Способ нанесения покрытия на рабочие поверхности деталей подшипников качения
Секция: Технические науки
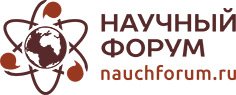
XL Студенческая международная научно-практическая конференция «Технические и математические науки. Студенческий научный форум»
Способ нанесения покрытия на рабочие поверхности деталей подшипников качения
Аннотация. В работе приведены способы нанесения покрытия на рабочие поверхности деталей подшипников качения и их недостатки.
На сегодняшний день одной из задач машиностроения является создание новых методов нанесения покрытия на рабочие поверхности деталей подшипников качения, которые заключаются в работоспособности в сложных и строго определенных условиях эксплуатации. В первую очередь встаёт необходимость выбора материала, способного выдерживать специфичные условия работы изделия в готовом механизме, с учетом нагрузки. Стоимость материала, в частых случаях, доходит до 50% от стоимости готового изделия. Для сокращения расходов на материал, часто прибегают к технологиям, которые в той или иной степени модифицируют определенные свойства выбранного материала. В соответствии с этим в технологический процесс вносятся определенные операции для изменения свойств материала. Такими операциями являются закалка, отпуск, цементация азотирование, поверхностная отделочная пластическая деформация поверхности и т.д.
Цель работы: провести сравнение способов нанесения покрытия на рабочие поверхности деталей подшипников качения и выявление их недостатков. Также на основании данного анализа выделить оптимальный способ нанесения покрытия.
Для повышения работоспособности роликоподшипника 42305 применяют различные способы нанесения функциональных покрытий на трущиеся поверхности деталей из стали 8Х4В9Ф2-Ш. Материалом роликов является сталь 15Г1.
На рис. 1 отображены рабочие поверхности подшипников - дорожки качения внутренних колец, на которые будет нанесено функциональное покрытие.
Рисунок 1. Роликоподшипник 42305, где 1 - наружное кольцо подшипника , 2 - внутреннее кольцо подшипника, 3 - ролик (шарик) подшипника, А – покрытие, О - центр подшипника, О1 - центр ролика
Одним из известных способов является - нанесение полимерного антифрикционного покрытия [4]. Данный способ включает в себя последовательно: очистку поверхности очищающим агентом, сушку очищенной поверхности, нанесение антифрикционного состава - раствора фторорганического поверхностно-активного вещества - эпилама - перфторполиоксиалкиленового или перфторированного соединения полиалкиленоксида путем погружения изделия в этот раствор, термообработку покрытия. Выполнение процесса происходит в двух ёмкостях. Очистку и сушку поверхности изделия осуществляют в первой ёмкости, при этом очистка проводится путем погружения изделия в ёмкость с очищающим агентом с применением ультразвука, сушка происходит под действием инфракрасных лучей, а нанесение антифрикционного состава и термообработка покрытия проводится во второй ёмкости, при этом стадия нанесения антифрикционного состава осуществляется погружением изделия в ёмкость с антифрикционным составом с температурой 50-60°C при воздействии ультразвука с частотой 18-22 кГц, термообработку покрытия осуществляют с помощью инфракрасного излучателя.
К недостаткам данного способа относятся:
- многооперационность технологического процесса;
- высокие энергозатраты;
- сложность нанесения покрытия на изделия с большими габаритными размерами, из - за необходимости применения больших ёмкостей и ,соответственно, приготовления больших объемов суспензии покрытия.
Современное машиностроение тесно связано с упрочнением поверхностных слоев и нанесением упрочняющих и защитных покрытий. Разработаны принципиально новые методы поверхностного упрочнения: наноструктурирование поверхностных слоев и нанесение наноструктурных покрытий [3].
Ещё один из существующих способов представляет собой нанесение покрытия на поверхность детали типа дорожки качения подшипников, включающий размещение порошка на обрабатываемую поверхность и последующее воздействие через слой порошка на поверхность вращающейся детали ультразвуковыми механическими колебаниями индентора со сферической рабочей поверхностью [5]. Поверхность дорожки качения подшипников предварительно подвергают механической обработке с образованием периодического микрорельефа с величиной шероховатости Rz=80-100 мкм, а поверхность обрабатываемого изделия погружают в порошок фторопласта, при этом дисперсность частиц порошка фторопласта составляет от 0,2 до 5 мкм.
Недостатки этого способа заключаются в ограниченности применения, поскольку порошок фторопласта не термостоек. Высокие температуры могут возникнуть при эксплуатации изделий. Данный способ рассчитан на использование простых по геометрической форме поверхностей, также не определяются условия эффективного воздействия индентора на обрабатываемую поверхность, что может снижать качество покрытия. Кроме того, порошок фторопласта обладает низкой адгезионной способностью по отношению к металлическим поверхностям и не обеспечивает глубокое его проникновение в обрабатываемую поверхность.
Также известен способ формирования покрытия на поверхности детали типа дорожки качения подшипника [6], включающий размещение порошка на обрабатываемой поверхности и последующее воздействие через слой порошка на поверхность, вращающейся детали ультразвуковыми механическими колебаниями индентора со сферической рабочей поверхностью, отличающийся тем, что используют индентор, радиус которого устанавливают равным минимальному значению радиуса профиля дорожки качения, при этом минимальную силу воздействия индентора на обрабатываемую поверхность устанавливают из условия возникновения контакта индентора по всему профилю обрабатываемой поверхности, а в качестве порошка используют мелкодисперсный графит или дисульфид молибдена.
Способ химико-термической обработки стальных изделий, в частности газовой нитроцементации[7], включает локальную защиту поверхности изделий при помощи нанесения обмазки, нагрева и диффузионного насыщения в атмосфере газового карбюризатора. В качестве науглероживающего газа используется сжиженный пропан-бутан с добавлением газообразного аммиака. При этом в качестве защитной обмазки перед нагревом на поверхность сначала наносят огнеупорную глину, просушивают ее, а затем наносят смесь оксидов железа с жидким стеклом, при этом весовое соотношение жидкого стекла и оксидов железа составляет 1:3. Данный способ позволяет повысить качество изделий, обеспечив защиту наружной поверхности от науглероживания и исключив снижение технологических свойств.
Недостатками способа можно выделить:
1. Большой расход энергии как следствие применения термических печей, ванн, камер.
2. Перед операцией химико-термической обработки изделия, на неработающих поверхностях, требуются операции защиты пастами, омеднением.
3. После химико-термической обработки требуется дополнительный этап - закалка при температуре 750 – 850°C, т.е. процесс многостадийный и длительный по времени.
В результате сравнения описанных способов нанесения покрытий на рабочие поверхности деталей подшипников качения наиболее оптимальным можно выделить формирование покрытия с использованием мелкодисперсного порошка графита или дисульфида молибдена, поскольку данный способ имеет высокую эффективность предложенной технологии обработки дорожек качения подшипников, снижение энергозатрат за счет применения ультразвуковых механических колебаний, упрощение технологии, снижение затрат на оснастку и используемое оборудование. При использовании мелкодисперсного порошка графита повышается возможная температура эксплуатации изделий. Ввиду того, что графит имеет удовлетворительную адгезию с железом, происходит диффузия частиц углерода в структуру сталей марок 8Х4В9Ф2-Ши 15Г1.
Выводы: проведенный сравнительный анализ способов нанесения покрытия на рабочие поверхности деталей подшипников качения определил достоинства и недостатки того или иного способа. Также данное исследование показало, какой из способов является более эффективным в своём использовании. Таковым является способ формирования функционального покрытия из порошка графита на рабочие поверхности детали типа дорожки качения подшипника.
