Методы получения наночастиц и наноматериалов
Журнал: Научный журнал «Студенческий форум» выпуск №12(33)
Рубрика: Технические науки
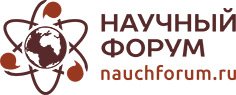
Научный журнал «Студенческий форум» выпуск №12(33)
Методы получения наночастиц и наноматериалов
Alexey Yatsutsenko
undergraduate, school of Engineering, FEFU, Russia, Vladivostok
Аннотация. В данной статье поднимаются такие вопросы как: ноночастицы, нанометериалы, и методы их получения Она будет полезна для тех, кто только начинает знакомство с новым объектом научных исследований, таким как наноматериалы.
Ключевые слова: наноматериалы, наночастицы, нанотехнологии,методы получения.
Abstract: This article raises such questions as: nanoparticles, nanomaterials, and methods of obtaining them. It will be useful for those who are just beginning to get acquainted with a new object of scientific research, such as nanomaterials.
Keywords: nanomaterials, nanoparticles, nanotechnologies, methods of production.
В настоящее время, со стороны машиностроительных предприятий, интерес к новому классу материалов очень сильно увеличился. Происходит это во многом из-за свойств, которыми они обладают.
Но прежде чем переходит к их использованию и внедрению новых материалов (наноматериалов) в машиностроении, необходимо изучить методы получения этих материалов.
Это позволит получить представление о структуре этих материалов и даст представление, где именно в машиностроении их можно будет использовать.
Методы получения наноматериалов, можно разделить на несколько групп: методы порошковой металлургии; методы поверхностных технологий, для создания наноструктурных слоев; методы, в основе которых лежит интенсивная пластическая деформация.
Для области машиностроения, по моему мнению, наиболее подходящими являются методы на основе порошковой металлургии, так как данные методы дают стабильный результат и высокое качество материала, и методы для создания наноструктурных слоёв, так как данные методы позволят укрепить изделие полученные традиционными технологиями, что дешевле, чем создание изделия с нуля.
В свою очередь, методы порошковой металлургии можно разделить на две группу: методы направленные на получение нанопорошков, и методы формования из них изделий.
В рамках данной статьи, рассматриваться будет только первая группа методов.
Основываясь на источниках [1,2], у методов, направленных непосредственно на получение наночастиц порошков, можно выделить ряд особенностей, которые отличаются от методов, на основе которых, получают порошки с обычным, т.е., превышающем 100 нм, размером частиц:
· зарождение наночастиц, происходит с более высокой скоростью, чем у обычных частиц порошков;
· рост частиц, происходит с очень маленькой скоростью;
· данные методы, позволяют получать частицы, размеры которых не превышают 100 нм;
· диапазон размеров частиц составляет от 5 до 100 нм,
· методы позволяют получать стабильный диапазон размеров части,
· повышенные требования по контролю параметров при получении частиц порошков.
Исходя из источника [3] общей чертой наночастиц порошков, получаемых любым из описанных методов, является то, что наночастицы склонны к объединению в так называемые агрегаты и агломераты. Из-за чего, необходимо учитывать не только размер отдельных наночастиц, но и размеры их объединений.
Четкого терминологического различие между агрегатами и агломератами провести невозможно[6], но считается, что в агрегатах связь между кристаллитами более сильная, а межкристаллическая пористость меньше, а для агломератов соответственно наоборот.
При последующем использовании нанопорошков для формирования изделий, для достижения заданной пористости материалов, агрегатированные порошки требуют более высокой температуры и давления по сравнению с неагрегантными[3].
Все методы получения нанопорошков разделяться на две большие группы. К первой группе относятся методы, в основе которых лежат химические процессы, а ко второй группе, методы на основе физических процессов.
Первая группа, состоит также из ряда методов, которые будут описаны ниже, взяты из общедоступных источников [2,4].
Первым рассмотрим методы химического осаждения из паровой фазы.
Данная группа методов основана на использовании химических реакций соединений металлов, находящихся в газовой фазе. У данного метода можно выделить два основных варианта протекания химических реакций.
При первом варианте соединения метолов разлагаются с образованием твердого осадка в виде нанопорошка и газообразных веществ. Во втором варианте, соединения металлов вступают в химические реакции между собой, и происходит образование частиц нанопорошка и газообразных веществ. В качестве исходного сырья могут быть использоваться галогениды (главным образом хлориды) металлов, алкильные соединения, карбонилы, оксихлориды. Размер получаемых частиц может регулироваться температурой и скоростью осаждения.
По такой технологии получают нанопорошки кремния, бора, оксидов титана, циркония, алюминия, нитриды, карбиды и карбонитриды кремния и диборид титана.
Данный метод позволяет получать частицы нанопрошка в диапазоне от 20 до 600 нм.
Следующая группа методов – это методы, в основе которых лежит высокоэнергетический синтез[7].
Эта группа методов основана на использовании реакций, которые происходят на высокой скорости в условиях, далеких от равновесия при высокоэнергетическом воздействии.
Для получения наночастиц порошков используются два основных метода: детонационный и плазмохимический.
Детонационный метод основан на воздействии ударной волны с давлением до нескольких десятков ГПа на смесь исходных реагентов. На основе этого метода получают алмазный нанопорошок со средним размером частиц 4 нм. Получают его из смеси графита с металлами порошка, путем взрыва органических веществ с высоким содержанием углерода и низким содержанием кислорода.
Плазмохимический метод проводят с использованием низкотемпературной плазмы дугового или тлеющего разряда.
Металлы, галогениды или другие соединения используются в качестве исходного сырья.
Из-за достаточно высокой температуры плазмы (до 10000 К) и высоких скоростей взаимодействия, исходные вещества переходят в газообразное состояние, а затем конденсируются и выпадают в виде нанопорошка с частицами правильной формы от 10 до 200 нм.
Далее рассмотрим ряд методов относящихся ко второй группе, основанных на физических процессах. Данные методы изложены в общедоступных источниках [2,4]
Методы физического осаждения из паровой фазы.
В настоящее время методы получения нанопорошков, основанные на физическом осаждении из паровой фазы, получили широкое распространение. Это связано с тем, что технологии испарения вещества с помощью различных источников энергии высокой интенсивности и последующего осаждения его из паровой фазы достаточно хорошо развиты и изучены.
К плюсам данного метода можно отнести: легко контролируется процесс осаждения и также данные методы обеспечивают высокие требования к чистоте полученного нанопорошка, особенно при использовании камер с контролируемой атмосферой.
Наиболее широкое распространение получили вакуумные камеры или камеры, заполненные инертными газами - гелием или аргоном, ксеноном.
При испарении металлов в вакууме или инертном газе атомы металла, прошедшего в газовую фазу (пары), имеют тенденцию объединяться в частицы размером порядка нескольких нанометров, которые затем осаждаются на охлажденную подложку.
Эта группа методов позволяет получать сложнолегированные порошки, сплавы заданного состава, могут быть получены либо путем испарения предварительно легированного материала, либо путем одновременного испарения отдельных компонентов.
Размер частиц полученных порошков может варьироваться от 5 до 100 нм, в зависимости от выбранного метода и параметров процесса.
Механическое размельчение.
Механическое размельчение частиц материала является одним из наиболее распространенных способов получения нанопорошков.
Особенно легко получить порошки на основе хрупких материалов. Порошки из пластичных, высокопрочных и аморфных материалов получить труднее. В этом случае увеличивается опасность чрезмерного нагрева материала и загрязнения его продуктами износа рабочих частей технологического оборудования.
При механическом размельчении с использованием мельниц, уменьшение размера частиц материала происходит в результате его интенсивного раздавливания между рабочими частями мельницы.
В зависимости от типа материала и требуемых свойств нанопорошков используются планетарные, шаровые и вибрационные мельницы.
Средний размер частиц полученных порошков составляет от 5 до 200 нм.
Подводя небольшой итог по методам получения наночастиц порошков, на основе порошковой металлургии, стоит отметить, что данные методы направлены на создание объемноструктурированных изделий, методами формования изделий из нанопорошков.
Но также, немаловажным является обеспечение машиностроительных предприятий, соответствующим режущим инструментом. Обеспечить таким инструментом, по моему мнению, помогут методы, в основе которых лежат технологии обработки поверхностей.
Анализ и описание данных технологий, осуществлялся на основе источников [2,5].
Технологии обработки поверхности материалов в настоящее время являются одними из наиболее развивающихся областей науки о материалах. Методы, связанные с созданием на поверхности материалов, особенно металлических, модифицированных слоев, были хорошо изучены, проработаны и широко используются на практике.
Многие из этих методов или их дополненные варианты можно рассматривать как нанотехнологические методы, поскольку они позволяют создавать наноразмерные и наноструктурные слои на поверхности материалов, что очень подходит для создания более прочного и эффективного режущего инструмента.
Наиболее широкое распространение получили так называемые методы лазерной группы.
Наноструктурированное состояние при этих методах достигается в тонких поверхностных слоях металлических материалов или изделий, полученных за счет традиционных технологий, под воздействием вещества с высокоплотным лазерным излучением.
Под действием лазерного облучения поверхностный слой материала толщиной 0,1 ... 100 мкм очень быстро расплавляется, плотность энергии лазерного излучения составляет 103…1010 Вт/см2 , а затем затвердевает при скоростях охлаждения 104…108 К/с.
В тоже время основная масса металлического материала не нагревается из-за короткой продолжительности теплового воздействия и обеспечивает высокую скорость теплоотвода, что приводит к тому, что изделие не теряет свою первоначальную форму и не требует последующей доработки.
Высокие скорости охлаждения позволяют достичь нанокристаллической структуры.
На основании проделанной работы, можно сделать небольшое заключение.
Так же данная статья направлена на дальнейшее изучение материалов по данной теме, так как в ней изложена только малая часть всех возможных методов. А так же только упомянуты, но не рассмотрены методы формовки изделий из нанопорошков.
