Исследование качества покрытия на внутренней поверхности пластически деформированных труб методом ранговой корреляции
Журнал: Научный журнал «Студенческий форум» выпуск №12(33)
Рубрика: Технические науки
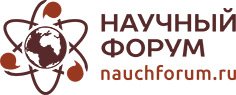
Научный журнал «Студенческий форум» выпуск №12(33)
Исследование качества покрытия на внутренней поверхности пластически деформированных труб методом ранговой корреляции
Investigation of the coating quality on the inner surface of plastically deformed pipes by the method of rank correlation
Maxim Myshkin
student of Izhevsk State Technical University named after M.T. Kalashnikov, Russian Federation, Izhevsk
Аннотация. Для получения необходимых свойств данного материала в современной металлургии применяют такие операции, как нанесение покрытия на изделие, которое защищает изделие от коррозии и других внешних воздействий, и обработка материалов давлением для получения изделий повышенной прочности. Оценить качество готовой продукции можно осуществить методом ранговой корреляции, при этом учитывая оценки квалифицированных специалистов-экспертов.
Abstract. To obtain the necessary properties of this material in modern metallurgy, operations such as coating the product, which protects the product against corrosion and other external influences, and the processing of materials by pressure to produce articles of increased strength are used. To assess the quality of finished products can be carried out by the method of rank correlation, while taking into account the assessments of qualified experts.
Ключевые слова: метод термического напыления; вакуумное хромирование; толщина покрытия; радиальная ковка; радиально-ковочная машина; метод ранговой корреляции.
Keywords: thermal spraying method; vacuum chrome plating; thickness of the coating; radial forging; radial forging machine; method of rank correlation.
В конструировании современных приборов и машин большое внимание уделяют необходимости повышения надежности, износостойкости, коррозионной стойкости, долговечности и прочности выпускаемых изделий. Часто определяющую роль в составных частях изделий играет не сам материал, а его поверхностный слой, который должен удовлетворять тем или иным техническим требованиям. На практике для получения определенных свойств материалов используют специальные покрытия, обеспечивающие нужную совокупность параметров этого материала.
Большой интерес представляют хромовые покрытия. Хромирование распространено в машиностроении и приборостроении, потому что оно позволяет получить высокую твердость покрытия, низкий коэффициент трения, высокую износостойкость и коррозионную стойкость. Несмотря на то, что хром относится к электроотрицательным металлам, он может сильно пассивироваться, благодаря чему приобретает свойства благородных металлов. Пассивная пленка окислов предохраняет хромовое покрытие от потускнения.
Также немаловажное значение, определяющее в большей степени прочность материала, имеет способность переносить значительное внешнее воздействие без особых изменений во внутренней структуре, например при ударных растягивающих нагрузках при выстрелах в артиллерийских орудиях или воздействии высокого давления (около 20 атм.) на топливные трубки в дизельных двигателях. В этих целях целесообразно упрочнение материала методом изменения его внутренней структуры, например с помощью термической обработки или пластического деформирования.
В частности была изучена технология радиальной ковки в холодном виде, которая используется при обработке деталей для предприятий, изготавливающих буровую технику, для деталей атомной промышленности и других материалов с труднодостижимыми показателями разнотолщинности (разностенности).
В данной работе представлен анализ качества пластически деформированных стальных трубок с хромовым покрытием на их внутренней поверхности в зависимости от толщины этого покрытия методом ранговой корреляции.
Методы нанесения покрытий в условиях разряжения (вакуума), в зависимости от особенностей, превращения материала покрытия в парообразное состояние с последующей конденсацией на защищаемой поверхности, часто называемой подложкой, можно разделить на три вида: катодное распыление, термическое напыление и ионное осаждение.
Рисунок 1. Схема устройства для нанесения покрытия
Было исследовано несколько трубок с разной толщиной хромового покрытия, нанесенного методом термического напыления с резистивным нагревом испаряемого материала (хрома). Схема устройства для нанесения покрытия представлена на рисунке 1. Этот метод обладает рядом преимуществ по сравнению с другими. Во-первых, высокая производительность и возможность без существенных переделок вакуумной установки получения покрытий из различных металлов и сплавов. Во-вторых, покрытия, нанесенные в вакууме, обладают высокой степенью чистоты и однородностью, а также в них исключена водородная хрупкость, которая имеется у гальванических покрытий из-за водорода, выделяющегося в процессе электролиза. В-третьих, метод позволяет получать послойные и комбинированные покрытия из металлов практически на любом материале.
К минусам данного метода можно отнести следующее: необходимость предварительного нагрева защищаемой поверхности для получения надежного сцепления покрытия с основой, низкий коэффициент полезного использования испаряемого металла и трудность получения однородного по толщине покрытия на деталях сложной конфигурации.
К главным физическим и технологическим параметрам процесса нанесения покрытий в вакууме относятся: температура конденсации, скорость конденсации, температура испарения и физическое состояние частиц пара, степень вакуума, угол падения потока атомов, способ испарения и материал тигля, последующая термическая обработка и толщина покрытия.
Толщина покрытия прежде всего влияет на коррозионную стойкость этого покрытия. В литературе существуют данные о коррозионном поведении вакуумных хромовых покрытий на стали в различных условиях, в том числе атмосферных. Например, результаты ускоренных коррозионных испытаний по методу CASS в камере тропического климата, в камере солевого тумана, во влажной атмосфере показывают, что изделия с покрытием толщиной 10 – 15 мкм обладают наибольшим индексом коррозионной стойкости. Почему же именно такая толщина хромового покрытия является наиболее коррозионно стойкой?
Ввиду того, что хромовые покрытия катодны по отношению к стали, коррозионные поражения возникают прежде всего в местах сквозных пор покрытия. Эти поры очень многочисленны в покрытиях толщиной до 5 мкм. С увеличением толщины покрытия количество пор уменьшается и покрытие толщиной 15 – 20 мкм практически беспористо. Поэтому защитные свойства хромовых покрытий с увеличением толщины от 5 до 20 мкм улучшаются, а при толщинах более 20 мкм ухудшаются, несмотря на уменьшение пористости. Визуальный осмотр изделий с покрытием 30 – 40 мкм после испытаний показал, что для них характерно вспучивание и растрескивание из-за больших напряжений сжатия.
Если рассматривать износостойкость покрытия, то в этом случае также наиболее стойкой к разрушению является покрытие толщиной 10 – 15 мкм. Для тонких покрытий после формирования первых слоев структура и свойства покрытия определяются материалом подложки (в нашем случае сталь), и поэтому тонкое покрытие практически не влияет на износостойкость изделия, которая определяется износостойкостью подложки.
Для покрытий толщиной более 20 мкм износостойкость уже определяется свойствами сформировавшегося слоя хрома, который имеет уже отличную от материала подложки собственную структуру. Покрытия большой толщины уступают по износостойкости покрытиям толщиной 10 – 15 мкм по нескольким причинам.
Во-первых, с возрастанием толщины хрома уменьшается диффузия внешних слоев покрытия с подложкой, и поэтому в этих слоях большая концентрация хрома, что приводит к возникновению больших внутренних напряжений, что в свою очередь приводит к разрушению покрытия при воздействии внешних нагрузок.
Во-вторых, процесс образования покрытия происходит с возникновением на подложке островков конденсированной фазы. С поступлением атомов на подложку происходит рост островков и образование сплошной пленки. Для толстых покрытий дальнейший рост толщины происходит с образованием последующих пленок, которые образуются аналогично первому. Но они уже конденсируются не на материал подложки, а на смешавшийся с атомами подложки в процессе диффузии слой хрома. Таким образом, адгезия внешних слоев покрытия с материалом подложки хуже, поэтому покрытия толщиной более 30 мкм могут вспучиваться в местах слабой адгезии при воздействии внешних нагрузок.
Таким образом, анализируя коррозионно стойкие и износостойкие качества хромового покрытия, можно уже до получения результатов исследования качества внутренней поверхности трубчатых пластически деформированных изделий методом ранговой корреляции сделать вывод, что наиболее высоким качеством обладают покрытия толщиной 10 – 15 мкм.
Преобладающее значение как при формировании поверхностных слоев, так и при эксплуатации изделий с покрытиями имеют процессы силового воздействий. Целенаправленное силовое воздействие на изделие с покрытием в процессах обработки материалов давлением (ОМД) производится с целью придания ему требуемого комплекса геометрических и физико-механических свойств.
Производство металлических изделий с покрытиями возможно формированием покрытия на конечные геометрические размеры и на заготовку с последующей деформацией слоистой композиции до готового размера. Производство по второй схеме позволяет получить изделия с повышенным уровнем ряда функциональных показателей: точности геометрических размеров изделия, параметров поверхности и защитных свойств покрытия (за счет уплотнения и увеличения адгезионных показателей) и др.
С помощью процесса радиальной ковки можно существенно снизить цену производства деталей сложной формы по сравнению с получением их процессами резания и одновременно обеспечить повышенные прочностные характеристики изделий.
Детали, полученные в процессе радиальной ковки, обладают следующими преимуществами:
■Благодаря высокой точности получаемой поверхности, изделия в большинстве случаев не требуют дополнительной механической обработки, что приводит к экономии металла и снижает себестоимость производства.
■ Благодаря радиальной ковке можно добиться больших степеней деформации по сравнению с обычными процессами ОМД без применения промежуточного отжига, что в свою очередь снижает количество требуемых операций для изготовления конечной детали.
При холодном деформировании степень деформации приповерхностного слоя в несколько раз превышает деформации в объеме металла, что в совокупности с высокой интенсивностью деформации сдвига приводит ,с одной стороны, к быстрому наклепу приповерхностного слоя, а с другой стороны, к интенсивному тепловыделению в этом слое.
Так как деформирование трубы с внутренним покрытием в процессе радиальной ковки происходит с внешней стороны, то степень деформации при приближении к внутренней поверхности уменьшается пропорционально толщине стенки трубы. Следовательно, внутренняя поверхность полученных после радиальной ковки в холодном виде труб практически не будет отличаться от внутренней поверхности исходных заготовок. Но все же в конечном итоге внутреннее покрытие окажется под влиянием сжимающих напряжений, которые приведут к сжатию имеющихся в нетолстых покрытиях (до 20 мкм) пор и к резкому возрастанию коррозионной стойкости.
Таким образом, можно утверждать, что технология радиальной ковки способствует улучшению физико-механических свойств трубы, а также увеличению коррозионной стойкости внутреннего покрытия трубы.
В практике научных исследований при изучении сложных физико-химических процессов большое значение на начальном этапе имеет сбор и объективная обработка имеющейся информации об объекте. Однако объективной информации часто бывает недостаточно для проведения исследований. В то же время у научных коллективов и отдельных специалистов накоплен богатый практический опыт в данной или близкой области, который может быть использован на предварительном этапе изучения объекта.
Таким образом, помимо общепринятых методов исследования, например, изучения физико-химического механизма процесса, его технологии и применения экспериментально-статистических методов, исследователь естественно, использует такие субъективные данные о процессе, как мнения технологов и операторов, управляющих данным объектом. При большом числе влияющих факторов мнения операторов и технологов относительно степени влияния этих факторов на процесс, могут расходиться. Поэтому возникает задача объективной обработки подобной субъективной информации, которая может быть решена методами ранговой корреляции.
Наиболее интересным практическим приложением ранговой корреляции является вопрос о рассмотрении корреляционной связи нескольких ранжированных рядов. Коэффициент ранговой корреляции показывает насколько значения нескольких ранжированных рядов связаны друг с другом. Теоретически и практически выгоднее применять коэффициент ранговой корреляции по Спирмену ρ. Значимость коэффициента ранговой корреляции обычно определяют по 5%-ному уровню значимости P0. Сравнивая эти величины можно сделать вывод о значимости коэффициента корреляции и о том, являются ли значения ранжированных рядов взаимосвязанными или они могли возникнуть случайно.
Толщина покрытия может оказывать влияние на геометрические размеры и качество канала готовой детали, прежде всего на операции радиального обжатия. Результаты исследования экспертами качества канала ствола после радиального обжатия в зависимости от толщины покрытия приведены в таблице 1.
Проранжировав в таблице 1 значения строк толщина покрытия и сумма оценок, определим коэффициент ранговой корреляции по Спирмену для этих двух ранжированных рядов:
где n – число объектов (труб).
Для n = 10 вероятность случайного появления S = 36 при отрицательном коэффициенте корреляции равна 0,0053. Это меньше принятого P0 = 0,05, значит величина ρ = -0,78 не может возникнуть случайно и приходится считать ρ = -0,78 значимым. Таким образом, гипотезу о наличии связи между толщиной покрытия и суммой оценок экспертов принимаем. Причем коэффициент корреляции отрицательный, следовательно, чем меньше толщина покрытия, тем больше сумма оценок и качество покрытия.
Таблица 1.
Влияние толщины покрытия на качество канала ствола после операции радиального обжатия
№ труб. заготовки |
28 |
27 |
25 |
30 |
34 |
37 |
32 |
33 |
35 |
24 |
Толщина покрытия, мкм |
5 |
6,2 |
7,3 |
8,5 |
10 |
12,5 |
15 |
14 |
20 |
21,5 |
Эксперт 1 |
5 |
3 |
3 |
3 |
4 |
2,5 |
2 |
1 |
1 |
1 |
Эксперт 2 |
4 |
3 |
3 |
3 |
5 |
2,5 |
2 |
1 |
1 |
1 |
Эксперт 3 |
4 |
3,5 |
3 |
3,5 |
5 |
2,5 |
2 |
1 |
1 |
1 |
Эксперт 4 |
4 |
4 |
3 |
3,5 |
5 |
2,5 |
2 |
1 |
1 |
1 |
Эксперт 5 |
5 |
4 |
4 |
3 |
5 |
2,5 |
2 |
1 |
1 |
1 |
Сумма оценок |
22 |
17,5 |
16 |
16 |
24 |
12,5 |
10 |
5 |
5 |
5 |
Если есть зависимость между толщиной покрытия и оценками экспертов, то можно определить толщину покрытия с самым высоким качеством. Для этого необходимо оценить степень согласия мнений исследователей о ранжировании объектов по данному признаку, которая может быть выражена через коэффициент конкордации W.
W = 0 означает, что связи между ранжировками исследователей не существует.
W = 1 означает, что все исследователи одинаково ранжируют объекты по данному признаку.
В случае, если ранжировки содержат совпавшие ранги, формула для вычисления W выглядит так:
W = ,
где
– число повторений каждого ранга в j – том ряду;
m – количество исследователей (экспертов);
n – количество объектов исследования.
Коэффициент конкордации также требует оценки значимости. Для этого при n>7 можно использовать критерий Пирсона (χ2), значение которого находят по формуле:
χ2 = , где d = (
)
Рассчитаем коэффициент конкордации. Для этого проведем ранжирование этих объектов по десятибалльной шкале в соответствии с оценками экспертов. Полученные данные занесем в таблицу 2:
Таблица 2.
Полученные данные
№ труб. заготовки |
28 |
27 |
25 |
30 |
34 |
37 |
32 |
33 |
35 |
24 |
Эксперт 1 |
10 |
7 |
7 |
7 |
9 |
5 |
4 |
2 |
2 |
2 |
Эксперт 2 |
9 |
7 |
7 |
7 |
10 |
5 |
4 |
2 |
2 |
2 |
Эксперт 3 |
9 |
7,5 |
6 |
7,5 |
10 |
5 |
4 |
2 |
2 |
2 |
Эксперт 4 |
8,5 |
8,5 |
6 |
7 |
10 |
5 |
4 |
2 |
2 |
2 |
Эксперт 5 |
9,5 |
7,5 |
7,5 |
6 |
9,5 |
5 |
4 |
2 |
2 |
2 |
d |
18,5 |
10 |
6 |
7 |
21 |
-2,5 |
-7,5 |
-17,5 |
-17,5 |
-17,5 |
d2 |
342,25 |
100 |
36 |
49 |
441 |
6,25 |
56,25 |
306,25 |
306,25 |
306,25 |
Найдем сумму квадратов отклонений рангов относительно среднего значения рангов и вычислим коэффициент конкордации:
S(d2) = 1949,5
W = .
Проведем оценку значимости коэффициента конкордации по критерию Пирсона (χ2), так как количество объектов n = 10>7:
χ2 = 44,25
Находим табличное значение критерия Пирсона для 5%-ного уровня значимости и числе степеней свободы ν = n – 1:
χ2табл. = 16,92.
Так как χ2 > χ2табл. , то гипотеза о наличии связи (согласия) между экспертами при ранжировании объектов принимается. При этом, так как коэффициент конкордации близок к единице, получается, что все эксперты почти одинаково оценивают качество канала трубы. Следовательно, можно сделать вывод о том, что более лучшее качество имеет покрытие с наибольшей суммой оценок экспертов, то есть наиболее качественный канал получается при радиальном обжатии трубчатых заготовок с хромовым покрытием толщиной 10 мкм. Таким образом, наши предположения о том, что для стальных трубок, подвергнутых радиальному обжатию, наилучшим качеством и свойствами будет обладать хромовое покрытие толщиной 10 – 15 мкм подтверждаются на практике.
