Промышленное повышение октанового числа бензинов методом риформинга
Конференция: XXX Студенческая международная научно-практическая конференция «Молодежный научный форум»
Секция: Химия
лауреатов
участников
лауреатов


участников


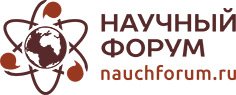
XXX Студенческая международная научно-практическая конференция «Молодежный научный форум»
Промышленное повышение октанового числа бензинов методом риформинга
Сырая нефть проходит множество этапов подготовки и переработки перед тем, как стать топливом, соответствующим всем нормируемым показателям. Получение бензина начинается с первичной переработки нефти методом разделения ее на отдельные группы углеводородов, характеризующим своим составом определенную фракцию нефти. Деление на фракции основано на различии температур испарения различных углеводородов (групп углеводородов) и осуществляется путем перегонки из смеси компонента с более низкой температурой кипения. Полученные пары после их сбора и охлаждения конденсируются, образуя так называемый дистиллят, который затем проходит несколько ступеней очистки для соответствия нормируемым показателям и сортируется по фракциям.
Однако такой бензин не всегда удовлетворяет товарным показателям. В частности, октановое число (показатель, характеризующий антидетонационные свойства бензина) такого бензина крайне мало (не более 70). Для повышения антидетонационных свойств бензинов с целью получения высокооктанового бензина используют вторичную перегонку нефти, основными видами которой являются крекинг (термический и каталитический), основной продукт которого - дополнительное количество легких, по большей части бензиновых фракций и риформинг, в процессе которого улучшаются антидетонационные свойства бензина.
При термическом крекинге высокомолекулярные углеводороды разлагаются на более легкие при температуре 450-550°С и давлении от 2 до 7 МПа. Крекингу обычно подвергают мазут или другие тяжелые нефтяные остатки прямых перегонок. При тяжелых термобарических условиях крекинга длинноцепочные молекулы исходного сырья рвутся с образованием более легких углеводородов, формирующих бензиновую фракцию. Продукты крекинга делятся ректификационной колонной на газообразные углеводороды, крекинг-бензин, крекинг-керосин [1, с. 88].
При каталитическом крекинге исходное сырье разлагаются при температурах 450-500°С и давлении 0,2 МПа с помощью катализаторов - веществ, ускоряющих реакцию и позволяющих ей протекать при более низких давлениях, чем при термическом крекинге. В качестве катализаторов обычно применяют окись алюминия (от 10 до 49 %) и окись кремния (от 50 до 85 %) .
Одна из разновидностей каталитического крекинга – риформинг, с использованием в качестве катализаторов окиси молибдена или платины при температуре около 500°С и давлении 2-4 МПа. Повышенное давление ускоряет процесс перегонки, однако требует более тщательного отбора исходного сырья. Обычно риформингу подвергают низкооктановый бензин прямой перегонки (с октановым числом 60-70) с получением в результате высокооктанового бензина. Процесс риформинга отличается сравнительной простотой и низкими энергетическими затратами. Общая схема установки риформинга (представлена на рисунке 1) аналогична установке каталитического крекинга: имеется печь для подогрева сырья, реактор (т.е. колонна), где производится реакция каталитического риформинга, ректификационная колонна для разделения продуктов риформинга [1, с. 89].
Рисунок 1. Схема установки каталитического риформинга со стационарным катализатором:
1 сырьевой насос; 2 - теплообменник; 3 - трубчатая печь; 4 - реакторы; 5 - сепаратор газа; 6 - абсорбер для обогащения водородом циркуляционного газа; 7 - сборник; 8 - абсорбер для газа; 9 - линия воздуха; 10 - линия регенерации; 11 - линии инертного газа; 12 - линия избыточного газа; 13 - линия на стабилизацию и перегонку; 14 - линия орошения.
Термический риформинг обычно проводится в трубчатых печах при температуре 550°С и давлении 70-100 ат. Выходящие из печи пары продукта подвергаются быстрому охлаждению (во избежание слишком глубокого распада). Выход реформированного бензина составляет 65-90% с октановым числом 70-80, против 45-50 у исходного продукта [2, с. 679] . Основные недостатки термического риформинга - сравнительно большой выход газа и кокса (являющимися, по сути, отходами процесса) и повышенная концентрация в бензине непредельных углеводородов, снижающих его стабильность. Из-за этого, даже при учете конструктивной простоты установки, гораздо большее распространение получил метод каталитического риформинга.
Каталитический риформинг имеет сложный химический состав исходного сырья, в который входят разнообразные бензиновые фракции, в основном представленными широкой фракцией бензина с более чем 150 углеводородами. Это углеводороды трех основных групп: предельные углеводороды (нормального и изостроения), нафтеновые углеводороды (с одной или несколькими замещающими алкильными группами) и ароматические углеводороды (бензол, толуол, ксилол и более тяжелые алкилбензолы). Перед процессом риформинга исходное сырье подвергается тщательному изучению для исключения из состава примесей более высоких фракций, усложняющих технологический процесс риформинга, повышающих рабочее давление и температуру и образующих в результате кокс (который необходимо своевременно удалять с рабочей поверхности установки каталитического риформинга).
Разеление исходного бензина (фракция 30-180 °С) при риформинге проходит на разные узкие фракции: 30 - 62 °С, 30 - 85 °С, 62 - 85 °С, 85 - 180 °С. Фракция 30 – 62 °С используется на получение петролейного эфира и как сырье в процессе компаундирования. Фракция 62 – 85 °С используется как растворитель или направляется на термический пиролиз. Фракция 85 – 180 °С применяется как предпочтительное сырье в процессе каталитического риформинга. Для фракции 105-180 °С выход высокооктанового бензина в среднем на 3-5 % выше, чем для фракции 85-180 °С при том же групповом составе исходного бензина [3] .
В процессе каталитического риформинга предъявляются высокие требования к качеству исходного сырья:
- содержание серы в сырье допускается не более 1∙10-4 % (1 мг/кг);
- содержание азота допускается не более 0,5∙10-4 %, так как азот (особенно азотистые основания) является ядом для катализаторов, разрушающим их кислотные центры [3] ;
- содержание влаги в сырье ограничивается величиной не более 1,5∙10-4 %, поскольку влага вымывает галоген, которым обрабатывается катализатор, и образует хлороводородную кислоту.
Итоговый продукт риформинга - стабильный высокооктановый бензин, содержащий до 50 % ароматических углеводородов, имеющий октановое число 94-96 и служащий базовым компонентом для автобензинов Аи-93 и Аи-98 [3] .
Бензин, получаемый каталитическим риформингом, имеет утяжеленный состав, в основном представленный ароматическими углеводородами (60-70 % (масс.)), и в чистом виде непригоден для применения (повышается нагарообразование и выбросы канцерогенных веществ.). Для получения товарных автомобильных бензинов бензин риформинга смешивают (компаундируют) с другими компонентами, выступающими в роли растворителя: легкими бензиновыми фракциями прямой перегонки нефти, изомеризатами и алкилатами.
