Положение контрольной тарелки в ректификационной колонне процесса отмывки изобутан-бутановой фракции от ацетонитрила
Журнал: Научный журнал «Студенческий форум» выпуск №11(32)
Рубрика: Технические науки
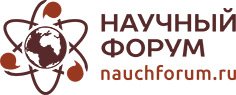
Научный журнал «Студенческий форум» выпуск №11(32)
Положение контрольной тарелки в ректификационной колонне процесса отмывки изобутан-бутановой фракции от ацетонитрила
Aspen HYSYS– это инструмент моделирования процессов для проектирования, оптимизации, бизнес-планирования, управления активами и мониторинга производительности химико-технологических производств.[4]
Массообменные процессы – такие технологические процессы, скорость протекания которых определяется скоростью переноса вещества (массы) из одной фазы в другую конвективной и молекулярной диффузией. Движущей силой массообменных процессов является разность концентраций распределяемого вещества во взаимодействующих фазах.
Массообменные процессы классифицируют по трем основным признакам: агрегатному состоянию вещества, способу контакта фаз и характеру их взаимодействия. В зависимости от сочетания фаз имеются способы их разделения, например, ректификация.
Колонна Кт28, являющаяся предметом нашего исследования, представляет собой тарельчатую ректификационную колонну, со следующими параметрами:
Диаметр – 1,6 м;
Высота – 36,7 м;
Количество тарелок – 46;
Тип контактного устройства – тарелка сетчатая провальная.
Ректификация – Процессами массообмена называют такие процессы, в которых основную роль играет перенос вещества из одной фазы в другую. Движущей силой этих процессов является разность химических потенциалов. Как и в любых других процессах, движущая сила массообмена характеризует степень отклонения системы от состояния динамического равновесия. В пределах данной фазы, вещество переносится от точки с большей к точке с меньшей концентрацией.[2]
Задачу для процесса отмывки изобутан-бутановой фракции от ацетонитрила можно сформулировать следующим образом: необходимо определить контрольную тарелку.
Для моделирования процесса необходимо знать технологический режим, а также состав сырья на входе в колонну.
Таблица 1.
Параметры на входе в колонну
Параметр |
Данные |
Температура, 0С |
50 |
Давление, МПа |
0,45 |
Расход, кг/ч |
2100 |
Таблица 2.
Состав исходной смеси на входе в колонну следующий
Состав |
% масс. |
Бутан |
38 |
Изобутан |
35 |
Ацетонитрил |
27 |
На основе вышеизложенных данных была смоделирована схема отмывки изобутан-бутановой фракции от ацетонитрила.
Рисунок 1. Схема отмывки изобутан-бутановой фракции от ацетонитрила
Таблица 3.
Температурные профили по высоте колонны при различных расходах, относительные отклонения температуры
№ тар. |
t при F=2100 кг/ч |
t при F+5% |
t при F+10% |
dt1 |
dt2 |
dt3 |
46 |
39,1 |
37,9 |
36,71 |
0,08 |
0,07 |
0,05 |
45 |
39,18 |
37,97 |
36,76 |
0,09 |
0,09 |
0,09 |
44 |
39,27 |
38,06 |
36,85 |
0,09 |
0,09 |
0,09 |
43 |
39,36 |
38,15 |
36,94 |
0,09 |
0,09 |
0,09 |
42 |
39,45 |
38,24 |
37,03 |
0,09 |
0,09 |
0,09 |
41 |
39,54 |
38,33 |
37,12 |
0,09 |
0,09 |
0,09 |
40 |
39,63 |
38,42 |
37,21 |
0,09 |
0,09 |
0,09 |
39 |
39,72 |
38,51 |
37,3 |
0,09 |
0,09 |
0,09 |
38 |
39,81 |
38,6 |
37,39 |
0,09 |
0,09 |
0,09 |
37 |
39,9 |
38,69 |
37,48 |
0,09 |
0,09 |
0,08 |
36 |
39,99 |
38,78 |
37,56 |
0,09 |
0,1 |
0,13 |
35 |
40,08 |
38,88 |
37,69 |
0,08 |
0,07 |
0,05 |
34 |
40,16 |
38,95 |
37,74 |
0,09 |
0,09 |
0,09 |
33 |
40,25 |
39,04 |
37,83 |
0,09 |
0,09 |
0,09 |
32 |
40,34 |
39,13 |
37,92 |
0,09 |
0,09 |
0,08 |
31 |
40,43 |
39,22 |
38 |
0,09 |
0,1 |
0,12 |
30 |
40,52 |
39,32 |
38,12 |
0,08 |
0,08 |
0,1 |
29 |
40,6 |
39,4 |
38,22 |
0,08 |
0,06 |
0 |
28 |
40,68 |
39,46 |
38,22 |
0,1 |
0,12 |
0,17 |
27 |
40,78 |
39,58 |
38,39 |
0,08 |
0,07 |
0,05 |
26 |
40,86 |
39,65 |
38,44 |
0,09 |
0,09 |
0,08 |
25 |
40,95 |
39,74 |
38,52 |
0,09 |
0,1 |
0,13 |
24 |
41,04 |
39,84 |
38,65 |
0,08 |
0,07 |
0,05 |
23 |
41,12 |
39,91 |
38,7 |
0,09 |
0,09 |
0,08 |
22 |
41,21 |
40 |
38,78 |
0,09 |
0,1 |
0,13 |
21 |
41,3 |
40,1 |
38,91 |
0,08 |
0,07 |
0,04 |
20 |
41,38 |
40,17 |
38,95 |
0,09 |
0,1 |
0,13 |
19 |
41,47 |
40,27 |
39,08 |
0,08 |
0,07 |
0,05 |
18 |
41,55 |
40,34 |
39,13 |
0,09 |
0,09 |
0,08 |
17 |
41,64 |
40,43 |
39,21 |
0,09 |
0,1 |
0,13 |
16 |
41,73 |
40,53 |
39,34 |
0,08 |
0,07 |
0,04 |
15 |
41,81 |
40,6 |
39,38 |
0,09 |
0,1 |
0,13 |
14 |
41,9 |
40,7 |
39,51 |
0,08 |
0,07 |
0,04 |
13 |
41,98 |
40,77 |
39,55 |
0,09 |
0,1 |
0,13 |
12 |
42,07 |
40,87 |
39,68 |
0,08 |
0,07 |
0,06 |
11 |
42,15 |
40,94 |
39,74 |
0,09 |
0,08 |
0,07 |
10 |
42,24 |
41,02 |
39,81 |
0,1 |
0,09 |
-0,13 |
9 |
42,34 |
41,11 |
39,68 |
0,11 |
0,31 |
1,29 |
8 |
42,45 |
41,42 |
40,97 |
-0,09 |
-0,67 |
-1,85 |
7 |
42,36 |
40,75 |
39,12 |
0,49 |
0,51 |
1,07 |
6 |
42,85 |
41,26 |
40,19 |
0,47 |
-0,05 |
0,28 |
5 |
43,32 |
41,21 |
40,47 |
0,99 |
-0,38 |
-3,71 |
4 |
44,31 |
40,83 |
36,76 |
2,36 |
2,95 |
4,13 |
3 |
46,67 |
43,78 |
40,89 |
5,99 |
6,1 |
6,21 |
2 |
52,66 |
49,88 |
47,1 |
5,97 |
5,62 |
5,28 |
1 |
58,63 |
55,5 |
52,38 |
0,08 |
0,07 |
0,05 |
Из полученных данных построим график распределения разницы температур по высоте колонны.
Рисунок. 1 - График распределения ∆T по высоте колонны при переменном расходе исходной смеси: 1 – при нормальном расходе исходной смеси; 2 – изменение расхода исходной смеси на +5%; 3 – изменение расхода исходной смеси на +10%.
По графику была определена контрольная тарелка, ею является тарелка №3.
