ИССЛЕДОВАНИЕ ВЛИЯНИЯ ОЧИСТКИ МЕТАЛЛОКЕРАМИЧЕСКОГО КОРПУСА НА АДГЕЗИОННЫЕ СВОЙСТВА ПОВЕРХНОСТИ
Журнал: Научный журнал «Студенческий форум» выпуск №21(288)
Рубрика: Технические науки
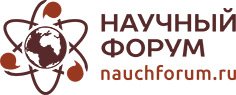
Научный журнал «Студенческий форум» выпуск №21(288)
ИССЛЕДОВАНИЕ ВЛИЯНИЯ ОЧИСТКИ МЕТАЛЛОКЕРАМИЧЕСКОГО КОРПУСА НА АДГЕЗИОННЫЕ СВОЙСТВА ПОВЕРХНОСТИ
Довольно часто в микроэлектронной промышленности используются различные методы очистки и обработки. Их можно условно разделить на две группы: сухие и жидкостные. Особенно они важны там, где присутствуют операции микромонтажа полупроводниковых кристаллов и разварки выводов. До недавнего времени предварительной обработке поверхности уделялось достаточно мало внимания, а ведь от неё напрямую зависит надежность и гарантийный срок работы изделия. Очистка помогает улучшить адгезию поверхности контактных площадок корпуса, повысить гидрофильность (рис.1), удалить органические загрязнения. Кроме того, возможно декапирование поверхности при использовании окисляющихся контактных площадок. Вследствие этого повышается прочность и надежность соединения, появляется возможность снизить параметры сварки.
Однако, традиционная жидкостная очистка, например, с помощью кислот, растворителей или щелочей, способна повлечь за собой деградацию параметров изделия. Вызвана она может быть, прежде всего, абсорбцией реактивов и продуктов реакции керамическим основанием корпуса. Поэтому довольно перспективными кажутся сухие плазменные методы. Но при использовании соответствующих установок необходимо контролировать целый ряд параметров, следовательно, потребуется не один эксперимент для отработки процесса. Целью работы являлся выбор оптимального режима плазменной очистки металлокерамического QLCC корпуса перед разваркой выводов. Оптимальным режимом будет считаться такой, при котором средние значения величин отрывного усилия проволоки и сдвига кристалла будут максимальными.
Рисунок 1. Пример необработанной (А) и обработанной (Б) в плазме поверхностей
Наиболее широко известен метод, основанный на обработке поверхности за счет плазмы газового разряда. В качестве такого газа могут выступать аргон, азот, кислород, гелий или их смеси. В данной работе предпочтение отдавалось именно смеси газов – аргону с кислородом, так как кислород удаляет органические загрязнения, а аргон является катализатором процесса, ускоряя диссоциацию молекул кислорода. Эксперимент проводился на установке плазменной обработки Nordson MARCH AP-1000. Корпуса располагались в реакционной камере на полке между токовым-питающим и заземленным электродами. Параметры установки были разделены на две группы: постоянные (рабочее давление в камере, мощность ВЧ-источника) и переменные (соотношение газов, время обработки). Постоянные параметры процесса приведены в таблице 1.
Таблица 1.
Постоянные параметры процесса
Параметр |
Значение |
Давление в камере, мТорр |
200 |
Мощность ВЧ-источника, Вт |
600 |
Частота ВЧ-источника, МГц |
13,56 |
Корпуса были разделены на шесть партий. Пять из них подверглись различной обработке – четыре с помощью плазменных процессов, одна – химической. Каждой из четырех партий соответствовала своя комбинация переменных параметров эксперимента, которые представлены ниже:
- Соотношение Ar/O2 80/20, время обработки 10 минут.
- Соотношение Ar/O2 80/20, время обработки 5 минут.
- Соотношение Ar/O2 90/10, время обработки 10 минут.
- Соотношение Ar/O2 90/10, время обработки 5 минут.
Пятая партия обрабатывалась химическим методом – обработкой в водном растворе соляной кислоты (1:1) в течение 60 секунд с последующей промывкой в деионизованной воде.
После плазменной обработки проводилась посадка кристалла в корпус на токопроводящий клей и разварка золотой проволоки к контактным площадкам. В качестве клея использовался ТОК-2, при этом его полимеризация проводилась при температуре 170°C в течение двух часов. Присоединение выводов (золотая проволока, 30 мкм) осуществлялось методом ультразвуковой сварки. Тип разварки – шарик-шарик.
В ходе испытаний на установке Nordson DAGE 4000Plus были измерены значения усилия на отрыв (χ) шести разварок на каждом из корпусов для всех партий, а затем рассчитаны средние значения (χср). Следующим шагом было измерение усилия на сдвиг кристалла (σ) и подсчет аналогичного среднего значения (σср). Таким образом, можно хотя бы приблизительно оценить насколько повышается надежность разварки, адгезионные свойства поверхности и качество очистки в целом. Рассчитанные данные приведены в таблице 2.
Таблица 2.
Рассчитанные средние значения χ и σ
№ партии |
χср, г. |
σср, кг. |
1 |
8.25 |
1.35 |
2 |
6.88 |
1.06 |
3 |
6.92 |
1.11 |
4 |
6.73 |
1.12 |
5* |
5.32 |
1.23 |
6** |
3.11 |
0.72 |
6** - корпуса без очистки.
Очевидно, что использование первого режима обеспечивает наивысшие значения отрывного усилия разваренной проволоки и усилия на сдвиг кристалла. Для более комфортного отображения результатов построим график зависимости величины отрывного усилия от общего количества выводов (рис.2). При этом, для лучшей наглядности, используем данные только трех партий: с наивысшими значениями χср, с традиционной химической обработкой и партию корпусов, которая не подвергалась никакой предварительной очистке.
Рисунок 2. Величина отрывного усилия разварки в зависимости от вида обработки
Объясняется положительный эффект очистки довольно просто. Энергия, выделяемая в плазме газового разряда, достаточна для того, чтобы разрушить большинство органических связей (С-С, С-Н, С-О и др.) поверхностных загрязнений. Кроме того, ионизованные молекулы кислорода (О2+, О2-, О3, О+, О-), а также свободные радикалы и электроны, образуют соединения CO, CO2 и различные углеводороды с низким молекулярным весом, которые удаляются в процессе вакуумной откачки. При этом, если обработке подвергаются корпуса с окисляющимися контактными площадками (медь, алюминий), то разумно использовать лишь инертные газы – гелий и аргон – в этом случае преобладало бы физическое распыление загрязнений.
Заметный рост усилия на сдвиг кристалла объясняется изменением краевого угла и активацией поверхности. Краевой угол (угол смачивания) – угол, который образует капля жидкости на поверхности твердого вещества к данной поверхности. Чем больше данная величина, тем сложнее смочить поверхность. Значит, в результате обработки её поверхностная энергия увеличивается, и она переходит из гидрофобного в гидрофильное состояние. Вследствие этого используемый адгезив (в данном случае клей ТОК-2) растекается более равномерно из-за сниженного угла смачивания. Таким образом, улучшается адгезия и прочность соединения кристалла с корпусом.
Из проведенной работы можно сделать следующие выводы. Очевидно, что достигнутые величины разрывного усилия значительно превышают подобные, получаемые без какой-либо обработки. Во-вторых, средние значения при всех исследуемых режимах плазменной обработки превышают значение, полученное химической очисткой. Оценка долговечности обработки поверхности показала, что эффект от обработки наблюдался в течение недели при хранении корпусов в вакуумном контейнере. В этот период монтаж выводов ультразвуковой сваркой осуществлялся без каких-либо затруднений. После этого срока количество неудачных разварок выводов значительно увеличилось. Выходом из данной ситуации является повторная плазменная обработка корпусов с уже посаженным кристаллом. Однако, необходимо учесть влияние плазмы на характеристики прибора, а особенно – на его надежность во время последующей эксплуатации.
Таким образом, сухие плазменные методы очистки имеют ряд преимуществ. Они достаточно эффективны и экологически безвредны. При массовом производстве корпусных полупроводниковых изделий они экономические выгоднее, чем химическая обработка. Обеспечивают повторяемость результатов за счет точной настройки параметров режимов и высокой степени автоматизации. Исходя из всего вышеперечисленного, они по праву заняли свое место в микроэлектронной промышленности.
