИТНЫЙ КОНТРОЛЬ ДЕТАЛИ ТИПА «ВАЛ» КОЛЕСНОЙ ПАРЫ
Журнал: Научный журнал «Студенческий форум» выпуск №1(224)
Рубрика: Технические науки
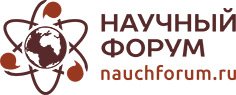
Научный журнал «Студенческий форум» выпуск №1(224)
УЛЬТРАЗВУКОВОЙ И МАГНИТНЫЙ КОНТРОЛЬ ДЕТАЛИ ТИПА «ВАЛ» КОЛЕСНОЙ ПАРЫ
В последние годы неразрушающие испытания материалов прочно вошли в процесс контроля. Благодаря своей эффективной работе эта процедура проверки стала решающей для всестороннего контроля процесса.
В то же время во многих отраслях уже недостаточно проверять только геометрические размеры детали. Это связано с тем, что все чаще предъявляются повышенные требования к тестированию деталей параллельно с непрерывной работой. Поэтому необходимы гораздо более обширные испытания, чтобы подтвердить соответствующие свойства в течение всего срока службы. Ультразвуковой контроль Ультразвуковой контроль включает в себя ряд методов неразрушающего контроля, которые посылают ультразвуковые волны через объект или деталь. Эти высокочастотные звуковые волны передаются в материалы для определения характеристик материала или обнаружения дефектов. В большинстве методов ультразвукового контроля используются короткие импульсные волны с частотами в диапазоне от 0,1 до 15 МГц, хотя могут использоваться частоты до 50 МГц. Ультразвуковой контроль использует пьезоэлектрический преобразователь, соединенный с дефектоскопом, который в своей основной форме представляет собой импульсный приемник и дисплей осциллографа. Преобразователь проходит над проверяемым объектом, который обычно связан с объектом контроля гелем, маслом или водой. Эта контактная жидкость необходима для эффективной передачи звуковой энергии от преобразователя в деталь, однако она не требуется при проведении испытаний бесконтактными методами, такими как электромагнитно-акустический преобразователь (ЭМАП) или лазерное возбуждение. Чтобы получить как можно больше энергии из преобразователя, размещается слой между активным элементом и лицевой стороной преобразователя. Оптимальное соотношение достигается за счет такого размера согласующего слоя, чтобы его толщина составляла 1/4 толщины желаемая длина волны. Это удерживает волны, отраженные в согласующем слое. Для контактных преобразователей согласующий слой выполнен из материала, который имеет акустическое сопротивление между активным элементом и поверхностью детали.
Ультразвуковой контроль можно проводить двумя основными методами – эхо-импульсным и сквозным. При импульсном эхо-контроле один и тот же преобразователь излучает и принимает энергию звуковой волны. В этом методе используются эхо-сигналы на границе раздела, например, на задней стороне вала или дефекта, для отражения волн обратно к датчику. Результаты представлены в виде линейного графика, где амплитуда по оси ординат представляет интенсивность отражения, а расстояние или время по оси абсцисс показывает глубину прохождения сигнала через деталь. При сквозном методе используется излучатель для отправки ультразвуковых волн с одной поверхности и отдельный приемник для приема звуковой энергии, достигшей противоположной стороны детали. Несовершенства материала уменьшают количество принимаемого звука, позволяя обнаружить дефекты. Ультразвуковой контроль также можно разделить на два основных типа: контактный или иммерсионный контроль. Контактный ультразвуковой контроль обычно используется для проверки доступности или портативности на месте. Контактный ультразвуковой контроль можно проводить, когда доступна только одна сторона испытуемого образца, или когда испытуемые детали имеют большие размеры, неправильную форму или их трудно транспортировать.
Иммерсионный ультразвуковой контроль - это лабораторный или заводской неразрушающий контроль, который лучше всего подходит для изогнутых компонентов, сложной геометрии и для разработки ультразвуковой техники. В этом методе компонент или материал погружают в воду, которая действует как контактная жидкость вместо гелей, используемых для контактного ультразвука. Иммерсионный ультразвуковой контроль обычно использует метод эхо-импульса, а траектории роботизированного датчика можно использовать для проверки сложных поверхностей, которые было бы трудно покрыть контактными датчиками.
Иммерсионный ультразвуковой контроль можно использовать для широкого диапазона толщин стенок и типов материалов, что делает его подходящим методом испытаний для различных областей применения и отраслей.
Ультразвуковой контроль как метод неразрушающего контроля идеально подходит для обнаружения дефектов и дефектов без повреждения детали. Периодические ультразвуковые проверки также могут использоваться для проверки коррозии или роста известных дефектов и, таким образом, потенциально предотвращать выход из строя детали, компонента или всего актива. Он используется в различных отраслях промышленности, включая аэрокосмическую, автомобильную, строительную, медицинскую, металлургическую и обрабатывающую.
Ультразвуковой контроль используется в самых разных отраслях промышленности из-за его пригодности для многих различных материалов.
Ультразвуковой контроль идеально подходит для контроля плотных кристаллических структур, таких как металлы. Керамика, пластмассы, композиты и бетон также могут успешно контролироваться, но с меньшим разрешением, поскольку затухание в этих материалах выше.
К преимуществам ультразвукового контроля относятся:
- Высокая проникающая способность, позволяющая обнаруживать дефекты глубоко внутри детали;
- Высокая чувствительность, позволяющая обнаруживать очень маленькие дефекты;
- Может использоваться для проверки, когда доступна только одна сторона объекта;
- Более высокая по сравнению с другими методами неразрушающего контроля точность определения глубины внутренних дефектов и толщины деталей с параллельными поверхностями;
- Способен оценить размер, форму, ориентацию и характер дефектов;
- Возможность оценить структуру сплава компонентов с различными акустическими свойствами;
- Безопасен для находящихся рядом людей, оборудования или материалов;
- Возможны высокоавтоматизированные и портативные операции;
- Можно получить немедленные результаты, что позволяет принимать незамедлительные решения.
Однако есть несколько ограничений для ультразвукового контроля, а именно:
- Требуется опытный технический персонал для осмотра и интерпретации данных;
- Ложноположительные результаты, также известные как ложные сигналы, могут быть результатом допустимых аномалий, а также самой геометрии компонента;
- Объекты шероховатые, неправильной формы, очень маленькие, тонкие или неоднородные трудно осмотреть;
- Отслоившуюся окалину или краску необходимо будет удалить перед началом испытаний, хотя чистую, правильно закрепленную краску можно оставить на месте;
-Ультразвуковой контроль может иметь меньшую чувствительность к объемным дефектам, особенно металлическим включениям, чем радиографический контроль.
Ультразвуковой контроль имеет множество применений в промышленности, включая проверку целостности материала или детали. Это может включать в себя проверку сварных швов для определения наличия каких-либо дефектов. Это испытание может быть выполнено как для черных, так и для цветных металлов, а также для более толстых участков и тех, которые доступны только с одной стороны. Ультразвуковой контроль также позволяет обнаруживать более мелкие дефекты и плоские дефекты, которые не так просто оценить с помощью радиографического контроля.
Магнитный контроль
Магнитопорошковый контроль является очень распространенным и простым в использовании методом неразрушающего контроля. Он работает, как следует из его названия, за счет того, что тестер создает магнитное поле вокруг проверяемой детали. Это делается с помощью постоянного или электромагнитного, наведенного магнитного поля (например, от катушки с током) или с помощью постоянного электрического тока, проходящего через деталь.
1868 год был первым зарегистрированным случаем использования магнетизма для проверки целостности материала. В то время он использовался для проверки стволов пушек на наличие дефектов путем намагничивания стволов, а затем отслеживания их длины с помощью магнитного компаса в поисках любых признаков нарушения магнитного тока. Когда появлялась неровность, указывающая на наличие дефекта в стволе, стрелка компаса двигалась, позволяя людям определить местонахождение дефектов, невидимых невооруженным глазом.
Пятьдесят лет спустя, в 1920-х годах, изобретатель Уильям Хок обнаружил, что он может использовать металлическую стружку для создания узоров на намагниченной ферромагнитной поверхности. Эти узоры будут группироваться вокруг дефектов на поверхности, показывая их местонахождение - точно так же, как сегодня магнитные частицы используются для идентификации дефектов.
В 1930-х годах железнодорожная промышленность начала использовать открытия Хока для проверки своих ферромагнитных материалов, а именно стали, и вскоре этот метод стал стандартным способом выявления дефектов в материалах. Принципы используемых сегодня тестов остаются в основном такими же, как и при их первоначальной разработке. В то время данный вид контроля использовались для испытания стальных материалов путем их намагничивания для получения линий потока. Если бы эти линии были прерваны дефектом в материале, это стало бы очевидным из-за создания второго магнитного поля или поля рассеяния потока в точке, где расположен дефект. При использовании электромагнита поле присутствует только при подаче тока. Когда магнитное поле сталкивается с разрывом, поперечным направлению магнитного поля, силовые линии создают собственное поле рассеяния магнитного потока. Ферромагнитные частицы («магнитные частицы») наносятся на поверхность детали, частицы будут втягиваться в несплошность, уменьшая воздушный зазор и создавая видимую индикацию на поверхности детали.
Магнитные частицы могут представлять собой сухой порошок или взвешенные в жидком растворе, они могут быть окрашены видимым красителем или флуоресцентным красителем, флуоресцирующим в ультрафиолетовом свете. Большинство проверок в полевых условиях выполняются с использованием хомута. Электрическая катушка наматывается вокруг центрального сердечника, и при подаче тока создается магнитное поле, которое распространяется от сердечника вниз через шарнирные ножки в деталь.
Это известно как продольное намагничивание, потому что линии магнитного потока проходят от одного плеча к другому.
Когда ножки размещены на ферромагнитной детали и ярмо находится под напряжением, в деталь вводится магнитное поле. Поскольку линии потока проходят от одного плеча к другому, могут быть обнаружены разрывы, ориентированные перпендикулярно линии, проведенной между плечами. Чтобы убедиться, что показания не пропущены, ярмо используется один раз в показанном положении, а затем снова используется с коромыслом, повернутым на 90°, чтобы не было пропущено ни одного показания. Поскольку весь электрический ток проходит через ярмо, а через часть проходит только магнитное поле, этот тип применения известен как непрямая индукция. Как упоминалось ранее, электрический ток часто используется для создания магнитного поля в компонентах при магнитопорошковом контроле. Переменный ток и постоянный ток - это два основных типа тока, которые обычно используются. Тип тока используемый оказывает влияние на получаемые результаты контроля. Постоянный ток течет непрерывно в одном направлении при постоянном напряжении. Батарея является наиболее распространенным источником постоянного тока. Ток течет от положительного к отрицательному выводу, хотя электроны текут в противоположно направлении. Преимущества магнитопорошкового контроля. В первую очередь, отметим, что метод магнитопорошкового контроля прост и удобен в эксплуатации. Также следует отметить относительно невысокую стоимость оборудования для проведения данного вида контроля и то что многие инструменты портативны. Данный метод контроля считается гораздо более точным, эффективным и действенным, чем проверки, в которых используются проникающие вещества. Магнитопорошковый контроль отлично подходит для обнаружения дефектов на поверхности деталей. Недостатки магнитопорошковой дефектоскопии. Самым большим недостатком данного метода является то, что он имеет гораздо более ограниченное применение для подповерхностных дефектов или трещин. Он не особенно эффективен, когда речь идет об измерении высоты или глубины поверхностной трещины (только длины и ширины). Это приводит к тому, что инспекторы получают лишь частичное представление о потенциальной проблеме. Другим недостатком является то, что это, по сути, субъективно. Он зависит от интерпретации инспектора, оставляя место для человеческой ошибки. Показания также могут быть неточными, если магнитное поле не идеально выровнено. Хотя метод магнитопорошкового контроля прост в использовании, его можно использовать только на ферромагнитных материалах - материалах, которые могут намагничиваться. Они должны быть чистыми и неокрашенными, после чего их нужно размагнитить.
