ЭКСПЕРИМЕНТАЛЬНОЕ ИССЛЕДОВАНИЕ МЕХАНИЧЕСКИХ СВОЙСТВ КОМПОЗИТНЫХ ПОКРЫТИЙ ДЕТАЛЕЙ ТРУБОПРОВОДНОЙ АРМАТУРЫ
Секция: Технические науки
лауреатов
участников
лауреатов


участников


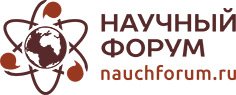
XLV Студенческая международная научно-практическая конференция «Технические и математические науки. Студенческий научный форум»
ЭКСПЕРИМЕНТАЛЬНОЕ ИССЛЕДОВАНИЕ МЕХАНИЧЕСКИХ СВОЙСТВ КОМПОЗИТНЫХ ПОКРЫТИЙ ДЕТАЛЕЙ ТРУБОПРОВОДНОЙ АРМАТУРЫ
Существует множество факторов, влияющих на качество и срок службы запорной арматуры. В основном к таким факторам относят условия окружающей среды, давление рабочей среды в трубопроводе, температурный режим и особенности веществ, транспортируемых через данный трубопровод.
В целях повышения ресурса шаровых кранов для изготовления их элементов применяют специально подобранные конструкционные материалы, используют различные методы финишной обработки поверхностей. Пробки кранов производят из латуни или нержавеющей стали. Шар и седла подвергают полировке или хромированию. Однако из-за того, что указанные материалы и способы обработки достаточно дороги, их применение далеко не всегда экономически выгодно, экологично и дает требуемый уровень надежности. В последнее время при изготовлении шаровых кранов все чаще используют технологию твердой смазки. Она позволяет обеспечить деталям весь комплекс необходимых эксплуатационных свойств, не требуя при этом больших материальных и временных затрат. Антифрикционные твердосмазочные покрытия, реализующие технологию твердой смазки, обладают высоким потенциалом в вопросах оптимизации конструкции шаровых кранов.
Такие материалы способны одновременно выполнять смазочные и защитные функции. Они не только снижают трение и износ контактирующих поверхностей, но и защищают детали от воздействия коррозионно-активных и химически-агрессивных сред. Функциональные покрытия-твердые смазки хорошо работают при отрицательных температурах в условиях наличия замерзших жидкостей с абразивными частицами, агрессивных сред, многократно снижается сила трения в узлах, момент сопротивления движению, момент страгивания, уменьшается износ, нагрузка на приводы и детали трубопроводов. За счет высокой температурной стойкости свойства материалов практически не изменяются при высоких или экстремально низких температурах. За счет высокой коррозионной стойкости замедляются процессы корродирования, разрушения поверхностей деталей, изменения физико-механических свойств поверхностей, геометрических параметров. Комплексное улучшение эксплуатационных свойств значительно повышает надежность трубопроводной системы нефте- и газопроводов, повышается ресурс деталей и узлов, снижается вероятность отказов, увеличивается межремонтный интервал, что позволяет длительно эксплуатировать трубопроводную систему в безаварийных условиях.
В предыдущей нашей статье [1] выполнен поиск подходящих материалов покрытия для вышеописанных условий, метода нанесения и технологии, выполнен предварительный анализ структурно-фазового состава покрытия. В качестве объекта исследования были выбраны два вида покрытия: плакированные никелем графитовый порошок (Ni 20 графит) и порошок гексагонального нитрида бора (BN). Метод нанесения покрытий – газоплазменный. Исследование структурно-фазового состава покрытий показало, что газоплазменное нанесение графитовых и BN никелированных порошков позволяет обеспечить высокое качество покрытия. Распределение включений графита и BN в матрице никеля в покрытии равномерное и является удовлетворительным для подобных типов покрытий.
Для экспериментального определения параметров шероховатости обработанной поверхности использовался портативный профилометр-профилограф TR 200. В качестве регистрируемых параметров, в соответствии с ГОСТ 2789–93, были выбраны наиболее часто используемые при проектировании деталей машин: среднее арифметическое отклонение профиля Ra, средний шаг неровностей профиля Sm.
Фотографии образцов приведены на рисунке 1. Шлифы образцов подготовлены на оборудовании ф. Struers.
Рисунок 1. Образцы для испытаний: внизу ЭИ961 (13Х11Н2В2МФ), слева гексагональный BN никелированный, справа графит никелированный
В таблице 1 приведены значения измеренной шероховатости поверхности образцов, среднее значение 5 измерений каждого образца.
Таблица 1
Значения измеренной шероховатости поверхности образцов
№ |
Образец |
Шероховатость Ra, мкм |
1 |
ЭИ961 |
0,51 |
2 |
гексагональный BN никелированный |
0,23 |
3 |
графит никелированный |
0,76 |
Определение микротвердости поверхностных слоев проводилось на серийном микротвердомере марки Duroscan. Cовременный микротвердомер по Виккерсу с уникальным рабочим диапазоном нагрузок 0,25 гс – 62,5 кгс и механическим столиком.. Измерения проводятся по шкалам Виккерса, Кнупа и Бринелля в нано, микро и макро диапазонах в автоматическом режиме. В качестве индентора использовалась стандартная алмазная пирамида Виккерса (ГОСТ 9377-81) с квадратным основанием и углом при вершине 136° между противоположными гранями.
В таблице 2 приведены значения измеренной микротвердости поверхности образцов, среднее значение 5 измерений каждого образца. Нагрузка на индентор 50 г.
Таблица 2
Значения измеренной микротвердости поверхности образцов
№ |
Образец |
Микротвердость HV |
1 |
ЭИ961 |
293 |
2 |
гексагональный нитрид бора BN никелированный |
59 |
3 |
графит никелированный |
96 |
а б
Рисунок 2. Изображение отпечатков: а – ЭИ961; б – графит никелированный
Как видно из данных таблицы 2, микротвердость коррозионностойкой стали (293 HV) в 3-5 раз выше, чем образцов с покрытием.
Данные по испытаниям трибологических свойств покрытий и их износостойкости будут приведены в следующих наших работах.
