К вопросу снижения пульсации давления в гидросистеме
Конференция: X Студенческая международная научно-практическая конференция «Молодежный научный форум»
Секция: Технические науки
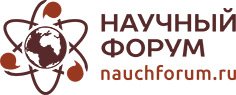
X Студенческая международная научно-практическая конференция «Молодежный научный форум»
К вопросу снижения пульсации давления в гидросистеме
С увеличением технологической точности и уменьшение вибро и шумовых характеристик возрастает требования, предъявляемые к гидравлическому оборудованию.
Важной проблемой на сегодняшний день является необходимость создания малошумных гидравлических систем кораблей, судов, атомной энергетики и объектов общепромышленного значения как для обеспечения увеличения ресурса работы установок и оборудования, подверженного выходу из строя в следствии вибрации, так и улучшения условий работы обслуживающего персонала. Немало важную роль играет и уменьшение пульсационных характеристик гидросистем и как следствие уменьшение уровня акустического шума в строении подводных лодок. В боевых – малошумных, режимах использования их подводная шумность и уровень помех формируются за счёт механических источников работающих механизмов. Снижение виброактивности и создание эффективных средств их виброподавления и вибродемпфирования приводит к тому, что формирование гидроакустического поля и уровни шума на судах становятся определяющим фактором незаметности.
Наиболее распространённым методом уменьшения пульсационных характеристик гидросистем является использование воздушных колпаков (гидроаккумуляторов).
Воздушный колпак представляет собой камеру, наполовину заполненную воздухом, давление которого примерно равно давлению жидкости в системе. За счёт деформации воздуха, колпак должен обеспечить более равномерное движение жидкости и спокойную работу насоса. [1].
Достоинствами являются: простота изготовления, удовлетворительные качества сглаживания пульсаций давления.
Недостатки воздушных колпаков – их большие габаритные размеры, что, как следствие, увеличивает и габаритные, и массовые характеристики гидроустановок.
Другим вариантом снижения пульсационных характеристик в гидросистемах является применение приёма дросселирования потока жидкости. Однако, при этом резко возрастает потребляемая мощность, что позволяет использовать данный метод лишь в гидросистемах с малыми расходными характеристиками [2].
В частности большое влияние на шумовые и вибрационные характеристики гидравлического оборудования оказывает неравномерность подачи жидкости, пульсация давления, вызванные конструктивными особенностями качающего органа.
В связи с этим встает вопрос нахождения таких технологических решений конструирования качающего органа, в которых теоретически подачи равномерна (насосы с вращающимися поршнями рис.1 ).
Рис. 1. Схемы насосов с вращающимися поршнями
Профили роторов таких насосов выполнены так, что они плотно замыкаются между собой и с колодцами корпуса [3].
При направлении вращения роторов, указанном на рис. 1 а, объем верхней камеры а (отмечено точечной штриховкой) будет уменьшаться и жидкость из нее вытесняться, а объем нижней камеры увеличиваться и жидкость будет в нее засасываться.
Рабочий объем (подача за один оборот) двухроторного насоса (рис. 1 а) может быть приближенно приравнен объему прямоугольного кольца высотой b, описанного окружностями радиусами R и r
(1)
где R - внешний радиус (радиус расточки корпуса); r - радиус внутренней части (впадин ротора); b - ширина ротора.
В соответствии с этим расчётная подача
(2)
Поскольку подобные роторы не могут передавать момент с ведущего ротора на ведомый, они соединяются между собой шестеренной парой, расположенной вне корпуса насоса.
В насосе, состоящем из двух роторов с тремя зубьями (выступами) (рис. 1 б), контакт каждого из роторов происходит по двум точкам с и d. Профили выступов образуются в этом насосе кривыми, выполненными так, чтобы контакт выступов при их повороте происходил на возможно большем угле.
На рис. 1 в показана схема насоса с вращающимися поршнями в виде двух обкатывающихся роторов a и b иного профиля. Роторы соединены внешней шестеренной связью и обкатываются по окружностям, образованным соответственно диаметрами D и d. Подача такого насоса определится как
(3)
где b и n - высота роторов и частота их вращения.
Ввиду того, что в приведенное выражение входят лишь параметры с постоянными размерами, расчетная подача жидкости происходит без пульсаций.
Но такие насосы высокотехнологичны и рассчитываются на сравнительно небольшие нагрузки. В следвии износа синхронизирующих шестерней такие насосы подвержены изменению заложенной конструктором кинематики, что приводит к появлению неравномерности подачи, увеличению износа и в конечном итоге выходу из строя рабочих органов.
Для синтеза нового технического решения была произведена дивергенция аналогов («разборка» их на конструктивные элементы с описанием функции каждого), исключение и замена проблемных элементов на технические решения, выполняющие заданные функции, но не имеющие обнаруженных недостатков, после чего осуществлена конвергенция («сборка») конструкции.
Ниже на рис (2 – 5) - представлена принципиальная схема данного технического решения [4].
Насос состоит из корпуса 1, основного 2 и дополнительного 3 цилиндров, имеющих одинаковый диаметр и высоту, приводного 4, вспомогательного 5 и дополнительного 6 валов, на концах которых имеются соответственно конические шестерни 7, 8 и 9, образующие кинематическую связь между приводным валом 4, вспомогательным валом 5 и дополнительным валом 6.
В цилиндрах 2 и 3 размещены основной 10 и дополнительный 11 роторы, имеющие выступы 12 и 13, ориентированные под углом 1800 друг к другу, радиусы выступающей части которых одинаковы и равны радиусам цилиндров 2 и 3. Роторы 10 и 11 соединены с валами 4 и 6 с помощью шпонок 14 и 15. . Плоскость дополнительного цилиндра 3 параллельна плоскости вращения основного ротора 10.
На вспомогательном валу 5 установлен соединенный с помощью шпонки 16 вспомогательный ротор 17 в плоскости, находящейся под углом 900 к плоскости вращения основного ротора 10. Ротор 17 имеет впадину 18 для размещения выступов 12 и 13 при синхронном и противоположно направленном вращении валов 4 и 6 с роторами 10 и 11, и его рабочая торцовая поверхность, обращенная в сторону цилиндров 2 и 3, расположена относительно оси вращения основного 10 и дополнительного 11 роторов на расстоянии, равном радиусу этих роторов.
В крышках 24 и 25 расположены соответственно соединенные между собой коммуникациями (на рисунках условно не показаны) всасывающие окна 27 и 28, соединенные с линией всасывания (на рисунке условно не показана) а также нагнетательные клапаны 29 и 30 (см. также рис. 3 и 4), соединенные с линией нагнетания (на рисунке условно не показана). Контуры всасывающих окон и нагнетательных клапанов показаны штриховыми линиями.
Валы 3, 5 и 6 вращаются в подшипниковых узлах 19, 20 и 21, болтовые соединения 22 и 23 служат соответственно для стяжки передней 24 крышки, цилиндров 2 и 3 и задней крышки 25, а также для крепления колпака 26.
На одной из торцовых стенок дополнительного цилиндра 3, например, на торце задней крышки 25 (рис. 4), изготовлены две сбрасывающие канавки 32 и 33, выполненные в виде углублений в этих стенках, и перекрывающие соответственно всасывающее окно 28 и нагнетательный клапан 30.
Направление вращения роторов 10 и 11 показано сплошными жирными стрелками. Направление вращения валов 4, 5 и 6 - фигурными стрелками.
На рис. 3 и 4 угол α – угол между положениями выступов 11 и 12 до и после их зацепления с выемкой вспомогательного ротора, угол β – угол между положениями выступа 13, в которых он сначала отсекает канавку 32 от остального объема цилиндра 3, а потом соединяет канавку 33 со всем объемом цилиндра 3.
Работа основного ротора 10 обеспечивает непрерывную и постоянную (постоянная величина расхода) подачу рабочей жидкости на протяжение (360 – α) градусов поворота основного вала 4. В течение поворота ротора 10 на α градусов подача рабочей жидкости полностью отсутствует.
Дополнительный ротор 11 с выступом 13 работает в противофазе (рис. 4 и 5) основному ротору 10. В то время, пока основной ротор 12 производит сжатие-нагнетание рабочего тела с постоянным расходом, находясь по углу поворота в промежутке (360 – α), дополнительный ротор 11 находится по углу поворота в промежутке (360 –β), когда со стороны его торца всегда есть канавка 33 или 34, или в радиальном направлении – впадина 18, которые позволяют рабочему телу свободно протекать мимо выступа 13, в результате чего в этом промежутке в цилиндре 3 постоянно находится рабочая жидкость под давлением всасывания, т.к. полость цилиндра постоянно сообщена со всасывающим окном. В идеальном случае угол β равен углу α и расположен строго симметрично этому углу (рис. 4). Как только выступ 12 основного ротора 10 начинает входить в зацепление с впадиной 18, т.е. когда подача рабочей жидкости ротором 10 прекращается, выступ 13 дополнительного ротора 11 уходит из зоны действия канавки 32, отсекая полость цилиндра 3 от всасывающего окна 28. При этом полость цилиндра 3, находящаяся перед выступом 13 (по ходу вращения ротора 11) оказывается геометрически замкнутой и с переменным объемом, т.к. выступ 13 при вращении ротора 11 уменьшает объем этой полости. В этом случае происходит сжатие рабочей жидкости, «отсеченной» от всасывающего окна 28 и нагнетание ее в линию нагнетания через клапан 30. Этот процесс длится до тех пор, пока выступ 13 не войдет в зону действия канавки 33, в результате чего рабочее тело получает возможность обтекать выступ 13, полость цилиндра 3, находящаяся перед выступом 13, соединяется со всасывающим окном 28, давление в полости цилиндра 3 падает до давления всасывания, и нагнетательный клапан 30 закрывается. Подача жидкости в нагнетательную линию машины прекращается.
Таким образом, в нагнетательную линию насоса в течение поворота основного вала 4 на угол (360 – α) и далее на угол β = α (то есть в течение всех 360 градусов поворота) поступает одинаковый и постоянный расход рабочей жидкости.
Такая машина отличается простотой изготовления, как роторов, так и цилиндров. Уплотнение «ротор - вспомогательный ротор» представляет собой сопряжение «радиус – плоскость» и имеет значительно большее гидравлическое сопротивление, чем у ролико-лопасного насоса. Конструкция не требует точной синхронизации роторов.
Исходя из вышерассмотренного разработка гидросистем и в частности гидронасосов с пониженными пульсационными характеристиками является актуальной задачей, решение которой можно искать исходя из комплексного рассмотрения всевозможных средств устранения пульсаций подачи жидкости, уменьшения пульсаций давления, и как следствие, уменьшение вибро и шумовых характеристик, увеличение срока службы рабочих органов насосов и улучшению условий труда персонала, эксплуатирующего данное оборудование.
