Влияние гидроактивации цемента на увеличение прочности цементно-песчаного раствора для дальнейшего его применения в пенобетоне
Конференция: IV Студенческая международная научно-практическая конференция «Молодежный научный форум»
Секция: Технические науки
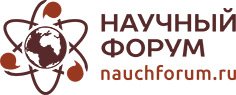
IV Студенческая международная научно-практическая конференция «Молодежный научный форум»
Влияние гидроактивации цемента на увеличение прочности цементно-песчаного раствора для дальнейшего его применения в пенобетоне
Вопросы энергосбережения в строительстве с каждым годом становятся все более актуальными. Большую роль в решении этой проблемы играют современные высокоэффективные теплоизоляционные материалы, применяемые в ограждающих конструкциях зданий.
С точки зрения энергоэффективности, прочности, экономичности, экологичности, долговечности, и противопожарных свойств на первом месте стоит теплоизоляционный пенобетон (фибропенобетон) низких плотностей (200-300 кг/м3) неавтоклавного твердения.
Наряду с явными преимуществами пенобетона (высокое сопротивление теплопередаче, замкнутые поры, цементная основа, низкое водопоглощение, достаточная паропроницаемость, сопоставимая с паропроницаемостью керамического кирпича, прирост прочности со временем, противопожарные свойства и др.), он имеет ряд недостатков, которые препятствуют его широкому применению: низкая начальная прочность и большая усадка. Эти недостатки обусловлены, прежде всего, несовершенством технологии изготовления пенобетона.
Поэтому повышение прочности пенобетона является актуальной задачей, над которой работают многие исследователи и производители пенобетона.
Прочность пенобетона зависит, прежде всего, от прочности цементно-песчаного раствора (ЦПР), из которого состоят межпоровые перегородки, составляющие пространственный несущий каркас пенобетона, который и воспринимает все нагрузки.
Очевидно, что прочность цементно-песчаного раствора зависит от нескольких факторов:
1. Вид, качество и количество цемента в 1 м3.
Между прочностью раствора и активностью цемента существует прямая линейная зависимость. Очевидно, что более прочные растворы получаются на цементах с высокой активностью (маркой). Бездобавочные цементы, как правило, показывают большую прочность, чем цементы с минеральными добавками. С увеличением количества цемента в составе ЦПР, прочность раствора так же увеличивается.
2. Водо-цементное отношение (В/Ц).
С понижением В/Ц прочность цементного камня уменьшается. Немаловажную роль играет и качество воды. Наличие в ней различных солей и примесей негативно сказывается на прочности ЦПР.
3. Качество заполнителей.
Качество заполнителя напрямую влияет на прочность ЦПР. Содержание в песке различных примесей (глины, морских раковин, органических включений) заметно снижает прочность ЦПР. Кроме того, важно правильно подобрать гранулометрию песка, чтобы обеспечить плотную упаковку ЦПР.
4. Применение специальных добавок, повышающих прочность ЦПР.
Производители пенобетона, конечно же, используют все указанные возможности для повышения прочности ЦПР, но до сих пор не получены результаты, которые бы в полной мере удовлетворили бы и производителей, и заказчиков.
Мы предлагаем, в дополнение к указанным факторам повышения прочности ЦПР, использовать имеющийся резерв в повышении активности цемента.
Как известно, диаметр частиц цемента составляет в среднем 80 микрон (мк). При взаимодействии с водой, гидратация начинается с поверхности цементных частиц и в реакцию вступает поверхностный слой толщиной примерно 20 мк, а ядро диаметром 40 мк остается сухим. Поэтому, можно констатировать, что в реакцию гидратации вступает порядка 60% от общего количества цемента, а около 40% цемента остается непрореагировавшим с водой. Вот этот резерв мы и планируем использовать для повышения прочности ЦПР. Для этого нужно измельчить зерна цемента примерно в 2 раза, чтобы получить средний размер ядра порядка 40 мк.
Этот прием не является новым, его довольно широко применяют, используя механический помол цемента в мельницах в присутствии сухих пластификаторов и песка (механоактивация цемента) [4,с. 23]. Таким образом получают ВНВ (вяжущие низкой водопотребности). Однако этот процесс отличается высокими энергозатратами, трудоемкостью и экономически целесообразен только в больших объемах и в стационарных условиях.
Мы предлагаем измельчать цемент не в мельницах (сухой помол), а в водной среде (гидроактивация цемента) в небольших компактных установках, которые можно установить не только на мини-заводах, но и непосредственно на строительных площадках для изготовления монолитного пенобетона. Прошедший гидроактивацию цемент в виде водо-цементной суспензии тут же применяется для производства пенобетона.
В данной статье мы рассмотрим только первую часть нашей работы, а именно: исследование влияния гидроактивации цемента на повышение прочности ЦПР. Работа проводилась в рамках выполнения гранта Федерального государственного бюджетного учреждения "Фонда содействия развитию малых форм предприятий в научно-технической сфере" (Договор №1841ГС/26933 от 03 марта 2017 г).
Проведя предварительные испытания гидроактиваторов разной конструкции, мы установили, что для глубокой активации цемента необходимо оборудование, обеспечивающее скорость вращения водо-цементной суспензии в камере со специальными выступами не менее 1 500 оборотов в минуту. В итоге мы применили компактный гидроактиватор специальной конструкции с 3000 об/мин и диаметром рабочей камеры 400 мм (далее "Установка").
На первом этапе мы отрабатывали режимы работы на Установке, меняли В/Ц (водоцементное отношение), время активации, интенсивность активации, применяли разные виды цемента и выявили некоторые особенности водо-цементной суспензии, подвергнутой глубокой гидроактивации:
1.В процессе глубокой гидроактивации цемент очень быстро начинает измельчаться, поверхность контакта цемента с водой значительно увеличивается и происходит ускоренная гидратация цемента, что влечет за собой быстрое загустевание суспензии и схватывание цемента прямо в Установке.
2. Процесс ускоренной гидратации цемента сопровождается быстрым повышением температуры водо-цементной суспензии: температура суспензии повышается с 180С до 500С примерно за 2 минуты работы Установки.
Эти особенности могут стать непреодолимым препятствием для применения процесса глубокой гидроактивации цемента при изготовлении ЦПР и, в конечном итоге, пенобетона.
Для исключения быстрого схватывания цемента и обеспечения его максимального измельчения в водной среде было принято решение проводить гидроактивацию цемента в присутствии суперпластификаторов, который будет препятствовать реакции гидратации цемента с водой на ранней стадии их смешивания. Применение эффективного суперпластификатора позволит решить еще одну задачу повышения прочности ЦПР: снижение В/Ц.
Важно было выбрать наиболее эффективный суперпластификатор, который бы обеспечивал максимальный пластифицирующий эффект, и в тоже время не конфликтовал с пенообразователем для пенобетона. Мы провели сравнительные испытания наиболее эффективных на наш взгляд суперпластификаторов зарубежного и российского производства. Испытания проводились путем определения консистенции (расплыва конуса) цементно-песчаного раствора с применением разных суперпластификаторов по методике ГОСТ 310.4-81 (при одинаковом водоцементном отношении) и сравнивали показатели расплыва конуса между собой.
Цементно-песчаные растворы изготавливались из одних и тех же компонентов, при одинаковом их соотношении и при одинаковой дозировке суперпластификаторов 0,7% от массы цемента (усредненная рекомендованная дозировка для указанных суперпластификаторов). Критерием эффективности в таком случае является максимальный расплыв конуса. Результаты испытаний приведены в таблице 1.
Таблица 1
Результаты испытаний суперпластификаторов
№№ пп |
Суперпластификатор |
Состав цементно-песчаного раствора |
Расплыв конуса
мм |
|||
Цемент
г |
Песок
г |
Вода
г |
Пласти-фикатор г |
|||
1 |
BASF Glenium - 116 |
1000 |
3000 |
430 |
7 |
105 |
2 |
BASFGlenium - 430 |
1000 |
3000 |
430 |
7 |
122 |
3 |
ПолипластСП СУБ |
1000 |
3000 |
430 |
7 |
114 |
4 |
Суперпластификатор №1 |
1000 |
3000 |
430 |
7 |
150 |
По результатам испытаний наилучший результат показал суперпластификатор №1, который мы и выбрали для дальнейшей работы.
На следующем этапе работы мы провели сравнительные испытания песков разных карьеров на территориях Республики Северная Осетия-Алания и Кабардино-Балкарии. Нужно было выбрать мелкий песок с минимальным загрязнением для изготовления цементно-песчаного раствора и пенобетона на его основе.
В результате длительных исследований нужный песок был найден на территории Республики Кабардино-Балкария недалеко от г. Прохладный, откуда он был завезен в лабораторию в достаточном количестве для проведения дальнейших испытаний в составе цементно-песчаного раствора.
Модуль крупности песка равен 1,898. По табл.1 ГОСТ 8736-2014 «Песок для строительных работ. Технические условия» данный песок относится к мелким пескам. Следовательно, он подходит и для применения в пенобетоне.
После того, как мы выбрали эффективный суперпластификатор и подобрали качественный песок для изготовления пенобетона, мы приступили непосредственно к проведению гидроактивации водо-цементной суспензии и изготовлению образцов из цементно-песчаного раствора на ее основе.
Для выявления влияния гидроактивации цемента на прочность цементно-песчаных растворов, мы сравнивали прочность обычного ЦПР, прочность ЦПР с суперпластификатором и прочность ЦПР с суперпластификатором, в котором цемент прошел гидроактивацию. При этом все виды цементно-песчаных растворов должны были иметь одинаковую подвижность (консистенцию). Подвижность (консистенция) цементно-песчаных растворов определялась следующим образом. На встряхивающий лабораторный столик ЛВС-01Р в его центре устанавливался стандартный конус широким основанием вверх. Затем конус наполняли изготовленным цементно-песчаным раствором, срезали излишек раствора шпателем и медленно поднимали конус вверх. Под действием собственного веса цементно-песчаный раствор растекался по столику, образуя круглую лепешку (встряхивание не проводилось!). Диаметр лепешки измерялся штангенциркулем в 2-х взаимно-перпендикулярных направлениях. Среднее из 2-х значений и принималось за расплыв конуса (консистенцию) ЦПР (Рис.1).
Рисунок 1. Расплыв конуса цементно-песчаного раствора равен 200 мм
Сначала был изготовлен Контрольный Состав ЦПР (КС-1) обычным способом (без гидроактивации) при соотношении Цемент:Песок = 1:1 (наиболее часто встречающееся соотношение при изготовлении конструкционно-теплоизоляционного пенобетона). Количество воды подобрали таким образом, чтобы получить оптимальную консистенцию (подвижность) ЦПР, равную 180-220 мм на встряхивающем столике по ГОСТ 310.4-81( без встряхивания).
Затем был изготовлен Второй Контрольный Состав (КС-2) цементно-песчаного раствора с таким же соотношением Ц:П = 1:1, но уже с применением Суперпластификатора №1 и с уменьшенным количеством воды. Количество воды подобрали таким образом, чтобы получить расплыв ЦПР, равный 180-220 мм.
И только после этого были изготовлены несколько Основных Составов (ОС), которые имели точно такой же состав ЦПР, как и в КС-2, с тем же соотношением всех компонентов (включая воду), но цемент проходил предварительную глубокую гидроактитвацию разной интенсивности.
Степень гидроактивации цемента мы определяли по температуре водо-цементной суспензии (ВЦС) на выходе из рабочей камеры. Чем выше температура (ВЦС) – тем выше степень гидратации, а значит и гидроактивации цемента. В процессе гидроактивации цемента мы доводили температуру водо-цементной суспензии до температуры 400С, 500С и 600С.
После изготовления каждого состава ЦПР и определения его подвижности (расплыва конуса) мы замеряли плотность цементно-песчаной смеси и изготавливали из нее образцы-кубики размером 100х100х100 мм.
После изготовления образцы-кубики хранились в нормальных условиях в течение 24 часов, после чего их распалубливали и помещали в емкость с водой при температуре 20 20С. На 3, 7 и 28 сутки хранения по 2 образца испытывались на прессе для определения прочности на сжатие. Результаты испытаний заносили в таблицу.
В таблице 2 приведены результаты испытаний контрольных и основных составов ЦПР. На Рис. 2 представлены графики набора прочности цементно-песчаных растворов контрольных составов КС-1 и КС-2 (с пластификатором) и основных составов ГА-1; ГА-2 и ГА-3, в которых цемент был подвергнут гидроактивации разной интенсивности (до температуры 400С, 500С и 600С соответственно.
Таблица 2
Результаты испытания контрольных и основных составов цементно-песчаного раствора
№ состава |
Плотность образцов состава , |
Прочность образцов ЦПР, МПа |
|||||
3 сутки |
7 сутки |
28 сутки |
|||||
КС-1 |
1984 |
13,03 |
13,2 |
20,08 |
20,2 |
29,7 |
30,8 |
13,29 |
20,31 |
31,95 |
|||||
КС-2 |
2033 |
19,85 |
20,1 |
27,23 |
28,2 |
38,54 |
38,7 |
20,36 |
28,8 |
38,7 |
|||||
ГА-1 (400С) |
2071 |
38,85 |
39,2 |
45,16 |
45,2 |
48,16 |
48,4 |
39,57 |
45,24 |
48,55 |
|||||
ГА-2 (500С) |
2082 |
48,85 |
47,7 |
56,06 |
54,0 |
55,33 |
54,6 |
46,8 |
52,01 |
53,93 |
|||||
ГА-3 (600С) |
2075 |
53,6 |
53,2 |
58,6 |
58,2 |
63,9 |
62,1 |
52,7 |
57,8 |
60.3 |
По результатам испытаний построены графики набора прочности ЦПР (Рис.2).
Рисунок 2. Графики набора прочности составов ЦПР
В процессе работы выяснилось, что повышение степени гидроактивации цемента приводит не только к ускорению гидратации цемента и повышению температуры водоцементной суспензии, но и значительно повышает пластичность (подвижность) ЦПР. Поэтому появляется дополнительная возможность уменьшить количество воды, и таким образом снизить В\Ц отношение, значит увеличить прочность ЦПР.
Анализируя результаты проведенных испытаний можно сделать следующие выводы:
1. Глубокая гидроактивация цемента возможна только в присутствии эффективного суперпластификатора.
2. Показателем глубокой гидроактивации является температура водо-цементной суспензии (рекомендуемая температура 50-600С);
3. Глубокая гидроактивация цемента практически в 2 раза повышает раннюю прочность ЦПР (в возрасте 3-7 суток);
4. Глубокая гидроактивация цемента более, чем в 1,5 раза повышает конечную прочность ЦПР.
Можно предположить, что и прочность пенобетона, изготовленного на гидроактивированном цементе будет значительно выше прочности пенобетона, изготовленного по обычной технологии.
