Выбор технологических условий обработки тонкостенных деталей из алюминиевых сплавов для уменьшения их коробления
Секция: Технические науки
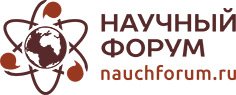
XXVIII Студенческая международная научно-практическая конференция «Технические и математические науки. Студенческий научный форум»
Выбор технологических условий обработки тонкостенных деталей из алюминиевых сплавов для уменьшения их коробления
При изготовлении тонкостенных деталей из алюминиевых сплавов появляются остаточные внутренние напряжения, возникающие в процессе формообразующих операций, а также на операциях получения заготовки. При механической обработке резанием нарушается общий баланс остаточных внутренних напряжений, это приводит к изменению размеров детали после её снятия со станочного приспособления или спустя некоторое время хранения на складе перед сборкой. Появление коробления у тонкостенных деталей, изготовленных из алюминиевых сплавов, усложняет технологический процесс обработки и сборки. Данное явление в большинстве случаев приводит к неисправимому браку. Поэтому изучение зависимости деформаций тонкостенных деталей, изготовленных из алюминиевых сплавов, от условий их механической и термической обработки на данный момент является актуальной производственной задачей. Примеры типовых деталей из алюминиевых сплавов показаны на рисунке 1.
Рисунок 1. Тонкостенные корпусные детали из алюминиевых сплавов
Из литературных источников известно, что остаточные напряжения в тонкостенных деталях из алюминиевых сплавов делятся на напряжения от термической и механической обработки. Напряжения от механической обработки делятся на напряжения от действия силового фактора, теплового фактора и напряжения от структурно-фазовых превращений в сплаве при его перегреве (рисунок 2).
Возникающие остаточные напряжения при изготовлении тонкостенной заготовки методами деформирования или литья приводят к нежелательным и недопустимым изменениям размеров и формы, а, следовательно, и к короблению деталей ГТД. Это явление часто возникает и после механической обработки.
Рисунок 2. Схема деления остаточных напряжений в деталях из алюминиевых сплавов
Таким образом, при изготовлении выше описанных деталей необходимо правильно подобрать средства технологического оснащения и режимные параметры обработки, приводящие к формированию минимальных значений остаточных напряжений.
Из литературных источников известно, что для конкретной пары обрабатываемый – инструментальный материал при заданных технологических условиях существуют оптимальные режимы резания, при которых обеспечивается минимальный износ инструмента (максимальная стойкость), а также наилучшие показатели параметров качества поверхностного слоя: минимальная шероховатость обработанной поверхности, минимальный уровень и глубина залегания остаточных напряжений и наклепа, благоприятные эксплуатационные свойства детали: максимальный предел выносливости и контактная жесткость. Оптимальные режимы резания характеризуются минимальным стабилизированным значением сил резания. Оптимальные режимы резания предпочтительно использовать на чистовом этапе обработки ответственных тонкостенных деталей, а также если требуется обеспечить высокую стойкость дорогостоящего режущего инструмента [1].
Таким образом, выполняя обработку заготовки острым инструментом на оптимальных режимах резания с небольшими глубинами и подачами можно максимально снизить влияние механической обработки резанием на суммарные остаточные напряжения. Существуют различные методики назначения оптимальных режимов обработки резанием [2,3], использование которых связано с необходимостью проводить трудоемкие эксперименты по механической обработке. Для уменьшения затрат времени и ресурсов на проведение опытов можно использовать экспериментальные данные, ранее полученные исследователями. В РГАТУ имени П.А. Соловьёва ранее была выполнена большая работа по исследованию процессов резания, накоплены данные о зависимостях параметров процесса резания от различных технологических условий обработки точением, фрезерованием и др., получены уравнения обрабатываемости для расчета оптимальных режимов обработки для различных сочетаний обрабатываемый – инструментальный материал. Анализируя ранее полученные данные средствами современного программного обеспечения, можно получить зависимости, пригодные для решения важных производственных задач. В частности, для исследуемого материала детали Д16Т на основе анализа протоколов экспериментов [4] была получена следующая зависимость критериев процесса резания и силы резания:
Б = 14,38∙А2,15 (1)
Pzmin = 682·S0,71 ·t0,94 (2)
где – энергетический критерий, характеризующий собой отношение количества тепла, уходящего при резании в стружку, к общему выделившемуся при резании количеству тепла;
где - критерий процесса резания, характеризующий степень влияния режимных условий процесса резания по сравнению с влиянием теплофизических свойств обрабатываемого материала;
а1 и b1 – толщина и ширина среза, м; t, S – соответственно глубина резания и подача, м; v – скорость резания, м/мин; а – температуропроводность обрабатываемого материала, м2/с; сρ – удельная объемная теплоемкость обрабатываемого материала, Дж/(м3 · с · град.); θ – температура в зоне резания, °С; Pzmin – минимально стабилизированная сила в зоне резания, Н, которая устанавливается после достижения оптимальной температуры θО в зоне резания.
С использованием графоаналитического метода профессора Силина С. С. [3], уравнений 1 и 2, можно получить уравнение обрабатываемости для расчета оптимальной скорости резания при точении для сочетания материалов инструмента и заготовки ВК8-Д16Т следующего вида:
(3)
В настоящее время в большинстве случаев обработка деталей выполняется инструментами зарубежных фирм Iscar, Sandvik Coromant и др. Зависимость (3) необходимо преобразовать с учетом особенностей современных режущих инструментов. Современные режущие инструменты отличаются от использованных ранее резцов с напайными пластинами наличием стружколомающих поверхностей, износостойких покрытий с низкими коэффициентами трения, новой геометрией режущего клина, маркой твердого сплава и др. Для учета особенностей используемой для Д16Т твердосплавной пластины IC907 SNMG120408-TF необходимо получить уточненное уравнение (2) в следующем виде [5]:
Pzmin = kп ·682·S0,71 ·t0,94 (4)
