Подбор материала уплотняющих манжет плунжера для повышения долговечности штангового глубинного насоса
Конференция: II Студенческая международная научно-практическая конференция «Молодежный научный форум»
Секция: Технические науки
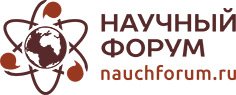
II Студенческая международная научно-практическая конференция «Молодежный научный форум»
Подбор материала уплотняющих манжет плунжера для повышения долговечности штангового глубинного насоса
Введение. Выбор материала является одним из важнейших этапов проектирования, влияющий на прочностные и эксплуатационные свойства, разрабатываемого изделия. Рассмотрим узел трения глубинного штангового насоса невставного типа. От выбранного материала зависит конструктивное оформление плунжера. Конструкция плунжера разрабатывается исходя из свойств материала таким образом, чтобы свести до минимума или полностью устранить вредное влияние отрицательных характеристик материала хрупкость, низкую теплопроводность, гигроскопичность, нестабильность размеров во времени и др. и наиболее полно использовать низкий коэффициент трения и высокую износостойкость материала.
С подобранного материала зависит плодотворное формирование плунжера. Система плунжера разрабатывается, отталкиваясь качеств использованного материала подобным способом, для того чтобы объединить вплоть до минимального количества либо полностью ликвидировать вредоносное воздействие негативных данных использованного материала, невысокую тепло проводимость, гигроскопичность, непостоянность объемов в период и др. и более подробно применять незначительный показатель и значительную износоустойчивость использованного материала.
Недостаточно обоснованный выбор материала для уплотнительных манжет плунжера штангового скважинного насоса, может стать причиной сокращения срока службы пары трения уменьшается, возрастает количество ремонтных работ, а также потери вырабатываемого продукта из-за дополнительных простоев оборудования [1].
Материалы и методы. При выборе материала для манжет плунжера, важнейшим фактором является износостойкость. Износ рабочих поверхностей манжет сверх допустимой величины нарушает точность взаимного расположения цилиндра с плунжером, что приводит к динамической неустойчивости и вибрации, возможности разрушения. Износ проявляется с увеличением давления, контактных напряжений, а коэффициент трения снижается либо остается постоянным до критического значения, соответствующего катастрофическому износу. Физико-механические качества материала манжет должны обеспечивать огромную прочность и упругий контакт при трении, наименьший процент трения, отсутствие тяги к задирам, отличную прирабатываемость. Непосредственно, материал должен иметь необходимую механическую прочность, технологичность и стойкость к коррозийной среде. Материал манжет необходим быть мало дефицитным, его технологическая обработка проста и доступна [2].
Материалы, используемые для манжет глубинных насосов, подразделяются на следующие группы:
А – металлические материалы (коррозионностойкие стали и сплавы, углеродистые и легированные стали, чугуны, цветные металлы, наплавочные сплавы);
Б – материалы на основе углерода;
В – неметаллические высокотвердые материалы;
Г – материалы на основе полимеров, в том числе металлополимерные.
На сегодняшний день в машиностроении обширное применение включают
В современном машиностроении широкое применение находят новые многообещающие материалы с отличительными параметрами. С технологической точки зрения наиболее эффективным является выбор материала с повышенной исходной твердостью и износостойкостью поверхностного слоя, рациональной шероховатостью, высокими жесткостью и усталостной прочностью. При многократном исследовании определено, что в сухом трении и при работе на малых скоростях скольжения наиболее твердые материалы изнашиваются меньше, чем пластичные. Следовательно, на практике выбор указанных параметров в материале может быть затруднен рядом технологических и технико-экономических факторов.
Известны подшипники из твердых порошковых сплавов. С данных использованных материалов изготавливают подшипниковые опоры валов реакторов, втулки цилиндров и штоки поршневых компрессоров, трущиеся пары фронтальных уплотнений, распыляющие форсунки и прочие элементы. Данные использованные материалы различаются значительной стойкостью к износу в кислотах, щелочах и иных химических сферах, а кроме того хорошо функционируют в обстоятельствах шлифующего изнашивания. Более коррозиеустойчивые жесткие сплавы ВК2, ВКЗ и ВК6, сущность кобальта в каковых никак не превосходит 6 %. Наилучшим использованным материалом согласно комплексу качеств, проявляемых при трении в химическом оснащении, считается прочное соединение ВК6, коррозийная устойчивость которого с сокращением шероховатости контактирующих плоскостей значительно увеличивается [3].
Повышение износостойкости пар трения достигается применением пористых металлических материалов, пропитанных фторопластом. Металлический пористый каркас изготовляют спеканием обычных дендритных порошков металлов, полученных электролитическим способом, или спеканием порошков антифрикционных сплавов сферической формы. Обычно используют порошки высокооловянной бронзы, иногда — железа, меди или серебра [4].
Технология изготовления металлофторопластового материала предусматривает спекание на омедненной стальной основе тонкого пористого слоя из частиц сферической формы высокооловянной бронзы с последующей пропиткой пор слоя чистым фторопластом или фторопластом с наполнителем. Процесс пропитки осуществляют таким образом, чтобы антифрикционный материал, заполняющий пустоты бронзового слоя, несколько, выступал за его пределы для образования поверхностного, так называемого приработочного слоя. Стальная основа придает металлофторопластовому материалу высокую прочность, бронзовый пористый каркас обеспечивает быстрый отвод тепла, возникающего при трении, и служит резервуаром для твердой смазки, роль которой играет фторопласт или фторопласт с наполнителем; поверхностный слой антифрикционного материала предотвращает износ сопряженной с цилиндром глубинного насоса и уменьшает трение.
Присутствие службе железная плоскость цилиндра и медно-бронзовые частички металлофторопластового использованного материала распределены тоненьким пластом полимера либо заполненного полимера. Данная, прослойка со временем снашивается, утончается, и в единичны зонах рушится, таким образом, появляется связь среди раздельными медно-бронзовыми частичками и принадлежащей с подшипником поверхностью. Трение материала о материал считается недолгим, так как оно приводит к здешнему увеличению температуры, из-за этого полимер, имеющий значительным коэффициентом термического расширения, вышвыривается с времен медно-бронзового скелета возобновляя и поддерживая единство полимерного покрова.
Таким образом в структуру металлофторопласта входит полимер, следует принимать во внимание присутствие при производстве продуктов деформированием присутствие высоких температур (температура деформирования обязана являться больше рабочих температур), то что полимер обладает абсолютной “пластической памятью” либо направленность к возобновлению начальной структуры присутствие согревании больше этой температуры, присутствие каковой совершалось деформация. Данный сухой плавный использованный материал с оптимальной износостойкостью и качествами несогласие с целью различных высокоскоростных систем скольжения и температур. Некто демонстрирует кроме того неплохие итоги с применением смазки.
Металлофторопласт наиболее эффективный с композитных использованных материалов, в коем совмещаются отличные сухие качества политетрафторэтилена с машинными качествами обыкновенного сплава. Некто обладает наиболее обширный спектр рабочих данных [4].
Наиболее оптимальным и долговечным металлофторопластом является пористая бронза, пропитанная фторопластом БрО10Фт. В таблице 1 показаны сравнительные свойства нескольких материалов [5].
Таблица 1.
Сравнительные свойства материалов
Тип материала |
Время полного износа при PV=38 кГ*м/см2*с, ч |
Причина выхода из строя |
Пористая бронза, пропитанная фторопластом Твердый графит Пористая бронза, пропитанная маслом Пористая бронза, пропитанная нейлоном Фторопласт Нейлон |
213 54 29 7 0,8 0,1 |
Износ 0,125мм Износ 0,256мм Разрушение Перегрев и износ Разрушение Разрушение |
Материал БрО10Фт имеет следующие свойства:
прочность при растяжении - 3,0 кГ/мм2,
твердость по Бринеллю 25-40 кГ/мм2,
коэффициент трения 0,05,
максимально допустимая температура 250 оС,
нагрузка 50 кГ/см2,
скорость скольжения 50 м/с.
Вывод. На основании всего выше изложенного следует отметить, что среди рассмотренных материалов для использования в паре трения штангового скважинного насоса наиболее подходит пористая бронза, пропитанная фторопластом (БрО10Фт) [5]. Данный материал позволит значительно увеличить срок службы узла трения плунжер - цилиндр, по сравнению с другими. Этот материал удачно сочетает в себе высокую конструкционную прочность, стабильность размеров и теплопроводность стали и бронзы, антифрикционные свойства фторопласта и наполнителей. Вместе с тем технология его получения достаточно проста и не требует больших трудозатрат. Все это, обусловило его более широкое применение, чем любого другого материала для пар трения.
Применение бронзофторопластового материала для изготовления уплотняющих мажет плунжеров глубинных штанговых насосов позволит повысить износостойкость последних, что в свою очередь приведет к увеличению долговечности насоса. Для разработки конструкции узла необходимо провести проверочные прочностные расчеты деталей узла и его характеристик в целом, в том числе с использованием модуля Femap CAD программ.
